Ultra-thin RF/Microwave PCB Manufacturer.An ultra-thin RF/Microwave PCB manufacturer specializes in creating exceptionally thin printed circuit boards designed for high-frequency applications. These advanced PCBs ensure superior performance and signal integrity in RF and microwave devices. By leveraging cutting-edge manufacturing techniques and materials, these manufacturers deliver reliable and compact solutions, catering to the demanding requirements of telecommunications, aerospace, and advanced electronics industries.
Ultra-thin RF/Microwave PCBs (Printed Circuit Boards) are specialized boards designed for high-frequency applications, where size, weight, and performance are critical. These PCBs are used in various industries, including telecommunications, aerospace, military, and medical devices, where compact, reliable, and efficient high-frequency signal transmission is essential.
What is an Ultra-thin RF/Microwave PCB?
An Ultra-thin RF/Microwave PCB is a type of circuit board specifically engineered to handle radio frequency (RF) and microwave signals, typically ranging from 1 MHz to 300 GHz. These PCBs are characterized by their reduced thickness, which can be as low as a few mils (thousandths of an inch), and their use of specialized materials and construction techniques to ensure minimal signal loss and interference.
Thin Profile: Significantly thinner than standard PCBs, allowing for more compact and lightweight designs.
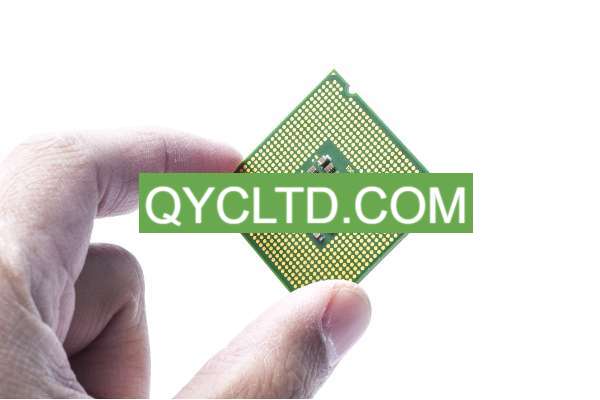
Ultra-thin RF/Microwave PCB Manufacturer
High-Frequency Performance:Optimized for minimal signal loss, low dielectric constant, and minimal signal distortion.
Thermal Management:Efficient heat dissipation to maintain performance and reliability.
Material Selection: Use of advanced materials such as PTFE, Rogers, and ceramic-filled substrates.
Precision Manufacturing:Requires precise manufacturing techniques to achieve the desired electrical performance and mechanical properties.
The Design Reference Guide for Ultra-thin RF/Microwave PCBs
Designing Ultra-thin RF/Microwave PCBs involves meticulous attention to detail to ensure they meet the high-frequency requirements and environmental challenges of their applications.
Substrates: Advanced materials like PTFE (Polytetrafluoroethylene), Rogers, and ceramic-filled substrates are preferred due to their low dielectric constants and high thermal stability.
Conductive Materials: High-purity copper is commonly used for its excellent electrical conductivity and minimal signal loss.
Multi-layer Construction:Often involves multiple layers to achieve the required electrical performance and to integrate various functions within a compact space.
Controlled Impedance: Critical for maintaining signal integrity in high-frequency applications. Requires precise control of the dielectric constant and the thickness of the dielectric layers.
Heat Dissipation:Essential to prevent overheating and maintain performance. Techniques include the use of thermal vias, heat sinks, and advanced materials with high thermal conductivity.
Thermal Simulation:Advanced simulation tools are used to predict and manage heat distribution across the PCB.
Minimizing Signal Loss: Ensuring low dielectric loss and maintaining signal integrity through careful material selection and precise manufacturing.
EMI Shielding:Electromagnetic interference (EMI) shielding techniques are employed to protect sensitive signals from external noise and interference.
Advanced Fabrication Techniques:Use of high-precision photolithography, laser drilling, and advanced etching processes to achieve the required dimensional accuracy.
Quality Control:Rigorous testing and inspection to ensure the PCB meets all electrical and mechanical specifications.
What Materials are Used in Ultra-thin RF/Microwave PCBs?
The materials used in Ultra-thin RF/Microwave PCBs are selected for their specific properties that support high-frequency signal transmission and thermal management.
PTFE (Polytetrafluoroethylene):Known for its low dielectric constant and low loss tangent, making it ideal for high-frequency applications.
Rogers Materials:A range of high-performance laminates specifically designed for RF and microwave applications. Examples include Rogers 4350B and Rogers 5880.
Ceramic-Filled Substrates:Offer a combination of low dielectric constant and high thermal conductivity, suitable for high-power applications.
High-Purity Copper: Used for signal traces and ground planes due to its excellent electrical conductivity and minimal signal loss.
Silver and Gold Plating:Sometimes used for surface finishes to enhance conductivity and protect against oxidation.
Low-Dk Dielectrics: Materials with low dielectric constants are used to minimize signal delay and distortion.
Thermal Interface Materials: Used to enhance heat dissipation between the PCB and heat sinks or other cooling solutions.
What Size are Ultra-thin RF/Microwave PCBs?
The size of Ultra-thin RF/Microwave PCBs can vary significantly based on the application and design requirements. However, their defining characteristic is their minimal thickness, which is often less than 0.5 mm.
Custom Dimensions:Designed to fit specific applications, these PCBs can range from small, intricate designs for compact devices to larger formats for more extensive systems.
Panel Sizes:Fabrication often starts with standard panel sizes, which are then cut and processed to the required dimensions.
Ultra-Thin Layers:The total thickness of the PCB can be as low as 0.2 mm, with individual layers being even thinner.
Variable Thickness:Depending on the number of layers and the specific design requirements, the overall thickness can be adjusted to balance performance and mechanical stability.
The Manufacturing Process of Ultra-thin RF/Microwave PCBs
The manufacturing process of Ultra-thin RF/Microwave PCBs involves several precise steps to ensure the final product meets the stringent requirements of high-frequency applications.
CAD Design:Detailed design using computer-aided design (CAD) software, incorporating all components, layers, and electrical paths.
Simulation: Electrical, thermal, and mechanical simulations are conducted to optimize the design for performance and reliability.
Substrate Preparation:High-quality substrates are prepared, often involving multiple layers for complex designs.
Lamination: Layers are laminated together using advanced processes to ensure uniformity and adhesion.
Photolithography:High-precision photolithography is used to define the circuit patterns on the substrate.
Etching:Chemical or plasma etching processes remove unwanted material to form the conductive traces and structures.
Micro Drilling:Laser or mechanical drilling creates vias and holes for inter-layer connections.
Plating:Copper and other materials are plated onto the vias and holes to establish electrical connectivity.
Surface Finish: Applying surface finishes such as ENIG (Electroless Nickel Immersion Gold) or HASL (Hot Air Solder Leveling) to protect the copper and enhance solderability.
Assembly:Components are mounted using surface-mount technology (SMT) or through-hole technology (THT) as required.
Electrical Testing:Rigorous tests are conducted to ensure all connections are intact and the PCB functions as intended.
Thermal Testing:Thermal tests verify the PCB’s ability to dissipate heat and maintain performance.
Final Inspection:A thorough inspection ensures the PCB meets all design specifications and quality standards.
The Application Area of Ultra-thin RF/Microwave PCBs
Ultra-thin RF/Microwave PCBs are used in various high-performance applications where compact, efficient, and reliable high-frequency signal transmission is essential.
Telecommunications: Used in RF modules, antennas, and other high-frequency components for mobile networks, satellite communications, and wireless infrastructure.
Aerospace and Defense:Deployed in radar systems, communication equipment, and electronic warfare systems, where performance and reliability are critical.
Medical Devices:Integrated into medical imaging equipment, diagnostic instruments, and wireless medical devices, where precision and reliability are essential.
Automotive: Used in advanced driver-assistance systems (ADAS), vehicle-to-everything (V2X) communication, and infotainment systems, where high-frequency performance is required.
Consumer Electronics:Found in smartphones, tablets, and wearable devices, where compact design and high-frequency performance are needed for advanced functionality.
What are the Advantages of Ultra-thin RF/Microwave PCBs?
Space and Weight Savings: The ultra-thin profile allows for more compact and lightweight designs, essential for portable and space-constrained applications.
High-Frequency Performance: Optimized materials and construction techniques ensure minimal signal loss and distortion, providing superior high-frequency performance.
Thermal Management:Efficient heat dissipation techniques maintain performance and reliability in high-power and high-frequency applications.
Flexibility:Can be tailored to specific applications with custom dimensions and layer stack-ups, providing versatility in design.
Reliability: High-quality materials and precise manufacturing processes ensure long-term reliability and performance in demanding environments.
FAQ
What materials are used in Ultra-thin RF/Microwave PCBs?
Ultra-thin RF/Microwave PCBs use advanced materials like PTFE, Rogers laminates, and ceramic-filled substrates, along with high-purity copper for conductive traces.
How are Ultra-thin RF/Microwave PCBs manufactured?
The manufacturing process involves CAD design, material preparation, photolithography, etching, drilling, plating, finishing, and rigorous testing and quality control.
In which industries are Ultra-thin RF/Microwave PCBs most commonly used?
They are commonly used in telecommunications, aerospace and defense, medical devices, automotive, and consumer electronics.
What are the main benefits of using Ultra-thin RF/Microwave PCBs?
The main benefits include space and weight savings, high-frequency performance, thermal management, design flexibility, and reliability.
What sizes are available for Ultra-thin RF/Microwave PCBs?
These PCBs can be custom-designed to specific dimensions, with thicknesses as low as 0.2 mm, depending on the application and performance requirements.