What are Ultra-small size BGA/IC Substrates?
Ultra-small Size BGA/IC Substrates Manufacturer.Our company is a leading manufacturer specializing in ultra-small size BGA and IC substrates. With cutting-edge technology and a commitment to precision, we produce high-quality substrates designed for advanced electronic applications. Our products meet the stringent requirements of modern microelectronics, ensuring exceptional performance and reliability in compact, high-density devices. Choose us for innovative solutions that drive the future of miniaturized electronics.
Ultra-small size BGA/IC substrate is a key technology in the electronics industry. It is designed to carry microchips (ICs) and components packaged in ultra-small Ball Grid Array (BGA). Compared with traditional circuit boards, this specially designed printed circuit board has a higher level of integration and a more compact size, making it suitable for the needs of various small electronic devices.
These substrates focus on high-density layout and optimized space utilization during the design and manufacturing process to ensure that more functional components can be accommodated in limited space. By adopting BGA packaging technology, ultra-small size BGA/IC substrates can connect the chip pins to the bottom of the substrate, thereby achieving a more compact layout and higher connection density.
Ultra-small size BGA/IC substrates usually use high-performance substrate materials, such as FR-4, polyimide (PI), etc., to ensure stability and reliability. During the manufacturing process, precision processing technology and advanced production equipment are applied to ensure product quality and performance.
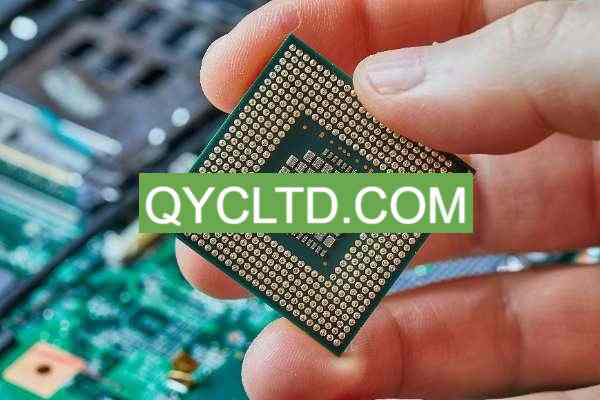
Ultra-small Size BGA/IC Substrates Manufacturer
This highly integrated ultra-small size BGA/IC substrate plays an important role in various small electronic devices, such as smartphones, tablets, wearable devices, etc. They can not only meet the miniaturization and lightweight requirements of modern electronic products, but also improve the performance and functionality of the device, bringing users a more convenient and diverse experience.
In general, ultra-small size BGA/IC substrates represent the direction of continuous innovation and progress in the electronics industry. With the continuous development of technology, it is believed that they will play an increasingly important role in future electronic devices, driving the development of electronic products in a more intelligent and portable direction.
Ultra-small size BGA/IC Substrates design Reference Guide.
Ultra-small size BGA/IC substrate design is a complex and critical task, which directly affects the performance, stability and reliability of electronic equipment. During the design process, there are multiple aspects that need to be considered to ensure the best possible working results. Here are some key principles and best practices for designers to consider:
Layout optimization
In ultra-small size BGA/IC substrate design, layout optimization is crucial. Good layout can minimize signal interference and electromagnetic interference and improve circuit performance. Designers should rationally arrange the location of components to minimize signal path length and reduce signal transmission delay. In addition, care must be taken to avoid cross-interference between components to ensure stable operation of the circuit.
Signal integrity
Maintaining signal integrity is another important consideration in ultra-small size BGA/IC substrate design. Designers need to pay attention to the impedance matching of signal transmission lines to reduce signal reflection and crosstalk. Proper ground design and power plane planning are also critical steps in ensuring signal integrity. In addition, using a suitable signal layer stacking structure can effectively reduce loss and distortion in signal transmission.
Thermal management
Ultra-small size BGA/IC substrates usually integrate a large number of functional modules, thus generating high power consumption and heat. During the design process, good thermal management options must be considered to ensure that circuit components operate within their normal operating temperature range. This includes measures such as rationally arranging radiators, increasing heat dissipation channels, and optimizing component layout. At the same time, the use of substrate materials and heat dissipation materials with high thermal conductivity is also an effective thermal management method.
In the design of ultra-small size BGA/IC substrates, the above principles and practices should be comprehensively considered and flexibly adjusted according to specific application requirements. Through reasonable design and optimization, it is possible to ensure that ultra-small size BGA/IC substrates have good performance and reliability, providing a reliable foundation for the development of electronic equipment.
What material is used in Ultra-small size BGA/IC Substrates?
The materials used in the manufacturing of ultra-small size BGA/IC substrates are one of the keys to its successful implementation. These substrates require excellent performance and reliability to meet the stringent stability and performance requirements of modern electronic devices. Several factors are often considered when selecting materials, including mechanical strength, heat resistance, chemical resistance, and electrical properties.
FR-4 is a commonly used substrate material composed of fiberglass and epoxy resin. It has good mechanical strength and heat resistance and is suitable for most conventional applications. For ultra-small size BGA/IC substrates, FR-4 material provides a good balance between cost and performance and is a common choice.
Another commonly used material is polyimide (PI), also known as bisimide or Kapton®. This material has excellent heat resistance, chemical stability and electrical insulation properties, making it suitable for high temperature environments and harsh working conditions. Polyimide substrates are commonly used in applications that require high performance and reliability, such as aerospace and medical devices.
In addition to these common materials, there are also some special-purpose substrate materials available, such as ceramic substrates and flexible substrates. These materials provide customized solutions for specific application needs, such as ceramic substrates for high-frequency and high-speed signal transmission, and flexible substrates for curved surface designs and compact spaces.
To sum up, the manufacturing of ultra-small size BGA/IC substrates usually relies on high-performance substrate materials, such as FR-4 and polyimide, to ensure their stability and reliability. Choosing the right material is critical to the performance of the substrate and the quality of the final product, so various factors need to be carefully considered during the manufacturing process and the material best suited for a specific application needs to be selected.
What size are Ultra-small size BGA/IC Substrates?
The size of ultra-small size BGA/IC substrate is one of the crucial considerations in the electronics industry. Its size is usually determined by the specific needs of the device and its integration requirements. Although in terms of manufacturing, technology has been able to achieve extremely small-sized BGA/IC substrates, in actual applications, the size is often restricted by a variety of factors.
First, the common size range of ultra-small size BGA/IC substrates usually ranges from a few millimeters to tens of millimeters, depending on the number of embedded chips, package type, and the overall design of the device. For example, portable devices such as smartphones usually require extremely small-sized substrates to meet thin, light and short design requirements, so the substrate size of these devices may range from a few millimeters to more than ten millimeters.
Secondly, the size of ultra-small size BGA/IC substrates will also change according to changes in different application requirements. In some specific application scenarios, size requirements may be more stringent. For example, in medical equipment or wearable devices, product size requirements may be more stringent, so ultra-small size BGA/IC substrates need to be designed more compactly to adapt to the miniaturization trend of equipment. In contrast, in some high-performance computers or network equipment, although a high-density layout is also required, the size constraints may be relatively loose to accommodate more functions and connectors.
Therefore, the size design of ultra-small size BGA/IC substrates needs to comprehensively consider many factors, including but not limited to the use environment of the equipment, power consumption requirements, heat dissipation requirements, and manufacturing costs. When manufacturers design ultra-small size BGA/IC substrates, they need to fully communicate with customers to understand their specific needs and tailor them according to the actual situation to ensure that the size of the substrate can best meet the product’s performance and design requirements.
To sum up, the size of ultra-small size BGA/IC substrate is the result of comprehensive consideration of many factors, and may have different performances and requirements in different application scenarios. Through reasonable design and manufacturing, ultra-small size BGA/IC substrates can provide strong support for the lightweight and compactness of electronic equipment, and promote the continuous innovation and development of electronic technology.
The Manufacturer Process of Ultra-small size BGA/IC Substrates.
The manufacturing process of ultra-small size BGA/IC substrates is a precise and complex process involving multiple key steps, from the design stage to final manufacturing. Here’s a detailed explanation of the process:
Design phase
The process of manufacturing ultra-small size BGA/IC substrates begins at the design stage. At this stage, engineers use CAD (computer-aided design) software to create prototype drawings of the circuit board. The design must take into account size, layout, stack-up structure, and routing of signals and power. Especially in ultra-small size substrates, space constraints and circuit layout become particularly critical.
Raw material preparation
Once the design is complete, the next step is to prepare the raw materials required for the manufacturing process. This includes substrate material, conductive material (usually copper foil), insulating layers and other auxiliary materials. These materials must meet strict quality standards to ensure the performance and reliability of the final product.
Sheet metal processing
In this step, the substrate material is cut to the required size and surface treated to enhance adhesion. Mechanical or laser cutting techniques are often used to ensure precision and consistency of the substrate.
Printing and molding
The next step is to print the circuit pattern onto the substrate surface. This is typically done by coating a photosensitive resin onto a substrate and using ultraviolet light exposure to form the pattern. Unwanted material is then removed or a conductive layer is added through chemical etching or metal deposition. The molding process may also involve multi-layer stacking, where different layers are connected to each other through lamination and gluing.
Component installation
Once the circuit pattern of the substrate is formed, the next step is to mount the electronic components into the corresponding locations. This may involve a manual or automated assembly process, depending on the production scale and requirements. In ultra-small size BGA/IC substrates, precise component placement and soldering are critical to ensure performance and reliability.
Debugging and testing
Finally, a critical step in the manufacturing process is debugging and testing the finished product. This includes checking the integrity of circuit connections and verifying circuit functionality and performance through analog and digital testing. Any issues found will be logged and fixed to ensure the quality of the final product.
Through these steps, ultra-small size BGA/IC substrates are manufactured, providing key support and functions for various small electronic devices.
The Application area of Ultra-small size BGA/IC Substrates.
As an indispensable core component in modern electronic equipment, ultra-small size BGA/IC substrates have an increasingly wide range of applications, covering the needs of multiple industries. The following are the wide applications of ultra-small size BGA/IC substrates in various fields:
Portable consumer electronics
In the field of portable consumer electronics, such as smartphones, tablets, headphones and other devices, ultra-small size BGA/IC substrates play a key role. These devices need to integrate more functions and components in a limited space, and the compact design and high integration level of ultra-small size BGA/IC substrates make them ideal for achieving this goal. Whether it is high-performance processors, memories or various sensors, precise and reliable integration can be achieved through ultra-small size BGA/IC substrates.
Medical equipment
In the field of medical equipment, the application of ultra-small size BGA/IC substrates is also becoming increasingly popular. Such as portable medical monitoring equipment, compact medical imaging equipment, etc., all require highly integrated circuit boards to achieve accurate data collection and processing. Ultra-small size BGA/IC substrates can not only meet the strict size requirements of these devices, but also provide stable and reliable performance to ensure the reliable operation of medical equipment in various environments.
Smart wearable devices
With the rise of smart wearable devices, ultra-small size BGA/IC substrates also play an important role in this field. Devices such as smart watches, smart glasses, and health monitors need to integrate multiple functions in an extremely limited space, and require circuit boards to be lightweight and low-power consumption. The application of ultra-small size BGA/IC substrates allows these smart wearable devices to achieve more refined and portable designs while maintaining high performance and long battery life.
In general, the wide application of ultra-small size BGA/IC substrates in portable consumer electronics, medical equipment, smart wearable devices and other fields has promoted the development of electronic equipment in a more compact, lightweight and intelligent direction, and has improved people’s lives and Work brings more convenience and possibilities.
What are the advantages of Ultra-small size BGA/IC Substrates?
Ultra-small size BGA/IC substrates have many advantages over traditional circuit connection methods. These advantages make them an indispensable and important component in the design of today’s electronic equipment. The following are several outstanding advantages of ultra-small size BGA/IC substrates:
Higher integration
Ultra-small size BGA/IC substrate adopts advanced manufacturing technology and high-density layout, which can accommodate more electronic components and functional modules in a limited space. Compared with traditional line connection methods, ultra-small size BGA/IC substrates can achieve a higher level of integration, making the circuit board more compact, thereby bringing greater flexibility and freedom to device design.
Smaller size
Due to the use of miniaturized BGA packaging and compact layout design, ultra-small size BGA/IC substrates have significant advantages in size. This small size design allows electronic devices to be lighter and more portable, and is suitable for products with strict volume requirements such as smartphones, tablets, and smart wearable devices.
More reliable performance
Ultra-small size BGA/IC substrates focus on key factors such as signal integrity, electromagnetic compatibility, and thermal management during the design and manufacturing process to ensure the stability and reliability of the circuit board. Compared with traditional line connection methods, BGA packaging provides more stable soldering contacts, which can effectively reduce circuit board failure rates and maintenance costs, and improve the overall performance and reliability of the equipment.
In general, ultra-small size BGA/IC substrates provide more flexible and reliable solutions for the design and manufacturing of electronic equipment through its advantages of high integration, small size and reliability. With the continuous advancement and innovation of technology, ultra-small size BGA/IC substrates will continue to play an important role in various fields, promoting the development of electronic products in the direction of more compact, lightweight and high-performance.
FAQ
How reliable are ultra-small size BGA/IC substrates?
Ultra-small size BGA/IC substrates adopt a series of strict quality control measures during the design and manufacturing process to ensure their stability and reliability. In addition, high-quality materials and advanced manufacturing processes also ensure the reliability of the substrate. Therefore, when used and maintained correctly, ultra-small size BGA/IC substrates have excellent reliability.
What aspects should be paid attention to when maintaining ultra-small size BGA/IC substrates?
When maintaining ultra-small size BGA/IC substrates, care should be taken to avoid excessive bending, excessive squeezing, or excessive stretching of the substrate to prevent damage or breakage. In addition, regular inspection of the status of connectors, solder joints and circuit components to promptly detect and repair possible problems is also an important part of maintenance work.
What is the environmental adaptability of ultra-small size BGA/IC substrates?
Ultra-small size BGA/IC substrates usually use high-quality materials and covering layers, have good moisture resistance, corrosion resistance and high temperature resistance, and can work stably in various harsh environmental conditions. However, when selecting and using substrates, users still need to make reasonable considerations and choices based on specific application environments and requirements.
How to solve the recycling problem of ultra-small size BGA/IC substrates?
Ultra-small size BGA/IC substrates usually contain a variety of materials, including metal, plastic, fiberglass, etc. Recycling of these substrates requires specialized processing and decomposition in order to effectively recover and reuse the resources within them. At present, some professional recycling organizations have begun to research and practice the recycling technology of ultra-small size BGA/IC substrates, making positive contributions to environmental protection.