What are Ultra High Density Wiring Substrates?
Ultra High Density Wiring Substrates Manufacturer, A pioneer in precision engineering, our company leads the industry as the foremost manufacturer of Ultra High Density Wiring Substrates. Combining cutting-edge technology with unparalleled craftsmanship, we specialize in producing substrates that redefine standards in compact electronics. Our dedication to innovation ensures that each substrate we create offers exceptional performance and reliability, meeting the rigorous demands of modern electronics. With a commitment to excellence ingrained in every aspect of our process, we empower businesses to achieve new heights of efficiency and functionality in their electronic devices.
Ultra High Density Wiring Substrates are an important part of today’s electronics industry and play a key role in connecting and supporting electronic components. They are used in a wide range of electronic devices, from smartphones and tablets to servers and industrial control systems.
These substrates are called “ultra-high density” because they have unusually high circuit routing densities and tiny pitches. On an ultra-high-density wiring substrate, thousands of tiny wires are precisely laid out in a very limited space. This highly dense design allows a large number of electronic components to be integrated in a limited space, thereby achieving more complex circuit functions.
In ultra-high-density wiring substrates, fine wires are usually manufactured through advanced printing technology and etching processes. These wires are usually constructed of highly conductive materials, such as copper or silver, and are embedded in a special insulating substrate to ensure the stability and reliability of the circuit.
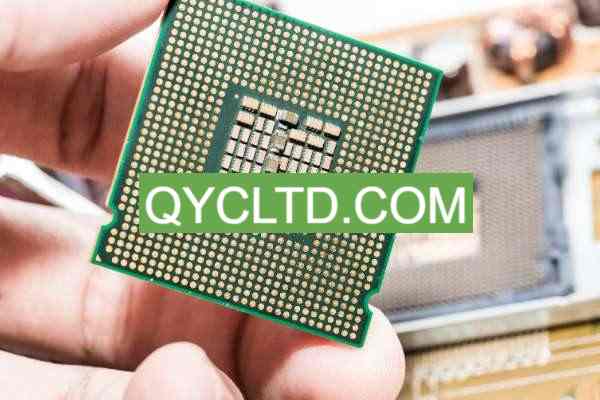
Ultra High Density Wiring Substrates Manufacturer
The design and manufacturing of ultra-high-density wiring substrates require highly precise processes and technologies. Engineers must consider factors such as routing rules, signal integrity, thermal management, and electromagnetic compatibility to ensure circuit performance and stability.
Overall, ultra-high-density wiring substrates play an integral role in modern electronic devices. Not only do they provide the infrastructure to support and connect electronic components, they also provide critical support for the functionality and performance of the device. With the continuous development and innovation of technology, ultra-high density wiring substrates will continue to play an important role in promoting the progress and development of the electronics industry.
Ultra High Density Wiring Substrates design Reference Guide.
The design of ultra-high-density wiring substrates is a complex and critical process that involves the comprehensive consideration of multiple factors. When designing ultra-high-density wiring substrates, engineers need to carefully consider wiring rules, inter-layer stacking, signal integrity and other aspects to ensure that the final product has excellent performance and reliability.
First, wiring rules are fundamental in the design process. Engineers need to determine the best cabling path to minimize signal transmission delays and interference while ensuring cabling stability and reliability. Reasonable wiring rules can effectively reduce signal noise and crosstalk, and improve circuit performance and stability.
Secondly, interlayer stacking is an important consideration in the design of ultra-high-density wiring substrates. By rationally designing the interlayer stacking structure, good isolation and interconnection between different signal layers can be achieved, thereby improving signal integrity and anti-interference capabilities. Reasonable inter-layer stacking design can also optimize wiring density and power consumption distribution, further improving circuit performance.
In addition, signal integrity is also an important aspect that cannot be ignored in the design of ultra-high-density wiring substrates. Engineers need to comprehensively consider the length of the signal transmission line, impedance matching, signal attenuation and other factors to ensure that the signal remains stable and accurate during the transmission process. Through reasonable signal integrity design, signal distortion and delay can be minimized and the reliability and performance of the circuit can be improved.
In summary, the Ultra-High Density Wiring Substrate Design Reference Guide provides key guiding principles to help engineers design circuit boards with excellent performance. By carefully considering wiring rules, inter-layer stacking, signal integrity and other aspects, the performance, reliability and stability of the circuit can be effectively improved to meet the needs of different application fields.
What material is used in Ultra High Density Wiring Substrates?
The material selection of ultra-high-density wiring substrates is crucial because it directly affects the performance, stability and reliability of the circuit board. Here are some commonly used high-performance substrate materials:
Special glass fiber reinforced epoxy resin (FR-4)
FR-4 is a common and widely used substrate material. It has excellent mechanical strength and thermal stability and is suitable for high-density wiring and miniaturization design. Its glass fiber reinforced structure makes the circuit board have good bending and impact resistance, as well as good high temperature resistance, making it suitable for applications in a variety of environmental conditions.
Polytetrafluoroethylene (PTFE)
PTFE material is favored for its excellent electrical properties. It has a low dielectric constant and low dielectric loss, making the board perform well in high-frequency applications. PTFE material also has excellent chemical stability and high temperature resistance, and can resist corrosion and the impact of high temperature environments on circuit boards. Therefore, it is widely used in fields such as communications and radar.
Multilayer composite materials
In addition to single materials, there are also substrates that use multi-layer composite materials. These materials combine the advantages of different materials, such as polyimide (PI) with FR-4 for better electrical and mechanical properties. The use of multi-layer composite materials can meet the performance requirements of different applications for circuit boards and provide more flexible options.
Metal substrate
For some applications that require better heat dissipation performance, such as LED lighting and automotive electronics, metal substrates are a common choice. Metal substrates have excellent heat dissipation properties and can effectively conduct heat to the surrounding environment, thereby maintaining a stable operating temperature of electronic components.
In summary, the material selection for ultra-high-density wiring substrates should be determined based on specific application needs and performance requirements. No matter which material is chosen, it needs to ensure that it has good electrical, mechanical and thermal properties to ensure stable operation of the circuit board under various environmental conditions.
What size are Ultra High Density Wiring Substrates?
Ultra High Density Wiring Substrates are an important part of today’s electronics industry, and their flexible size selection provides customized solutions for various applications. Whether it’s a small handheld device or a large server, ultra-high-density cabling substrates can meet different scale and performance needs.
Size is often a key consideration in the design and manufacture of electronic devices. Flexible size options for ultra-high-density wiring substrates provide designers with greater freedom. For small handheld devices, such as smartphones, tablets, and wearables, ultra-high-density wiring substrates can be designed to be more compact to fit into limited internal space. By minimizing size, thinner, more portable product designs can be achieved and user experience improved.
For applications such as large servers and data centers, the size of ultra-high-density wiring substrates can be designed to be larger to accommodate more electronic components and connectors. These large devices often need to handle large data streams and complex computing tasks, so higher performance and larger size are required to support these functions. Ultra-high-density wiring substrates can be designed into different shapes and sizes according to specific needs to meet the needs of different application scenarios.
In addition, ultra-high-density wiring substrates are also widely used in automotive, aerospace, medical and other industries. In the automotive industry, they can be used in in-vehicle electronic systems to provide vehicle control, navigation and entertainment functions. In the aerospace field, ultra-high-density wiring substrates can be used in key equipment such as flight control systems, communication systems, and navigation systems. In medical equipment, they can be used in medical imaging equipment, patient monitoring equipment, and diagnostic equipment, among others.
Overall, the flexible size options of ultra-high-density wiring substrates provide customized solutions for a variety of industries and applications. Whether it is a small handheld device or a large server, they can meet different scale and performance requirements, providing important support for the design and manufacturing of modern electronic devices.
The Manufacturer Process of Ultra High Density Wiring Substrates.
The manufacturing process of ultra-high-density wiring substrates is a precise process involving multiple complex steps. Each step is crucial and directly affects the quality and performance of the final product. The first is multi-layer stacking, which is to meet the complexity of the circuit and the need for high-density wiring. Multilayer circuits are routed and connected by stacking multiple layers of substrates (usually FR-4 or other high-performance materials) together and adding conductive layers within them.
Next is circuit diagram design, which is one of the key steps in manufacturing ultra-high-density wiring substrates. Design engineers must accurately plan wiring paths, determine electrical connections, and route signal transmission to ensure circuit performance and stability. With advanced design software and technology, they are able to achieve compact layouts of complex circuits within limited space and maximize wiring density.
Then comes chemical etching, which is one of the indispensable process steps in manufacturing ultra-high-density wiring substrates. Chemical etching technology removes unnecessary copper foil by soaking the circuit board in a specific etching solution to form the desired circuit pattern. This process requires highly precise control and monitoring to ensure that the etching depth and accuracy meet design requirements while avoiding damage to other parts.
High-precision manufacturing processes are key to ensuring the performance and reliability of ultra-high-density wiring substrates. Each step requires strict quality control and testing to ensure the accuracy and stability of the circuit board. Through superb technology and strict manufacturing processes, manufacturers are able to produce ultra-high-density wiring substrates that meet high standards, providing important support for the performance improvement and innovation of various electronic devices.
The Application area of Ultra High Density Wiring Substrates.
Ultra-high density wiring substrate is a vital technology in the electronics industry. It is widely used in many fields and provides key support for the functionality and performance improvement of modern electronic equipment. The following are examples of ultra-high-density wiring substrate applications in communications, medical and aerospace fields:
In the field of communications, ultra-high-density wiring substrates are widely used in various communications equipment, such as mobile phones, base stations, and satellite communication systems. These devices require highly integrated circuit boards to implement complex signal processing and data transmission functions. Ultra-high-density wiring substrates provide stable and reliable circuit support for communication equipment through compact layout and high-performance electrical characteristics, thereby improving the efficiency and reliability of communication networks.
In the medical field, ultra-high-density wiring substrates play an important role in medical equipment. For example, medical imaging equipment (such as MRI, CT scanners) and life monitoring equipment (such as electrocardiographs, blood pressure monitors) often require high-density, high-performance circuit boards to achieve precise signal processing and data transmission. The application of ultra-high-density wiring substrates makes these medical devices more accurate and reliable, helping doctors accurately diagnose conditions and provide effective treatment plans.
In the aerospace field, ultra-high-density wiring substrates are widely used in aircraft and spacecraft control systems, communication systems, and navigation systems. These systems have strict requirements for highly integrated circuit boards, which require them to operate stably and reliably in extreme environments (such as high temperature, low temperature, high altitude, etc.). Ultra-high-density wiring substrates ensure the performance and safety of aerospace equipment through optimized design and reliable manufacturing processes, providing important support for the development of the aerospace industry.
Overall, ultra-high-density wiring substrates play a key role in applications in multiple fields such as communications, medical, and aerospace. Its highly integrated and high-performance characteristics provide a reliable foundation for the functionality and performance improvement of modern electronic equipment, and promote the technological progress and development of various industries.
What are the advantages of Ultra High Density Wiring Substrates?
Ultra-high-density wiring substrates have many obvious advantages over traditional circuit boards. First, they offer a higher level of integration, which means more electronic components can be accommodated on the same size substrate. This increase in integration allows circuit boards to implement more complex functions while being more flexible in design.
Secondly, ultra-high-density wiring substrates have superior performance. Due to denser wiring, the signal transmission path is shorter, resulting in faster signal transmission and less signal interference. Such performance advantages are particularly significant in high-frequency applications, which can ensure the stability and reliability of data transmission.
Most importantly, ultra-high-density wiring substrates are smaller in size. Circuit boards with the same functions can be designed to be more compact, which is especially important for electronic devices that require miniaturization. The small size of the circuit board also means that the overall device is smaller, allowing for the design of lighter and more portable products.
In addition, ultra-high-density wiring substrates enable compact layout of complex circuits. Through multi-layer stacking and miniaturized wiring technology, various functional modules can be more closely integrated, thereby reducing the overall volume of electronic equipment. This compact layout also helps reduce electromagnetic interference from the circuit board, improving overall system performance and stability.
To sum up, the advantages of ultra-high-density wiring substrates include high integration, superior performance, small size, and compact layout. These advantages make ultra-high-density wiring substrates an indispensable key technology in today’s electronics industry, providing important support for the performance improvement and innovation of various electronic devices.
FAQ
What is the biggest advantage of ultra-high-density wiring substrates?
The biggest advantages of ultra-high-density wiring substrates are their high integration and superior performance. Because its design and manufacturing process can achieve smaller wiring pitches and higher interlayer stacking, it can integrate more electronic components in a limited space. This not only makes the device more compact, but also improves the performance and reliability of the circuit. At the same time, ultra-high-density wiring substrates can also meet the needs of modern electronic equipment for high-speed transmission, low power consumption and high frequency, so they are widely used in various fields.
What key processes are required to manufacture ultra-high-density wiring substrates?
Manufacturing ultra-high-density wiring substrates requires multiple precision processes. First of all, designers need to conduct rigorous circuit diagram design and layout planning to ensure that the circuit layout is compact and reasonable. Next comes the design of inter-layer stacking, which requires precise control of wiring and signal transmission paths between different layers. In the manufacturing process, chemical etching is one of the key steps to form precise wiring structures by controlling the etching rate and etching depth. In addition, multiple metal deposition, etching and packaging processes are required to ensure the accuracy and stability of wiring. The entire manufacturing process requires a high degree of automation and precision control to ensure product quality and production efficiency.
In which industries are ultra-high-density wiring substrates widely used?
Ultra-high-density wiring substrates are widely used in communications, medical, aerospace, automotive and other fields. In the field of communications, they are used to manufacture high-performance network equipment and communication base stations, supporting high-speed data transmission and low-latency communications. In the medical field, ultra-high-density wiring substrates are used in high-precision equipment such as medical diagnostic equipment and medical image processing systems to provide stable and reliable circuit support. In the aerospace field, ultra-high-density wiring substrates are used to manufacture avionics equipment, satellite communication equipment, etc., with high anti-interference and high reliability. In the automotive field, they are used in on-board electronic systems, autonomous driving technology and other fields to provide stable circuit support and data transmission.
What is the future development trend of ultra-high density wiring substrates?
As electronic devices continue to develop and miniaturization trends intensify, ultra-high-density wiring substrates will continue to play an important role. In the future, the development of emerging technologies such as artificial intelligence, the Internet of Things, and 5G communications will further promote the demand for ultra-high-density wiring substrates. At the same time, the continuous innovation of manufacturing technology and the continuous improvement of processes will also enable ultra-high-density wiring substrates to achieve greater breakthroughs in performance, cost and reliability, bringing more innovation and development opportunities to the electronics industry.