High frequency Cavity PCBs Manufacturer.”High frequency cavity PCBs manufacturer specializes in crafting advanced printed circuit boards optimized for high-frequency applications. These PCBs feature meticulously designed cavities that enhance signal integrity and performance, catering to industries requiring robust and reliable electronic solutions.”
High-frequency cavity PCBs are specialized printed circuit boards designed to operate at high frequencies and incorporate cavities or hollow spaces to optimize signal performance. These PCBs are critical in applications requiring precise control of high-frequency signals, such as telecommunications, อวกาศ, defense, and advanced medical devices. By incorporating cavities, these PCBs enhance signal integrity, reduce electromagnetic interference, and minimize signal loss.
What is a High-Frequency Cavity PCB?
A high-frequency cavity PCB is a printed circuit board that includes strategically placed cavities or hollow spaces within its structure to optimize the performance of high-frequency circuits. These cavities help to isolate RF components, reduce cross-talk, and minimize signal loss, ensuring reliable and efficient operation at high frequencies. The design and construction of high-frequency cavity PCBs require advanced materials and precise manufacturing techniques to meet stringent performance requirements.
High-Frequency Cavity PCB Design Reference Guide
Designing a high-frequency cavity PCB involves several critical considerations to ensure optimal performance. The following sections outline the key aspects of high-frequency cavity PCB design.
The choice of materials is crucial for the performance of high-frequency cavity PCBs. Key materials include:
Substrate Materials: High-frequency substrates such as Rogers, ไฟเบอร์ (Teflon), and ceramic-filled materials are commonly used due to their low dielectric constant (Dk) and low dissipation factor (Df). These materials help maintain signal integrity at high frequencies.
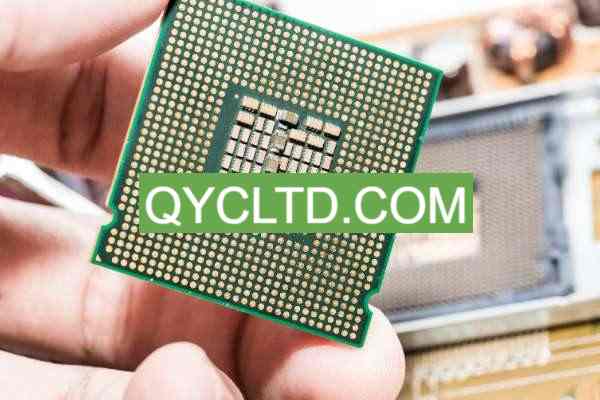
High frequency Cavity PCBs Manufacturer
Copper Foil: High-purity copper is used for the conductive traces and planes, providing excellent electrical conductivity and reliability.
Prepreg and Laminate: High-performance prepreg and laminate materials are used to bond the layers together, offering low dielectric loss and high thermal stability.
The design of cavities in high-frequency PCBs is a critical factor in their performance:
Cavity Placement: Cavities are strategically placed to isolate RF components, reduce cross-talk, and minimize signal loss. The placement is determined based on the specific circuit design and frequency requirements.
Cavity Depth and Shape: The depth and shape of the cavities are designed to optimize the performance of the high-frequency circuits. This may involve complex geometries to match the impedance and enhance signal propagation.
Shielding and Grounding: Proper shielding and grounding techniques are implemented to prevent electromagnetic interference (EMI) and ensure signal integrity.
The layer stack-up is designed to support the high-frequency requirements of the circuits:
Signal Layers: Multiple signal layers are used to route high-frequency signals. These layers are designed with controlled impedance to ensure minimal signal loss and high signal integrity.
Power and Ground Planes: Dedicated power and ground planes provide stable voltage references and reduce noise, which is critical for maintaining signal integrity in high-frequency applications.
Thermal Management Layers: Thermal vias and heat spreaders are incorporated to dissipate heat generated by high-frequency components, ensuring reliable performance.
Several key considerations must be addressed during the design phase:
Signal Integrity: High signal integrity is maintained through controlled impedance, differential pair routing, and minimizing parasitic effects. The design must ensure that the signal paths are as short and direct as possible.
Power Distribution: Efficient power distribution is ensured through dedicated power planes, minimizing voltage drops and ensuring stable power delivery to RF components.
Thermal Management: Effective thermal management techniques, such as thermal vias and heat spreaders, prevent overheating and ensure consistent performance.
Mechanical Stability: The board must provide robust mechanical support to withstand the stresses of handling and operation in high-frequency environments.
What Materials are Used in High-Frequency Cavity PCBs?
Materials used in high-frequency cavity PCBs are selected for their electrical, thermal, and mechanical properties:
Rogers Substrate: Rogers materials are widely used in high-frequency applications due to their low dielectric constant and low loss, which are essential for high-frequency performance.
ไฟเบอร์ (Teflon): PTFE is another popular choice for high-frequency substrates, offering excellent electrical properties and low dielectric loss.
Ceramic-Filled Materials: These materials provide high thermal stability and low dielectric loss, making them suitable for high-power RF applications.
Copper Foil: High-purity copper is used for the conductive traces and planes, providing excellent electrical conductivity and reliability.
Prepreg and Laminate: High-performance prepreg and laminate materials are used to bond the layers together, offering low dielectric loss and high thermal stability.
What Size are High-Frequency Cavity PCBs?
The size of high-frequency cavity PCBs varies depending on the application and specific design requirements:
Thickness: The thickness of high-frequency cavity PCBs can range from 0.5 mm to several millimeters, depending on the number of layers and the thermal management requirements.
Dimensions: The length and width of the PCBs are determined by the size of the components and the layout of the system. They can range from small form factors for compact devices to large boards for complex RF systems.
The Manufacturing Process of High-Frequency Cavity PCBs
The manufacturing process of high-frequency cavity PCBs involves several precise and controlled steps to ensure high quality and performance:
High-performance substrate materials, copper foils, and prepreg materials are prepared and cut into appropriate sizes for processing.
Layers are fabricated by laminating conductive and insulating materials in a stack. Each layer is patterned using photolithography to define the circuitry.
Cavities are created using precise drilling and milling techniques. The depth and shape of the cavities are carefully controlled to meet the design specifications.
Microvias and through-holes are drilled using laser or mechanical drilling techniques. These holes are then plated with copper to create electrical connections between layers.
The individual layers are laminated together under heat and pressure to form a solid, multilayer structure. This process ensures that all layers are firmly bonded and aligned.
Photolithography and etching processes are used to create fine-pitch circuitry on each layer, requiring high precision for accurate interconnections.
After fabrication, the board is assembled with any necessary components and connectors. Rigorous testing is conducted to ensure that the board meets all design specifications and performance requirements.
The Application Area of High-Frequency Cavity PCBs
High-frequency cavity PCBs are used in a wide range of high-frequency applications:
In telecommunications, high-frequency cavity PCBs are used in base stations, antennas, and other high-frequency communication equipment to ensure reliable signal transmission and reception.
In aerospace and defense applications, high-frequency cavity PCBs are used in radar systems, อุปกรณ์สื่อสาร, and electronic warfare systems, where precise control of RF signals is critical.
In medical devices, high-frequency cavity PCBs are used in imaging systems, diagnostic equipment, and wireless communication devices, where high-frequency performance is essential.
In test and measurement equipment, high-frequency cavity PCBs are used to support high-frequency signal testing and analysis, ensuring accurate and reliable results.
What are the Advantages of High-Frequency Cavity PCBs?
High-frequency cavity PCBs offer several advantages that make them indispensable in high-frequency applications:
High Performance: They provide excellent electrical properties, enabling reliable high-frequency signal transmission with minimal loss.
Signal Integrity: High signal integrity is maintained through controlled impedance and low-loss materials, ensuring accurate signal transmission.
Thermal Management: Effective thermal management techniques prevent overheating and ensure consistent performance at high frequencies.
Mechanical Stability: Robust mechanical properties ensure the board can withstand the stresses of handling and operation in high-frequency environments.
Reliability: High-quality materials and precise manufacturing processes ensure long-term reliability and performance.
คำถามที่ถามบ่อย
What are the key considerations in designing a high-frequency cavity PCB?
Key considerations include material selection for electrical and thermal performance, cavity design for signal isolation and loss minimization, layer stack-up for complex routing, and ensuring signal integrity, การกระจายพลังงาน, thermal management, mechanical stability, และความน่าเชื่อถือ.
How do high-frequency cavity PCBs differ from standard PCBs?
High-frequency cavity PCBs are specifically designed for high-frequency applications, featuring cavities for signal isolation and optimized materials for minimal signal loss, while standard PCBs are used for general electronic applications with less demanding performance requirements.
What is the typical manufacturing process for high-frequency cavity PCBs?
The process involves material preparation, layer fabrication, cavity creation, drilling and plating, lamination, circuit patterning, assembly, and rigorous testing to ensure high quality and performance.
What are the main applications of high-frequency cavity PCBs?
These PCBs are used in telecommunications, aerospace and defense, medical devices, and test and measurement equipment, providing advanced functionality and reliability in high-frequency applications.