What are FC-LGA Package Substrates?
FC-LGA วัสดุพิมพ์แพ็คเกจ ผู้ผลิต. FC-LGA Package Substrates Manufacturer specializes in crafting cutting-edge substrates tailored for FC-LGA packages. With a relentless pursuit of excellence, our skilled team engineers substrates with precision and reliability, meeting the exacting standards of modern electronics. Employing advanced techniques and materials, we ensure optimal electrical performance and thermal management crucial for high-functioning FC-LGA assemblies. Our commitment to innovation drives us to continually push boundaries, delivering solutions that empower the next generation of electronic devices. Trust in our expertise to provide substrates that form the backbone of seamless connectivity and robust performance in FC-LGA applications.
FC-LGA packaging substrate is a packaging method that directly connects the bare chip (bare crystal) to the substrate through flip-chip (Flip-Chip) technology. This technology offers significant advantages over traditional บรรจุ ภัณฑ์ methods, especially in high-performance and high-density applications. Traditional packaging technology usually uses wire bonding to connect the chip and the substrate through small metal wires. อย่างไรก็ตาม, this method has obvious limitations in high-frequency and high-power applications, such as large signal delay and low heat dissipation efficiency.
Flip chip technology greatly shortens the signal transmission path by flipping the bare chip so that its pads (bumps) are in direct contact with the interconnection points on the substrate. This design not only reduces signal delay and capacitive effects, but also improves the electrical connection performance between the chip and the substrate. ในเวลาเดียวกัน, flip-chip technology allows the chip to be more closely attached to the substrate, increasing the compactness and integration of the package.
In the structure of FC-LGA packaging substrate, high-performance insulating materials are usually selected as substrate materials, such as BT resin (Bismaleimide-Triazine Resin) or ceramic materials. These materials have excellent electrical insulation properties and thermal conductivity, and can maintain stable operation in high temperature and high frequency environments. The substrate is usually covered with a layer of copper foil to form circuit patterns and connection points to ensure reliable connection between the chip and the substrate.
In FC-LGA packaging, thermal performance is a key factor. Since the chip generates a lot of heat when operating at high frequency and high power, reasonable heat dissipation design is crucial. Flip chip technology allows heat dissipation materials or heat dissipation structures, such as thermal interface materials (TIM) or heat sinks, to be placed directly between the chip and the substrate, thereby improving heat dissipation efficiency and ensuring the stability and reliability of the chip during high-power operation.
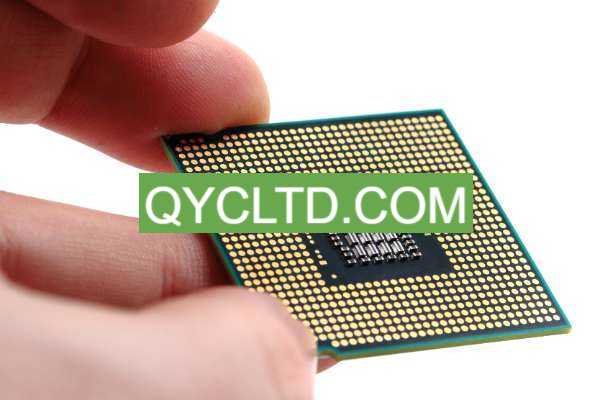
ผู้ผลิตพื้นผิวแพ็คเกจ FC-LGA
นอกจากนี้, the FC-LGA packaging substrate also supports higher I/O density, which means that more input/output connection points can be arranged on the same area of the substrate. This is particularly important for modern high-performance computing devices and communications equipment, which require high bandwidth and high-speed data transmission.
ทั้งหมด, FC-LGA packaging substrate has significant advantages in improving electrical performance, heat dissipation performance and integration, and is widely used in high-performance computing, อุปกรณ์สื่อสาร, high-end consumer electronics and other fields. Its technological innovation not only improves the overall performance of the chip, but also promotes the development of electronic products toward more efficiency and miniaturization. By adopting advanced packaging technology, FC-LGA packaging substrates will continue to play an important role in the electronics industry, providing reliable solutions for a variety of complex and demanding applications.
FC-LGA Package Substrates design Reference Guide.
When designing an FC-LGA (Flip-Chip Land Grid Array) พื้นผิวบรรจุภัณฑ์, multiple key factors need to be carefully considered to ensure that its performance and reliability can meet the needs of high-end applications. The following are several aspects that require special attention when designing:
Layout design
Layout design is the basis for FC-LGA package substrate design. Ensuring that the connection between the chip and the substrate is as short as possible is critical to reducing signal delays and losses. Short connections can not only increase signal transmission speed, but also reduce energy loss during transmission. นอกจากนี้, layout design also needs to take into account the uniformity and symmetry of wiring to avoid delay differences caused by inconsistent lengths of signal paths. This is especially important in high-frequency applications, where any minor inconsistencies can cause signal integrity issues.
Material selection
The choice of materials directly affects the electrical and thermal properties of the substrate. Commonly used substrate materials include BT resin (Bismaleimide-Triazine Resin) and ceramic substrates. BT resin has excellent electrical and mechanical properties and is suitable for high-frequency applications; while ceramic substrates have excellent thermal conductivity and stability and are suitable for high-power and high-temperature environments. Choosing the right materials can ensure that the substrate can still operate stably under harsh operating conditions. นอกจากนี้, the coefficient of thermal expansion (CTE) of the substrate material also needs to be considered to ensure that it matches the CTE of the chip material to reduce stress generated during thermal cycling.
Thermal design
As chip power density increases, thermal design becomes even more important. Effective heat dissipation path design can significantly improve the reliability and life of the chip. When designing the FC-LGA package substrate, you should consider using materials with good thermal conductivity, such as copper or aluminum, as heat dissipation channels. นอกจากนี้, the heat dissipation effect can be enhanced by adding heat dissipation holes or heat sinks. For high-power applications, you can also consider using active cooling methods, such as fans or liquid cooling systems, to further improve cooling capabilities.
Power and ground planes
The design of power and ground planes is critical to reducing electromagnetic interference (EMI) and power supply noise. ในระหว่างกระบวนการออกแบบ, ensure that power and ground planes cover the entire substrate to provide good electrical connections and shielding. Multi-layer substrate design can further optimize the power and ground plane layout by adding power and ground planes between different layers to form multi-point grounding and reduce power supply noise. นอกจากนี้, attention should also be paid to the isolation between power supply and signal to avoid the impact of power supply noise on signal integrity.
สรุป, designing the FC-LGA packaging substrate requires comprehensive consideration of many factors such as layout design, การเลือกวัสดุ, การออกแบบการกระจายความร้อน, and power and ground plane layout. By optimizing these design elements, the performance and reliability of FC-LGA packaging substrates can be effectively improved to meet the strict requirements of high-end applications. In the actual design process, the design plan needs to be continuously adjusted and optimized based on specific application needs to achieve the best results.
What material is used in FC-LGA Package Substrates?
In FC-LGA (Flip-Chip Land Grid Array) พื้นผิวบรรจุภัณฑ์, choosing the right material is a key factor to ensure its performance and reliability. The following are several commonly used FC-LGA packaging substrate materials, each of which has unique properties to meet different application needs.
BT resin (Bismaleimide-Triazine Resin)
BT resin is a substrate material commonly used in high-frequency applications and has excellent electrical and mechanical properties. Its main features include:
Excellent electrical properties:BT resin has a low dielectric constant and small dielectric loss, which allows it to effectively reduce signal loss and interference in high-frequency environments, thereby improving the overall performance of the circuit.
High mechanical strength:BT resin has high flexural strength and tensile strength and can withstand large mechanical stress, which is particularly important in multi-layer substrates.
Good heat resistance:BT resin maintains stable performance in high-temperature environments and is suitable for applications requiring high heat resistance, such as high-frequency circuits in computing and communication equipment.
Ceramic substrate
Ceramic substrates are ideal for high power and high temperature environments due to their excellent thermal conductivity and stability. Its main features include:
Extremely high thermal conductivity:Ceramic materials such as aluminum oxide (Al2O3) and aluminum nitride (AlN) have extremely high thermal conductivity and can quickly dissipate heat to prevent chip damage due to overheating. This is especially important for high power applications.
Excellent stability:Ceramic substrates have high chemical stability and mechanical strength, can maintain stable performance for a long time in harsh environments, and are not susceptible to moisture or oxidation.
Good electrical insulation properties:The electrical insulation properties of ceramic materials are very superior, which can effectively prevent short circuits and leakage in the circuit and improve the reliability of the entire package.
Copper
As a conductive layer material, copper plays a vital role in the FC-LGA packaging substrate. Its main features include:
Excellent electrical conductivity:Copper has extremely high conductivity, allowing signals to be transmitted quickly on the substrate, reducing signal delay and improving the overall performance of the circuit.
High thermal conductivity:The thermal conductivity of copper is also very high, which can effectively dissipate heat and maintain the stability of the chip during high-performance operation. This is especially critical for high frequency and high power applications.
Good processability:Copper materials are easy to process and can be etched with fine circuit patterns to meet the needs of complex circuit designs. นอกจากนี้, the surface of copper can be plated, such as gold or silver, to further improve the reliability and corrosion resistance of its electrical connections.
When selecting FC-LGA packaging substrate materials, it is necessary to comprehensively consider various factors such as electrical properties, mechanical properties, thermal conductivity, and application environment. BT resin, ceramic substrate and copper each have their own advantages and can meet the needs of different application scenarios. BT resin is suitable for high-frequency circuit applications, ceramic substrates are suitable for high-power and high-temperature environments, and copper provides excellent electrical and thermal conductivity. The reasonable combination and application of these materials can not only improve the overall performance of the packaging substrate, but also extend its service life and ensure the reliability and stability of electronic equipment.
What size are FC-LGA Package Substrates?
The size of the FC-LGA packaging substrate is a crucial consideration for different application fields and specific needs. It not only affects the performance and stability of the equipment, but is also directly related to the overall size and appearance design of the equipment. Here is a more detailed discussion of FC-LGA package substrate dimensions:
The size of the FC-LGA packaging substrate can be customized according to specific application requirements. Common ones include:
Standard size
Standard size FC-LGA packaging substrates are usually used in general electronic equipment, such as computers, อุปกรณ์สื่อสาร, ฯลฯ. The dimensions of these package substrates typically follow industry standards, such as ATX (12 × 9.6 inches) or MicroATX (9.6 × 9.6 inches), to ensure compatibility with a variety of devices and systems. The standard size FC-LGA packaging substrate is designed to focus on versatility and standardization to meet the needs of most application scenarios.
Custom size
Custom-sized FC-LGA packaging substrates are more designed and customized according to specific application requirements. These applications may include high-end servers, high-performance computing equipment, specialized equipment for specific industries, ฯลฯ. In these applications, higher computing power, larger memory capacity, or more input and output interfaces are usually required, so custom-sized packaging substrates are required to meet these needs. The size of these package substrates may vary depending on application requirements and may be larger and thicker to accommodate more components or provide more space for heat dissipation.
Custom-sized FC-LGA packaging substrates generally require more engineering resources and cost investment in design and manufacturing, but they can provide higher performance and reliability, as well as better adaptability to specific application scenarios.
The size of the FC-LGA packaging substrate is not only a technical parameter, but also an important factor closely related to the performance, stability and appearance design of the device. By choosing the appropriate size, the actual needs of the equipment can be better met and the performance and reliability of the equipment can be improved. เพราะฉะนั้น, when designing and selecting FC-LGA packaging substrates, it is necessary to comprehensively consider factors such as application scenarios, performance requirements, and cost to ensure that the most appropriate size and specifications are selected.
The Manufacturer Process of FC-LGA Package Substrates.
The manufacturing process of FC-LGA packaging substrate is a complex and precise process that requires multiple key steps to ensure the quality and reliability of the final product.
ที่หนึ่ง, design is the foundation of the entire manufacturing process. Depending on the application requirements, engineers must design appropriate substrate layouts and circuit diagrams. This includes determining where and how the chip will be connected, as well as designing the traces and connection points on the circuit board. The quality of the design directly affects the efficiency and accuracy of subsequent manufacturing and testing.
Next comes the process of fabricating the substrate. Use high-precision processes such as chemical etching and laser cutting to convert the designed circuit diagram into an actual substrate. In this process, material and process parameters need to be strictly controlled to ensure that the geometry and size of the substrate meet the design requirements, and the surface is smooth and flat for subsequent chip connection work.
Chip connection is a critical part of the manufacturing process. Using flip-chip technology, the bare chip is precisely connected to the substrate. This requires high-precision equipment and technology to ensure the quality and stability of the connection between the chip and the substrate. During this process, precise alignment and welding work is also required to ensure that each chip can be correctly connected to the corresponding position on the substrate.
ในที่สุด, there is the packaging and testing stage. ในขั้นตอนนี้, the manufacturer performs functional and reliability testing on the connected chip to ensure that the package quality and performance meet requirements. This includes checking circuit connectivity, testing the chip’s power consumption and performance parameters, and conducting temperature and environmental stress testing. Only by passing strict testing can we ensure that the quality and reliability of the FC-LGA packaging substrate reaches the expected level.
โดยทั่วไป, the manufacturing process of FC-LGA packaging substrate is a precise and complex process that requires highly professional technology and strict quality control to ensure that the performance and reliability of the final product meet the requirements.
The Application area of FC-LGA Package Substrates.
FC-LGA packaging substrate is an advanced packaging technology that is widely used in various fields. The following are the applications of FC-LGA packaging substrates in different fields:
High performance computing
In the field of high-performance computing, such as servers and supercomputers, FC-LGA packaging substrates play a vital role. These applications have extremely high requirements for processing large-scale data and complex computing tasks, requiring high computing power and high data transfer rates. FC-LGA packaging substrate provides excellent performance and stability to support these demanding applications.
Communication device
FC-LGA packaging substrates are also widely used in communication equipment, especially in equipment such as 5G base stations and high-speed routers. These devices need to handle large amounts of high-frequency signals and maintain stable performance. FC-LGA packaging substrate has become an ideal choice for these communication devices through its high-frequency signal processing capabilities and stability.
Consumer Electronics
ในด้านอุปกรณ์อิเล็กทรอนิกส์สําหรับผู้บริโภค, such as high-end smartphones and tablets, FC-LGA packaging substrates also have important applications. As the performance and functional requirements of consumer electronics products continue to increase, higher integration and smaller size are required. FC-LGA packaging substrate can achieve high integration and miniaturization while maintaining good performance and stability, so it has become the preferred packaging method for these consumer electronics products.
โดยทั่วไป, FC-LGA packaging substrates are widely used in high-performance computing, อุปกรณ์สื่อสาร, consumer electronics and other fields. Its superior performance, stability and miniaturization make it an ideal choice for a variety of demanding applications. With the continuous advancement of technology and the expansion of application scope, FC-LGA packaging substrates will continue to play an important role in the future, promoting development and innovation in various fields.
What are the advantages of FC-LGA Package Substrates?
As an advanced packaging technology, FC-LGA packaging substrate stands out among many advantages. The following is a detailed description of its main advantages:
high performance
FC-LGA packaging substrate can easily cope with high frequency and high data rate application requirements. Its design uses flip-chip technology, which makes the connection between the chip and the substrate closer and the signal transmission path shorter, thereby reducing signal delay and loss. This design feature makes the FC-LGA packaging substrate outstanding in fields such as high-performance computing and high-speed communications.
High reliability
The FC-LGA packaging substrate uses advanced manufacturing processes and materials, such as high-quality BT resin or ceramic substrates, and excellent conductive copper layers to ensure its long-term stable operation. นอกจากนี้, flip-chip technology can provide a more stable connection and reduce the risk of failure caused by temperature changes or mechanical vibration, so it is favored in application scenarios with high reliability requirements.
Good heat dissipation performance
Due to the reasonable design of the FC-LGA packaging substrate, effective heat dissipation paths can ensure that the chip maintains stability during high-power operation. The flip-chip connection method allows the back of the chip to be in direct contact with the substrate, effectively promoting heat conduction. ในเวลาเดียวกัน, the design usually includes structures such as heat dissipation holes and heat dissipation layers to enhance the heat dissipation effect. This advantage allows the FC-LGA packaging substrate to perform well in high power density and high temperature environments.
Miniaturization
The FC-LGA packaging substrate has a compact design and is suitable for high integration and miniaturization application requirements. The flip-chip structure makes the entire package flatter, making the device smaller and lighter. This miniaturization feature makes FC-LGA packaging substrates have broad application prospects under the trend of thinning, lightness, and portability, especially in the field of consumer electronics, เช่นสมาร์ทโฟน, แท็บ เล็ต, and other products.
โดยสรุป, FC-LGA packaging substrate has become the preferred packaging method for many high-end electronic products due to its high performance, high reliability, good heat dissipation performance and miniaturization, providing technology development and innovation in various industries. reliable support.
คำถามที่ถามบ่อย
What are the advantages of FC-LGA packaging substrate compared with other packaging methods?
FC-LGA packaging substrate has several significant advantages compared to other packaging methods. ที่หนึ่ง, it uses flip-chip technology, which allows the chip to be directly connected to the substrate, reducing the connection distance and signal transmission delay, thereby improving electrical performance. ประการ, the FC-LGA packaging substrate has better heat dissipation performance. By designing effective heat dissipation paths, it can effectively conduct heat to the external environment and ensure the stability of the chip during high-power operation. นอกจากนี้, the FC-LGA packaging substrate also has the advantages of high reliability and miniaturization, and is suitable for various high-performance and miniaturization application scenarios.
Is the manufacturing cost of FC-LGA packaging substrate high?
เมื่อเทียบกับเทคโนโลยีบรรจุภัณฑ์แบบดั้งเดิม, the manufacturing cost of FC-LGA packaging substrate is usually slightly higher. This is because FC-LGA packaging substrates require the use of advanced manufacturing processes and materials, such as flip-chip technology and high-performance substrate materials, to ensure high performance and reliability. อย่างไรก็ตาม, with the continuous advancement of technology and continuous competition in the market, the manufacturing cost of FC-LGA packaging substrates has been gradually reduced, and more companies and manufacturers are constantly promoting the development and popularization of this technology.
What applications are FC-LGA packaging substrates suitable for?
FC-LGA packaging substrate is suitable for a range of applications requiring high performance, high frequency and high heat dissipation requirements. เช่น, in the field of high-performance computing, such as servers and supercomputers, which need to process large amounts of data and complex computing tasks, FC-LGA packaging substrates can provide sufficient computing power and data transmission rates. ในด้านอุปกรณ์สื่อสาร, such as 5G base stations and high-speed routers, high-frequency signals and stable communication connections need to be processed, and FC-LGA packaging substrates can meet these requirements. นอกจากนี้, in the field of consumer electronics, such as high-end smartphones and tablets, which require high integration and miniaturization, FC-LGA packaging substrates can also provide suitable solutions.