What are Ultra-Multilayer BGA Substrates?
Ultra-Multilayer BGA Substrates Manufacturer.”Ultra-Multilayer BGA Substrates Manufacturer” refers to a company specializing in the production of advanced Ball Grid Array (BGA) substrates with multiple layers.
A super multi-layer BGA substrate is a complex printed circuit board (Печатная плата) designed to support ball grid array (BGA) packaged electronic components. This type of substrate enables higher component density and more complex circuit designs through a staggered combination of multiple layers of conductive copper and insulating materials, making it suitable for advanced electronic devices and high-performance applications.
Первый, understanding the basics of BGA packaging is key. BGA (Ball Grid Array) packaging is a surface mount packaging technology that achieves electrical connection by distributing multiple solder balls on the bottom of the device. Compared with traditional lead frame packaging, BGA packaging has better thermal and electrical performance and takes up less space.
In order to meet the needs of BGA packaging, ultra-multilayer BGA substrates are usually composed of multiple layers of conductive copper and insulating materials. Conductive copper layers are used to form circuit paths, while layers of insulating material separate and support the conductive layers, avoiding electrical shorts and providing mechanical strength. Common insulation materials include FR4 (fiberglass reinforced epoxy) and polyimide, which have excellent electrical insulation properties and heat resistance to meet the needs of high-performance applications.
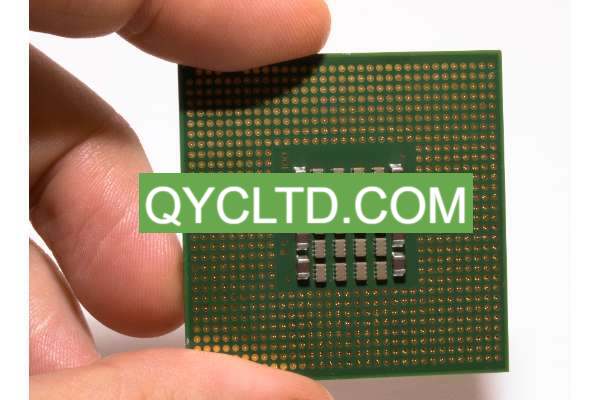
Ultra-Multilayer BGA Substrates Manufacturer
The design and manufacturing process of ultra-multilayer BGA substrates is very complex and requires highly precise processes and advanced technology. Первый, the layout and wiring planning of the substrate are carried out according to the design requirements. Then, conductive and insulating layers are built layer by layer through processes such as photolithography, etching, and electroplating. In order to ensure the reliability of electrical connections, drilling and hole filling processes are also required to achieve conductive connections between different layers.
In practical applications, ultra-multilayer BGA substrates are widely used in various high-performance electronic devices and systems. Например, in consumer electronics such as smartphones and tablets, ultra-multilayer BGA substrates can accommodate more functional modules and complex circuit designs, achieving higher performance and smaller size. В дополнение, in high-end computing equipment such as communication equipment and data center servers, ultra-multilayer BGA substrates support high-speed data transmission and high-performance computing by optimizing electrical performance and heat dissipation performance.
Вообще, ultra-multilayer BGA substrate is an advanced printed circuit board technology that achieves higher component density and more complex circuit design through the ingenious combination of multiple layers of conductive and insulating materials. Its excellent performance and wide range of applications make it an indispensable key component in modern electronic equipment. Through continuous technological innovation and process improvement, ultra-multilayer BGA substrates will continue to promote the development of electronic technology and meet the growing needs for high performance and miniaturization.
Ultra-Multilayer BGA Substrates design Reference Guide.
The Ultra-Multilayer BGA Substrate Design Reference Guide is a comprehensive manual tailored for engineers and designers to guide them in achieving efficient and reliable substrate design in complex electronic design environments. This guide covers key areas including design rules, best practices, software tools, and necessary technologies.
In ultra-multilayer BGA substrate design, design rules are the basis for ensuring circuit function and reliability. These rules cover aspects such as circuit layout, signal integrity, power distribution, thermal management, и так далее., to maximize circuit performance and reduce the risk of electromagnetic interference and signal distortion through reasonable layout and wire planning.
The best practices section highlights key strategies for optimizing designs at different stages. From initial concept to detailed design, and subsequent verification and adjustments, there are specific suggestions and techniques to help designers maintain high efficiency and quality throughout the project cycle.
Software tools play a vital role in ultra-multilayer BGA substrate design. Advanced CAD tools and simulation software can not only support complex layout and stack-up designs, but also predict and solve potential design problems, improving design accuracy and reliability.
In addition to tools and rules, the guidelines cover required techniques such as material selection, lamination processes, welding techniques and testing methods. These techniques require designers to have a deep understanding of the material’s electrical properties, thermal characteristics, and challenges that may be encountered during manufacturing to ensure that the final product meets expected quality standards.
Резюме, the Ultra-Multilayer BGA Substrate Design Reference Guide provides engineers and designers with the key tools to successfully design and produce substrates in a highly complex and competitive market through a systematic approach and detailed guidance. It is not only a support for technological innovation, but also an important guarantee for improving product competitiveness and market share.
What material is used in Ultra-Multilayer BGA Substrates?
Material selection for ultra-multilayer BGA substrates is critical to its performance and reliability. These substrates often use a variety of advanced materials to meet different application needs and performance requirements.
Прежде всего, FR4 material is the most common substrate in ultra-multilayer BGA substrates. FR4 is a fiberglass-reinforced epoxy laminate favored for its excellent electrical insulation properties and mechanical strength. The dielectric constant of FR4 material is stable and can maintain good electrical properties over a wide frequency range. В дополнение, FR4 has high heat resistance and moisture resistance, can remain stable in harsh environments, and is suitable for various electronic equipment applications.
For applications that require flexibility, polyimide materials may be used for ultra-multilayer BGA substrates. Polyimide has excellent thermal stability and mechanical flexibility, making it suitable for use in circuit designs that require bending and folding. This material not only remains stable in high-temperature environments, but can also withstand repeated bending without damage and is widely used in flexible electronics and wearable devices.
В дополнение, in order to enhance the thermal conductivity of the substrate, ultra-multilayer BGA substrates may also use ceramic fillers and other thermal conductive materials in combination. These materials effectively dissipate heat, preventing electronic components from overheating and improving overall system reliability and performance.
In high-frequency applications, materials with low dielectric constant and low dissipation factor may be chosen, such as PTFE (polytetrafluoroethylene) or modified epoxy resins. These materials can maintain low loss in high-frequency signal transmission, ensuring signal integrity and transmission speed, and are suitable for high-speed data communications and radio frequency applications.
In order to improve the durability and performance of the circuit board, multi-layer copper foil may also be used in the ultra-multi-layer BGA substrate. Multilayer copper foil provides higher electrical conductivity and current carrying capabilities for applications requiring high power transmission.
In short, the material selection for ultra-multilayer BGA substrates is diverse and complex, and the appropriate material combination needs to be selected according to specific application requirements. FR4 and polyimide are the most commonly used materials, providing excellent electrical properties and mechanical flexibility respectively. Combined with the use of thermally conductive materials and high-frequency materials, the overall performance of the substrate can be significantly improved to meet the needs of different electronic devices. By properly selecting and matching these materials, ultra-multilayer BGA substrates can demonstrate excellent performance and reliability in various applications.
What size are Ultra-Multilayer BGA Substrates?
The size of ultra-multilayer BGA substrates varies depending on the specific application, meeting a variety of needs from small portable devices to large industrial equipment. Different application scenarios have different size requirements for the substrate, which determines its flexibility and versatility in actual use.
In the field of consumer electronics, such as smartphones and wearable devices, small ultra-multilayer BGA substrates are particularly important. These devices require a high degree of integration and compact layout of electronic components and circuits to ensure the device is lightweight and portable. The internal space of smartphones is limited and the substrate needs to be as small as possible to accommodate various complex functional modules, such as processors, memory, cameras and sensors. Therefore, the size of ultra-multilayer BGA substrates is usually only a few square centimeters, and the thickness is strictly controlled to ensure a slim design of the device.
On the contrary, in the fields of industrial equipment and power electronics, the size of ultra-multilayer BGA substrates can be much larger. These devices are often not limited by space, but instead need to handle higher power loads and more complex circuit designs. Например, in industrial control systems, server motherboards and large communication equipment, the size of the substrate can reach tens of square centimeters or even larger to accommodate a large number of electronic components and complex circuit wiring. These substrates not only need to support multi-layer circuit designs, but also need to have good heat dissipation performance and mechanical strength to cope with harsh working environments and long-term high-load operation.
В дополнение, in high-reliability fields such as automotive electronics and aerospace, the size design of ultra-multilayer BGA substrates also needs to take into account specific technical requirements and application environments. Automotive electronic systems require substrates that can withstand harsh conditions such as high temperature and high vibration, and they also need to be miniaturized to fit into the limited installation space in the car. Similarly, substrates in aerospace equipment need to be highly reliable and immune to interference, while being precisely dimensioned to meet tight space constraints and weight controls.
Резюме, the size design of ultra-multilayer BGA substrates is a complex and critical process that requires comprehensive consideration of factors such as the needs of specific applications, the size of electronic components, and the available space within the device. Whether it is a small consumer electronic device or a large industrial and power electronic device, appropriate substrate size design can not only improve the performance and reliability of the device, but also effectively optimize space utilization and promote the continuous progress and innovation of electronic technology.
The Manufacturer Process of Ultra-Multilayer BGA Substrates.
The manufacturing process of ultra-multilayer BGA substrates is complex and delicate, involving multiple steps to ensure that each layer and component fits together accurately. The following are the main manufacturing steps:
Substrate preparation: The manufacturing process begins with substrate preparation, typically using high-performance materials such as FR4. These substrate materials provide the necessary mechanical strength and electrical insulation. The preparation process includes cutting and cleaning the substrate to ensure there are no impurities or dirt.
Copper Layer Deposition: Следующий, a thin layer of copper foil is deposited on the substrate. This step is usually accomplished by chemical deposition or electroplating methods to form a conductive layer. These copper layers will serve as the basis for subsequent circuit patterns.
Photoresist application and exposure: Apply a layer of photoresist (photosensitive material) over the copper layer. A circuit pattern is projected onto the photoresist through a mask, and exposure causes the photoresist to chemically change in specific areas. The unexposed portions are then removed with a developer, leaving behind the circuit pattern that needs to be preserved.
Офорт: The etching process uses chemical reagents to remove the copper layer not covered by photoresist, leaving only the copper pattern in the protected area. This step accurately creates circuit wires and connections.
Сверление: The drilling step creates vias and socket holes on the substrate to connect electrical signals between different layers. These holes are typically made using a laser or mechanical drill press, ensuring high precision and consistency.
Lay-up and Lamination: To build a multi-layer substrate, multiple prefabricated layers are stacked together and laminated into a single unit using heat and pressure. This process ensures a strong bond and electrical connection between each layer.
Component Placement: After completion of stacking and lamination, the component placement process begins. Electronic components are placed precisely at designated locations on a substrate using automated equipment. This step relies heavily on surface mount technology (SMT) to ensure high density and high precision component placement.
Soldering: The soldering process securely fastens components to the substrate, ensuring a reliable electrical connection. Commonly used methods include reflow soldering and wave soldering, suitable for different types of components and design requirements.
Testing: Наконец, the manufactured substrate undergoes rigorous testing to ensure that all electrical connections and functionality meet design specifications. Testing includes electrical performance testing, functional testing and environmental stability testing to ensure product quality and reliability.
According to design requirements, ultra-multilayer BGA substrates will also use advanced processes such as through-hole mounting to meet specific application needs. The entire manufacturing process requires precise control and high standards of quality management to ensure the performance and reliability of the final product. The comprehensive application of these steps enables ultra-multilayer BGA substrates to play a vital role in modern electronic devices, supporting the implementation of high-performance and complex circuits.
The Application area of Ultra-Multilayer BGA Substrates.
Ultra-multilayer BGA substrates occupy an indispensable position in the modern electronics industry and are widely used in various industries, including consumer electronics, communications, automobiles, aerospace, медицинское оборудование, and industrial automation. Its excellent performance and highly integrated design make it a core component of various high-end devices.
In the field of consumer electronics, ultra-multilayer BGA substrates are widely used in devices such as smartphones, tablets, laptops, and smart watches. These devices require highly integrated circuits to achieve complex functions and miniaturized designs. The multi-layer design of the ultra-multi-layer BGA substrate can provide more electrical connections, support more complex functions, and ensure high performance and reliability of the device.
In the communications industry, ultra-multilayer BGA substrates are used in key components such as network equipment, routers, switches, and base stations. These devices need to process large amounts of data and require high-speed signal transmission and high reliability. The ultra-multilayer BGA substrate can meet these needs and ensure stable operation of the equipment through its excellent electrical performance and thermal management capabilities.
The automotive industry has extremely high requirements for the reliability and durability of electronic equipment. Ultra-multilayer BGA substrates are used in automotive electronic control units (ECUs), advanced driver assistance systems (АДАС) and in-vehicle entertainment systems. Its high heat resistance and strong electrical performance make it perform well in harsh automotive environments, ensuring the safety and reliability of vehicle electronic systems.
In the aerospace field, ultra-multilayer BGA substrates are used in navigation systems, communication systems and control systems for satellites, spacecraft and aircraft. Aerospace equipment needs to work in extreme environments and has extremely high requirements on circuit boards. The ultra-multilayer BGA substrate ensures the reliable operation of these high-value devices with its high-density integration and excellent anti-interference capabilities.
The medical device industry has strict standards for the stability and accuracy of electronic components. Ultra-multilayer BGA substrates are widely used in high-precision medical instruments such as pacemakers, CT scanners, and MRI equipment. Its highly reliable and precise circuit design ensures the accuracy and safety of medical equipment.
In the field of industrial automation, ultra-multilayer BGA substrates are used in programmable logic controllers (PLC), industrial robots and automated production line control systems. These systems require highly reliable electronic controls for efficient and precise operation. The ultra-multilayer BGA substrate meets the needs of industrial automation for stability and high performance with its powerful processing capabilities and durability.
In short, the wide application of ultra-multilayer BGA substrates not only improves the performance and reliability of equipment in various industries, but also promotes technological progress and innovation. Its wide range of applications in different fields fully reflects its core position and importance in modern electronic technology.
What are the advantages of Ultra-Multilayer BGA Substrates?
Ultra-Multilayer BGA Substrates have many significant advantages over other wiring methods, making them occupy an important position in modern electronic equipment.
The ultra-multilayer design allows for a more compact layout, making it possible to miniaturize electronic devices. By routing wiring on multiple levels, engineers can integrate more electronic components into a limited space. This design is particularly suitable for advanced devices that require high-density components and complex circuits, such as smartphones, tablets, and wearable devices, greatly optimizing space utilization.
The ultra-multilayer BGA substrate adopts a standardized manufacturing process to ensure the stability of quality and reliability. The wiring and electrical connections at each level are strictly controlled and tested, reducing the risk of short circuits and open circuits. Its high reliability makes it widely used in fields requiring high precision and stability, such as aerospace and medical equipment.
The automated assembly process simplifies production, reduces labor costs, and increases efficiency. The ultra-multilayer BGA substrate design takes into account the needs of modern automated production lines, making the welding and installation of components more efficient and accurate. This level of automation not only reduces human error, but also significantly increases production speed, making mass production possible.
Ultra-multilayer BGA substrates can be designed according to specific requirements, including complex circuits and component integration. Whether it is high-frequency signal transmission, thermal management or electromagnetic compatibility, ultra-multilayer BGA substrates can meet specific application needs through customized designs. This flexibility makes them excellent in a variety of application scenarios, from high-performance computing to advanced communications equipment, providing optimal solutions.
Mass production reduces unit costs, making it economical to manufacture at large scale. Although the initial design and development costs may be higher, the cost benefits of ultra-multilayer BGA substrates become apparent once they enter the mass production stage. The economics of high-volume production make it ideal for consumer electronics and industrial applications, while also promoting the popularity and development of the technology.
Полный, ultra-multilayer BGA substrates have become key components in the design and manufacturing of modern electronic products due to their compactness, reliability, ease of assembly, customizability, and cost-effectiveness. As technology continues to advance, these advantages will be further enhanced, promoting continued innovation and development in the electronics industry.
Вопросы и ответы
What is a super multi-layer BGA substrate?
A super multilayer BGA substrate is a complex printed circuit board (Печатная плата) whose structure contains multiple layers of conductive copper and insulating materials. They are designed to support high-density ball grid array (BGA) packaging for electronic devices requiring complex circuitry and high-performance requirements.
What are the main advantages of ultra-multilayer BGA substrate?
Ultra-multilayer BGA substrates have higher component density and more compact design than traditional single-layer or double-layer PCBs, enabling miniaturization and lightweighting of equipment. В дополнение, their standardized manufacturing process ensures reliability and consistent quality while supporting highly customized design needs for a variety of complex electronic applications.
What is the manufacturing process of super multi-layer BGA substrate?
Manufacturing ultra-multilayer BGA substrates involves several key steps: from substrate preparation and deposition of conductive copper layers, to photoresist application and etching, to drilling, precise placement of components and final soldering and testing. These processes require sophisticated equipment and technology to ensure high quality and reliability.
In what fields are ultra-multilayer BGA substrates widely used?
Ultra-multilayer BGA substrates are widely used in many industries such as consumer electronics, communication equipment, Автомобильная электроника, aerospace, медицинское оборудование, and industrial automation. They are able to meet complex circuit requirements and support high-frequency and high-speed transmission, so they occupy an important position in modern high-performance devices.