Rogers Circuit Board Manufacturer.”Rogers Circuit Board Manufacturer specializes in producing high-quality circuit boards using advanced Rogers materials. With expertise in custom designs and precision manufacturing, we ensure reliable performance and durability for diverse electronic applications.”
In the rapidly advancing world of electronics, Rogers circuit boards stand out for their высокочастотный performance and reliability. These specialized circuit boards, crafted from Rogers materials, are known for their exceptional dielectric properties and thermal management, making them ideal for applications where signal integrity is paramount. This article delves into various aspects of Rogers circuit boards, including their definition, design guidelines, материалы, sizes, manufacturing process, application areas, advantages, and frequently asked questions. This comprehensive overview aims to provide readers with a deep understanding of what makes Rogers circuit boards a preferred choice in high-frequency and high-performance electronic applications.
What is Rogers Circuit Board?
Rogers circuit boards are a type of high-frequency printed circuit board (Печатная плата) made from materials manufactured by Rogers Corporation. Known for their superior dielectric properties, these materials provide excellent signal integrity and thermal management, making them ideal for high-frequency applications such as radio frequency (RF) and microwave circuits. Unlike conventional FR4 boards, Rogers circuit boards are engineered to handle higher frequencies and provide more consistent performance across a wide range of environmental conditions.
One of the key characteristics of Rogers circuit boards is their low dielectric constant (Dk) and low dissipation factor (Df). These properties ensure minimal signal loss and distortion, which are critical for high-speed and high-frequency applications. The low Dk value helps in maintaining signal speed, while the low Df minimizes energy loss as heat, ensuring the board remains cool during operation. This combination of properties results in reliable and efficient performance, even in demanding applications.
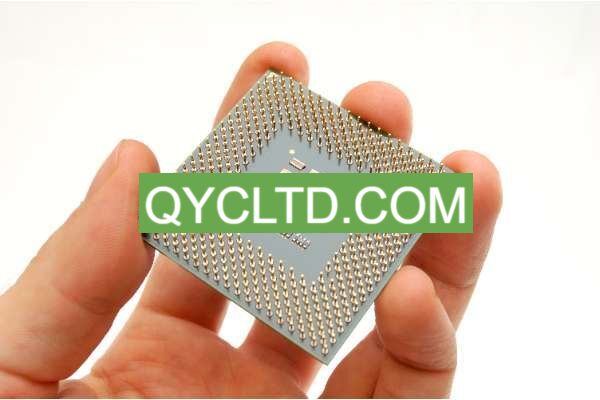
Rogers Circuit Board Manufacturer
Rogers circuit boards also offer excellent thermal management, thanks to their high thermal conductivity. This is particularly important in high-power applications where heat dissipation is crucial to maintain the reliability and longevity of the electronic components. The materials used in Rogers circuit boards can withstand higher temperatures compared to traditional PCB materials, reducing the risk of thermal-related failures.
Moreover, Rogers circuit boards exhibit outstanding dimensional stability. This means that they maintain their structural integrity and electrical properties even under varying environmental conditions, such as changes in temperature and humidity. This stability is essential for applications that require precise and consistent performance over time, such as aerospace and defense systems.
The versatility of Rogers circuit boards extends to their compatibility with various fabrication processes. They can be easily integrated into existing manufacturing workflows, allowing for seamless production without the need for significant modifications. This makes them an attractive option for manufacturers looking to upgrade their products’ performance without overhauling their production lines.
Rogers Circuit Board Design Reference Guide
Designing Rogers circuit boards requires a thorough understanding of the specific properties and requirements of the materials used. This involves several critical steps, from material selection to final testing, ensuring the board meets the desired performance criteria.
The first step in designing a Rogers circuit board is selecting the appropriate Rogers material based on the application’s requirements. Rogers offers a variety of materials, each with specific dielectric properties, thermal conductivities, and mechanical strengths. Commonly used materials include RO4000, RO3000, and RT/duroid series, each tailored for different high-frequency and high-power applications. The choice of material depends on factors such as the operating frequency, power handling capability, and environmental conditions the board will be exposed to.
Designing the layer stack-up is crucial for maintaining signal integrity and minimizing interference. The stack-up configuration, including the number of signal layers, ground planes, and power planes, affects the board’s electrical performance. Rogers materials allow for complex multilayer designs, enabling the integration of various circuit functions on a single board. Proper stack-up design ensures controlled impedance, reduced crosstalk, and efficient power distribution, which are essential for high-frequency applications.
Резюме, designing Rogers circuit boards involves a comprehensive approach that addresses material selection, impedance control, thermal management, signal integrity, and fabrication considerations. By following these guidelines and leveraging the unique properties of Rogers materials, designers can create high-performance, reliable PCBs for a wide range of high-frequency applications.
What Material is Used in Rogers Circuit Boards?
Rogers circuit boards are renowned for their use of advanced materials that offer superior dielectric properties, thermal management, and mechanical stability. These materials are specifically engineered to meet the stringent requirements of high-frequency and high-power applications.
One of the most commonly used materials in Rogers circuit boards is the RO4000 series. This material offers excellent high-frequency performance with a low dielectric constant (Dk) and low dissipation factor (Df). The RO4000 series is known for its stability over a wide range of temperatures, making it ideal for applications where environmental conditions may vary. Its high thermal conductivity ensures efficient heat dissipation, which is crucial for maintaining reliability in high-power applications.
The RO3000 series is another popular choice, particularly for applications that require low loss and high thermal conductivity. This series includes materials with a dielectric constant as low as 3.0, which helps in maintaining signal integrity at high frequencies. The RO3000 materials are also known for their low coefficient of thermal expansion (CTE), which matches well with copper, reducing the risk of delamination and improving the longevity of the board.
The RT/duroid series is highly regarded for its exceptional dielectric properties and mechanical robustness. These materials are often used in aerospace and defense applications, where reliability and performance are critical. The RT/duroid series offers a range of dielectric constants, allowing designers to choose the best material for their specific application needs. Its low outgassing properties make it suitable for use in vacuum environments, further expanding its range of applications.
The combination of these advanced materials in Rogers circuit boards ensures that they meet the high-performance, reliability, and thermal management requirements of modern electronic applications. By carefully selecting the appropriate materials based on the specific needs of the application, designers can leverage the unique properties of Rogers materials to create high-performance PCBs that excel in demanding environments.
What Size are Rogers Circuit Boards?
Rogers circuit boards are available in various sizes, tailored to the specific requirements of different applications. The size of a Rogers circuit board is determined by several factors, including the dimensions of the electronic components, the complexity of the circuit,the operating frequency, and the overall design requirements. Understanding these factors is crucial for selecting the appropriate board size for a given application.
The operating frequency of the application also plays a significant role in determining the size of the Rogers circuit board. High-frequency signals require precise impedance control and minimal signal loss, which can influence the trace widths, интервал, and overall board layout. Rogers materials’ consistent dielectric properties help in achieving the desired electrical performance, but the board size must be optimized to maintain signal integrity at high frequencies. This often involves balancing the need for compactness with the electrical requirements of the application.
Effective thermal management is crucial for high-power applications, and it can influence the size of the Rogers circuit board. Larger board sizes may be necessary to incorporate thermal vias, Радиаторы, и другие механизмы охлаждения для эффективного рассеивания тепла. The high thermal conductivity of Rogers materials helps in managing heat distribution, but the board’s physical dimensions must be designed to accommodate these thermal management features without compromising performance.
The fabrication process also imposes certain constraints on the size of Rogers circuit boards. Factors such as panel size, drilling capabilities, and lamination processes can impact the maximum and minimum board dimensions that can be produced. Understanding these constraints and working closely with the fabricator can help in designing a board size that is both manufacturable and meets the application’s performance requirements.
Резюме, the size of Rogers circuit boards is influenced by a combination of factors, including component size and density, circuit complexity, operating frequency, thermal management, application-specific requirements, and fabrication constraints. By carefully considering these factors, designers can select the appropriate board size that meets the performance, reliability, and cost requirements of their specific application.
The Manufacturing Process of Rogers Circuit Boards
The manufacturing process of Rogers circuit boards involves several critical steps, each of which is essential for ensuring the high performance and reliability of the final product. This process includes material preparation, layer stacking, drilling, plating, imaging, etching, solder masking, surface finishing, and testing. Each step must be carefully controlled and executed to meet the stringent requirements of high-frequency and high-power applications.
The first step in the manufacturing process is preparing the Rogers materials. This involves selecting the appropriate Rogers laminate based on the specific requirements of the application. The laminate sheets are typically pre-cut to the desired size and inspected for any defects. The quality of the initial materials is crucial, as any imperfections can impact the performance and reliability of the final circuit board.
For multilayer Rogers circuit boards, the next step is stacking the individual layers of dielectric and conductive materials. This involves aligning the layers precisely to ensure proper registration and lamination. The stack-up configuration, including the number of signal layers, ground planes, and power planes, is designed based on the electrical performance requirements. Rogers materials allow for complex multilayer designs, enabling the integration of various circuit functions on a single board.
Once the layers are stacked, the next step is drilling the holes that will be used for vias and through-hole components. This step requires precision to ensure that the holes are accurately positioned and of the correct size. Advanced drilling techniques, such as laser drilling, may be used for microvias and other high-precision requirements. The drilled holes are then inspected to ensure they meet the required specifications.
Резюме, the manufacturing process of Rogers circuit boards involves a series of carefully controlled steps, from material preparation and layer stacking to drilling, plating, imaging, etching, solder masking, surface finishing, testing, and final inspection. Each step is critical for ensuring the high performance, reliability, and quality of the final product, making Rogers circuit boards a preferred choice for high-frequency and high-power applications.
The Application Area of Rogers Circuit Boards
Rogers circuit boards are renowned for their high performance in a wide range of applications, particularly where signal integrity and thermal management are critical. Their superior dielectric properties and mechanical stability make them suitable for various high-frequency and high-power applications. Here are some of the key application areas where Rogers circuit boards excel:
One of the primary application areas for Rogers circuit boards is telecommunications. These boards are used in various high-frequency devices, включая базовые станции, Антенны, satellite communication systems, and microwave links. The low dielectric constant and low dissipation factor of Rogers materials ensure minimal signal loss and distortion, which are crucial for maintaining the integrity of high-frequency signals in telecommunications. Additionally, the excellent thermal management properties help in dissipating the heat generated by high-power RF components, ensuring reliable and efficient operation.
Rogers circuit boards are widely used in aerospace and defense applications due to their high reliability, stability, and performance in extreme environments. They are used in radar systems, satellite communication, avionics, and electronic warfare systems. The low outgassing properties of some Rogers materials make them suitable for use in vacuum environments, such as space applications. The ability to maintain consistent performance under varying temperature and humidity conditions is essential for mission-critical systems in aerospace and defense.
The automotive industry is increasingly relying on advanced electronics for various applications, including advanced driver-assistance systems (АДАС), radar sensors, информационно-развлекательные системы, and electric vehicle (EV) power management. Rogers circuit boards are ideal for these applications due to their high-frequency performance, thermal stability, and reliability. The low dielectric loss ensures efficient signal transmission for radar and communication systems, while the high thermal conductivity helps in managing the heat generated by power electronics in EVs.
Резюме, Rogers circuit boards are used in a wide range of applications across various industries, including telecommunications, aerospace and defense, Автомобильная электроника, medical devices, consumer electronics, industrial electronics, 5G and IoT applications, and renewable energy systems. Their superior dielectric properties, thermal management, and mechanical stability make them an ideal choice for high-frequency, high-power, and high-reliability applications, ensuring optimal performance and reliability in demanding environments.
What are the Advantages of Rogers Circuit Boards?
Rogers circuit boards offer several advantages that make them a preferred choice for high-frequency, high-power, and high-reliability applications. These advantages stem from the unique properties of Rogers materials, including their dielectric, thermal, and mechanical characteristics. Here are some of the key advantages of Rogers circuit boards:
One of the most significant advantages of Rogers circuit boards is their superior dielectric properties. Rogers materials have a low dielectric constant (Dk) and low dissipation factor (Df), which are essential for maintaining signal integrity and minimizing signal loss in high-frequency applications. The low Dk ensures that the signal speed is maintained, while the low Df minimizes energy loss as heat, resulting in efficient and reliable performance. These properties make Rogers circuit boards ideal for applications such as RF and microwave circuits, where signal integrity is critical.
Rogers circuit boards are known for their excellent thermal management capabilities. The high thermal conductivity of Rogers materials helps in efficiently dissipating heat generated by high-power components, ensuring stable and reliable operation. This is particularly important in applications such as power amplifiers, radar systems, and automotive electronics, where effective heat dissipation is crucial for preventing thermal-related failures. The ability to manage heat effectively also enhances the longevity and reliability of the electronic components.
Another advantage of Rogers circuit boards is their outstanding dimensional stability. Rogers materials maintain their structural integrity and electrical properties even under varying environmental conditions, such as changes in temperature and humidity. This stability is essential for applications that require precise and consistent performance over time, such as aerospace and defense systems. The low coefficient of thermal expansion (CTE) of Rogers materials ensures that the board remains stable and minimizes the risk of delamination or mechanical failure.
Rogers materials exhibit low outgassing properties, making them suitable for use in vacuum environments, such as space applications. Low outgassing is essential for preventing contamination of sensitive electronic components and ensuring reliable performance in environments with low atmospheric pressure. This property makes Rogers circuit boards an excellent choice for aerospace and defense applications where reliability in extreme conditions is critical.
Вопросы и ответы
What makes Rogers circuit boards different from traditional FR4 boards?
Rogers circuit boards differ from traditional FR4 boards primarily in their material properties. Rogers materials offer superior dielectric properties, including a low dielectric constant (Dk) and low dissipation factor (Df), which are essential for high-frequency applications. These materials also provide excellent thermal management, dimensional stability, and low outgassing, making them suitable for demanding environments. In contrast, FR4 boards are more commonly used for general-purpose applications and may not offer the same level of performance in high-frequency and high-power applications.
Can Rogers circuit boards be used in high-power applications?
Да, Rogers circuit boards are well-suited for high-power applications. The high thermal conductivity of Rogers materials helps in efficiently dissipating heat generated by high-power components, ensuring stable and reliable operation. This makes Rogers circuit boards ideal for applications such as power amplifiers, radar systems, and automotive electronics, where effective heat dissipation is crucial for preventing thermal-related failures and maintaining the reliability of electronic components.
Are Rogers circuit boards suitable for use in harsh environments?
Rogers circuit boards are highly suitable for use in harsh environments. Their superior dielectric properties, excellent thermal management, and dimensional stability ensure reliable performance under varying environmental conditions, such as high temperatures, humidity, and mechanical stress. Additionally, the low outgassing properties of some Rogers materials make them suitable for use in vacuum environments, such as space applications. These characteristics make Rogers circuit boards an excellent choice for aerospace, defense, automotive, and other mission-critical applications.
How does the manufacturing process of Rogers circuit boards differ from traditional PCB manufacturing?
The manufacturing process of Rogers circuit boards involves several steps that are similar to traditional PCB manufacturing, such as material preparation, layer stacking, drilling, plating, imaging, etching, solder masking, surface finishing, and testing. However, certain considerations must be made due to the unique properties of Rogers materials. Например, the lamination process may require different temperatures and pressures compared to traditional PCBs. The drilling and plating processes must also account for the materials’ mechanical properties to avoid defects such as delamination or burrs. Working with experienced fabricators familiar with Rogers materials is essential to ensure high-quality production.