What is RF PCB?
RF PCB Manufacturer.”RF PCB Manufacturer” refers to a company specializing in the production of printed circuit boards designed specifically for radio frequency (RF) Приложений. They excel in manufacturing boards that ensure optimal signal integrity, low loss, and high-frequency performance, crucial for industries like telecommunications, aerospace, and wireless technology. These manufacturers employ advanced materials and precise fabrication techniques to meet stringent RF requirements, catering to the growing demand for reliable and efficient RF electronic devices.
RF PCB (radio frequency printed circuit board) is a printed circuit board specially designed to handle high frequency signals and microwave signals. Compared with traditional circuit boards, RF PCBs have higher frequency and signal transmission requirements, so they play a vital role in fields such as wireless communication equipment, radar systems, satellite communications, and wireless sensor networks.
In wireless communication equipment, RF Печатная плата is widely used in base stations, wireless routers, and wireless modules in mobile phones and other mobile devices. They ensure stable transmission and low loss of high-frequency signals through optimized circuit layout and material selection, thereby improving device performance and coverage.
In radar systems, RF PCBs are used to receive and process radar echoes, helping detect targets and provide precise location information. High frequency and precise signal processing capabilities make RF PCB critical in these systems, directly affecting the detection range and accuracy of radar.
The field of satellite communications is also one of the important application scenarios of RF PCB. Satellites need to be able to receive and transmit signals efficiently while being adaptable to environmental changes. The excellent high-frequency performance and stability of RF PCB make it an indispensable component of satellite communication systems, supporting global data transmission and communication needs.
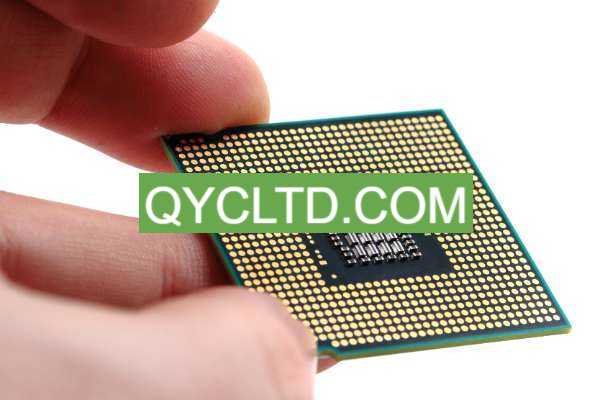
RF PCB Manufacturer
В дополнение, RF PCBs are widely used in wireless sensor networks, which are often distributed over wide geographical areas to monitor and collect environmental data. RF PCB can provide reliable data transmission and processing capabilities in these applications, as well as good anti-interference performance, ensuring efficient communication and data exchange between sensor nodes.
In short, RF PCB provides key support for the development of modern wireless communication technology through its specially designed high-frequency circuits and precise manufacturing processes. They not only play a role in traditional communication equipment, but also promote the widespread application and progress of wireless technology in fields such as satellites, radars and sensor networks.
RF PCB design Reference Guide.
When designing RF PCB, compared with traditional circuit boards, special attention needs to be paid to key factors such as signal integrity, impedance matching, and signal transmission loss. These factors directly affect the performance and stability of high-frequency circuits, so the design guide covers a series of best practices and technical points to ensure that RF PCBs can achieve the expected performance levels in practical applications.
In RF PCB design, signal integrity is a crucial consideration. Due to the characteristics of high-frequency signals, including fast signal transmission speed and short wavelength, signal reflection, crosstalk or attenuation must be avoided. Therefore, designers need to employ appropriate routing techniques and material selections to minimize the loss of signal integrity.
Impedance matching is one of the key factors to ensure the quality of signal transmission in RF PCB. In high-frequency circuits, any impedance mismatch may cause signal reflection and power loss, thereby affecting system performance and stability. The design guide will detail how to implement strict impedance control in layout and interlayer design to ensure smooth signal transmission and efficient energy transfer.
Another important design consideration is signal transmission loss. During the transmission process of high-frequency signals, energy loss occurs due to factors such as conductor loss, dielectric dissipation, and edge effects. The design guide will explore how to improve system efficiency and performance by minimizing energy loss during signal transmission through optimizing routing paths, selecting low-loss materials, and proper electromagnetic shielding design.
The RF PCB Design Guide will also introduce a series of best practices and advanced technical tools to help designers achieve the best results during the design process. These tools include simulation software, wiring rule checking tools, three-dimensional electromagnetic field simulation software, и так далее., which can accurately analyze and evaluate circuits in the early stages of design, and identify potential design problems in advance and solve them.
Резюме, the RF PCB design guide not only focuses on theoretical knowledge and design techniques, but also emphasizes experience summary and engineering practice in practical applications. By following these guidelines, designers can better understand and apply the complexity of RF PCB design, thereby improving product performance and reliability and meeting the stringent requirements for high-frequency circuits in different application scenarios.
What material is used in RF PCB?
RF PCB (radio frequency printed circuit board) is a key component used in high-frequency signal processing, and its material selection is crucial. Generally, RF PCB uses materials with low dielectric constant and low loss tangent properties, such as polytetrafluoroethylene (PTFE) and its composite materials.
Polytetrafluoroethylene (PTFE) is a material with excellent electrical properties. Its main features include extremely low dielectric constant and loss tangent, which makes it excellent in high-frequency signal transmission. The low dielectric constant means that the signal transmits faster in the PCB board. The low tangent loss reduces the energy loss during signal transmission, thus improving the efficiency and performance stability of the entire system.
In addition to PTFE, RF PCB can also use PTFE composite materials, such as glass fiber reinforced PTFE (PTFE-Glass) or ceramic filled PTFE (PTFE-Ceramic). These composites incorporate different reinforcements to further improve the material’s mechanical strength and thermal resistance while maintaining the excellent properties of low dielectric constant and low loss tangent. These characteristics enable RF PCB to operate stably in various complex environments and high-frequency applications, such as wireless communication equipment, radar systems, satellite communications, и так далее.
During the design process of RF PCB, choosing the appropriate material is crucial to ensure the high-frequency performance of the circuit. High-frequency circuits usually require precise impedance control and low signal loss, and the use of materials with low dielectric constant and low-loss tangent can effectively reduce attenuation and interference in signal transmission, thereby improving the reliability and stability of the system.
In short, the material selection of RF PCB not only affects the performance and reliability of the circuit board, but is also directly related to the work efficiency and signal transmission quality of the entire system. Therefore, when designing and manufacturing RF PCBs, the selection of materials should fully take into account the circuit’s operating frequency range, environmental conditions, and system performance requirements to ensure optimal engineering implementation and long-term stable operation.
What size are RF PCB?
RF PCB dimensions vary depending on application needs and are typically designed based on the device’s functionality and space constraints. The choice of size is crucial for the transmission of high-frequency signals and electromagnetic compatibility.
In wireless communications and radio frequency technology, RF PCB dimensions can range from very small, a few square millimeters, to several square meters. Small RF PCBs are commonly found in mobile devices, wireless sensor networks, and small communications modules such as smartphones, Bluetooth devices, and wearable technology. These devices require compact designs to accommodate a variety of RF components and electronics while ensuring good signal integrity and transmission efficiency.
On the other hand, large RF PCBs are mainly used in base stations, radar systems, satellite communications, and industrial automation equipment. These systems typically need to handle larger data volumes and more complex signal processing tasks, so the size of the RF PCB is correspondingly larger to accommodate more electronic components and longer signal transmission paths.
Regardless of the size of the RF PCB, the design and manufacturing processes require strict control to ensure signal stability and reliability. From material selection to layout and wiring, key factors such as impedance matching, electromagnetic interference suppression, and thermal management for signal transmission need to be considered. Therefore, when designing RF PCB, engineers need to balance size, performance and manufacturing cost according to specific application scenarios and technical requirements to achieve the best design effect and system performance.
Резюме, the size of RF PCB can vary depending on the application, but the key consideration in its design principles and manufacturing process is always to ensure the stability and reliability of high-frequency signal transmission and system performance.
The Manufacturer Process of RF PCB.
The manufacturing process of RF PCB is a complex and precise process, which is related to the stability and reliability of high-frequency circuits. Following are the main steps of RF PCB manufacturing process:
The first step in manufacturing an RF PCB is selecting the appropriate substrate material. Commonly used materials include FR4, PTFE, and other materials with specific electrical properties. Substrates need to undergo strict inspection and pre-treatment to ensure that the surface is smooth and meets manufacturing requirements.
The surface of the substrate needs to be coated with a thin layer of copper to facilitate the subsequent formation of circuit paths and connections. Copper layer deposition can use chemical methods or electroplating methods to ensure that the copper layer is uniform and has good conductivity.
Coat the surface of the copper layer with photoresist, and then use a photolithography exposure machine to map the designed circuit pattern onto the photoresist. After exposure, the photoresist cures to form the circuit board’s pattern.
After photolithography exposure, the copper layer that is not protected by the photoresist is removed by chemical etching to form the designed circuit paths and connections. The etching process requires control of time and chemical solution concentration to ensure etching accuracy and quality.
After etching is completed, holes need to be drilled at designated locations for subsequent component installation and connection. The accuracy and position of drilling have a significant impact on the performance of the overall circuit, so high-precision drilling equipment and technicians are required to operate it.
After drilling is completed, the electronic components are accurately installed at the predetermined location through an automated or semi-automated assembly line. The component installation process needs to consider the size, positioning accuracy and welding characteristics of the components to ensure the stability and functional integrity of the circuit board.
After completing the installation of the components, the components are firmly connected to the copper paths on the circuit board through a soldering process. Commonly used soldering methods include surface mount technology (SMT) and through-hole technology (THT), with the specific choice depending on the circuit design and component type.
The final step is rigorous testing and quality control of the assembled RF PCB. Testing includes electrical testing, functional testing, and possible environmental testing (such as temperature and humidity testing) to ensure that the board is stable and reliable under various operating conditions.
Through the above precise manufacturing process steps, RF PCB can ensure the performance and stability of high-frequency circuits and is widely used in wireless communications, radar systems, satellite communications and other high-frequency equipment, promoting the development and application of modern wireless technology.
The Application area of RF PCB.
RF PCB (radio frequency printed circuit board), as a key technology for high-frequency signal processing, plays an indispensable role in modern electronic systems. With their excellent performance and stability, they are widely used in many important fields, including wireless communications, radar and navigation, satellite communications, медицинское оборудование, and military and aerospace industries.
Первый, RF PCB plays a central role in wireless communication equipment. From mobile communication base stations to home wireless routers, RF PCBs are used to process and transmit high-frequency signals to ensure communication stability and coverage. Whether it is the construction of urban communication networks or communication coverage in remote areas, RF PCB is one of the key factors to ensure communication quality.
Во-вторых, RF PCB also has important applications in radar and navigation systems. Radar systems rely on precise signal processing and reflection analysis. RF PCB can provide high-frequency transmission and low signal loss to ensure reliable operation of the radar system under various environmental conditions. At the same time, navigation systems such as GPS and inertial navigation systems also require precise control of high-frequency signals. The design and manufacturing of RF PCB is crucial to improving the accuracy and stability of the navigation system.
In the field of satellite communications, RF PCB is widely used in satellite communications equipment. Satellite communications require efficient signal transmission and reception capabilities. RF PCB ensures high-quality transmission of satellite signals through optimized design and material selection, supporting two-way communications from the ground to the satellite.
В дополнение, the field of medical equipment is also one of the important application scenarios of RF PCB. Medical equipment like MRI (magnetic resonance imaging) equipment and wireless monitoring systems require high-frequency circuits to process and transmit biological signals while ensuring the safety and stability of the equipment. The application of RF PCB in medical equipment not only improves the accuracy of diagnosis and treatment, but also improves the patient’s treatment experience.
Наконец, RF PCBs are of strategic importance in the military and aerospace fields. From military communication equipment to navigation and control systems for aircraft and satellites, RF PCBs play an important role in ensuring national security and performing important tasks. Its high-frequency performance and reliability ensure stable operation in extreme environments, providing key support for battlefield command, intelligence collection and air operations.
Подведем итоги, RF PCB has become an indispensable and important part of modern electronic systems due to its wide application in wireless communications, radar navigation, satellite communications, медицинское оборудование, military aerospace and other fields. With the advancement of technology and the expansion of application fields, the design and manufacturing of RF PCB will continue to play a key role in promoting technological innovation and development in all walks of life.
What are the advantages of RF PCB?
As an indispensable component of modern wireless communication systems, RF PCB (radio frequency printed circuit board) has multiple obvious advantages compared to other transmission lines, making it perform well in high-frequency environments.
Первый, the RF PCB ensures stability and low loss in the high frequency range through specially optimized design and material selection. Since high-frequency signals have strict requirements on the physical properties of the circuit board, RF PCB uses low-loss dielectric materials, such as PTFE (polytetrafluoroethylene), which effectively reduces energy loss in signal transmission and ensures the clarity and strength of the signal.
Во-вторых, RF PCB achieves precise impedance control during the design process, which is the key to ensuring signal transmission quality and integrity. Through strictly controlled impedance matching, RF PCB can minimize signal reflection and loss, ensure stable transmission of high-frequency signals, and avoid signal distortion and performance degradation caused by impedance mismatch.
RF PCB can also operate stably in complex environments, such as high temperature, high humidity or severe electromagnetic interference. Its design and material selection give it good anti-interference ability and environmental adaptability, ensuring stable performance and reliable working status under various extreme conditions.
В дополнение, RF PCB has strong customization capabilities and can be designed according to specific needs, suitable for different application scenarios and product requirements. Whether in wireless communication equipment, radar systems, satellite communications or medical equipment, RF PCB can be customized and optimized according to system requirements to maximize the performance and functional requirements of specific applications.
Наконец, the reliability of RF PCB is highly guaranteed. The adoption of standardized manufacturing processes and strict quality control ensures product stability and long-term reliability. This reliability not only meets the needs of the commercial market, but also plays a key role in military, aerospace and other fields, ensuring the safe and stable operation of key systems.
Подведем итоги, RF PCB has become an indispensable part of modern wireless communications and radio frequency technology with its excellent high-frequency performance, precise impedance control, ability to adapt to complex environments, strong customization and high reliability. , promoting the continuous advancement of technology and the expansion of application scope.
Вопросы и ответы
What are the main application areas of RF PCB?
RF PCB is widely used in wireless communication equipment (such as base stations, WiFi routers), radar systems, satellite communications, медицинское оборудование (such as MRI machines and wireless monitoring systems), military and aerospace fields. Its high frequency performance and stability make it an indispensable component in modern electronic systems.
What is the difference between RF PCB and traditional PCB?
RF PCB differs from traditional PCB in design and material selection. RF PCB requires special consideration of the transmission characteristics of high-frequency signals, so the substrate materials used usually have low dielectric constant and low loss tangent, such as PTFE (polytetrafluoroethylene) or its composite materials. В дополнение, impedance matching needs to be strictly controlled in RF PCB design to ensure signal transmission quality and integrity.
What are the key steps included in the RF PCB manufacturing process?
The manufacturing process of RF PCB involves multiple key steps such as substrate preparation, copper layer deposition, photoresist coating and exposure, etching, drilling, component mounting, soldering and testing. Each step requires precise operation and strict quality control to ensure the stability and reliability of RF PCB in high-frequency environments.
How to choose suitable RF PCB material?
Selecting a suitable RF PCB material requires consideration of multiple factors, including high-frequency performance, диэлектрическая проницаемость, loss tangent, mechanical strength, and cost. Common materials include PTFE and its composite materials, FR4, and specific ceramic materials. Each material has its applicable scenarios, advantages and disadvantages.