What is LED ceramic substrate?
Micro LED Substrate Manufacturer. A pioneering force in the realm of display technology, our company stands as a leading Micro LED substrate manufacturer. With precision engineering and cutting-edge fabrication processes, we craft substrates of unparalleled quality, enabling the creation of next-generation displays. Our commitment to innovation drives us to push the boundaries of possibility, fostering advancements in clarity, brightness, and energy efficiency. Empowering the future of visual experiences, we deliver substrates that redefine excellence, setting new standards in the industry and igniting the imagination of consumers worldwide.
LED ceramic substrate is a special printed circuit board (Печатная плата) that plays an important role in high-power applications such as LED lighting and power modules. Compared with traditional glass fiber substrates, LED ceramic substrates use ceramic materials as the substrate, which have higher thermal conductivity and high temperature resistance, so they can effectively dissipate heat and maintain a stable operating temperature.
Прежде всего, the LED ceramic субстрат consists of a ceramic substrate, a conductive layer and an insulating layer. Ceramic substrates are usually made of materials such as aluminum oxide (Al2O3) or silicon nitride (Si3N4). These materials have excellent thermal conductivity and electrical insulation properties and can effectively conduct heat away from the LED chip and maintain the stable operation of the LED chip. temperature. The conductive layer usually uses metallized ceramics or thick film technology to print circuit patterns on the surface of the ceramic substrate to achieve electrical connections. The insulating layer is used to protect the conductive layer and prevent circuit short circuits and leakage.
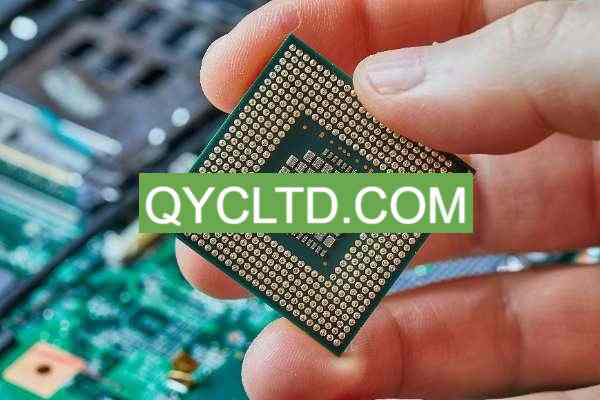
Micro LED Substrate Manufacturer
The excellent performance of LED ceramic substrates makes them widely used in high-power applications such as LED lighting and power modules. Due to the high operating temperature of LED light-emitting devices, traditional glass fiber substrates are often difficult to meet the heat dissipation requirements, which can easily lead to a decrease in LED luminous efficiency and shortened lifespan. The LED ceramic substrate has excellent heat dissipation performance, which can effectively conduct the heat generated by the LED out quickly and maintain the stable operating temperature of the LED chip, thus improving the luminous efficiency and service life of the LED.
In addition to the field of LED lighting, LED ceramic substrates are also widely used in power modules, power amplifiers, high-frequency circuits and other fields. In these high-power applications, stable operating temperature and reliable performance are crucial, and LED ceramic substrates are an ideal choice due to their excellent heat dissipation performance and high temperature resistance.
Вообще, LED ceramic substrates have been widely used in high-power applications such as LED lighting and power modules due to their excellent heat dissipation performance, stable operating temperature and reliable performance, providing improved performance and reliability of electronic equipment. Important Guarantee.
How to design LED ceramic substrate?
Designing LED ceramic substrates is a critical process, which directly affects the performance and stability of LED products. The design process of LED ceramic substrate will be introduced in detail below.
Прежде всего, designing LED ceramic substrate requires clear circuit requirements. This includes determining required electrical characteristics, power requirements, interface types, и так далее. Based on these needs, the design team can begin selecting the appropriate design software. Commonly used design software includes Altium Designer, Cadence Allegro, и так далее., which provide a wealth of functions and tools to meet the needs of complex circuit design.
Следующий, the design team will perform schematic design and layout and routing. During the schematic design stage, the designer draws the circuit diagram, connects the electrical components, and makes necessary symbols and annotations. The place and route phase involves placing circuit components on the Печатная плата board and connecting them through wires. Designers need to consider factors such as layout compactness, signal transmission path length, and impedance matching to ensure good electrical performance and signal integrity.
The design team will also perform thermal simulation and verification to ensure that the LED ceramic substrate can effectively dissipate heat and maintain a stable temperature when working. Thermal simulation tools can simulate the heat distribution and conduction paths of LED lamps when they are working, helping designers optimize heat dissipation structures and material selection. The verification phase involves actual testing of the electrical and thermal characteristics of the design to verify that the design meets the expected requirements.
На протяжении всего процесса проектирования, LED ceramic substrate manufacturers usually provide design guidance and technical support. They have extensive experience and expertise to help design teams solve various design problems and challenges. Manufacturers may also offer customized solutions, personalized to the customer’s specific needs.
Резюме, designing LED ceramic substrates is a complex and critical process that involves multiple aspects of technology and considerations. Through appropriate design software, careful schematic design and layout, and effective thermal simulation and verification, the design team can ensure that the LED ceramic substrate has excellent performance and reliability. Technical support and guidance from manufacturers are also an integral part of the design process, and their expertise and experience can help customers achieve the best design results.
What is the manufacturing process of LED ceramic substrate?
The manufacturing process of LED ceramic substrates is a complex and precise process, which includes multiple key steps. Each step is crucial and directly affects the quality and performance of the final product.
The manufacturing of LED ceramic substrates begins with the selection of raw materials. Типично, the main material of ceramic substrates is aluminum oxide or silicon nitride. These materials have excellent thermal conductivity and electrical insulation properties and are very suitable for high-power LED applications. Manufacturers select high-quality raw materials to ensure stable performance and reliability of the final product.
After the raw materials are prepared, the next step is to print the conductive layer onto the ceramic substrate. This is usually done through screen printing technology, where manufacturers print conductive patterns on the surface of ceramic substrates based on design requirements and circuit layout to enable the connection of electronic components.
After printing, the ceramic substrate needs to be metallized to increase conductivity and connection strength. This step involves depositing a metallic material, such as copper, onto a printed conductive pattern, typically using techniques such as chemical deposition or vacuum evaporation.
After metallization is complete, the next step is to drill holes into the ceramic substrate. Drilling is used to form connection holes and soldering holes on the substrate for mounting electronic components and making circuit connections. Manufacturers use high-precision drilling equipment to ensure accuracy and consistency of hole locations.
After drilling is completed, the LED ceramic substrate needs to undergo a welding process to install the electronic components to the designated position and connect them to the conductive pattern through welding technology. Commonly used welding methods include surface mount technology (SMT) and through-hole welding technology (PTH). Manufacturers will choose the appropriate welding method based on product requirements.
Наконец, after completing all manufacturing steps, the LED ceramic substrate needs to undergo strict final inspection. Manufacturers will conduct multiple tests such as visual inspection, electrical testing and functional verification of products to ensure that the products meet design requirements and customer needs. Only products that have passed strict quality control and testing will be sent to customers.
Выполнив описанные выше шаги, LED ceramic substrate manufacturers can ensure the high quality and stable performance of their products and meet customer needs for efficient LED lighting and other applications. Manufacturers continue to improve and optimize their manufacturing processes to adapt to market changes and customer needs, and maintain their leading position in the LED ceramic substrate industry.
How much does an LED ceramic substrate cost?
How much does an LED ceramic substrate cost? This problem is not simple, because the price of LED ceramic substrates is affected by many factors. In this paragraph, we will delve into these factors and explain why the cost of LED ceramic substrates varies.
Прежде всего, the cost of LED ceramic substrate depends on the number of layers. Generally, LED ceramic substrates can be single-layer, double-layer or multi-layer structures. More layers means more complex circuit design and manufacturing processes, so the cost will increase accordingly.
Во-вторых, the complexity of LED ceramic substrate is another important factor affecting the price. If the LED ceramic substrate has a complex layout, dense component arrangement, or special requirements (such as blind holes, buried holes, и так далее.), the manufacturing process will be more complicated, resulting in increased costs.
В дополнение, the size of the LED ceramic substrate will also directly affect its cost. Larger substrate sizes require more material and longer manufacturing time, so the cost will be relatively higher.
Наконец, production scale is also one of the important factors that determine the cost of LED ceramic substrates. Large-scale production often reduces unit costs because fixed costs can be spread over more products. Conversely, small-scale production may result in higher unit costs.
Подведем итоги, the cost of LED ceramic substrates depends on many factors such as the number of board layers, complexity, size and production scale. Manufacturers often provide quotation services based on customers’ specific needs and requirements to ensure the final price meets the customer’s budget and expectations. Therefore, if you need LED ceramic substrates, it is recommended to contact the manufacturer to learn more about their quotation policy and service content.
What material is the LED ceramic substrate made of?
LED ceramic substrate is a key electronic component that plays a vital role in LED lighting and other high-power applications. Understanding the material composition of LED ceramic substrates is critical to understanding their performance and applications.
LED ceramic substrates are usually made of ceramic materials such as aluminum oxide (Alumina) or silicon nitride (Silicon Nitride). These ceramic materials have many excellent properties, making them one of the preferred materials for LED ceramic substrates.
Aluminum oxide is a commonly used LED ceramic substrate material that is favored for its good thermal conductivity, mechanical strength and electrical insulation properties. It can effectively dissipate heat and maintain the stable operating temperature of the LED device, thereby extending its life. В дополнение, alumina also has good corrosion resistance and chemical stability, making it suitable for applications in a variety of environmental conditions.
Silicon nitride is another common LED ceramic substrate material with excellent thermal conductivity and mechanical strength, as well as a low thermal expansion coefficient. Compared with alumina, silicon nitride has better stability at high temperatures and is suitable for some special high-temperature application scenarios. В дополнение, silicon nitride also has good insulation properties and chemical stability, making it suitable for long-term use under various environmental conditions.
The conductive layer of LED ceramic substrate usually uses metallized ceramics or thick film technology to achieve stable electrical connection. Metallized ceramics is a technology that combines metal materials (such as silver) with ceramic substrates through a special process. It has good electrical conductivity and durability. Thick film technology coats conductive materials on the surface of ceramic substrates by spraying or printing, and then sinters them to form a stable conductive layer.
The material selection of LED ceramic substrate has an important impact on its performance and application. Ceramic materials such as aluminum oxide and silicon nitride as well as conductive layers of metallized ceramics and thick film technology are key factors in achieving the excellent performance of LED ceramic substrates. When selecting an LED ceramic substrate, appropriate materials and manufacturing processes should be selected based on specific application needs and environmental conditions to ensure optimal performance and reliability.
Who is the LED ceramic substrate manufacturer?
In the field of modern technology, LED ceramic substrate manufacturers play a vital role. These manufacturers support the development of LED lighting, power modules and other high-power applications by providing high-quality LED ceramic substrates. Among many manufacturers, finding a reliable supplier is particularly important.
Our company is a leading LED ceramic substrate manufacturer committed to providing customers with high-quality products and customized solutions. We have many years of experience and technical strength, and have accumulated rich professional knowledge in the field of LED ceramic substrates.
As an LED ceramic substrate manufacturer, we focus on technological innovation and quality management. We have a team of technical professionals capable of providing professional technical support and customized solutions. Whether in the design stage or during the manufacturing process, we are committed to providing our customers with the best products and services.
We use high-quality ceramic materials and advanced production processes to ensure that the LED ceramic substrate has excellent thermal conductivity and electrical insulation properties. Our products undergo strict quality control to ensure stable performance and reliability.
We understand that each client’s needs and requirements are unique, so we provide a personalized service. No matter what kind of LED ceramic substrate you need, we can customize it according to your requirements to ensure that your needs are fully met.
As a high-quality LED ceramic substrate manufacturer, we continuously optimize production processes and technologies to meet the changing market and customer needs. We adhere to the concept of continuous improvement and strive to improve product quality and service levels.
When choosing an LED ceramic substrate manufacturer, our company will be your ideal choice. We have rich experience and professional knowledge to provide you with high-quality products and excellent services. If you have any needs or questions, please feel free to contact us and we will be happy to serve you.
5 premium qualities of LED ceramic substrate manufacturers
The 5 high-quality characteristics of LED ceramic substrate manufacturers are the cornerstones of their success, and they directly affect customer experience and product quality. Below is a detailed description of these qualities:
Technical expertise: A high-quality LED ceramic substrate manufacturer should have rich experience and deep technical strength. Their teams should be composed of experienced engineers and technical experts capable of handling a variety of complex design and manufacturing challenges. These professionals should keep a close eye on the latest developments and technology trends in the industry to ensure that their products remain at the cutting edge.
Customized services: Every customer’s needs are unique, so a quality LED ceramic substrate manufacturer should be able to provide personalized solutions. They should be able to work closely with customers to understand their specific needs and requirements and tailor design and production solutions to those needs. Whether customers require special sizes, materials or processes, manufacturers should be able to meet their requirements and provide customized products and services.
Quality Assurance: In order to ensure the stable performance and reliability of products, LED ceramic substrate manufacturers must have a strict quality management system. From raw material procurement to production and manufacturing to final inspection, every link must undergo strict control and testing. Manufacturers should adopt advanced production equipment and technology and conduct comprehensive quality inspections to ensure that each product meets high standard quality requirements.
Timely response: In a highly competitive market environment, timely response to customer needs and problems is crucial. A quality LED ceramic substrate manufacturer should be able to respond quickly to customer inquiries and orders, and provide efficient technical support and services. Whether it is technical consultation, sample customization or after-sales support, manufacturers should be able to meet customer needs in a timely and thoughtful manner and establish a good cooperative relationship.
Continuous improvement: As an industry leader, LED ceramic substrate manufacturers should continuously optimize their production processes and technologies to meet the changing market and customer needs. They should actively invest in R&D and innovation, introduce new materials and technologies, and improve product performance and reliability. Through continuous improvement, manufacturers can maintain a competitive advantage and provide customers with more reliable and advanced LED ceramic substrate products.
In short, a high-quality LED ceramic substrate manufacturer should have five key characteristics: technical expertise, customized services, quality assurance, timely response and continuous improvement. The combination of these qualities will provide customers with the best possible product and service experience, ensuring their needs are fully met and fostering long-term relationships.
FAQs
How to choose the appropriate LED ceramic substrate material?
Selecting the appropriate LED ceramic substrate material is a critical step to ensure product performance and reliability. Первый, you should consider your application environment and needs, such as operating temperature range, heat dissipation requirements, and mechanical strength. Generally, Alumina is a common choice with good thermal conductivity and electrical insulation properties, making it suitable for most applications. Additionally, for high power density and high frequency applications, Silicon Nitride may be a better choice due to its higher thermal conductivity and dielectric constant.
What is the maximum operating temperature of LED ceramic substrate?
LED ceramic substrates generally have high thermal stability and can operate in a wide temperature range. Generally speaking, the maximum operating temperature of aluminum oxide substrates is about 150°C to 200°C, while silicon nitride substrates can reach higher temperature ranges, usually above 200°C. However, the maximum operating temperature also depends on other factors, such as thermal conductivity and heat dissipation design and the maximum operating temperature of the component.
How to optimize the heat dissipation performance of LED ceramic substrate?
In order to optimize the heat dissipation performance of LED ceramic substrates, you can take several measures. Первый, ensure good thermal design, including appropriate heat sinks and heat dissipation structures. Во-вторых, choose ceramic materials with high thermal conductivity and rationally design heat conduction channels to improve heat transfer efficiency. В дополнение, you can consider using thermal sensitive components and temperature sensors to monitor temperature changes in real time and take appropriate measures to adjust the working status of the system.
How long is the production cycle of LED ceramic substrates?
The production cycle of LED ceramic substrates depends on a variety of factors, including order volume, complexity and the manufacturer’s production capabilities. Generally speaking, the standard LED ceramic substrate production cycle is usually between 2 and 4 weeks, but it may take longer for customized products and mass production. In order to ensure timely delivery, please communicate with the manufacturer in advance and develop a reasonable production plan.
How to contact a reliable LED ceramic substrate manufacturer?
To contact a reliable LED ceramic substrate manufacturer, you can search and contact through a variety of channels. Первый, you can search on the Internet and browse the manufacturer’s official website to learn about its products and services. Во-вторых, you can refer to industry guides and relevant exhibitions to find well-known manufacturers and suppliers. Наконец, share experiences with other industry experts and users and seek recommendations and advice by participating in industry forums and social media platforms.