What is Metallic Substrate?
Metallic Substrate Manufacturer.A leading Metallic Substrate Manufacturer, we specialize in producing high-quality substrates for various industries, including electronics, automotive, and aerospace. Our advanced manufacturing processes and rigorous quality control ensure superior performance and reliability. With a commitment to innovation and customer satisfaction, we deliver customized solutions that meet the specific needs of our clients, setting the standard for excellence in the metallic substrate industry.
As a special type of printed circuit board (Печатная плата), the base material of metal substrate is different from traditional non-conductive materials such as FR4, but uses metal materials. This design not only gives the circuit board excellent thermal conductivity, but also improves its mechanical strength, making it suitable for applications requiring efficient heat dissipation and stability.
In traditional electronic design, the use of non-conductive substrates such as FR4, although economical and easy to process, has poor thermal conductivity, limiting the application of electronic devices under high-power and high-density conditions. In contrast, metal substrates significantly improve heat conduction capabilities by using metal materials such as aluminum and copper as the base, effectively dispersing and dissipating the heat generated by electronic components, thereby maintaining the stability of the circuit board during operation.
In addition to excellent heat dissipation performance, metal substrates also have high mechanical strength and can resist vibration and physical stress caused by the external environment, thus improving the durability and reliability of electronic devices. This makes metal substrates particularly suitable for industrial control systems, Автомобильная электроника, aerospace equipment and other fields that require high stability and long-term reliability.
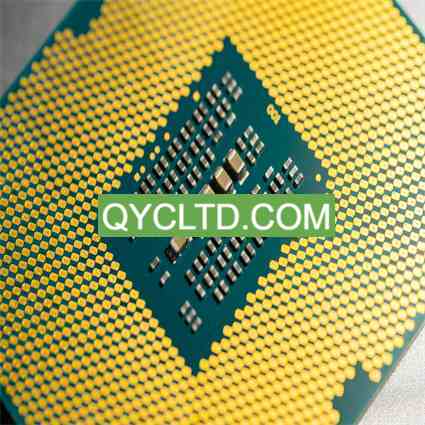
Metallic Substrate Manufacturer
During the manufacturing process, the preparation of metal substrates includes process steps such as multi-layer stacking, etching, drilling and coating to ensure that the circuit boards meet the needs of complex electronic designs and undergo rigorous testing to ensure that they meet high quality standards.
Подведем итоги, as an important part of modern electronic equipment, metal substrates not only provide excellent heat dissipation performance and mechanical strength, but also open up new possibilities for electronic design. With the advancement of technology and the expansion of application scope, metal substrate PCB will continue to play an important role in improving the performance and reliability of electronic equipment, bringing more innovative solutions and development opportunities to various industries.
Metallic Substrate design Reference Guide.
As an indispensable component of modern electronic equipment, metal substrate PCB (Printed Circuit Board) has gradually become the first choice for various high-performance electronic equipment due to its excellent thermal conductivity and mechanical strength. This guide will introduce the key elements and best practices of metal substrate PCB design to help engineers effectively utilize this technology to optimize electronic designs.
Metal substrate PCB is a special type of printed circuit board whose base material is metal instead of traditional non-conductive base materials such as FR4. This design not only improves the heat dissipation performance of the circuit board, but also enhances its durability and stability in harsh environments. It is especially suitable for applications that require high power and high-density integrated electronic components.
Choose metal materials suitable for high-temperature environments and high-power electronic devices, such as aluminum, copper or their alloys. These materials have excellent thermal conductivity and mechanical strength, effectively dissipating heat and reducing thermal stress.
Optimize the heat dissipation design, including the layout of heat sinks and heat dissipation channels, to ensure that electronic components maintain a stable operating temperature when working under high loads.
Design multi-layer structures to meet the connection needs of complex circuits while maximizing PCB space utilization.
Metal substrate PCB design not only improves the performance and reliability of electronic devices, but also provides engineers with powerful tools in the design of high-performance and high-density integrated circuits. By following the design elements and best practices in this guide, engineers can more effectively utilize metal substrate PCB technology and promote innovation and development in electronic design.
What material is used in Metallic Substrate?
Metallic Substrate, as a special type of printed circuit board (Печатная плата), mainly uses metal materials as its base, which is different from traditional non-conductive base materials. Common metal substrate materials include aluminum, copper and other alloys. These materials have excellent thermal conductivity and mechanical strength and are suitable for the design of electronic devices that require efficient heat dissipation and stable performance.
Aluminum substrates are widely used due to their superior thermal conductivity properties. It has good heat dissipation capabilities and can effectively conduct the heat generated by the circuit board to the surrounding environment. Aluminum substrates are commonly used in high-power LED lamps, power modules and other electronic devices that require efficient heat dissipation.
Copper substrate has high electrical conductivity and mechanical strength, making it suitable for demanding communication equipment and industrial control systems. The copper substrate can provide stable signal transmission and power distribution, and has good corrosion resistance, making it suitable for long-term stable operation under various environmental conditions.
In addition to aluminum and copper, some special alloys are also used as material choices for metal substrates. Например, iron-nickel alloys have good resistance to high temperatures and corrosion, making them suitable for electronic devices that need to operate in extreme environments, such as circuit board designs in aerospace and military applications.
Metal substrate PCBs demonstrate significant advantages in many fields due to the properties of their materials:
Optimized heat dissipation performance: It can effectively reduce the operating temperature of circuit components and improve the reliability and stability of the equipment.
Enhanced mechanical strength: Reduces the impact of vibration and mechanical stress on the circuit board, extending its service life.
Adapt to complex environments: Able to maintain stable performance under various harsh environmental conditions, such as high temperature, high humidity or chemically corrosive environments.
Резюме, metal substrates, as an indispensable part of modern electronic equipment, provide reliable solutions and technical support for various application scenarios through their unique material advantages and design flexibility. As technology continues to advance, the importance of metal substrate PCBs in electronic design will continue to increase, bringing more possibilities for future innovation.
What size are Metallic Substrate?
As an important part of modern electronic design, metal substrates have various needs and characteristics in different application scenarios due to their size and application fields. Below is a detailed discussion on metal substrate dimensions and their applications.
The size of the metal substrate can vary depending on the specific application needs. Типично, metal substrates can range from a few millimeters to tens of centimeters. Small metal substrates are commonly found in mobile devices and small electronic products, such as smartphones, tablets, и так далее. These products usually require circuit boards to be compactly laid out in a limited space to meet the requirements of high integration and lightweight design. Large metal substrates are more used in fields such as industrial equipment, power systems, and communication infrastructure to support applications with complex circuits and high power requirements.
Metal substrates play an important role in many fields, and their main applications include but are not limited to the following aspects:
Industrial automation: used in industrial control systems, automated production lines and robotics to support complex control logic and high-speed data transmission.
Automotive electronics: widely used in automotive electronic control systems, driving assistance systems and infotainment systems to provide reliable circuit protection and efficient energy management.
Aerospace: used in avionics equipment, aviation communications and navigation systems, requiring high temperature resistance, vibration resistance and lightweight design.
Energy management: Supporting high power density and long-term reliable operation in power systems, solar and wind energy conversion devices.
With the continuous advancement of technology and the growth of market demand, the application of metal substrates in electronic design is constantly expanding. In the future, as the demand for high performance and low energy consumption increases, metal substrates will continue to exert their advantages in improving circuit performance, optimizing heat dissipation, and enhancing mechanical strength. At the same time, as the size of electronic products continues to shrink and their functions continue to increase, the demand for miniaturized and integrated metal substrates will further increase.
Резюме, metal substrates not only play a key role in traditional industrial and communication applications, but their applications in emerging technology fields such as artificial intelligence, the Internet of Things, and smart manufacturing are also expanding. Through reasonable selection of size and materials, metal substrates can provide reliable circuit support and optimized performance for various electronic devices, promoting the progress and development of the entire electronics industry.
The Manufacturer Process of Metallic Substrate.
As a special type of printed circuit board (Печатная плата), the manufacturing process of metal substrate is different from traditional non-conductive substrates. It focuses on improving thermal conductivity and mechanical strength, and is suitable for high-power and high-density electronic designs. The following is an overview of the main manufacturing processes for metal substrates:
The manufacturing process of metal substrates begins with the design and layout phase. Using computer-aided design (ХАМ) программное обеспечение, engineers determine the layout of the circuit board based on circuit requirements and space constraints, including the placement of various components and the design of connection paths.
The first step in manufacturing a metal substrate is to prepare the substrate material. Commonly used metals include aluminum, copper or other alloys. These substrate materials are cut and surface cleaned to ensure good surface roughness and geometric accuracy.
After the substrate is prepared, the next step is to laminate the copper foil to the metal substrate. These copper foil layers are used for subsequent circuit patterning and establishment of signal transmission paths. The temperature and pressure need to be strictly controlled during the lamination process to ensure that the copper foil is firmly bonded to the substrate.
Once the copper foil layer is successfully bonded to the substrate, the next step is to form the circuit pattern through an etching process. Etching is the use of chemical solutions or mechanical methods to remove unnecessary copper foil, leaving only the parts required to form circuit paths. This step requires precise control of etching time and solution concentration to avoid excessive etching or residue of circuit paths.
After completing the circuit patterning, drilling and via coating are next. These holes are used to mount electronic components and connect signal transmission between circuit layers. Via-hole coating is a metal layer coated on the hole wall to improve connection reliability and conductive performance.
To enhance the board’s durability and performance, metal plating and protective coatings are applied next. Metal plating is often used to enhance electrical conductivity and corrosion resistance, while protective coatings are used to protect circuits from external environmental effects, such as moisture, chemicals, and mechanical wear.
The final step is final testing and quality control. Ensure metal substrates meet design specifications and customer requirements through electrical testing, optical inspection and mechanical performance evaluation. These tests include checking circuit connectivity, thermal conductivity and environmental resistance to ensure each metal substrate will perform well in real-world applications.
Through the above precise manufacturing process, metal substrates can meet the needs of various high-demand electronic applications, from consumer electronics to industrial equipment, providing a solid foundation and reliable support for modern technological innovation.
The Application area of Metallic Substrate.
Metal substrates are used in a wide range of applications in modern electronic technology, and their excellent thermal conductivity and mechanical strength make them ideal for many critical applications. The following are the main applications of metal substrates in different fields:
В автомобильной промышленности, metal substrates are widely used in electric control units (ECUs) and battery management systems (BMS) of electric vehicles. The metal substrate can effectively dissipate heat, ensuring that electronic components work stably in high-temperature environments. It is also resistant to vibration and environmental corrosion, ensuring the reliability and long life of the vehicle’s electronic system.
In the field of industrial automation, metal substrates are used to manufacture control modules and sensor systems for industrial robots. These applications usually require circuit boards to withstand complex working environments and frequent operations. Metal substrates can provide the necessary durability and stability to ensure efficient operation and production efficiency of the equipment.
The LED lighting industry has high requirements for the thermal conductivity of circuit boards to ensure that LED lamps can effectively dissipate heat when working at high power for a long time and avoid overheating that affects light efficiency and lifespan. The excellent thermal conductivity of metal substrates makes them the preferred substrate material for LED lamps, which can effectively improve the stability and reliability of the product.
In the communication field, such as base stations and communication network equipment, metal substrates are widely used in the manufacture of high-frequency circuits and microwave devices. Metal substrates can not only provide good signal transmission characteristics, but also effectively reduce signal loss and interference, ensuring the performance and signal quality of communication equipment.
Medical electronic equipment has extremely high requirements for the reliability and safety of circuit boards. Metal substrates are widely used in pacemakers, medical imaging equipment and diagnostic tools because of their stable performance and ability to resist environmental influences. These devices must operate reliably in a variety of environmental conditions, and metal substrates provide the required support and protection.
Вообще, metal substrates are widely used in many high-demand electronic equipment fields due to their excellent thermal conductivity, mechanical strength, and stability. With the advancement of technology and the continuous expansion of application requirements, the role and influence of metal substrates in the electronics industry will be further enhanced, providing key support and guarantee for various innovative electronic designs.
What are the advantages of Metallic Substrate?
As an important type of PCB (Printed Circuit Board), metal substrate has unique advantages and application value compared with traditional non-conductive substrates such as FR4.
Metal substrates are known for their excellent thermal conductivity, which can effectively disperse the heat generated by electronic components, thereby maintaining the stability and reliability of the circuit board. Especially suitable for high-power electronic equipment, such as LED lamps and power amplifiers, it can effectively reduce temperature gradients and extend the service life of equipment.
Compared with traditional substrates, metal substrates usually have higher mechanical strength and vibration resistance, and can maintain the stability of circuits in harsh environments. This makes metal substrates widely used in industrial control systems, automotive electronics and aerospace fields, and can withstand stress caused by vibration, shock and temperature changes.
The metal substrate itself has good electromagnetic shielding properties and can effectively reduce the impact of electromagnetic interference on surrounding electronic equipment. It is particularly important in communications and radio frequency sensitive applications, helping to improve the signal integrity of the device and the reliability of data transmission.
The excellent thermal conductivity and mechanical strength of metal substrates enable it to support the design of complex circuits and the layout of high-density components. Through multi-layer structure and precise manufacturing process, metal substrate PCB can achieve more functions and connections in a limited space, thereby meeting the dual needs of modern electronic equipment for performance and volume.
Metal-based PCBs can generally be recycled and reused more easily, and their production consumes relatively less energy and resources than traditional substrates. This makes metal substrates an attractive choice in today’s pursuit of environmental protection and sustainable development.
Вообще, metal substrate PCB provides important technical support for the performance improvement and reliability assurance of modern electronic equipment with its superior thermal management capabilities, high mechanical strength, excellent electromagnetic shielding performance and ability to support complex circuit design. and solutions. With the advancement of technology and the expansion of application fields, metal substrate PCB will continue to exert its unique advantages to promote progress and innovation in the electronics industry.
Вопросы и ответы
What are the advantages of metal substrate PCB compared with traditional FR4 PCB?
Compared with traditional FR4 PCB, the main advantage of metal substrate PCB lies in its better thermal management capabilities and mechanical strength. Metal substrates can effectively improve the heat dissipation effect of circuit boards and are suitable for designs that require high power and high density electronic components. В дополнение, metal substrates can also reduce the impact of circuit board temperature fluctuations on the stability of electronic components, and are therefore widely used in industrial control, automotive electronics and other fields.
How to choose a suitable metal substrate material?
Selecting a suitable metal substrate material requires consideration of factors such as application environment, heat dissipation requirements, and mechanical strength. Common metal substrate materials include aluminum substrates, copper substrates and iron-nickel alloys, each of which has its own unique advantages. Например, aluminum substrates are suitable for LED lamps and power modules that require excellent heat dissipation performance, while copper substrates are common in high-frequency communication equipment and industrial control systems.
How to optimize the heat dissipation effect of metal substrate in PCB design?
To optimize heat dissipation from metal substrates, design engineers can adopt a variety of strategies. Первый, the heat dissipation area and vents should be properly designed to increase air flow and promote heat dissipation. Во-вторых, select the appropriate metal substrate thickness and material to improve thermal conductivity. Наконец, consider using accessories such as heat sinks or thermal pads to further improve heat dissipation.
In which industries are metal substrate PCBs most widely used?
Metal substrate PCB is widely used in consumer electronics, Автомобильная электроника, industrial automation, aerospace and other fields. Например, in consumer electronics, they are used for power management and processor cooling in high-performance devices such as mobile phones and tablets. In the field of automotive electronics, metal substrate PCBs are used in vehicle electronic control systems and infotainment equipment and are favored for their stability and high temperature resistance.
How to evaluate the cost-effectiveness of metal substrate PCB?
When evaluating the cost-effectiveness of a metal substrate PCB, factors such as design requirements, Выбор материала, and manufacturing complexity need to be considered. Although the initial cost of a metal-based PCB may be higher, the long-term stability and performance benefits often offset the additional cost. В дополнение, accurate cost analysis also needs to consider factors such as mass production efficiency and maintenance costs to ensure that the overall cost is controlled within a reasonable range.