Ultra-Multilayer FC-BGA Package Substrates Manufacturer.We specialize in crafting ultra-multilayer FC-BGA package substrates, employing cutting-edge techniques for superior performance and reliability. Our expertise lies in designing and manufacturing substrates with intricate layering, ensuring optimal electrical connectivity and thermal management. Trust us as your go-to manufacturer for top-tier FC-BGA package substrates that meet the most demanding requirements of modern electronic applications.
With the continuous development of electronic equipment, the demand for high-performance, high-density circuit boards continues to increase. As an advanced technology, ultra-multilayer FC-BGA packaging substrate is gradually becoming an ideal choice to meet this demand. This article will delve into the characteristics, applications and advantages of ultra-multilayer FC-BGA packaging substrates.
What are Ultra-Multilayer FC-BGA Package Substrates?
Ultra-Multilayer FC-BGA Package Substrates is a highly integrated printed circuit board technology that uses ultra-multilayer technology and FC-BGA packaging. In this technology, multi-layer circuit boards are combined through precision stacking and interconnection processes, while using Fine-Pitch Ball Grid Array (FC-BGA) packaging to achieve high-performance and high-density circuit designs.
The main features of this technology include:
High-density design: Through multi-layer stacking technology, higher circuit density and component integration are achieved, which is suitable for complex circuit design and can meet the high performance and high density requirements of modern electronic equipment.
FC-BGA packaging: Using FC-BGA packaging, the circuit board has higher integration and smaller package size while maintaining high performance, making it suitable for space-limited application scenarios.
Optimized design: By optimizing the layout and shielding design, the electromagnetic interference between circuit boards is reduced, the stability of signal transmission is improved, and the reliability and stability of the circuit board are ensured.
Wide range of applications: Ultra-Multilayer FC-BGA Package Substrates are widely used in communication equipment, automotive electronics, medical equipment, industrial automation and other fields, providing high performance and reliability solutions for various applications.
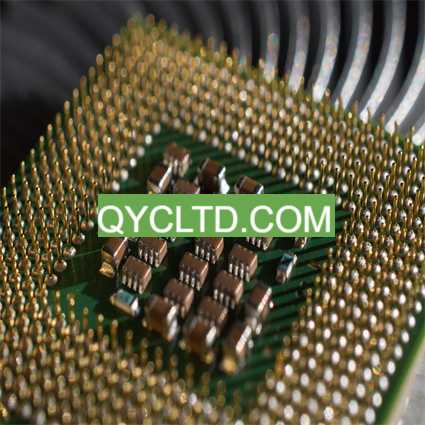
Ultra-Multilayer FC-BGA Package Substrates Manufacturer
In short, the introduction of Ultra-Multilayer FC-BGA Package Substrates technology provides new possibilities for the development of electronic equipment and provides more efficient and reliable solutions for application scenarios in various industries.
Ultra-Multilayer FC-BGA Package Substrates design Reference Guide.
Ultra-Multilayer FC-BGA packaging substrate is an advanced printed circuit board technology that provides important support for the design of high-performance electronic devices. The following are the main contents of the design reference guide:
Ultra-Multilayer FC-BGA packaging substrate uses multi-layer stacking technology to achieve highly integrated circuit functions through precise layout and interconnection design. The design process should fully consider factors such as circuit layout, signal integrity, and thermal management.
Proper layout is key to ensuring circuit board performance and reliability. During the layout process, component locations and signal paths should be optimized based on circuit functions and signal transmission requirements to minimize signal interference and crosstalk.
The design of Ultra-Multilayer FC-BGA packaging substrate should consider signal integrity, including signal transmission speed, transmission line length, impedance matching and other factors. Technologies such as differential signal transmission and hierarchical layout between signal layers are used to improve the stability and reliability of signal transmission.
Due to the increase in high integration and power density, thermal management has become an important issue in Ultra-Multilayer FC-BGA package substrate design. Appropriate heat dissipation design and materials should be used to ensure that the circuit board maintains good heat dissipation performance when operating under high loads.
Selecting the appropriate FC-BGA package is one of the key decisions in the design process. The appropriate package type and density should be selected based on factors such as circuit complexity, power requirements, and space constraints to achieve optimal performance and reliability.
The manufacturing process of Ultra-Multilayer FC-BGA packaging substrate requires high-precision process control and advanced production equipment. Designers should work closely with manufacturers to ensure that the design meets manufacturing requirements and conduct necessary design verification and sample testing.
The Ultra-Multilayer FC-BGA package substrate design reference guide is designed to help designers fully understand the characteristics and design points of this technology, so as to better apply it to the design of high-performance electronic equipment. Through reasonable layout, signal integrity and thermal management design, the high performance and reliability of the circuit board can be achieved and promote the continuous development of electronic technology.
What size are Ultra-Multilayer FC-BGA Package Substrates?
The ultra-multilayer FC-BGA packaging substrate uses a series of high-performance materials to ensure its excellent performance in high-density, high-speed and high-reliability applications. Main materials include:
Substrate material: The basic material of ultra-multilayer FC-BGA packaging substrate is usually high-performance glass fiber reinforced epoxy resin (FR-4) or polyimide (PI). These materials have excellent mechanical strength and thermal stability. and electrical insulation performance, able to meet the requirements of complex circuit design.
Conductive layer material: The conductive layer of the ultra-multilayer FC-BGA package substrate usually uses high-purity copper foil to ensure good conductive performance and reliable soldering connections. Copper foil has good electrical conductivity and processability, and can meet the needs of high-speed signal transmission and high-density layout.
Insulating layer material: In the super multi-layer FC-BGA packaging substrate, the insulating layer plays the role of isolation and support. Glass fiber cloth or thin glass fiber cloth impregnated with epoxy resin (Prepreg) is usually used. These materials have good insulation properties. and mechanical strength, which can effectively isolate the circuit between conductive layers and provide stable support.
Solder material: The solder material of ultra-multilayer FC-BGA package substrate usually uses lead-free solder or low-temperature solder to ensure the reliability and environmental protection of the soldering connection. These solder materials have good welding performance and thermal stability, and can meet the requirements of high-temperature welding and long-term stable operation.
Solder mask material: The solder mask is used to cover the surface of the circuit board to protect the wires and pads. It usually uses a mixture of epoxy resin and pigments. It has good heat resistance, chemical resistance and wear resistance, and can effectively prevent soldering. Short circuit and metal oxidation.
To sum up, the ultra-multilayer FC-BGA packaging substrate uses a series of high-quality materials, including high-performance substrate materials, conductive layer materials, insulating layer materials, solder materials and solder mask materials, ensuring its high-density , excellent performance and stability in high-speed and high-reliability applications.
The Manufacturer Process of Ultra-Multilayer FC-BGA Package Substrates.
The manufacturing process of the ultra-multilayer FC-BGA packaging substrate has gone through a series of precise and complex process steps to ensure its high performance and reliability. The following is an overview of its main manufacturing processes:
Substrate Preparation: The first step in the manufacturing process is substrate preparation. Choose high-quality substrate materials such as fiberglass-reinforced epoxy (FR-4) to ensure the mechanical strength and electrical performance of the circuit board. The substrate is cleaned and surface-treated in preparation for subsequent process steps.
Stacking and lamination: The ultra-multilayer FC-BGA packaging substrate uses multi-layer stacking technology to stack multiple single-layer circuit boards according to design requirements. During the lamination process, conductive glue or copper foil is coated between each layer of circuit boards to form an interconnect layer. Then, the stacked circuit boards are pressed together into one body through a lamination process to form a multi-layer circuit board structure.
Copper foil processing: The surface of the laminated multi-layer circuit board is coated with copper foil to form a conductive layer. According to the design requirements, methods such as chemical etching or mechanical etching are used to peel off or remove the excess copper foil to form the circuit pattern and connection holes of the circuit board.
Finished product inspection: Strict quality inspection is required at every stage of the manufacturing process. After the copper foil processing is completed, the circuit board is inspected for appearance, dimensional measurement, and line connectivity testing to ensure that the quality of each circuit board meets standard requirements.
Surface treatment: Apply protective copper coating or solder paste to the surface of the circuit board to improve soldering performance and corrosion protection. The surface treatment process also includes spray metallization to form a solderable metal layer on the surface of the circuit board.
Finished product testing and packaging: The manufactured ultra-multilayer FC-BGA packaging substrate needs to undergo final functional testing and reliability testing to ensure that its performance and reliability meet the design requirements. Through high-temperature aging testing, electrical performance testing and other means, the stability of the circuit board in various working environments is verified. Finally, the tested circuit boards are packaged to prevent damage during transportation and storage.
In general, the manufacturing process of ultra-multilayer FC-BGA packaging substrates involves multiple precise process steps and requires a high degree of technical and equipment support. Through strict quality control and testing, the high performance and reliability of circuit boards are ensured, meeting the needs of high-density, high-performance circuit boards in various application scenarios.
The Application area of Ultra-Multilayer FC-BGA Package Substrates.
Ultra-multilayer FC-BGA packaging substrates are widely used in various fields. First of all, it plays a key role in the field of communications, used for high-speed data transmission and network communication equipment, such as routers, switches, etc. Its high density and optimized design enable communication equipment to achieve faster signal transmission speeds and more stable network connections, meeting the strict requirements for performance and reliability of modern communication systems.
Secondly, in the field of automotive electronics, ultra-multilayer FC-BGA packaging substrates are widely used in vehicle control systems, vehicle entertainment systems, etc. The demand for high performance and high reliability in automotive electronic systems is growing day by day. The ultra-multilayer FC-BGA packaging substrate improves the performance and reliability of automotive electronic systems through compact packaging design and optimized layout, while also meeting the requirements of automotive electronic systems. Requirements for compact space and lightweight design.
In addition, in the field of medical equipment, ultra-multilayer FC-BGA packaging substrates are used in medical imaging equipment, patient monitoring equipment, etc. Medical equipment has particularly prominent requirements for high performance and high reliability. The ultra-multilayer FC-BGA packaging substrate ensures the stability and reliability of medical equipment through optimized design and high-quality manufacturing processes, providing a platform for the development of the medical industry. Reliable technical support.
Finally, in the field of industrial automation, ultra-multilayer FC-BGA packaging substrates are widely used in industrial control systems, robot control systems, etc. Industrial automation has a high demand for high-performance and high-reliability control systems. The ultra-multilayer FC-BGA packaging substrate improves the performance and stability of the control system, improves industrial production efficiency and automation levels, and promotes the development of industrial automation technology. and applications.
In summary, ultra-multilayer FC-BGA packaging substrates are widely used in communications, automotive electronics, medical equipment, industrial automation and other fields. Its excellent performance and reliability will provide strong support for the development of various industries. .
What are the advantages of Ultra-Multilayer FC-BGA Package Substrates?
The ultra-multilayer FC-BGA packaging substrate has many advantages, making it a popular choice in the design of modern electronic equipment.
First of all, the ultra-multilayer FC-BGA packaging substrate achieves high integration and high-density layout in circuit design. Through multi-layer stacking technology, more circuit components and connection lines can be accommodated in a limited space, thereby achieving more complex circuit designs. This high-density layout not only saves space, but also reduces the overall size of the circuit board, making it suitable for a variety of space-constrained application scenarios, such as smartphones, tablets and other portable devices.
Secondly, the ultra-multilayer FC-BGA packaging substrate has excellent electromagnetic compatibility and signal integrity. Through optimized layout and shielding design, electromagnetic interference between circuit boards is effectively reduced, ensuring the stability and reliability of signal transmission. This characteristic makes it particularly suitable for applications with high signal quality requirements, such as communication equipment, medical equipment, etc.
In addition, the ultra-multi-layer FC-BGA packaging substrate uses advanced manufacturing processes and high-quality materials to ensure the stability and reliability of the circuit board. Its excellent performance makes it the preferred circuit board solution in harsh environments such as industrial and aerospace. At the same time, high reliability also brings longer service life and lower maintenance costs to equipment manufacturers.
In short, the ultra-multilayer FC-BGA packaging substrate has become an ideal choice in the design of various electronic equipment due to its high integration, excellent signal integrity and stable and reliable performance. Its advantages are not only reflected in improving the flexibility and performance of circuit design, but also providing a strong guarantee for the reliable operation of electronic equipment and promoting the continuous progress of electronic technology.
FAQ
What is FC-BGA package?
FC-BGA (Fine-Pitch Ball Grid Array) packaging is a high-density, high-performance packaging technology in which tiny solder balls are arranged in a grid form to connect chips and printed circuit boards (PCBs). It is usually used in electronic devices with high integration and small package size, providing better performance and reliability.
What is the difference between ultra-multilayer FC-BGA packaging substrate and traditional circuit board?
The ultra-multilayer FC-BGA packaging substrate uses multi-layer stacking technology, which has higher circuit density and component integration than traditional circuit boards. In addition, it has the advantages of lower electromagnetic interference, higher reliability and more compact package size.
What fields are ultra-multilayer FC-BGA packaging substrates suitable for?
Ultra-multilayer FC-BGA packaging substrate is widely used in communication equipment, automotive electronics, medical equipment, industrial automation and other fields. They are suitable for applications requiring high performance, high reliability and compact packaging.
What are the advantages of ultra-multilayer FC-BGA packaging substrate?
This packaging substrate has the advantages of high density, low electromagnetic interference, high reliability and compact packaging. They improve board performance, save space, and ensure long-term stable operation.
What factors need to be considered when selecting a super multi-layer FC-BGA packaging substrate?
When selecting a super multi-layer FC-BGA packaging substrate, factors such as its performance indicators, packaging size, environmental adaptability, and manufacturer’s reputation need to be considered. Make sure you choose a product that meets your project needs and has guaranteed reliability.