What is RF High Frequency Flip Chip Substrate?
RF High Frequency Flip Chip Substrate Manufacturer. An RF High Frequency Flip Chip Substrate Manufacturer specializes in crafting advanced substrates for flip chip technology, specifically tailored for high-frequency radio frequency applications. With precision engineering and cutting-edge materials, they fabricate substrates optimized for seamless integration in RF circuits, ensuring exceptional signal integrity and minimal interference. Their expertise lies in creating substrates that meet stringent performance requirements, enabling seamless communication in wireless devices, radar systems, and satellite communications. Committed to innovation, they continually push boundaries in RF substrate design, empowering next-generation technologies with enhanced reliability and performance.
RF high-frequency flipping chip substrate is an important technology in the field of radio frequency electronic device manufacturing today, providing a stable and reliable electronic platform for modern communications, radar, satellite communications and other applications. This special type of PCB exhibits excellent performance and reliability in high-frequency environments, becoming a key link in the field of RF electronics.
One of the keys to RF high-frequency flip chip substrate design is its material selection. Usually, these substrates use high-frequency materials, such as PTFE (polytetrafluoroethylene), etc., to ensure excellent electrical performance in high-frequency environments. PTFE material has low dielectric loss and excellent insulation properties, is suitable for high-frequency signal transmission, and can effectively reduce signal attenuation and ensure signal stability and reliability.
Precision manufacturing technology is the key to ensuring stable performance of RF high-frequency flip chip substrates. During the manufacturing process, strict quality control and precision processing technology ensure the flatness and surface quality of the plates, thereby ensuring good signal transmission and reliability. In addition, advanced production equipment and process technology also provide a strong guarantee for the manufacturing of RF high-frequency flip chip substrates, enabling it to meet increasingly demanding high-frequency application requirements.
RF high-frequency flip chip substrates play a key role in the manufacturing of high-frequency electronic devices. It not only provides a stable and reliable electrical connection, but also maintains good signal transmission characteristics in high-frequency environments. Therefore, whether in the fields of communications, radar or satellite communications, RF high-frequency flip chip substrates play an irreplaceable role.
In short, the RF high-frequency flip chip substrate is the key link to the high-frequency world, and its stability and reliability provide a solid foundation for the development of modern radio frequency electronic devices. By continuously improving materials, processes and technical levels, we can expect RF high-frequency flip chip substrates to be more widely used in the future, bringing more surprises and possibilities to the development of high-frequency electronics.
RF High Frequency Flip Chip Substrate design Reference Guide.
In the field of RF high-frequency flip chip substrate manufacturing, a good reference guide is crucial to ensure product quality and performance. Here are some key takeaways for reference:
Understand the properties of high frequency materials
RF high-frequency flipping chip substrates usually require the use of high-frequency materials, such as PTFE (polytetrafluoroethylene), PTFE composite materials, and special ceramic materials. These materials have low dielectric constant, low loss factor and good high-frequency performance, ensuring stable signal transmission and performance in high-frequency environments. Manufacturers need a deep understanding of the properties of different materials in order to select the appropriate material for specific application needs.
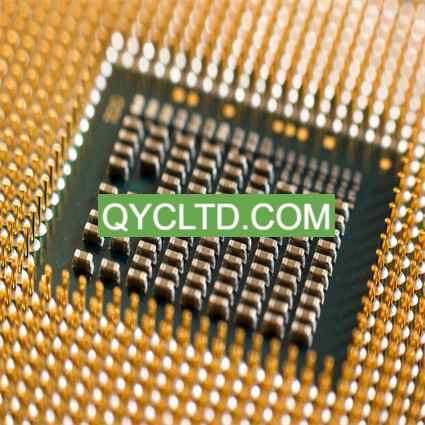
RF High Frequency Flip Chip Substrate Manufacturer
Master advanced design software and tools
In the design process of RF high-frequency flip chip substrate, the use of advanced design software and tools can improve design efficiency and accuracy. These tools usually include CAD (computer-aided design) software, simulation tools and layout tools, etc., which can help manufacturers perform circuit design, layout optimization and signal simulation to ensure that the design meets high-frequency requirements and meets performance indicators.
Learn about the latest manufacturing technologies and standards
With the continuous development of science and technology, RF high-frequency flip chip substrate manufacturing technology is also constantly improving. Manufacturers need to keep up with the latest manufacturing technologies and standards in the industry and continuously improve and optimize manufacturing processes to improve product quality and production efficiency. In addition, understanding the latest industry standards and certification requirements can help manufacturers ensure that their products comply with relevant regulations and standards and enhance market competitiveness.
In summary, having a good reference guide is crucial for RF high-frequency flip chip substrate manufacturers. By having a deep understanding of the properties of high-frequency materials, mastering advanced design software and tools, and understanding the latest manufacturing technologies and standards, manufacturers can improve product quality, reduce production costs, and achieve greater success in a highly competitive market.
What material is used in RF High Frequency Flip Chip Substrate?
The performance and reliability of RF high-frequency flip chip substrates depend largely on the materials used. In this field, common materials include high-frequency materials such as PTFE and FR-4, as well as special materials such as metallized ceramics. Let’s take a closer look at these materials and their role in RF high-frequency flip chip substrate manufacturing.
PTFE (polytetrafluoroethylene)
PTFE is a material widely used in high-frequency circuits and is favored for its low dielectric constant, low loss and excellent high-frequency performance. In RF high-frequency flip chip substrates, PTFE is usually used as the base material, which can effectively reduce losses during signal transmission and provide stable performance.
FR-4 (fiberglass reinforced epoxy resin)
FR-4 is a common substrate material that is widely used in general PCB manufacturing. However, in the manufacturing of RF high-frequency flip chip substrates, special FR-4 materials are selected, which have lower dielectric constants and losses to meet the requirements in high-frequency environments. Although the high-frequency performance of FR-4 is slightly inferior to PTFE, it still has certain advantages in certain application scenarios.
Metallized ceramics
Metallized ceramic is a special material with excellent high-frequency performance and high-temperature resistance. In the manufacturing of RF high-frequency flip chip substrates, metallized ceramics are often used as substrate materials, and their surfaces are coated with a conductive metal layer to achieve good signal transmission and ground shielding effects. Metallized ceramic materials can provide stable performance in extreme environments and are therefore widely used in some applications that require extremely high stability.
In general, the materials used in the manufacturing of RF high-frequency flip chip substrates have strict requirements and need to have excellent high-frequency performance, low loss, stable characteristics, and good environmental resistance. Material selections such as PTFE, special FR-4, and metallized ceramics can effectively meet these requirements and provide a solid foundation for the performance of RF high-frequency flip chip substrates. When selecting materials, manufacturers need to consider specific application needs and performance requirements to ensure the quality and performance of the final product meet expectations.
What size are RF High Frequency Flip Chip Substrate?
The size of the RF high-frequency flip chip substrate is one of the crucial considerations in the design and manufacturing process. These sizes are often based on specific application needs, as different applications require different sized substrates for optimal performance and functionality. The following is a detailed discussion on the substrate size of RF high-frequency flip chip:
Micro size chip level
In some application scenarios, especially in mobile devices and microelectronics, there are strict restrictions on the size of the PCB. RF high-frequency flip chip substrates can be designed into tiny sizes to fit into these compact space requirements. This micro-sized substrate is usually integrated into microchips or modules, such as smartphones, tablets, headphones and other devices.
Micro-sized substrates require advanced manufacturing technology and precision processes to ensure circuit layout and connections within a limited space while maintaining good signal integrity and stability.
Large size communication equipment level
On the other hand, some application scenarios require larger-sized RF high-frequency flip chip substrates, especially in fields such as communication equipment and radar systems. These large-sized substrates usually carry complex circuits and functional modules, requiring high integration and reliability.
Large-sized substrates can accommodate more electronic components and connection lines, allowing for more complex circuit designs and functional implementations. They are usually used to manufacture high-performance communication equipment, such as base stations, satellite communication systems, radar systems, etc.
Flexible size design
The size design of RF high-frequency flip chip substrates is usually flexible and can be adjusted and customized according to specific application requirements. Manufacturers can design and manufacture substrates in different sizes according to customer requirements and equipment specifications to ensure optimal performance and adaptability.
The flexible size design also provides possibilities for emerging application fields and technologies, such as the Internet of Things (IoT), 5G communications, medical electronics, etc. Manufacturers can customize RF high-frequency flip chip substrates that meet specific requirements based on the needs of different industries and fields to promote technological progress and innovation.
The size design of RF high-frequency flip chip substrate is a complex and critical process, which directly affects the performance, function and applicability of the product. Through flexible size design and customized manufacturing, manufacturers can meet the needs of various application scenarios and provide customers with the best solutions and products.
The Manufacturer Process of RF High Frequency Flip Chip Substrate .
The manufacturing process of RF high-frequency flip chip substrate is a complex and precise process that requires multiple critical steps to ensure product performance and reliability. The manufacturing process of RF high-frequency flip chip substrate will be introduced in detail below.
Design
The first step in manufacturing an RF high-frequency flip chip substrate is design. Factors such as circuit layout, signal transmission paths, power distribution, and heat dissipation need to be considered during the design process. Designers use professional circuit design software to design to ensure that performance requirements can be met in high-frequency environments.
Material selection
Choosing the right materials is critical to the performance of RF high-frequency flip chip substrates. Commonly used materials include PTFE (polytetrafluoroethylene), FR-4 (glass fiber composite) and other high-frequency materials. They have low loss, high dielectric constant and other characteristics, and can meet the requirements of high-frequency environments.
Plate preparation
During the board preparation stage, the selected materials will be cut into required size substrates and surface treated to improve welding and printing accuracy. This step requires strict control of the thickness, surface flatness and roughness of the plate to ensure the smooth progress of subsequent processes.
Printing
Printing is one of the key steps in the manufacturing of RF high-frequency flip chip substrates. During the printing process, conductive ink is printed on the surface of the substrate to form circuit patterns and component connection points. The printing process requires high-precision equipment and process control to ensure the accuracy and stability of the circuit.
Assemble
Assembly is the process of mounting various components (such as chips, resistors, capacitors, etc.) onto a substrate. During the assembly process of RF high-frequency flip chip substrates, advanced welding technology and precise position control are required to ensure a stable and reliable connection between components and substrates.
QC
Quality control is a vital part of the entire manufacturing process. Through strict quality control measures, including raw material inspection, process monitoring, finished product testing, etc., we ensure that products meet specified performance indicators and standards. Only through strict quality control can the stability and reliability of RF high-frequency flip chip substrates be guaranteed.
In summary, the manufacturing process of RF high-frequency flip chip substrates involves multiple key steps and requires precise manufacturing processes and strict quality control. Only through continuous optimization and improvement of manufacturing technology can we produce RF high-frequency flip chip substrates with stable performance and reliable quality, providing solid support for the development of electronic equipment.
The Application area of RF High Frequency Flip Chip Substrate .
RF High Frequency Flip Chip Substrate plays a vital role in the field of modern technology, and its wide range of applications covers wireless communications, radar, satellite communications, medical equipment and other fields. These fields have extremely high requirements for the performance and reliability of high-frequency electronic devices, and RF high-frequency flip chip substrates are a key component that can meet these needs.
Wireless communication
In the field of wireless communication, the development and popularization of 5G communication technology has put forward higher requirements for high-performance and high-reliability radio frequency devices. RF high-frequency flip chip substrate can provide stable high-frequency performance and low signal loss, making it an ideal choice for various wireless communication equipment, including base stations, antennas, RF front-end modules, etc.
Radar
Radar systems play a vital role in military, civilian and other fields, and the application of high-frequency flip chip substrates in radar systems is particularly prominent. Since the radar system needs to detect targets quickly and accurately and transmit data, it has extremely high requirements on the performance and stability of its radio frequency components. The RF high-frequency flip chip substrate is an ideal choice to meet these requirements.
Satellite Communications
Satellite communications are an important part of the modern communications field, and RF high-frequency flip chip substrates are one of the indispensable key components in satellite communications systems. Satellite communication systems need to maintain stable signal transmission and data transmission under extreme environmental conditions, and high-frequency flip chip substrates can provide stable high-frequency performance and reliability to ensure the normal operation of satellite communication systems.
Medical equipment
In the field of medical equipment, such as medical imaging equipment, wireless medical monitoring equipment, etc., the performance and reliability requirements of radio frequency devices are also very high. The RF high-frequency flip chip substrate can provide stable high-frequency performance and low signal loss, making it an important component of various medical equipment, providing a solid foundation for technological progress in the medical field and patient health protection.
In general, RF high-frequency flip chip substrates play an important role in many fields such as wireless communications, radar, satellite communications, medical equipment, etc. Its stable performance and reliability provide a solid foundation for these applications. With the continuous development and progress of science and technology, it is believed that RF high-frequency flip chip substrates will play a more important role in more fields and promote the continuous innovation and development of all walks of life.
What are the advantages of RF High Frequency Flip Chip Substrate?
RF high-frequency flip chip substrate plays a vital role in modern high-frequency electronic equipment. It has obvious advantages. Compared with traditional PCB, it has the following outstanding features:
Better high frequency performance
The RF high-frequency flip chip substrate uses special high-frequency materials and precise manufacturing processes to achieve better performance in high-frequency environments. They can effectively reduce the attenuation and distortion of high-frequency signals, providing more stable and reliable signal transmission.
Lower signal loss
Since the RF high-frequency flip chip substrate uses high-quality high-frequency materials and precise manufacturing processes, its signal transmission loss is relatively low. This means that during signal transmission, the strength and quality of the signal can be maintained to the maximum extent, thereby improving the performance and efficiency of the entire system.
Higher integration
The RF high-frequency flip chip substrate has a higher integration level and can achieve more complex and compact circuit designs. By integrating multiple functional modules on the same substrate, the number of connections and wiring in the system can be reduced, improving the reliability and stability of the system while reducing the overall cost and volume.
Smaller size
Since the RF high-frequency flip chip substrate has a higher integration level and a more optimized design, smaller size products can be achieved. This is crucial for modern electronic devices, especially for portable and micro devices, and can greatly improve the portability and applicability of the product.
In summary, RF high-frequency flip chip substrates have obvious advantages over traditional PCBs, including better high-frequency performance, lower signal loss, higher integration, and smaller size. These advantages enable it to meet the strict performance and size requirements of modern high-frequency electronic equipment, providing strong support and impetus for the development and innovation of the electronics industry.
These characteristics make RF high-frequency flip chip substrates the first choice in many fields, such as communications, radar, satellite communications, medical equipment, etc. With the continuous advancement and innovation of technology, it is believed that RF high-frequency flip chip substrates will play an increasingly important role in the future high-frequency electronics field.
FAQ
What is the difference between RF high-frequency flip chip substrate and traditional PCB?
RF high-frequency flip chip substrate is specially designed for the manufacturing of radio-frequency high-frequency electronic devices. Compared with traditional PCB, it is different in material selection, design layout and manufacturing process. RF high-frequency flip chip substrates usually use materials with better high-frequency properties, such as PTFE, etc., to provide better high-frequency performance and signal transmission characteristics. In addition, in terms of design layout, the RF high-frequency flip chip substrate will consider factors such as the transmission characteristics and signal loss of radio frequency signals, so it has better high-frequency performance compared with traditional PCBs.
How long is the manufacturing cycle for RF high-frequency flipping chip substrates?
The manufacturing lead time for RF high frequency flip chip substrates depends on the specific design and requirements and is usually between days and weeks. The manufacturing cycle is affected by many factors, including design complexity, material selection, process requirements, etc. Typically, a simple RF high-frequency flip chip substrate may be fabricated in a few days, while a complex design may take weeks to complete.
What are the main application areas of RF high-frequency flipping chip substrates?
RF high-frequency flip chip substrates are mainly used in various high-frequency electronic equipment and systems, including but not limited to wireless communications, radar, satellite communications, medical equipment and other fields. In these fields, RF high-frequency flip chip substrates can provide stable high-frequency performance and reliable signal transmission characteristics to meet various complex application requirements.
What factors need to be considered when designing RF high-frequency flip chip substrates?
When designing an RF high-frequency flip chip substrate, many factors need to be considered, including frequency range, signal transmission path, impedance matching, signal loss, radio frequency interference, heat dissipation, etc. Reasonable layout design and material selection are key to ensuring stable performance of RF high-frequency flip chip substrates. Design engineers need to comprehensively consider these factors and verify the feasibility and performance of the design through simulation and experiments.