What is a military PCB?
Military PCB Manufacturer. A Military PCB Manufacturer specializes in crafting printed circuit boards engineered to meet stringent standards for defense applications. These companies meticulously design and fabricate PCBs to withstand extreme conditions, ensuring reliability in combat zones and critical military operations. Employing cutting-edge technology and adhering to rigorous quality control measures, they produce PCBs tailored to the specific needs of military equipment, from communication systems to weaponry. Their expertise lies not only in manufacturing but also in understanding military requirements, guaranteeing that each component contributes to the effectiveness and resilience of the overall defense infrastructure.
In modern military equipment, printed circuit boards (PCBs) play a vital role. As the foundation for connecting and supporting electronic components, military PCBs play a key role in military communications, navigation, weapons systems, and a variety of military equipment.
First, a military PCB is a support board made of conductive material whose surface is covered with one or more layers of conductive traces. These wires enable the transmission of information and signals through connections between electronic components. PCBs provide more stable and reliable connections than traditional hand wiring methods and can accommodate more electronic components in a smaller space.
Military PCBs are more than simple circuit connection boards; they have many special design and performance requirements. In military environments, PCBs are often required to work under extreme conditions such as high and low temperatures, high pressure, and severe vibration. Therefore, the design of military PCBs must take these factors into account to ensure their stability and reliability under harsh conditions.
Additionally, military PCBs need to meet strict safety and military standards. This includes strict requirements for material selection, manufacturing process control, product testing and quality assurance. Military PCB manufacturers must strictly adhere to these standards to ensure that their products can operate stably on the battlefield and will not affect the conduct of military operations due to electronic failures.
Overall, military PCB is a vital component that plays an irreplaceable role in modern military equipment. Their precision design, high-quality materials and strict manufacturing standards provide critical support to the military industry, ensuring the performance and reliability of military equipment.
Military PCB design Reference Guide.
The design of military PCBs is a complex and critical process that requires strict compliance with various standards and guidelines to ensure reliability and stability in extreme environments. In the military industry, equipment often faces extreme conditions such as high temperatures, high pressures, vibrations, and other harsh environments, so PCBs must be designed to handle these challenges.
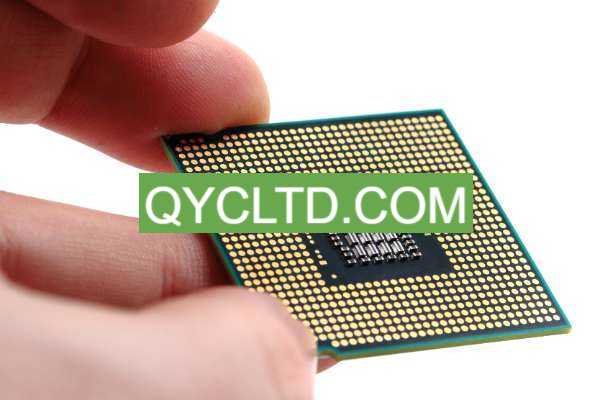
Military PCB Manufacturer
Taking into account extreme conditions
Military PCB designs must take into account the various extreme conditions that may be encountered. First, high-temperature environments may cause damage to PCB materials and components, so it is crucial to choose high-temperature-resistant materials and appropriate heat dissipation design. Secondly, the high-voltage environment may cause electrical breakdown and leakage, so measures need to be taken to ensure the insulation performance of the circuit. In addition, vibration and shock can cause components to loosen or break, so the way the PCB is constructed and fastened needs to be carefully designed and tested.
Comply with standards and guidelines
Military PCB designs must meet a stringent set of standards and guidelines to ensure their performance and reliability. These standards and guidelines cover various aspects, including material selection, wiring layout, welding processes, protective measures, etc. For example, IPC (International Printed Circuit Association) has developed a series of PCB design standards, including IPC-2221, IPC-2222, IPC-2223, etc., covering all aspects from material properties to structural design. In addition, the military industry has some specific standards and guidelines, such as MIL-PRF-31032 (Military Printed Circuit Board Technical Specification) and MIL-STD-810 (Military Environmental Engineering Considerations), etc., which are used to guide the design and implementation of military PCBs. test.
Taking various factors into consideration
When designing military PCBs, engineers need to consider a variety of factors, including performance, reliability, cost and manufacturing feasibility. They need to select the appropriate materials, processes and design solutions based on specific application needs to maximize PCB performance and reliability. In addition, they need to work closely with experts in other fields, such as materials scientists, mechanical engineers and test engineers, to solve various challenges and ensure the success of the final product.
The design of military PCBs is a complex and critical process that requires engineers to strictly follow various standards and guidelines to ensure their reliability and stability in extreme environments. By considering various factors and working closely with experts in other fields, we can design high-performance, high-reliability military PCBs that provide critical support for the development of military equipment.
What material is used in Military PCB?
Military PCB manufacturers use high-quality materials in military equipment to ensure their reliability and stability in extreme environments. Here are some commonly used materials:
FR-4 epoxy fiberglass
FR-4 is a common PCB board material made from fiberglass cloth impregnated with epoxy resin. It has excellent insulation properties and mechanical strength, and can withstand stress in high temperature and high pressure environments. The stability and durability of FR-4 material make it one of the top choices for military PCBs.
Polyimide (PI)
Polyimide is a high-performance engineering plastic with excellent high temperature resistance and chemical stability. It can maintain stable electrical performance under extreme temperatures and is suitable for high-temperature applications in military equipment, such as engine control systems and fire control systems.
Polyimide nitrile (PIA)
Similar to polyimide, polyimide nitrile is a high-performance polymer material with excellent heat resistance and chemical stability. It is often used in military PCBs for special applications such as high-frequency communication equipment and radar systems, where it is favored for its low dielectric loss and stable dielectric constant in high-frequency environments.
These materials not only have excellent high temperature resistance, corrosion resistance and mechanical strength, but also meet the strict requirements for stability and reliability of military equipment. By choosing the right materials, military PCB manufacturers can ensure the long-term stable operation of their products in harsh conditions, providing critical support for military operations.
What size are Military PCB?
Military PCBs come in a wide variety of sizes, depending on specific application needs and equipment requirements. They can be small, compact boards or large, complex boards, more on this below.
Small and compact board
In military equipment, there are many scenarios that require the use of small and compact PCB boards. These small PCBs are often used for assembly in missiles, aircraft, drones and other equipment. Since these devices have very tight space constraints, the size of the PCB must be as small as possible to fit into their compact body designs. At the same time, these PCBs must also feature a high degree of integration to minimize size and maximize performance. For example, PCBs for missile guidance systems may be very small, but they need to ensure highly accurate signal processing and data transmission under extreme conditions.
Large and complex boards
On the other hand, some military equipment, such as radar systems, communication equipment, etc., may require large and complex PCB boards. These devices typically handle large amounts of data and complex signal processing tasks, requiring more functionality and higher performance. To meet these requirements, large, complex PCBs may need to contain multiple layers of wiring and components, as well as numerous connections and interfaces. In addition, since these devices are often deployed in complex environments such as land, sea, or air, their PCBs must also have good anti-interference and shock resistance. For example, PCBs for radar systems can be very large to accommodate components such as complex signal processors, antenna systems, and power amplifiers, and to ensure reliable operation in a variety of environments.
In summary, military PCBs come in a wide range of sizes, from small, compact boards to large, complex boards. Regardless of their size, these PCBs play a vital role in ensuring the performance and reliability of military equipment. Therefore, military PCB manufacturers must be able to provide PCB boards in various sizes and specifications according to specific needs to meet the needs of different military applications.
The Manufacturer Process of Military PCB.
The manufacturing process of military PCBs is a complex and sophisticated process involving multiple critical steps that require strict quality control from design to final testing. The manufacturing process of military PCB will be introduced in detail below:
Design and layout
The first step in manufacturing a military PCB is design and layout. This phase involves determining the functionality, circuit layout, component arrangement, and hierarchy of the PCB. Design engineers use professional PCB design software to create prototypes of PCBs and ensure that they comply with military standards and specifications.
Forming
After the design and layout are complete, the prototype of the PCB is fabricated into the actual board. The process typically involves covering a substrate with conductive material and chemically treating or machining it to form the desired circuit structure.
Chemical processing and gold plating
After forming, the PCB needs to go through chemical processing and gold plating steps. Chemical processing cleans the PCB surface, removes unwanted impurities, and prepares it for gold plating. Gold plating is to enhance the conductivity and corrosion resistance of the PCB surface, usually using metals such as nickel and gold.
Punch holes
Next is the step of drilling holes. This step involves using sophisticated equipment to drill holes into the PCB in order to mount components and connect circuits. The location and size of the holes require precise control to ensure the accuracy and reliability of the final assembly.
Printing is the process of printing circuit patterns and markings on a PCB onto the surface. This step is usually performed using screen printing technology or inkjet technology to ensure clarity and precision of printing.
Assemble
Assembly is the step of mounting electronic components onto a PCB. This includes soldering components, connecting wiring, installing connectors, etc. The assembly process requires precision operations and a high level of skill to ensure that each component is connected correctly and meets design requirements.
Test
The last critical step is testing. During the testing phase, manufacturers will perform functional, electrical, and environmental testing on the PCB to ensure that it performs as expected and operates stably under a variety of conditions. The testing process requires the use of professional testing equipment and technology, and requires strict recording and analysis.
The manufacturing process of military PCBs is a complex and sophisticated process involving multiple critical steps and strict quality control. Through careful design, high-quality materials and precise manufacturing, military PCB manufacturers are able to provide reliable electronic support for military equipment to ensure stable operation in extreme environments.
The Application area of Military PCB.
Military PCBs play an integral role in modern military equipment, and their high performance and reliability provide critical support for various military operations. Here are some areas where military PCBs are widely used:
Communication Systems
Military communications systems are critical to the success of military operations. Military PCBs are used in a wide variety of communications equipment, including satellite communications, radio communications, and mobile communications systems. These PCBs need to have highly stable signal transmission performance and anti-interference capabilities to ensure communication stability in complex electromagnetic environments.
Radar system
Radar systems are important tools in military equipment for reconnaissance, surveillance and target tracking. Military PCBs play a critical role in radar systems, supporting connections between radar transmitters, receivers, and signal processing units. These PCBs require a high degree of electrical performance and signal processing capabilities to ensure accurate target recognition and tracking.
Navigation equipment
Military navigation equipment is used to determine and track the position, speed and direction of military units. Military PCBs are used to support critical components such as GPS receivers, inertial navigation systems, and map displays. These PCBs need to have a high degree of accuracy and stability to ensure accurate navigation and positioning capabilities, especially in complex terrain and harsh weather conditions.
Missile system
Missile systems are one of the important weapons in modern warfare and are used to strike enemy targets at long range. Military PCBs play a vital role in missile systems for control, guidance and target identification. These PCBs need to be extremely reliable and precise to ensure that the missile accurately hits its target and performs its intended mission.
In these areas, the high performance and reliability of military PCBs provide critical support for military operations, providing advantages and strategic advantages to the military. Therefore, the role of military PCB manufacturers is crucial as they provide a solid foundation for the successful operation and execution of military equipment by providing high-quality PCB solutions.
What are the advantages of Military PCB?
As one of the key components of modern military equipment, military PCBs (Printed Circuit Boards) have many advantages, making them an indispensable component. Compared to traditional connection methods, military PCBs have significant advantages in density, electrical performance, failure rates, and maintenance.
Higher density
Military PCBs have higher component density, which means more electronic components can be accommodated in a limited space. In modern military equipment, space is often a precious resource, so the high-density design of PCBs allows for a more compact equipment layout, thereby improving equipment performance and efficiency.
Better electrical performance
Because the PCB’s wires are manufactured directly on the board through printing technology, military PCBs have lower electrical noise and more stable signal transmission characteristics compared to manual wiring or other traditional connection methods. This design can reduce signal interference and errors and improve equipment performance and reliability.
Lower failure rate
Military PCBs undergo rigorous design and manufacturing processes, using high-quality materials and advanced technology. This allows them to have a lower failure rate and be able to operate stably for a long time in extreme environments and harsh conditions. In military operations, the reliability of equipment is crucial, and the low failure rate of PCBs can greatly improve the reliability and durability of equipment.
Easier maintenance
Military PCBs are designed to be easier to maintain and repair than traditional hand-routed or soldered connections. Because all connections are centralized on the PCB and use standardized connection interfaces, diagnosing problems and replacing damaged parts is easier and faster. This not only reduces maintenance costs, but also reduces repair time, allowing the equipment to return to combat status more quickly.
To sum up, military PCB, as a key component of modern military equipment, has many advantages such as high density, good electrical performance, low failure rate and convenient maintenance. These advantages make them play an irreplaceable role in various military applications, providing key technical support and strategic advantages to the military.
FAQ
How are military PCBs different from regular PCBs?
Military PCBs have higher requirements and standards than regular PCBs. First, military PCBs need to operate stably in extreme environments, so their design and material selection are more stringent. Second, military PCBs need to meet military-specific standards and certification requirements to ensure their reliability and safety. Finally, the manufacturing process for military PCBs can be more complex and require more stringent quality control.
How long is the production cycle for military PCBs?
The production cycle for military PCBs usually takes weeks or even months, depending on their complexity and volume. During the production process, multiple stages such as design verification, sample production, and mass production are required to ensure the quality and performance of the final product.
How to ensure the reliability of military PCBs?
The reliability of military PCBs is ensured through rigorous design, manufacturing and testing. During the design phase, performance requirements in extreme environments need to be considered and appropriate materials and processes used. During the manufacturing process, each step needs to be strictly controlled to ensure that the product meets specification requirements. Finally, during the testing phase, various tests need to be conducted, including environmental testing, functional testing, reliability testing, etc., to verify the performance and reliability of the product.
How is military PCB maintenance and repair performed?
Maintenance and repair of military PCBs often requires specialized skills and equipment. Generally, if a PCB is found to be faulty or damaged, maintenance can be performed by inspecting, replacing, or repairing the damaged parts. During the repair process, strict processes and standards need to be followed to ensure that the repaired PCB meets specification requirements and maintains its original performance and reliability.