Microtrace RF PCB Manufacturer, Microtrace RF PCB Manufacturer specializes in crafting high-performance printed circuit boards (PCBs) tailored for radio frequency (RF) applications. With a dedication to precision engineering and cutting-edge technology, Microtrace excels in producing PCBs optimized for the demands of modern wireless communication systems. Utilizing advanced materials and manufacturing processes, they ensure superior signal integrity, minimal interference, and maximum efficiency. Whether for telecommunications, aerospace, or IoT devices, Microtrace’s RF PCBs consistently deliver exceptional performance, reliability, and innovation, making them a trusted partner for companies pushing the boundaries of wireless technology.
In today’s modern wireless communications field, RF (radio frequency) PCB plays a vital role. They not only support and connect radio frequency electronic components, but also directly affect the performance and reliability of wireless communication equipment. This article will delve into the manufacturing process of RF PCB and focus on how Microtrace, as a leading RF PCB manufacturer in the industry, provides customers with high-quality solutions through its professional technology and excellent service.
What is RF PCB?
RF PCB, Radio Frequency Printed Circuit Board (Radio Frequency Printed Circuit Board), plays a vital role in the field of modern communications and radio. Compared with traditional printed circuit boards, RF PCBs are not just simple boards used to support and connect electronic components, they are highly complex circuit boards specifically designed to handle radio frequency signals.
First of all, RF PCB has special structure and materials to meet the requirements of high-frequency signal transmission. Compared with ordinary circuit boards, RF PCBs usually use special substrate materials with low loss dielectric constant and low dielectric loss, such as PTFE (polytetrafluoroethylene) or FR-4 (glass fiber reinforced epoxy resin). These materials have excellent high-frequency characteristics and can provide stable signal transmission and low signal attenuation at high frequencies, thereby ensuring the performance and reliability of RF PCBs in wireless communication systems.
Secondly, the structure of the RF PCB is also carefully designed to minimize signal loss and interference. To achieve this, RF PCBs often use special wiring layouts and stack-up structures to ensure that the signal transmission path is as short and consistent as possible. Additionally, RF PCBs may include special ground planes and shielding layers to reduce crosstalk between signals and the effects of external interference.
Microtrace, as a professional RF PCB manufacturer, is committed to providing customers with high-performance solutions. We have advanced production equipment and rich industry experience, and are able to customize the design and manufacturing of RF PCB according to the specific needs of customers. Whether in communications, radar, radio or other wireless applications, Microtrace is able to provide customers with high-quality RF PCB products and ensure their stability and reliability at high frequencies.
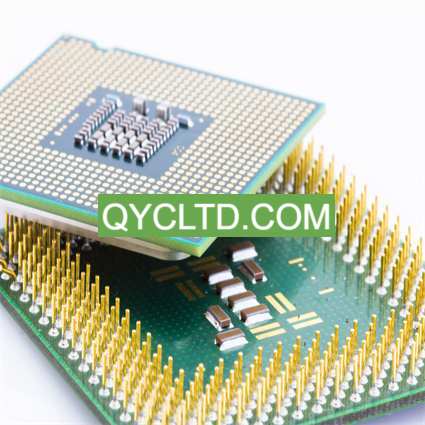
Microtrace RF PCB Manufacturer
In short, RF PCBs play an irreplaceable role in the field of modern communications. They are key components that support the normal operation of wireless communication systems. Through special structures and materials, as well as carefully designed wiring layouts, RF PCBs are able to provide stable performance and reliable signal transmission at high frequencies to meet the needs of various wireless applications. As a leader in the RF PCB manufacturing industry, Microtrace will continue to be committed to providing customers with high-performance RF PCB solutions and promoting the development and progress of wireless communication technology.
How to design RF PCB?
The design of RF PCB is a complex and critical process that requires consideration of multiple factors to ensure its stability and performance in high-frequency environments. As a leading RF PCB manufacturer, Microtrace has an experienced engineering team and is able to provide customers with customized design services to meet their specific application needs.
First, an important factor to consider when designing an RF PCB is the operating frequency. Different frequencies require different board layouts and line width spacing to ensure the stability and reliability of signal transmission. Microtrace’s engineering team will conduct precise designs based on customers’ frequency requirements to maximize the performance of RF PCBs.
Secondly, transmission line characteristics are also one of the factors that need to be considered during the design process. The impedance, length and matching of transmission lines are critical to the transmission of RF signals and need to be precisely controlled to avoid signal distortion and attenuation. Microtrace engineers will use advanced simulation tools and technologies to accurately simulate and analyze transmission lines to ensure that they meet design requirements.
In addition, noise and interference issues also need to be considered during the design process. In high-frequency environments, noise and interference may have an adverse impact on signal quality, so corresponding measures need to be taken for suppression and filtering. Microtrace’s engineering team will select appropriate filters and shielding technologies based on the customer’s application scenario to minimize the impact of noise and interference.
Finally, Microtrace’s engineering team will also provide customized design solutions based on customers’ specific needs. Whether it is layout design, material selection or inter-layer connections, we work closely with our customers to ensure that the design fully meets their application needs and achieves the best balance between performance and cost.
In short, the design of RF PCB is a complex process that takes into account multiple factors and requires the engineering team to have rich experience and expertise. As an expert in RF PCB manufacturing, Microtrace is able to provide customers with highly customized design services to ensure their projects achieve optimal performance and reliability.
What is the manufacturing process of RF PCB?
The manufacturing process of RF PCB is a complex process involving multiple critical steps. At Microtrace, we pay attention to every detail to ensure every RF PCB meets the highest standards of performance and reliability.
First, the process of manufacturing RF PCB begins with the preparation of raw materials. We choose high-quality base materials, such as PTFE (polytetrafluoroethylene) or FR-4, etc. These materials have good dielectric properties and high-frequency transmission characteristics, and can meet the needs of high-frequency signal processing. At this stage, we strictly control the quality of the raw materials to ensure they meet our standards and specifications.
Next comes the plate processing stage. At this stage, we use advanced processing equipment and technology to cut the raw materials into sheets of the required size and shape. Our engineering team precisely processes panels to customer design requirements to ensure the quality and performance of the final product.
This is followed by the printing stage. At this stage, we use screen printing technology to print the circuit pattern and component layout onto the board surface. Our printing process is precise and efficient, ensuring clarity and accuracy of circuit patterns to maximize RF PCB performance.
Then comes the shaping stage. At this stage, we laminate the boards together through heat pressing or chemical methods to form a multi-layer PCB structure. This process is very critical because it affects the interlayer connection quality and overall stability of the PCB. We use advanced molding technology to ensure each RF PCB has a solid structure and good inter-layer connections.
Finally comes the assembly stage. At this stage, we solder the electronic components to the PCB and conduct final testing and quality inspection. Our engineering team is rigorously trained and certified to ensure the accuracy and consistency of the assembly process, ensuring that each RF PCB meets customer requirements and expectations.
Overall, Microtrace uses advanced manufacturing technology and strict quality control processes to ensure each RF PCB has excellent performance and reliability. We are committed to providing customers with the best solutions to meet their specific application needs and continuously improving production efficiency and product quality.
How much does it cost to manufacture an RF PCB?
The manufacturing cost of RF PCB is a crucial consideration in the entire production process. Microtrace understands that manufacturing costs are affected by many factors, including variables such as panel type, number of layers, size and quantity. Therefore, we are committed to providing our customers with competitive prices and customized quotations based on their specific needs.
First of all, board type is an important factor in determining RF PCB manufacturing cost. Different types of boards have different costs. For example, the commonly used FR-4 (fiberglass reinforced epoxy resin) is relatively economical, while special materials such as PTFE (polytetrafluoroethylene) are more expensive. Microtrace will select the most appropriate plate type based on the customer’s application needs and budget requirements to ensure the best balance between performance and cost.
Secondly, the number of layers of RF PCB will also affect its manufacturing cost. Typically, the higher the number of layers, the higher the manufacturing cost because more processing steps and complex processes are required. Microtrace will reasonably evaluate the number of layers based on the customer’s design requirements and performance needs, and provide corresponding quotation plans.
In addition, the size and quantity of RF PCBs are also important factors affecting manufacturing costs. Larger sheet sizes require more material and processing costs, while mass production can reduce unit costs. Microtrace will flexibly adjust prices and provide corresponding discounts based on customer order volume and plate size.
To sum up, the manufacturing cost of RF PCB is affected by a variety of factors. Microtrace will provide customized quotation plans based on customers’ specific needs and budget requirements to ensure that customers can get the most competitive price and quality. and achieve the best balance in performance.
What materials are RRF PCB made of?
RF PCB (radio frequency printed circuit board) is a key component used to process radio frequency signals, and its material selection is crucial to ensure the stability and reliability of high-frequency signal transmission. Usually, RF PCB uses special materials, the most common of which include polytetrafluoroethylene (PTFE) and FR-4.
First of all, polytetrafluoroethylene (PTFE) is a high-performance polymer material characterized by excellent insulation properties and high temperature resistance. Because PTFE has the characteristics of low dielectric constant and low loss tangent, it has low signal loss at high frequencies and is suitable for application scenarios in which high-frequency signals are processed. In addition, PTFE material also has good chemical stability and corrosion resistance, allowing it to maintain stable performance in harsh environments.
Secondly, FR-4 is a common glass fiber reinforced epoxy resin material commonly used to manufacture standard PCBs. Although the dielectric properties of FR-4 materials are not as superior as PTFE, they are more economical and perform well in general low- and mid-frequency applications. For some less demanding RF applications, the use of FR-4 materials can also meet the needs.
As a professional RF PCB manufacturer, Microtrace will work closely with customers to select the most suitable materials based on their application needs and performance requirements. During the material selection process, we not only consider the electrical properties of the material, but also comprehensively consider factors such as its physical properties, cost, and processability. By working closely with our customers, we ensure that the materials selected best meet their application needs and provide exceptional performance and reliability.
In short, the material selection of RF PCB is crucial, and different materials have different characteristics and application ranges. Microtrace will carefully select materials based on customers’ specific needs and application scenarios, and provide high-quality RF PCB solutions to meet customer needs and expectations.
Who makes RF PCBs?
In the field of RF PCB manufacturing, supplier selection is crucial because they directly affect the quality and performance of the product. Microtrace, as a professional RF PCB manufacturer, is proud to announce that we are not only your supplier, but also your partner.
At Microtrace, we not only provide high-quality RF PCB products, but also strive to establish long-term and stable cooperative relationships. We have advanced production equipment and rich industry experience to meet the various needs of our customers.
First, we focus on quality. We strictly implement the ISO quality management system and strictly control every aspect from raw material procurement to production and manufacturing to ensure that every RF PCB has excellent performance and reliability. Our quality assurance team conducts rigorous inspections on each batch of products to ensure compliance with customer requirements and standards.
Secondly, we focus on innovation. As a leader in the field of RF PCB, we continue to invest in R&D and innovation to lead the development direction of the industry. Our engineering team has the experience and expertise to provide customers with customized solutions to meet their specific application needs.
In addition, we focus on service. Our sales team and customer service team are always customer-centric, respond promptly to customer needs and problems, and provide professional technical support and solutions. Our goal is to establish long-term and stable cooperative relationships with customers and achieve a win-win situation together.
Finally, we focus on responsibility. As a socially responsible enterprise, we are committed to promoting sustainable development and contributing to society and the environment. We take a series of measures to reduce energy consumption, reduce emissions, improve resource utilization, and strive to become a responsible corporate citizen.
In short, Microtrace is not only your RF PCB supplier, but also your partner. We will continue to uphold the core values of quality first, innovation first, service first, and responsibility, and work with you to create a better future.
Five Characteristics of Great Customer Service
Excellent customer service is crucial in any industry, especially in electronics manufacturing such as RF PCB manufacturing. Microtrace, as a leading RF PCB manufacturer, is committed to providing customers with an excellent service experience. Here are the top five features of great customer service we provide:
Prompt response: At Microtrace, we understand that our customers’ time is valuable. Therefore, we promise to respond quickly as soon as we receive customer inquiries or needs. Whether it’s email, phone or online chat, our customer service team responds quickly and provides customers with the support and information they need.
Professional technical support: Our team is composed of experienced engineers and technical experts, able to provide customers with professional technical support. Whether it is about RF PCB design, material selection or technical issues during the manufacturing process, we are able to provide professional advice and solutions to ensure that our customers’ needs are met.
Customized Solutions: Every customer’s needs are unique, so we are committed to providing customized solutions. Whether it is RF PCB design for a specific application or customizing the production process according to customer requirements, we are able to respond flexibly and provide customers with the most suitable solution.
Quality Assurance: At Microtrace, quality is always our top priority. We strictly follow the ISO quality management system and conduct strict quality control throughout the entire production process. From raw material procurement to final product delivery, we always maintain high standards for product quality and ensure that each RF PCB has excellent performance and reliability.
After-sales service: Our services not only stop at product delivery, we also provide comprehensive after-sales service support. Whether there are problems during product use or maintenance and upgrades are required, we will fully support our customers and ensure that they receive ongoing support and services.
In short, Microtrace is committed to providing customers with high-quality RF PCB manufacturing services and creating maximum value and satisfaction for customers through timely response, professional technical support, customized solutions, quality assurance and comprehensive after-sales service.
FAQs
How long is the design cycle of RF PCB?
The design cycle of RF PCB depends on the complexity of the project and the customer’s needs. Typically, the design cycle may only take a few weeks for simple projects, while it may take several months for complex projects. During the design process, communication and feedback from the customer will also impact the design cycle, so it is recommended to contact the manufacturer early to determine the project timeline.
What is the maximum operating frequency of RF PCB?
The maximum operating frequency of an RF PCB depends on the quality of design and manufacturing, as well as the materials and processes selected. Generally, RF PCB can support operating frequencies of several GHz or even higher. However, in order to ensure stability and reliability, it is usually recommended to clarify the operating frequency requirements during the design stage and select appropriate materials and manufacturing processes.
How do I choose the RF PCB manufacturer that’s right for me?
Choosing the right RF PCB manufacturer is one of the key steps to ensure a successful project. First, you need to examine the manufacturer’s experience and expertise, especially in the RF PCB field. Secondly, you should pay attention to the manufacturer’s production capacity and quality control system to ensure that it can meet your needs and provide high-quality products. Finally, communicating with manufacturers and seeking customer feedback is also an important basis for evaluating whether a manufacturer is a good fit.
How to calculate the cost of RF PCB?
The cost of RF PCB is affected by many factors, including board type, number of layers, size, process complexity and order quantity. Typically, the manufacturing cost of RF PCB increases with the number of layers and process complexity, while the order quantity may affect the unit price. Therefore, it is recommended that when quoting an RF PCB project, detailed design requirements and order quantities should be provided as much as possible so that the manufacturer can provide an accurate quotation.