What are Microtrace RF Substrates?
Microtrace RF Substrates Manufacturer.Microtrace RF Substrates Manufacturer specializes in crafting cutting-edge substrates tailored for radio frequency applications. With meticulous precision and advanced technology, they engineer substrates that optimize signal transmission, minimize interference, and enhance performance across a spectrum of frequencies. Their dedication to innovation and quality ensures that each substrate meets stringent industry standards, catering to diverse needs in telecommunications, aerospace, and beyond. From prototype to production, Microtrace RF Substrates Manufacturer is the trusted partner for delivering reliable, high-performance solutions that drive advancements in wireless communication technology.
Microtrace RF substrate is a substrate specially designed for use in high frequency electronic equipment. In today’s increasingly developing fields of science and technology, high-frequency electronic technology plays an increasingly important role in communications, radar, radio, etc. Microtrace RF substrate is the shining star in this field. This substrate is not just an ordinary circuit board, it is a masterpiece of precision engineering, carefully designed and manufactured to meet the special needs of high-frequency electronic equipment.
Microtrace RF substrates use state-of-the-art materials and manufacturing processes to ensure excellent dielectric properties and stability. This substrate typically uses high-performance dielectric materials such as PTFE (Polytetrafluoroethylene) and RO4003C (Glass Fiber Reinforced PTFE). These materials have low loss, low dielectric constant and excellent thermal stability, allowing Microtrace RF substrates to Provides excellent signal transmission and anti-interference capabilities in high-frequency environments. In addition, the manufacturing process uses advanced micro-machining technology to ensure the uniformity and stability of the plates, further improving the performance and reliability of the entire system.
In the field of high-frequency electronic technology, stable signal transmission and anti-interference ability are crucial. Microtrace RF substrates are able to meet these requirements, making them the first choice for many high-frequency electronic devices. Whether it is communication equipment, radar systems, satellite communications, or medical equipment, Microtrace RF substrates play a key role, providing a reliable foundation for high-frequency signal transmission and processing of equipment.
In general, Microtrace RF substrate is not only a key component in the field of high-frequency electronic technology, but also an excellent solution that provides reliable signal transmission and processing capabilities for various application scenarios. With the continuous advancement of technology, Microtrace RF substrates will continue to play an important role, leading the new trend of high-frequency electronic technology.
Microtrace RF Substrates design Reference Guide.
As a key component in the field of high-frequency electronic technology, the design of Microtrace RF substrate is crucial. Designers need to consider many factors to ensure that the final product achieves optimal levels of performance, stability, and reliability. The following is a reference guide for Microtrace RF substrate design:
Choose the right substrate material
Selecting the appropriate substrate material is critical to Microtrace RF substrate design. Typically, PTFE and its composites are preferred because of their excellent dielectric properties, low losses, and stable thermal properties. When selecting materials, temperature and humidity changes in the working environment also need to be taken into consideration to ensure that the substrate can maintain stable performance under various conditions.
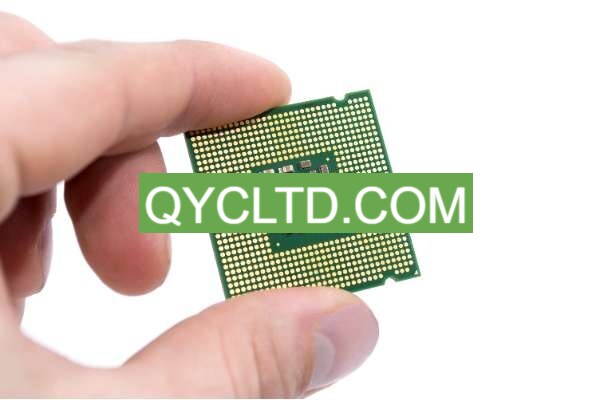
Microtrace RF Substrates Manufacturer
Determine the layer structure
The layer structure of Microtrace RF substrate directly affects its performance and layout. Designers need to determine the number and layout of board layers based on system requirements and signal transmission characteristics. Typically, double- or multi-layer structures provide better signal isolation and anti-interference capabilities, but also increase manufacturing complexity and cost.
Consider ground and power plane design
In Microtrace RF substrate design, the design of ground and power planes is crucial. Ground and power planes should be laid out to minimize signal return flow and interference. At the same time, the ground wire and power plane can also provide good electromagnetic shielding effects to protect the system from external interference.
Optimized routing and impedance matching
Layout and impedance matching are aspects that require special attention in Microtrace RF substrate design. Reasonable wiring and impedance matching can minimize signal loss and reflection and improve the transmission efficiency and stability of the system. Designers need to use simulation tools and real-world testing to make precise adjustments to routing and impedance to meet system requirements.
Consider thermal management and mechanical construction
Finally, designers also need to consider the thermal management and mechanical structure of the Microtrace RF substrate. Proper thermal management design can ensure that the system can operate normally in high-temperature environments, while a solid mechanical structure can protect the substrate from external shock and vibration. Designers need to consider these factors to ensure the stability and reliability of the final product.
By following the above guidelines, designers can better design Microtrace RF substrates to ensure that the final product reaches the best level in terms of performance, stability and reliability to meet the needs of various high-frequency electronic systems.
What material is used in Microtrace RF Substrates?
Microtrace RF substrates utilize a range of high performance materials to ensure excellent performance and reliability in high frequency environments. Among the most commonly used materials are polytetrafluoroethylene (PTFE) and its fiberglass-reinforced version RO4003C.
First of all, polytetrafluoroethylene (PTFE) is one of the main materials of Microtrace RF substrate. PTFE is known for its excellent dielectric properties and chemical stability. It has low loss and low dielectric constant, making it ideal for high-frequency electronic equipment. In the Microtrace RF substrate, PTFE is used as the basic material of the substrate, providing good electrical performance and stability for the entire system.
Secondly, glass fiber reinforced polytetrafluoroethylene (RO4003C) is also one of the commonly used materials in Microtrace RF substrates. This material combines polytetrafluoroethylene with glass fiber, combining the excellent properties of PTFE with the reinforcing properties of glass fiber. RO4003C has higher mechanical strength and thermal stability, making it suitable for applications that require higher substrate strength and stability.
In addition to PTFE and RO4003C, Microtrace RF substrates may also use other materials, such as ceramic substrates, polyimide (PI), etc. These materials are selected based on specific application needs and performance requirements to ensure that the substrate can provide stable and reliable performance in different environments.
To sum up, Microtrace RF substrate uses a series of high-performance materials, such as polytetrafluoroethylene (PTFE) and RO4003C, to meet the requirements of high-frequency electronic equipment for excellent electrical performance, stability and reliability. The selection and application of these materials enable Microtrace RF substrates to perform excellently in various high-frequency application scenarios, providing users with excellent experience and reliability.
What size are Microtrace RF Substrates?
Microtrace RF substrates utilize a range of high performance materials to ensure excellent performance and reliability in high frequency environments. Among the most commonly used materials are polytetrafluoroethylene (PTFE) and its fiberglass-reinforced version RO4003C.
First of all, polytetrafluoroethylene (PTFE) is one of the main materials of Microtrace RF substrate. PTFE is known for its excellent dielectric properties and chemical stability. It has low loss and low dielectric constant, making it ideal for high-frequency electronic equipment. In the Microtrace RF substrate, PTFE is used as the basic material of the substrate, providing good electrical performance and stability for the entire system.
Secondly, glass fiber reinforced polytetrafluoroethylene (RO4003C) is also one of the commonly used materials in Microtrace RF substrates. This material combines polytetrafluoroethylene with glass fiber, combining the excellent properties of PTFE with the reinforcing properties of glass fiber. RO4003C has higher mechanical strength and thermal stability, making it suitable for applications that require higher substrate strength and stability.
In addition to PTFE and RO4003C, Microtrace RF substrates may also use other materials, such as ceramic substrates, polyimide (PI), etc. These materials are selected based on specific application needs and performance requirements to ensure that the substrate can provide stable and reliable performance in different environments.
To sum up, Microtrace RF substrate uses a series of high-performance materials, such as polytetrafluoroethylene (PTFE) and RO4003C, to meet the requirements of high-frequency electronic equipment for excellent electrical performance, stability and reliability. The selection and application of these materials enable Microtrace RF substrates to perform excellently in various high-frequency application scenarios, providing users with excellent experience and reliability.
The Manufacturer Process of Microtrace RF Substrates.
The manufacturing process of Microtrace RF substrates is precision designed and strictly controlled to ensure that the final product meets the stringent requirements of high frequency electronic equipment. The following are the key steps in the manufacturing process of Microtrace RF substrates:
Raw material selection and preparation
The manufacturing of Microtrace RF substrates begins with the selection and preparation of raw materials. High-performance dielectric materials such as premium PTFE and glass fiber reinforced PTFE are carefully selected to ensure they meet design requirements. After rigorous testing and screening, the materials are pre-treated to ensure that the surface is clean and flat, ready for subsequent processing steps.
Sheet pressing and processing
The pre-treated material is fed into the plate press, and the material is pressed into the required plate thickness and shape through a high-temperature and high-pressure process. Subsequently, the plate is sent to the CNC machining center for precise cutting, hole processing and shape processing to ensure that the size of each plate is accurate and the position of the holes is accurate.
Metallization
After the sheet is processed, it is metallized to enhance its electrical conductivity. Through processes such as chemical copper plating or vacuum copper plating, the copper foil layer is covered on the surface of the board to form a conductive layer. The thickness and uniformity of the conductive layer are critical to the performance of Microtrace RF substrates, so this step needs to be tightly controlled.
Graphical processing
After the metallization treatment is completed, the designed circuit is patterned onto the surface of the board through processes such as photolithography and etching. This step requires precise equipment and process control to ensure the clarity and accuracy of circuit graphics.
Surface treatment and packaging
Finally, the patterned board is fed into the surface treatment and encapsulation process. Surface treatment includes coating protective layer, pad treatment and other steps to improve the corrosion resistance and weldability of the board. Packaging includes steps such as soldering components, printing logos, etc., and finally forming the finished Microtrace RF substrate.
The manufacturing process of Microtrace RF substrates is a highly precise and complex process that requires strict control of parameters and conditions at each step. Only through exquisite technology and strict quality control can we produce high-quality Microtrace RF substrates that meet the requirements of high-frequency electronic equipment.
The Application area of Microtrace RF Substrates.
The application fields of Microtrace RF substrates widely involve communication equipment, radar systems, satellite communications, medical equipment and other fields. There is an increasing demand for high-frequency electronics in these areas, and Microtrace RF substrates are ideally suited to meet these needs.
In the field of communication equipment, Microtrace RF substrates play a key role. They are widely used in communication equipment such as mobile phones, base stations, and antenna systems to ensure stable transmission and efficient processing of signals. Whether in cities or remote areas, Microtrace RF substrates can provide a reliable foundation for communication equipment to ensure unimpeded communication.
Radar systems are also one of the important application areas of Microtrace RF substrates. Radar systems require precise control and rapid processing of high-frequency signals, and Microtrace RF substrates are ideally suited to meet this need. From military radar to weather radar, Microtrace RF substrates can provide a stable and reliable signal transmission and processing platform for radar systems to ensure efficient operation of the system.
In the field of satellite communications, Microtrace RF substrates also play an important role. Satellite communication systems require high-frequency electronic equipment that can operate stably in extreme environments, and Microtrace RF substrates are ideal for meeting this need. They can ensure stable and reliable signal transmission of satellite communication systems and ensure smooth communication between the ground and satellites.
In addition, Microtrace RF substrates are also widely used in the field of medical equipment. Medical equipment has extremely high requirements for precise control and stable transmission of high-frequency signals, and Microtrace RF substrates are the ideal choice to meet this demand. From medical imaging equipment to wireless monitoring systems, Microtrace RF substrates can provide reliable signal processing and transmission platforms for medical equipment, ensuring the accuracy and efficiency of medical diagnosis and treatment.
In short, Microtrace RF substrates play a key role in communication equipment, radar systems, satellite communications, medical equipment and other fields, providing a reliable foundation for high-frequency signal transmission and processing. With the continuous advancement of technology and the continuous expansion of application fields, it is believed that Microtrace RF substrates will continue to play an important role in promoting the development and innovation of high-frequency electronic technology.
What are the advantages of Microtrace RF Substrates?
As a leading choice in the field of high-frequency electronic technology, Microtrace RF substrate is widely praised in the industry for its outstanding performance advantages. These advantages include low loss, high frequency bandwidth and excellent thermal stability, providing users with an excellent experience.
First, Microtrace RF substrate has low loss characteristics. During high-frequency signal transmission, loss will cause signal attenuation and distortion, affecting system performance and stability. Microtrace RF substrate uses high-quality dielectric materials and precision processing technology, which effectively reduces energy loss during signal transmission and ensures high-quality signal transmission.
Secondly, Microtrace RF substrate has a broad high-frequency bandwidth. High-frequency bandwidth is one of the important indicators to measure the performance of the substrate, which determines the frequency range that the substrate can transmit. Microtrace RF substrate achieves a wider frequency response range by optimizing material selection and manufacturing process, meeting the requirements for high-frequency bandwidth in different application scenarios.
In addition, Microtrace RF substrates have excellent thermal stability. In high-temperature environments, some substrates may experience performance degradation or failure, affecting the long-term stable operation of the equipment. The Microtrace RF substrate uses high-quality materials and uses precise processing technology to ensure the stability and reliability of the substrate in high-temperature environments and ensure the continuous and efficient operation of the equipment.
Finally, Microtrace RF substrate’s investment in precision processing and high-quality materials ensures stable transmission of high-frequency signals. Whether in communication equipment, radar systems or satellite communications, Microtrace RF substrates can provide a reliable signal transmission foundation and provide users with an excellent experience.
To sum up, Microtrace RF substrate occupies an important position in the field of high-frequency electronic technology due to its many advantages such as low loss, high-frequency bandwidth, and excellent thermal stability. Through continuous technological innovation and quality assurance, Microtrace RF substrates will continue to provide users with high-performance, high-reliability solutions and promote the development and progress of the industry.
FAQ
What is Microtrace RF Substrate?
Microtrace RF substrate is a substrate specially designed for high-frequency electronic equipment. It has excellent dielectric properties and stability and is used to transmit and process high-frequency signals.
What materials are used in Microtrace RF substrates?
Microtrace RF substrates use high-performance dielectric materials such as PTFE and RO4003C, which have low loss, low dielectric constant and excellent thermal stability.
What is the manufacturing process of Microtrace RF substrate?
The manufacturing process of Microtrace RF substrate uses advanced micro-machining technology to ensure the uniformity and stability of the board. This includes rigorous material selection, precision printing and etching processes, and more.
What fields are Microtrace RF substrates suitable for?
Microtrace RF substrates are widely used in communication equipment, radar systems, satellite communications, medical equipment and other fields, providing a reliable foundation for high-frequency signal transmission and processing of equipment.
What are the advantages of Microtrace RF substrates?
Microtrace RF substrate has the advantages of low loss, high frequency bandwidth, and excellent thermal stability. Its precision machining and high-quality materials ensure stable transmission of high-frequency signals, improving system performance and reliability.