Aln Substrate Manufacturer.An AlN Substrate Manufacturer specializes in producing high-quality Aluminum Nitride (재질 보기 AlN) substrates, known for their excellent thermal conductivity and electrical insulation properties. These substrates are essential in high-power electronics, LED applications, and advanced semiconductor devices, 최적의 성능과 신뢰성 보장. The manufacturer utilizes state-of-the-art technology and stringent quality control measures to deliver substrates that meet the demanding specifications of modern electronic applications.
Aluminum nitride (재질 보기 AlN) substrates are widely used in various high-performance applications due to their excellent thermal conductivity, electrical insulation properties, and mechanical strength. These substrates are essential in the semiconductor industry, high-power electronics, and microwave communications, among other fields. The unique combination of properties offered by AlN makes it a preferred material for applications requiring efficient heat dissipation and reliable electrical performance.
What is an AlN Substrate?
An AlN substrate is a type of ceramic material made from aluminum nitride. It is known for its high thermal conductivity, which is significantly higher than that of traditional ceramic materials such as alumina (알2O3). AlN substrates also offer excellent electrical insulation, making them ideal for applications where thermal management and electrical isolation are critical.
AlN substrates are typically used in the production of semiconductor devices, LEDs, and other high-power electronic components. Their ability to efficiently dissipate heat helps in maintaining the performance and longevity of these devices. 또한, AlN substrates are used in microwave and RF applications due to their low dielectric loss and stable dielectric properties over a wide frequency range.
AlN Substrate Design Reference Guide
Designing with AlN substrates involves several critical considerations to ensure optimal performance and reliability. The following sections outline the key aspects of AlN substrate design.
The choice of materials in conjunction with AlN substrates is crucial for achieving the desired performance. Key materials include:
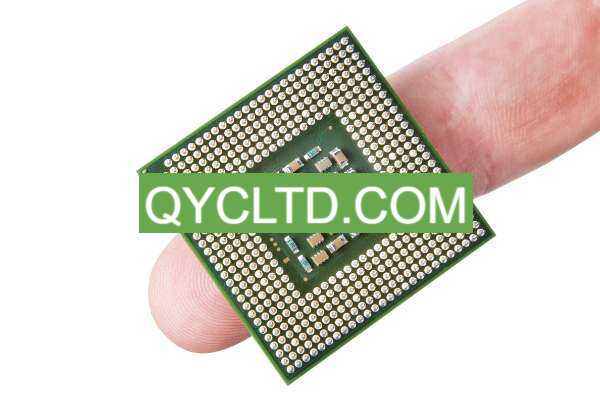
Aln Substrate Manufacturer
High-Purity Aluminum Nitride: High-purity AlN is used to ensure excellent thermal conductivity and electrical insulation properties.
Metallization Layers: Conductive layers such as gold, silver, or copper are used for creating electrical pathways on the AlN substrate. These layers must be carefully selected and applied to maintain adhesion and conductivity.
Dielectric Layers: Dielectric materials with low loss and stable properties are used for insulation and signal integrity in 고주파 응용 프로그램.
Several key considerations must be addressed during the design phase:
Thermal Management: Effective thermal management is crucial for high-power applications. The design must incorporate thermal vias, heat spreaders, or other techniques to efficiently dissipate heat.
Electrical Performance: The design must ensure high electrical performance with minimal loss and stable characteristics over a wide frequency range.
Mechanical Stability: The substrate must provide robust mechanical support to withstand thermal cycling and mechanical stresses during operation.
Reliability: Long-term reliability is ensured through the use of high-quality materials and precise manufacturing processes, preventing issues such as delamination and cracking.
What Materials are Used in AlN Substrates?
Materials used in AlN substrates are selected for their complementary properties to enhance the overall performance of the substrate:
High-Purity Aluminum Nitride: Provides the foundation for the substrate with excellent thermal conductivity and electrical insulation.
Metallization Layers: Conductive metals such as gold, silver, and copper are used for creating electrical connections on the substrate.
Dielectric Materials: Low-loss dielectric materials are used for insulation and maintaining signal integrity in high-frequency applications.
Protective Coatings: Coatings such as silicon nitride or alumina are applied to protect the substrate from oxidation and environmental degradation.
What Size are AlN Substrates?
The size of AlN substrates varies depending on the application and specific design requirements:
Thickness: The thickness of AlN substrates can range from a few hundred micrometers to several millimeters, depending on the thermal and mechanical requirements.
Dimensions: The length and width of the substrates are determined by the size of the components and the layout of the system. They can range from small form factors for compact devices to larger substrates for complex electronic systems.
The Manufacturing Process of AlN Substrates
The manufacturing process of AlN substrates involves several precise and controlled steps to ensure high quality and performance:
High-purity aluminum nitride powder is prepared through chemical processes to ensure the desired purity and particle size distribution.
The AlN powder is pressed into green bodies using uniaxial or isostatic pressing techniques. These green bodies are then sintered at high temperatures in a controlled atmosphere to form dense, polycrystalline AlN substrates.
The sintered AlN substrates are machined to the desired dimensions and polished to achieve a smooth surface finish. This step is critical for ensuring good adhesion of metallization layers and reliable electrical performance.
Conductive layers are deposited onto the AlN substrates using techniques such as sputtering, evaporation, or screen printing. These metallization layers form the electrical pathways on the substrate.
The finished AlN substrates undergo rigorous inspection and testing to ensure they meet all design specifications and performance requirements. This includes checking for mechanical integrity, 열전도율, and electrical insulation properties.
AlN substrates are used in a wide range of high-performance applications:
In semiconductor devices, AlN substrates are used for their excellent thermal management properties, helping to dissipate heat generated by high-power components and maintaining device performance.
What are the Advantages of AlN Substrates?
AlN substrates offer several advantages that make them indispensable in high-performance applications:
High Thermal Conductivity: AlN substrates provide excellent thermal management, dissipating heat efficiently and maintaining the performance of high-power components.
Electrical Insulation: AlN substrates offer excellent electrical insulation properties, making them suitable for applications requiring reliable electrical isolation.
Mechanical Strength: AlN substrates provide robust mechanical support, withstanding thermal cycling and mechanical stresses during operation.
Low Dielectric Loss: AlN substrates offer low dielectric loss and stable dielectric properties, ensuring minimal signal attenuation and distortion in high-frequency applications.
Biocompatibility: AlN substrates are biocompatible, making them suitable for use in medical devices and other applications where biocompatibility is essential.
자주 묻는 질문(FAQ)
What are the key considerations in designing an AlN substrate?
Key considerations include material selection for thermal and electrical performance, layer stack-up for thermal management and electrical routing, and ensuring mechanical stability and reliability.
How do AlN substrates differ from other ceramic substrates?
AlN substrates offer higher thermal conductivity and better electrical insulation properties compared to other ceramic substrates such as alumina (알2O3). This makes them more suitable for high-power and high-frequency applications.
What is the typical manufacturing process for AlN substrates?
The process involves powder preparation, pressing and sintering, machining and polishing, metallization, and rigorous inspection and testing to ensure high quality and performance.
What are the main applications of AlN substrates?
AlN substrates are used in semiconductor devices, LEDs, RF and microwave devices, power electronics, and medical devices, providing advanced functionality and reliability in high-performance environments.