What are Ultrathin BGA Package Substrates?
Ultrathin BGA Package Substrates Manufacturer.As a manufacturer specializing in ultrathin BGA package substrates, we pride ourselves on precision engineering and cutting-edge technology. Our substrates are meticulously crafted to meet the stringent demands of modern electronics, offering unrivaled thinness without compromising on performance or durability. With a relentless commitment to innovation, we provide solutions that empower next-generation devices, from smartphones to IoT gadgets. Our state-of-the-art facilities and experienced team ensure the highest quality standards, making us the preferred choice for companies seeking reliable, high-performance substrate solutions.
Ultra-thin BGA Package Substrates are a flat and functional electronic component foundation that plays a vital role in modern electronic devices. 通常, this substrate is made from a non-conductive material such as fiberglass, epoxy or composite. Its key feature is its extremely thin design, which allows it to significantly reduce the overall thickness of electronic devices while maintaining stability. It is especially suitable for electronic products that require thinness and lightness.
On the ultra-thin BGA package substrate, conductive paths, namely wiring, are formed by etching or printing. The design of these traces is fine and compact, providing precise electrical connections to the various electronic components mounted on the substrate. Due to their ultra-thin design, these substrates enable more efficient connections between electronic components in densely laid out circuits, thereby improving overall circuit performance and reliability.
The manufacturing process of ultra-thin BGA packaging substrates usually requires multiple rigorous steps, including preparation of substrate materials, design and production of traces, drilling of component holes, coating of solder cap layers, and final component assembly and testing. These steps require a high degree of technical and process control to ensure the final substrate has stable performance and reliability.
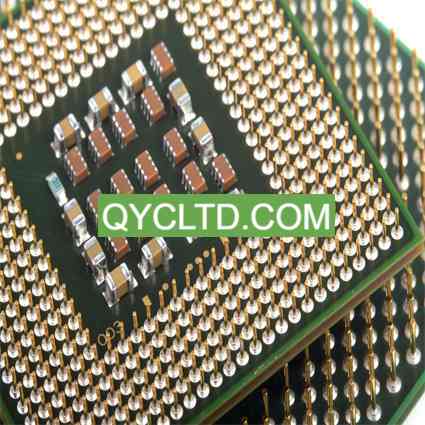
Ultrathin BGA Package Substrates Manufacturer
実際のアプリケーションで, ultra-thin BGA packaging substrates are widely used in many fields, including smartphones, tablet computers, portable electronic equipment, medical equipment, および産業オートメーション. Its ultra-thin design makes it particularly suitable for application scenarios that require thin, light and highly integrated devices, providing important support for the design and manufacturing of modern electronic products.
原則として, ultra-thin BGA packaging substrate, as a key component in modern electronic equipment, plays an extremely important role. Its precise design and manufacturing process, as well as its wide range of application fields, make it an important force in promoting the progress of electronic technology and product innovation.
Ultrathin BGA Package Substrates design Reference Guide.
When designing ultra-thin BGA packaging substrates, several factors need to be considered to ensure that the final product has good functionality and performance. These factors include component placement, routing of electrical connections, シグナルインテグリティ, thermal management, and manufacturability.
まずは, component layout is a crucial step in the design process. Proper component layout can minimize the size of the circuit board and ensure that the electrical connection paths between various components are as short as possible, thereby reducing signal transmission delays and interference. さらに, a good layout can also improve the heat dissipation effect of the circuit board and help maintain a stable operating temperature of the components.
第二に, the routing of electrical connections needs to be carefully designed to ensure the stability and reliability of signal transmission. During the routing process, attention needs to be paid to avoiding cross-interference between signal lines and the length of the signal return path, and adopting appropriate inter-layer wiring methods to minimize signal noise and distortion.
同時に, signal integrity is one of the key issues that need to be considered during the design process. By adopting appropriate impedance matching and signal layer design, reflection and power loss during signal transmission can be effectively reduced, ensuring signal stability and accuracy.
さらに, thermal management is also one of the factors that must be considered in the design of ultra-thin BGA package substrates. By rationally designing the heat dissipation structure and heat dissipation channels, the heat dissipation efficiency of the circuit board can be effectively improved, preventing components from being damaged due to overheating, thereby ensuring the long-term stable operation of the product.
最終的に, the manufacturability of the design is key to ensuring smooth mass production of the product. During the design process, it is necessary to consider the requirements of the manufacturing process and avoid overly complex or unrealizable design solutions to ensure that the production cost and production cycle of the product can be controlled within a reasonable range.
まとめると, designing an ultra-thin BGA packaging substrate requires comprehensive consideration of factors such as component layout, electrical connection routing, シグナルインテグリティ, thermal management, and manufacturability. Only by taking reasonable and comprehensive considerations into these aspects can we design ultra-thin BGA packaging substrate products with excellent performance, 安定性と信頼性.
What material is used in Ultrathin BGA Package Substrates?
The materials used in ultra-thin BGA packaging substrates are crucial to their performance and application range. 通常, these substrates are made from materials such as fiberglass reinforced epoxy (FR4). FR4 is a common substrate material with good mechanical properties, insulation properties and heat resistance, making it suitable for many common electronic applications.
しかし, under specific application requirements, other materials may be required for ultra-thin BGA packaging substrates. 例えば, when higher thermal stability is required in high-temperature environments, ポリイミド (円周率) substrates can be selected. Polyimide substrates have excellent high temperature resistance and chemical stability and are suitable for aerospace, 自動車用電子機器, industrial control and other fields.
かつ, for applications where size and weight are critical, such as portable electronics or aerospace devices, ceramic substrates may be a better choice. Ceramic substrates have excellent mechanical and thermal properties, as well as low dielectric constant and loss, providing higher signal transmission rates and stability.
さらに, some special applications may require metal core substrates. Metal core substrates have excellent thermal conductivity properties and are suitable for high power density and high frequency electronic devices such as LED lighting, power modules and radio frequency (RF) アプリケーション.
そこで, the choice of materials for ultra-thin BGA packaging substrates should be weighed and selected based on specific application needs to ensure that the final product has good performance, reliability and cost-effectiveness.
What size are Ultrathin BGA Package Substrates?
The dimensions of ultra-thin BGA package substrates vary depending on the specific application and design of the electronic device or system. They can range in size from small substrates for mobile phones and wearable devices to large substrates for industrial equipment and telecommunications infrastructure.
In the field of consumer electronics, the size demand for ultra-thin BGA packaging substrates is particularly prominent. Smartphones, 錠剤, smartwatches and other portable devices have strict requirements on substrate size. These devices have limited internal space and therefore require very small and highly integrated substrates. 通常, these substrates range in size from a few millimeters to several centimeters to accommodate compact device designs while ensuring performance and thermal requirements.
例えば, the ultra-thin BGA packaging substrate in smartphones is usually within a few tens of millimeters in length and width, and the thickness is controlled below 1 millimeter. This size can effectively support the packaging of high-density integrated circuits while meeting the needs of mobile phones for thinness, lightness and portability. さらに, the ultra-thin design leaves more space for the battery and other functional components, thereby improving overall device performance and user experience.
Wearable devices such as smart watches and fitness trackers have stricter substrate size requirements. Due to the smaller size of these devices, ultra-thin BGA package substrates may be only a few millimeters square and even less than 0.5 mm thick. This extreme size design not only requires a precise manufacturing process, but also requires materials with high strength and good heat dissipation properties to ensure the reliability and comfort of the device during long-term use.
In industrial equipment and telecommunications infrastructure, the sizes of ultra-thin BGA packaging substrates are more diverse. These applications typically require larger substrate sizes to support more complex circuits and more connection interfaces. 例えば, substrates in servers and communications equipment may be hundreds of millimeters long and wide, with thicknesses ranging from 0.5 mm to 2 mm depending on specific design requirements. The larger substrate size can accommodate more electronic components and complex circuit designs, while providing better heat dissipation performance to ensure stable operation of the device under high load conditions.
さらに, the application of ultra-thin BGA packaging substrates in automotive electronics and medical equipment also presents diverse size requirements. Automotive electronic systems, such as engine control units and in-vehicle infotainment systems, require substrates that are both strong and thin to handle harsh operating environments and vibration conditions. Medical devices such as portable diagnostic instruments and implantable devices require extremely small and reliable substrates to meet stringent volume and performance requirements.
まとめ, the size of ultra-thin BGA packaging substrates depends on its specific application scenarios, ranging from micro substrates of a few millimeters to large substrates of hundreds of millimeters. Substrates of different sizes not only meet the design needs of various types of electronic equipment, but also ensure the performance and reliability of the equipment in various environments through optimized manufacturing processes and material selection. Whether it is consumer electronics or industrial and medical applications, ultra-thin BGA packaging substrates are promoting the development of electronic devices in the direction of smaller, thinner and stronger.
The Manufacturer Process of Ultrathin BGA Package Substrates.
The manufacturing process of ultra-thin BGA packaging substrates is a highly refined and multi-step process, ensuring that each substrate meets high quality and performance standards. The following are the main steps in the manufacturing process, each with its key role:
The first step in the manufacturing process is substrate preparation. 通常, the substrate is made of fiberglass reinforced epoxy (FR4), or other materials such as ceramic or polyimide depending on application needs. Substrate materials must meet strict thickness and flatness requirements to ensure the quality of the final product. Substrates are typically cleaned and surface treated first to remove any impurities that may affect subsequent processes.
In the manufacturing of multi-layer PCBs, layer alignment is a crucial step. The conductive patterns on each layer must be precisely aligned to ensure correct electrical connections and signal integrity. The alignment process typically uses optical alignment systems, which can provide sub-micron accuracy. The aligned layers are temporarily bonded together in preparation for further processing.
The formation of conductive traces is achieved through etching or printing techniques. Etching involves covering the surface of a substrate with a layer of photosensitive material, exposing and developing it through a mask to pattern the conductive areas that need to be retained, and then etching away the unprotected copper layer in a chemical solution. Printing technology uses conductive ink to print patterns directly on the substrate, which is suitable for flexible substrates for some special applications.
In order to mount electronic components and make electrical connections between multiple layers, holes need to be drilled into the substrate. The diameter and position accuracy of these holes are critical, especially in high-density BGA packages. Drilling is typically done using high-precision mechanical drills or laser drills, which can process tiny hole diameters and ensure the exact location and size of each hole.
The solder cap layer is coated to protect the conductive pattern from the external environment and prevent short circuits during the soldering process. The solder cap layer is usually a green or other colored epoxy material that covers a non-conductive area on the surface of the substrate. After application, the weld cap layer needs to be cured, usually by heat treatment.
During the component assembly process, electronic components are placed precisely in designated locations on the substrate. This process typically uses automated equipment, such as a pick-and-place machine, to place components on pads pre-coated with solder paste. The solder paste melts during the subsequent reflow soldering process, forming a strong electrical and mechanical connection.
The final step in the manufacturing process is testing. Each substrate must undergo rigorous electrical and functional testing to ensure there are no manufacturing defects. These tests include open and short circuit tests, functional tests and thermal cycle tests to ensure that each substrate can work stably under various operating conditions.
Through the above-mentioned detailed manufacturing steps, the ultra-thin BGA packaging substrate can achieve high-density and high-performance requirements and meet the stringent requirements for reliability and precision of modern electronic equipment. Every aspect of these manufacturing processes is critical, ensuring the quality and performance of the final product.
The Application area of Ultrathin BGA Package Substrates.
Ultra-thin BGA packaging substrates play an important role in modern technology and are widely used in multiple industries, including consumer electronics, 自動車, 航宇, medical equipment, telecommunications, および産業オートメーション. Its outstanding performance and design flexibility make it a core component of various high-tech equipment.
In the field of consumer electronics, ultra-thin BGA packaging substrates are favored for their compact design and high performance. Portable devices such as smartphones, 錠剤, and laptops require high-density packaging and efficient heat dissipation, which makes ultra-thin BGA substrates an ideal choice. Its miniaturized design not only saves space, but also improves the overall performance and reliability of the device. さらに, emerging electronic products such as smart watches and wearable devices are increasingly using ultra-thin BGA packaging substrates to meet the needs of lightweight and high performance.
The automotive industry is increasingly dependent on electronic systems, from engine control units to in-car entertainment systems to advanced driver assistance systems (ADAS), and ultra-thin BGA packaging substrates play a vital role in these applications. Since automotive electronic systems usually work in harsh environments, the high reliability and good thermal performance of ultra-thin BGA packaging substrates are particularly important. They can withstand the challenges of high temperature, vibration and humidity, ensuring long-term stable operation of vehicle electronic systems.
In the aerospace industry, electronic equipment has extremely strict weight and size restrictions. Ultra-thin BGA packaging substrates have become an ideal choice for spacecraft and aircraft electronic systems due to their lightweight and high performance. From navigation systems to communication equipment to flight control computers, ultra-thin BGA packaging substrates can provide reliable support. Its excellent thermal performance and high-density packaging capabilities ensure the normal operation of these critical systems under extreme conditions.
Medical equipment has very high requirements for accuracy and reliability, and ultra-thin BGA packaging substrates play an important role in this field. Whether it is portable diagnostic equipment, implantable medical equipment, or large-scale medical imaging equipment, ultra-thin BGA packaging substrates can provide stable performance and efficient signal transmission. Its miniaturized design makes medical equipment more portable and easier to use, while ensuring high-precision data processing and real-time monitoring.
The telecommunications industry has extremely high requirements for high-speed data transmission and high reliability. Ultra-thin BGA packaging substrates are widely used in telecommunications equipment such as base stations, routers, and switches. Its excellent electrical performance and high-density connection capabilities support the rapid transmission and processing of large amounts of data. さらに, with the development of 5G technology, the demand for ultra-thin BGA packaging substrates will further increase to meet higher frequency and lower latency requirements.
Industrial automation equipment requires highly reliable electronic systems to ensure the continuity and efficiency of the production process. Ultra-thin BGA packaging substrates are widely used in equipment such as industrial controllers, sensors, and robots. Its excellent thermal management and high-density packaging capabilities ensure the stable operation of industrial electronic equipment under high loads and complex environments.
要は, ultra-thin BGA packaging substrates are widely used in various industries due to their unique advantages. From consumer electronics to automobiles, from aerospace to medical equipment, to telecommunications and industrial automation, ultra-thin BGA packaging substrates are driving the development and innovation of modern technology. Its superior performance and versatility make it a key component in the design of future electronic products.
What are the advantages of Ultrathin BGA Package Substrates?
Ultra-thin BGA packaging substrates play a key role in modern electronic devices and have many significant advantages over other wiring methods. These advantages, discussed in detail below, include compact size, high reliability, ease of mass production, reduced assembly errors, improved signal integrity, and improved thermal performance.
Ultra-thin BGA packaging substrate is much smaller in size than traditional PCB due to its highly integrated design and ultra-thin characteristics. This compactness makes it ideal for use in small electronic devices that need to save space, such as smartphones, 錠剤, and wearables. Its compact size not only reduces the size of electronic devices, but also improves design flexibility, making products more lightweight and portable.
High reliability is another major advantage of ultra-thin BGA packaging substrates. Due to its strict manufacturing process and material selection, ultra-thin BGA substrates can maintain stable performance under extreme conditions. This is particularly important for applications that require long-term reliable operation such as medical equipment, automotive electronics and aerospace systems. さらに, the solid structure of the ultra-thin BGA packaging substrate can effectively resist mechanical shock and vibration, further improving its reliability.
The design and manufacturing process of ultra-thin BGA packaging substrates have been highly standardized, making them ideal for mass production. Mass production not only reduces unit costs but also ensures product consistency. Manufacturers can efficiently produce ultra-thin BGA substrates through automated production lines, thereby shortening the production cycle and meeting the market’s rapid demand for high-performance electronic products.
In the electronic device assembly process, precision is critical. The ultra-thin BGA packaging substrate uses advanced manufacturing technology, and its high-precision design can significantly reduce assembly errors. Through its ball grid array structure, the BGA package enables more precise positioning of soldering points, reducing the risk of deviations and short circuits caused by traditional pin soldering methods. This not only improves production efficiency, but also improves the quality and reliability of the final product.
In high-frequency and high-speed signal transmission, signal integrity is a critical factor. The ultra-thin BGA packaging substrate uses high-quality materials and precise wiring design, which effectively reduces electromagnetic interference and crosstalk in signal transmission. Its optimized interlayer structure and uniform dielectric constant keep signals stable and clear during transmission. This is particularly important for equipment that requires high-precision and high-speed data processing, such as computers, communication equipment, and high-end audio and video equipment.
As the functionality and integration of electronic devices increases, heat dissipation issues become increasingly important. The ultra-thin BGA packaging substrate fully considers thermal management in its design. By using materials with excellent thermal conductivity and optimized heat dissipation channels, heat is effectively conducted away from high-heat areas. Its thin-layer structure also allows heat to diffuse more quickly, lowering the operating temperature of electronic components, extending the life of the device and improving overall performance.
まとめ, ultra-thin BGA packaging substrates have become an indispensable component of modern electronic devices due to their compact size, high reliability, ease of mass production, low assembly errors, improved signal integrity and superior thermal performance. With the continuous advancement of technology and the increasing market demand, ultra-thin BGA packaging substrates will show their unique advantages and broad application prospects in more fields.
FAQ
What is the design software for ultra-thin BGA packaging substrate?
Designing ultra-thin BGA packaging substrates requires professional circuit design software, such as Altium Designer, Cadence Allegro, 等. These softwares provide a wealth of functionality for component layout, routing, signal integrity analysis, and more.
What materials are used in ultra-thin BGA packaging substrates?
Ultra-thin BGA packaging substrates usually use materials such as glass fiber reinforced epoxy resin (FR4), ポリイミド (円周率) or metal core substrates. Factors such as temperature characteristics, dielectric constant, and mechanical strength need to be considered when selecting materials.
What are the key steps in the manufacturing process of ultra-thin BGA packaging substrate?
The key steps in manufacturing ultra-thin BGA packaging substrates include substrate preparation, layer alignment, conductive trace etching or printing, component hole drilling, solder cap layer coating, component assembly and testing, 等.
What are the limitations on the size of ultra-thin BGA package substrates?
The size of the ultra-thin BGA packaging substrate is limited by the manufacturing process, material properties, and the size of the electronic device to which it is applied. 通常, smaller substrates are suitable for portable devices, while larger substrates are suitable for industrial equipment and communication systems.
How to deal with thermal management of ultra-thin BGA package substrate?
Due to the small size of ultra-thin BGA package substrates, thermal management is particularly important. Heat sinks, radiators, heat pipes and other methods are usually used to effectively handle heat to ensure the normal operation of electronic components and extend their life.