What are RF Package Substrates?
RF Package Substrates Manufacturer.As an RF Package Substrates Manufacturer, we specialize in crafting advanced substrates tailored for radio frequency applications. Our expertise lies in developing high-performance substrates optimized for wireless communication, レーダーシステム, and satellite technology. With a focus on precision engineering and cutting-edge materials, we ensure optimal signal integrity and reliability in demanding RF environments.
RF Package Substrates are key components designed to support radio frequency (RF) circuits. These substrates use specific materials and manufacturing processes designed to ensure stable transmission of RF signals and optimization of high-frequency characteristics. 通常, RF Package Substrates are constructed of specific dielectric materials, such as polytetrafluoroethylene (PTFE) or hybrid ceramics, to meet the special requirements of RF circuits.
The design and manufacturing process of RF Package Substrates involves multiple key technologies, including high-frequency characteristic optimization, impedance matching and electromagnetic compatibility design. During the design stage, parameters such as dielectric constant, dielectric loss, line width, and spacing need to be considered to ensure the stability and performance of RF signals in high-frequency environments. さらに, RF Package Substrates also need to take appropriate shielding and grounding measures to reduce external interference and protect sensitive circuits.
In terms of material selection, RF Package Substrates usually use materials with excellent dielectric properties and high temperature resistance. PTFE substrate is widely used in high-frequency RF circuit design due to its low loss and high dielectric constant. Hybrid ceramic substrates combine the advantages of ceramics and organic materials, have good high-frequency characteristics and mechanical strength, and are suitable for complex RF packaging applications.
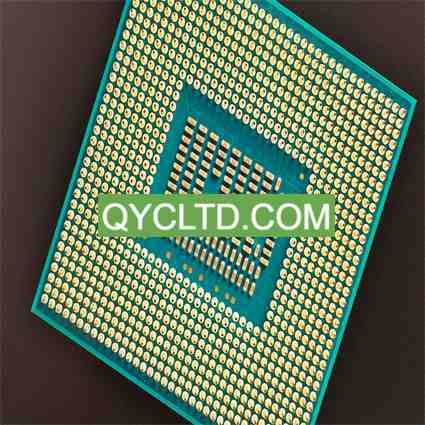
RF Package Substrates Manufacturer
原則として, RF Package Substrates play an important role in the fields of modern communication equipment, レーダーシステム, satellite communications, ワイヤレスネットワーク, and medical electronics, providing reliable support and guarantee for high-frequency circuits in these fields. By having an in-depth understanding of the key technologies and application fields of RF Package Substrates, we can better understand and apply the key technologies in this field, improve the level of RF circuit design, and solve practical engineering problems.
RF Package Substrates design Reference Guide.
RF package substrate design is a crucial part of RF circuit design, which directly affects the performance and stability of the system. This guide is intended to provide a comprehensive reference to help design engineers effectively design RF package substrates and ensure high-frequency circuit reliability and excellent performance.
The design of RF packaging substrates requires special attention to the optimization of high-frequency characteristics, including factors such as dielectric constant, dielectric loss and conductivity. By selecting appropriate substrate materials and controlling parameters such as line width and spacing, precise control of high-frequency signals can be achieved and the system’s operating frequency and signal transmission efficiency can be improved.
Good impedance matching is one of the keys to RF circuit design. In the design of RF packaging substrates, measures such as appropriate line width, スペーシング, and interlayer structure need to be adopted to ensure the impedance matching of signals throughout the circuit, reduce signal reflection and loss, and improve system performance and stability.
Radio frequency circuits often have high requirements for electromagnetic interference (EMI) and electromagnetic compatibility (EMC). In the design of RF packaging substrate, effective shielding and grounding measures need to be taken to reduce the system’s sensitivity to external interference and ensure the stable operation and reliability of the system.
The material selection of RF packaging substrate directly affects the performance and cost of the system. Commonly used materials include polytetrafluoroethylene (PTFE), hybrid ceramics, 等。, which have excellent dielectric properties and high-frequency characteristics and are suitable for different radio frequency application scenarios.
The manufacturing process of RF packaging substrates includes substrate preprocessing, printed circuits, metallization, assembly and testing. Advanced manufacturing technology and equipment ensure precision processing and high-quality production of packaging substrates, ensuring system performance and reliability.
RF package substrate design is a crucial part of RF circuit design and is directly related to the performance and stability of the system. By in-depth understanding of key technologies such as high-frequency characteristic optimization, impedance matching design, EMI/EMC design, 材料の選択, and manufacturing processes, design engineers can effectively design RF packaging substrates to ensure high performance and reliability of the system.
What material is used in RF Package Substrates?
RF packaging substrate is a key component used to support radio frequency (RF) circuits. Its material selection is crucial and directly affects RF performance and signal transmission quality. In the manufacturing of RF packaging substrates, commonly used materials include polytetrafluoroethylene (PTFE) substrates and hybrid ceramic substrates.
まずは, ポリテトラフルオロ エチレン (PTFE) substrate is a very common RF packaging substrate material. PTFE has excellent dielectric properties, low dielectric loss and high temperature resistance, making it an ideal choice for high-frequency RF circuit design. The characteristics of PTFE substrate include low loss dielectric constant and stable dielectric properties, and it has good signal transmission characteristics in high frequency environment. そこで, PTFE substrates are often used to manufacture packaging substrates for microstrip antennas, power amplifiers and other high-frequency radio frequency circuits.
第二に, hybrid ceramic substrate is also one of the commonly used materials for RF packaging substrates. Hybrid ceramic substrates combine the advantages of ceramics and organic materials, and have both good high-frequency characteristics and high mechanical strength and processing performance. The characteristics of hybrid ceramic substrates include high dielectric constant, low dielectric loss and excellent high temperature resistance, making them suitable for complex RF packaging applications. In some demanding RF applications, hybrid ceramic substrates can provide better performance and reliability.
原則として, the material selection for RF packaging substrate depends on the specific application needs and design requirements. Both polytetrafluoroethylene (PTFE) substrates and hybrid ceramic substrates have their own advantages and scope of application, and play an important role in RF circuit design. そこで, when selecting RF packaging substrate materials, it is necessary to fully consider factors such as its dielectric properties, mechanical strength, processing performance, and cost to ensure that design requirements are met and good RF performance is achieved.
What size are RF Package Substrates?
The size of the RF package substrate typically varies from application to application, depending on the required circuit complexity, frequency requirements, and packaging space constraints. Generally speaking, RF packaging substrates can have different size ranges, ranging from as tiny as a few millimeters to as large as tens of centimeters. Here are examples of some common size ranges:
Micro packaging substrate: For some micro RF devices, such as microstrip antennas, RF identification tags, 等。, the size of the packaging substrate is usually small, maybe only a few millimeters to a few centimeters in size. These miniature substrates are often used in portable devices or embedded systems.
Medium packaging substrate: For some medium-complexity RF circuits, such as wireless communication modules, antenna arrays, 等。, the size of the packaging substrate may be slightly larger, usually between a few centimeters to tens of centimeters. These packaging substrates are commonly found in devices such as smartphones and wireless routers.
Large packaging substrate: For some complex RF systems, such as radar systems, satellite communication equipment, 等。, the packaging substrate may be larger, even exceeding tens of centimeters in size. These large substrates are typically used in industrial-grade applications that need to support more complex RF functions and higher performance requirements.
原則として, RF packaging substrates are available in a wide range of sizes and can be custom designed to meet specific application needs. そこで, when designing and selecting RF packaging substrates, factors such as circuit function, packaging space, performance requirements, and cost need to be comprehensively considered to ensure optimal performance and reliability.
The Manufacturer Process of RF Package Substrates.
The manufacturing process of RF packaging substrate is a complex and precise process involving multiple key links to ensure the high quality and reliability of the final product. The following are the main steps in the manufacturing process of RF packaging substrates:
まずは, select an appropriate substrate material, usually one with excellent high-frequency properties, such as PTFE or hybrid ceramics. The substrate is then pre-treated, including cleaning, removing surface oxide and applying a special adhesive.
The next step is to print the circuit pattern on the surface of the substrate. This is usually accomplished through a process of photolithography and etching, where the circuit pattern is transferred to photoresist and then etched on the copper foil to form the required conductive paths.
After the circuit is printed, it needs to be metallized to enhance conductivity and corrosion resistance. This step involves plating a layer of metal (usually copper) onto the surface of the circuit to create a conductive layer.
After metallization is complete, the assembly step proceeds. This includes installing RF components (such as amplifiers, filters, 等。) as well as other necessary components such as connectors and wires.
最終的に, the RF package substrate is tested. By using high-frequency test instruments and equipment, the performance of the circuit is comprehensively tested and evaluated to ensure that it meets the design requirements and has good working stability.
Through these steps, RF packaging substrate manufacturers can produce high-quality, reliable RF packaging substrates to meet the needs of various communication and RF applications.
The Application area of RF Package Substrates.
RF packaging substrates have a wide range of applications in various fields, mainly reflected in the following aspects:
Communication equipment: RF packaging substrates play a key role in communication equipment. Whether it is mobile communication base stations, satellite communication terminals or wireless LAN equipment, high-performance RF packaging substrates are required to support the transmission and processing of radio frequency signals. These devices need to have high-frequency characteristics, stability and anti-interference capabilities. RF packaging substrates can meet these needs and ensure the reliability and performance of communication equipment.
Radar system: Radar systems have extremely high requirements for high-frequency signal processing, and RF packaging substrates are one of the key components that support the high performance of radar systems. From military radar to civilian weather radar, RF packaging substrates are responsible for the important tasks of carrying, transmitting and processing radio frequency signals to ensure the accuracy and reliability of the radar system.
Satellite communications: The field of satellite communications requires high-performance radio frequency equipment to achieve communication between satellites and ground stations or mobile terminals. RF packaging substrate serves as a key interface in satellite communication systems, carrying the transmission and processing functions of radio frequency signals. High-density, high-reliability packaging substrates can ensure the stable operation and data transmission quality of satellite communication systems.
Wireless network: Wireless network equipment such as base stations, routers, wireless access points, 等. need to support the transmission and processing of high-frequency radio frequency signals. As the core component of these devices, the RF packaging substrate is responsible for the transmission and demodulation of radio frequency signals, ensuring the stability and coverage of the wireless network.
Medical electronics: In the field of medical electronics, RF packaging substrates are also widely used. 例えば, wireless monitoring sensors in medical equipment and radio frequency signal processing modules in medical imaging equipment all require high-performance RF packaging substrates to support data transmission and signal processing to ensure the accuracy and reliability of medical equipment.
まとめると, RF packaging substrates are widely used in fields such as communications, レーダー, satellite communications, wireless networks and medical electronics. They provide reliable support and guarantee for high-frequency circuits in these fields and promote the development of modern electronic technology. Continuous development and application.
What are the advantages of RF Package Substrates?
As an important part of radio frequency (RF) circuit design, RF packaging substrates have many advantages, which make them widely used in modern electronic equipment.
最初です, the RF packaging substrate has excellent high-frequency characteristics and can effectively transmit radio frequency signals. Its special design and material selection ensure low loss, stable impedance matching and accurate signal transmission, making it perform well in high-frequency environments.
第二に, the RF packaging substrate has good mechanical properties and reliability. The use of high-quality base materials and manufacturing processes ensures the stability and reliability of the packaging substrate under different temperature and humidity conditions, and is suitable for various harsh working environments.
さらに, RF packaging substrates offer flexible design and manufacturing capabilities. According to specific application requirements, packaging substrates of different sizes, levels and characteristics can be customized to meet the needs of different RF circuit designs, with high applicability and flexibility.
さらに, the RF packaging substrate has good EMI/EMC performance. The use of shielding and grounding technology effectively reduces the impact of external interference on RF circuits and ensures the stability and reliability of the system.
最終的に, RF packaging substrates have lower manufacturing costs and shorter production cycles. Advanced manufacturing technology and efficient production processes reduce manufacturing costs, improve production efficiency, and provide affordable solutions for RF circuit design.
まとめると, RF packaging substrate has the advantages of excellent high-frequency characteristics, reliable mechanical performance, flexible design, good EMI/EMC performance and low manufacturing cost. It is an indispensable and important component in modern RF circuit design.
FAQ
What is the difference between RF packaging substrate and ordinary PCB?
RF packaging substrates are specially designed for radio frequency circuits and have excellent high frequency characteristics and signal transmission performance. Compared with ordinary PCBs, RF packaging substrates are different in material selection, design optimization and manufacturing processes to meet stability and performance requirements in high-frequency environments.
How to choose the appropriate RF packaging substrate material?
Selecting the appropriate RF packaging substrate material requires consideration of factors such as dielectric constant, dielectric loss, high temperature resistance, and mechanical strength. Commonly used materials include polytetrafluoroethylene (PTFE) substrates and hybrid ceramic substrates, selected based on specific application needs.
How to achieve impedance matching of RF packaging substrate?
Impedance matching is the key to RF circuit design. The RF packaging substrate achieves impedance matching by controlling parameters such as line width, スペーシング, and interlayer structure to ensure signal transmission efficiency and stability.
What are the considerations for electromagnetic compatibility (EMC) design of RF packaging substrates?
RF packaging substrates need to consider electromagnetic interference (EMI) and electromagnetic compatibility (EMC) design, and take shielding and grounding measures to reduce external interference and protect sensitive circuits.
What is the manufacturing process of RF packaging substrate?
The manufacturing process of RF packaging substrates includes substrate preprocessing, printed circuits, metallization, assembly and testing. Advanced manufacturing technology and equipment ensure precision processing and high-quality production of packaging substrates.