What is RF Modules Substrate?
RF Modules Substrate Manufacturer.A leading innovator in electronic component fabrication, our company specializes in producing RF modules substrates, catering to diverse technological applications. With state-of-the-art facilities and a team of seasoned experts, we ensure precision engineering and superior quality in every substrate manufactured. Our commitment to excellence drives us to continually push the boundaries of substrate design and production, meeting the evolving demands of the industry. From prototyping to mass production, we offer tailored solutions that guarantee optimal performance and reliability, making us the preferred choice for RF module manufacturers worldwide.
RF module substrate, referred to as プリント基板 (Printed Circuit Board), is an indispensable component of radio frequency electronic equipment. As a type of printed circuit board, the RF module substrate carries the key components and connections of the radio frequency circuit, providing the necessary support structure for the wireless communication system. Driven by modern communication technology, the importance of RF module substrates has become increasingly prominent.
The design of the RF module substrate takes into account the characteristics and transmission requirements of the radio frequency signal. Compared with traditional line wiring, the design of RF module substrate pays more attention to signal integrity and anti-interference ability. Through precise layout and wiring, signal loss and crosstalk can be minimized and system performance and stability improved.
The materials used in the RF module substrate are also critical. Common materials include FR-4, PTFE (ポリテトラフルオロ エチレン), Rogers, Arlon, 等. These materials have different dielectric constants, dissipation factors and thermal properties, and the most appropriate material can be selected based on the requirements of the specific application to ensure optimal system performance.
The size of the RF module substrate usually depends on the purpose of the device and space constraints. They can range from a few millimeters for tiny devices to tens of centimeters for large base station equipment. In size design, factors such as performance, power consumption, cost, and physical space need to be comprehensively considered to meet the overall needs of the product.
まとめると, RF module substrates play a vital role in the field of modern communications. Through precision design and manufacturing, they provide stable and reliable support for wireless communication systems and promote the continuous progress and innovation of wireless technology.
RF Modules Substrate design Reference Guide.
Designing an RF module substrate is a complex and critical task that requires sophisticated technology and specialized knowledge. The development of design guidelines is critical to ensuring the performance and reliability of the final product.
まずは, designing the RF module substrate requires an understanding of RF signals. This includes a deep understanding of RF signal characteristics, propagation patterns, and interference relationships with other signals. Understanding the behavior of RF signals is critical to properly designing substrate layout and routing.
第二に, layout and routing specifications are key elements in design guidelines. Good layout design can minimize RF signal loss and interference, thereby improving system performance and stability. Cabling specifications include requirements for signal paths, lengths, and interlayer connections to ensure signal integrity and reliability.
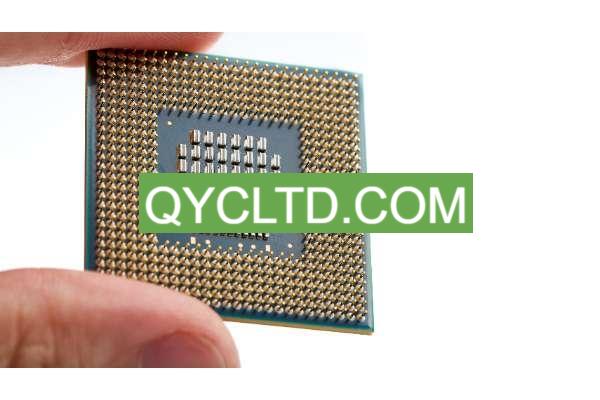
RF Modules Substrate Manufacturer
Signal integrity is another important aspect in design guidelines. This involves analysis and optimization of signal waveforms, timing and stability. With the right design and simulation tools, designers can ensure that signals are transmitted and processed within the substrate without distortion or loss.
最終的に, the management of EMI (Electromagnetic Interference)/EMC (Electromagnetic Compatibility) is a part of the design guidelines that cannot be ignored. Radio frequency circuits often produce strong electromagnetic radiation, which may cause interference to surrounding electronic equipment and systems. そこで, the design guide will include requirements for EMI/EMC test standards, as well as corresponding suppression and shielding measures.
まとめると, designing the RF module substrate requires comprehensive consideration of the characteristics of the RF signal, layout and wiring specifications, シグナルインテグリティ, and EMI/EMC management. Manufacturers often provide detailed design guidelines to help designers follow best practices during the design process to ensure the final product’s performance and reliability meet expected levels.
What material is used in RF Modules Substrate?
The performance of the RF module substrate is directly affected by the materials selected, and the selection of these materials is critical to the performance and stability of the RF system. Common RF module substrate materials include FR-4, PTFE (ポリテトラフルオロ エチレン), Rogers, Arlon, 等. Each material has unique properties that affect RF performance differently.
まずは, let’s take a look at the FR-4. This is one of the most common PCB substrate materials, is relatively inexpensive, and is suitable for many general-purpose RF applications. しかし, its relatively high dielectric constant may result in slower signal transmission and a certain signal loss.
In comparison, PTFE materials such as Teflon have a lower dielectric constant and loss factor, making it ideal for high-frequency RF applications. PTFE has excellent thermal stability and chemical stability and is suitable for applications in high temperature and high pressure environments.
さらに, specialized RF substrate materials such as Rogers and Arlon perform well in RF performance. They have lower loss factors and more stable dielectric constants, enabling higher signal transmission speeds and lower signal losses. These materials are often used in RF applications with high performance requirements, such as antenna design, microwave communications and radar systems.
When selecting RF module substrate materials, trade-offs need to be made based on specific application requirements. 例えば, for low-cost, high-volume production, FR-4 may be a suitable choice, while for applications with higher performance requirements, specialized RF substrate materials such as Rogers or Arlon may be required. さらに, factors such as material processing properties, availability and cost also need to be taken into consideration.
まとめ, the choice of RF module substrate material is crucial, as it directly affects the performance and stability of the RF system. When selecting materials, it is necessary to fully consider the application needs and conduct a comprehensive evaluation to ensure that the most suitable material is selected to meet the design requirements.
What size are RF Modules Substrate?
The size of the RF module substrate is one of the crucial considerations in the design process. The choice of these sizes depends not only on the specific use of the device, but also on a range of factors, such as performance requirements, power consumption constraints, cost budgets, and physical space constraints.
For small to micro devices, the size of the RF module substrate may be only a few millimeters. Such devices include smart wearable devices, sensor nodes, medical equipment, 等. Since these devices usually require the integration of multiple functional modules within a limited space, the RF module substrate must be small enough to ensure the compactness and portability of the device. 同時に, power consumption and cost are also crucial considerations for these devices, so the size selection needs to save energy consumption and cost as much as possible while ensuring performance.
In comparison, the size of the RF module substrate required for large base station equipment may be much larger, reaching tens of centimeters or even larger. These devices are typically used in communications infrastructure such as cell phone base stations, satellite communications stations, 等. Because these devices are typically deployed in relatively large spaces and need to handle large amounts of data traffic, the RF module substrate can be larger to accommodate more circuit components and connectors. さらに, performance is one of the most critical considerations for this type of equipment, so sizing is often chosen to maximize the stability and reliability of the equipment while ensuring performance.
Whether it is a small or large RF module substrate, the size selection requires comprehensive consideration of multiple factors, trade-offs and optimization at different design stages. Manufacturers and design engineers often leverage advanced design tools and simulation techniques to evaluate the performance and feasibility of different sizing options to ensure the final product meets customer needs and expectations.
そこで, the size selection of the RF module substrate is not only a technical issue, but also an engineering task that requires comprehensive consideration, which needs to meet the actual application needs of the equipment to the greatest extent while ensuring performance and reliability.
The Manufacturer Process of RF Modules Substrate.
The manufacturing process of RF module substrate is a complex and precise process, which involves multiple links, each of which has a vital impact on the performance and quality of the final product.
The first is the design verification phase. この段階では, engineers will use CAD software to design the PCB according to the customer’s needs and design specifications. Design verification includes simulation and analysis of layout, シグナルインテグリティ, EMI/EMC, 等. to ensure the feasibility and stability of the design.
Next is the procurement of raw materials. After determining the design plan, the manufacturer will purchase the required raw materials, including substrate materials, conductive materials, chemical treatments, 等. The selection and quality control of raw materials directly affects the performance and reliability of the final product.
Then comes the printing and chemical processing stage. この段階では, manufacturers will use printing technology to print the designed circuit pattern onto the substrate. Then, after chemical treatment, unnecessary parts are removed, leaving the required circuit patterns and conductive layers to form a complete circuit structure.
Drilling is the next critical step. この段階では, manufacturers use precision drilling equipment to drill holes into the substrate to install components and connect circuits. The precision and accuracy of drilling are crucial to the subsequent process.
Next comes the metallization stage. この段階では, manufacturers form a metallization layer on the surface of the substrate through chemical or physical methods to protect the wires and circuits from environmental influences and provide good electrical conductivity.
Assembly is another critical part of the manufacturing process. この段階では, the manufacturer will install the components on the substrate according to the design requirements and perform welding or other connection processes to form a complete RF module. The quality of assembly directly affects the stability and reliability of the product.
Finally comes the testing phase. この段階では, the manufacturer will conduct various performance tests and functional verification on the assembled RF module to ensure that it meets the design requirements and customer needs. Testing includes static testing, dynamic testing, temperature testing, 等. to ensure the stability and reliability of the product.
原則として, the manufacturing process of RF module substrates is a process that requires extremely high precision and quality control. Each link requires rigorous inspection and testing to ensure that the performance and reliability of the final product meet industry standards and customer expectations.
The Application area of RF Modules Substrate.
As a core component of radio frequency electronic equipment, RF module substrate is widely used in various fields. They not only provide critical support for fields such as communications, medical care, military, 航宇, automotive and industrial control, but also play an important role in promoting scientific and technological development and social progress.
最初です, in the field of communications, RF module substrates act as a bridge between people and people and things. From smartphones to communication base stations, the construction and operation of wireless networks are inseparable from high-performance RF module substrates. They not only provide stable signal transmission, but also support the development of various wireless communication technologies, such as 5G and the Internet of Things.
第二に, the medical field is also one of the important application fields of RF module substrates. In medical equipment, such as medical imaging equipment, vital signs monitoring instruments and medical wireless communication systems, RF module substrates play a key role. They ensure the stability, accuracy and safety of medical equipment and provide reliable technical support for medical diagnosis, treatment and monitoring.
Third, the demand for RF module substrates in the military field is also very important. From military communication equipment to radar systems, from navigation systems to drones, RF module substrates play a key role in military applications. They need to have a high degree of anti-interference capability, stable performance and secure communication guarantee to meet complex military requirements.
さらに, the aerospace field is also one of the important application fields of RF module substrates. In aerospace vehicles, avionics equipment and aviation communication systems, RF module substrates undertake tasks such as data transmission, navigation and positioning, and communication links, providing reliable technical support for aerospace exploration and aviation safety.
The automotive industry is also one of the important markets for RF module substrates. In modern automobiles, RF module substrates are used in vehicle communication systems, vehicle entertainment systems, インテリジェント運転支援システム, 等. They not only improve vehicle safety and comfort, but also provide a technical foundation for the development of smart transportation and smart cars.
最終的に, in the field of industrial control, RF module substrates are widely used in industrial automation, smart manufacturing, and the Internet of Things. They are used for sensor data collection, remote monitoring, equipment networking, 等。, providing more efficient and smarter solutions for industrial production and management.
要は, the wide application of RF module substrates in various fields not only promotes technological progress and innovation, but also provides strong support for social development and progress. With the continuous development of technology and the expansion of application scenarios, RF module substrates will continue to play an important role, injecting new power and vitality into the development of all walks of life.
What are the advantages of RF Modules Substrate?
RF module substrates continue to consolidate their position in wireless communication systems, and one of their advantages is that they have many advantages over traditional line wiring. The following is an extension of the advantages of RF module baseplates:
Higher integration
The RF module substrate achieves a high degree of integration by integrating multiple functional modules on a compact board. Compared with traditional line wiring, this level of integration greatly reduces the complexity and volume of the circuit, making the entire system more compact and lightweight. This is particularly important for applications with high space and weight requirements, such as mobile communications devices and embedded systems.
Better signal integrity
The design of the RF module substrate pays more attention to signal integrity, and through reasonable layout and wiring planning, signal interference and attenuation are effectively reduced. This design can maintain signal accuracy and stability to the greatest extent, and maintain good signal transmission quality in high-frequency environments. それに対して, traditional line wiring may have problems such as signal cross-interference and reflection loss, which affect the performance and stability of the system.
Lower signal loss
The design of the RF module substrate considers the loss in signal transmission, and takes corresponding measures to reduce signal loss. By selecting low-loss materials, optimizing wiring paths, and rationally designing power transmission structures, RF module substrates can reduce energy loss during signal transmission and improve system efficiency and performance. しかし, traditional line wiring may have problems such as wire impedance mismatch and line length mismatch, resulting in large signal loss.
Smaller size
RF module substrates usually have smaller sizes to meet the needs of space-constrained applications. This allows them to be easily integrated into a variety of devices, providing greater flexibility in device design and layout. 同時に, the small size of the RF module substrate also helps to reduce the weight and cost of the entire system and improve the portability and economy of the system.
まとめると, RF module substrates have the advantages of higher integration, better signal integrity, lower signal loss and smaller size than traditional line wiring. These advantages make them an ideal choice in wireless communication systems. Indispensable part. With the continuous development of wireless communication technology, RF module substrates will continue to play an important role in driving the entire industry forward.
FAQ
How long is the manufacturing cycle of RF module substrate?
A: The manufacturing cycle of RF module substrates usually depends on the size and complexity of the project, as well as the manufacturer’s production capacity and order status. Generally speaking, a simple RF module substrate may be fabricated in a few days, while complex projects may take weeks. During the design phase, it is important to communicate with the manufacturer and ensure adequate planning and time allowance to help ensure the project is completed on time.
What is the cost of RF module substrate?
The cost of RF module substrates is affected by many factors, including the type of material used, the size and number of layers of the board, production quantity, surface treatment requirements, and special processing techniques. そこで, it is not possible to provide a fixed price range. 通常, manufacturers provide personalized quotes based on the customer’s specific requirements. It is recommended to conduct detailed communication and quotation with the manufacturer before the project starts to ensure that the actual cost of the project is understood.
What special skills are required for the design of RF module substrates?
The design of RF module substrates requires in-depth RF and circuit knowledge, as well as an understanding of PCB layout and routing. さらに, proficiency in professional design software such as Altium Designer, Cadence Allegro, 等. is also necessary. Designers need to understand the transmission characteristics of RF signals on circuit boards and how to optimize layout and routing to ensure good signal integrity and interference immunity. 同時に, for complex projects, radio frequency simulation and electromagnetic compatibility testing may be required, so relevant skills and experience are also essential.
How to ensure the reliability of RF module substrate?
The reliability of the RF module substrate is one of the key factors to ensure long-term stable operation of the equipment. Manufacturers usually adopt strict quality control measures, including strict screening and testing of raw materials, strict monitoring and management of the production process, and comprehensive testing and verification of the final product. さらに, some manufacturers may also hold relevant certifications such as ISO 9001, which indicates that their quality management system has met international standards. Taking these factors into consideration, choosing an experienced and reputable manufacturer can effectively ensure the reliability of the RF module substrate.
What is the environmental performance of RF module substrates?
As environmental awareness increases, more and more manufacturers are paying attention to the environmental performance of their products. During the manufacturing process of RF module substrates, manufacturers usually take a series of environmental protection measures, including the compliant use of environmentally friendly materials, optimizing production processes to reduce waste and pollutant emissions, and promoting sustainable development concepts. Some manufacturers may also hold environmental management system certifications (such as ISO 14001) to ensure that their production activities comply with environmental standards and regulations. Choosing a manufacturer that pays attention to environmental protection can help improve the environmental performance of RF module substrates and contribute to the sustainable development of enterprises.