What is Microwave/Microtrace PCB?
Microwave/Microtrace プリント基板 Manufacturer. “Specializing in precision engineering, our company, Microwave/Microtrace PCB Manufacturer, stands at the forefront of technological advancement in printed circuit board production. With a relentless commitment to quality and innovation, we excel in crafting intricate circuitry solutions for diverse industries. Utilizing state-of-the-art manufacturing processes and cutting-edge materials, we ensure unparalleled performance and reliability in every PCB we produce. From prototype to mass production, our expertise and attention to detail guarantee the fulfillment of even the most demanding project requirements. Trust us to bring your electronic designs to life with precision and efficiency.”
Microwave/microtrace PCB (Printed Circuit Board) is a special PCB manufacturing technology widely used in high-frequency microwave applications. 従来のPCBとの比較, microwave/microtrace PCB pays more attention to the precise control and stability of high-frequency signals during the design and manufacturing process. It is a basic component that connects electronic components. It is a technology that fixes electronic components to insulating plates through a series of precise conductive paths. In microwave and high-frequency applications, circuit board size, circuit layout, 材料の選択, and manufacturing processes all have an important impact on system performance.
Microwave/Microtrace PCB manufacturing technology has unique advantages and application prospects in high-frequency microwave applications. It not only achieves stable transmission of high-frequency signals and good impedance matching, but also provides excellent performance in complex RF environments. The key lies in designing precise micro-circuits and conductive paths to ensure accurate signal transmission and efficient energy transfer. 同時に, Microwave/Microtrace PCB manufacturing technology also focuses on material selection, using high-frequency dielectric materials and special conductive materials to ensure stable performance and low loss in high-frequency environments.
Microwave/Microtrace PCBs are increasingly used in fields such as wireless communications, レーダーシステム, satellite communications, medical equipment, and high-speed data transmission. Its high frequency characteristics and stable performance make it the first choice for many critical applications. 正確な設計と製造プロセスを通じて, Microwave/Microtrace PCB can meet the needs of different industries for high-performance, high-reliability electronic systems, providing important support for the development of modern technology.
Microwave/Microtrace PCB design Reference Guide.
The key to Microwave/Microtrace PCB manufacturing is design. In the field of high-frequency microwaves, appropriate design is the key to ensuring stable signal transmission and good impedance matching. From routing to layout, the specificities of microwave and high-frequency signals need to be taken into account to ensure optimal PCB performance and reliability.
Cabling design
In Microwave/Microtrace PCB design, routing is a crucial step. The wiring path must be as short as possible to reduce signal transmission delays and losses. Especially in high-frequency microwave signal transmission, the length and shape of the path will have a significant impact on the signal transmission. そこで, designers need to accurately calculate and plan wiring paths to ensure stable signal transmission and minimal loss.
Layout design
Microwave/Microtrace PCB layout design is also critical. Layout design involves the placement of various components and the routing of wires. For high-frequency microwave signal transmission, the layout design must take into account factors such as the signal transmission path, the grounding method of the signal and the ground plane, and the interference between the signal and other signals. Professional layout design can minimize signal crosstalk and interference and ensure PCB performance and reliability.
インピーダンスマッチング
Impedance matching is a crucial consideration in Microwave/Microtrace PCB design. Impedance mismatch will cause signal reflection and loss, affecting signal transmission quality and stability. そこで, designers need to ensure that the impedance of the signal lines on the PCB matches the set value through appropriate line width, line spacing, and material selection. Professional design guides will provide designers with impedance matching calculation methods and technical guidance to ensure optimal PCB performance.
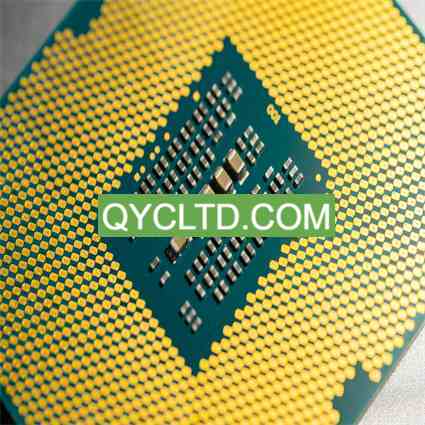
Microwave/Microtrace PCB Manufacturer
まとめると, the key to the success of Microwave/Microtrace PCB design lies in professional design guidelines and rigorous design process. Through proper routing design, layout design, and impedance matching, designers can ensure optimal PCB performance and reliability for high-frequency microwave applications.
What material is used in Microwave/Microtrace PCB?
The materials used in Microwave/Microtrace PCB manufacturing are key to ensuring its stable performance and low loss in high-frequency environments. These materials include high-frequency dielectric materials, conductive materials and special substrate 料.
まずは, high-frequency dielectric materials play a vital role in the manufacturing of Microwave/Microtrace PCBs. Among them, PTFE (ポリテトラフルオロ エチレン) is one of the most common high-frequency media. PTFE has excellent dielectric properties and stable chemical properties, providing excellent signal transmission performance in high-frequency environments. Its low dielectric loss and low water absorption make it ideal for microwave and high-frequency circuits.
第二に, FR-4 (グラスファイバー強化エポキシ) is also one of the commonly used Microwave/Microtrace PCB materials. Although FR-4’s high-frequency performance is slightly inferior to PTFE, it is cheaper and easier to process, making it suitable for the manufacture of certain low-frequency, high-speed circuits.
In addition to high-frequency dielectric materials, Microtrace PCB manufacturing also requires special conductive materials. Generally, copper is one of the most common conductive materials. The wires in Microtrace PCBs are usually made from thin copper foil to ensure good conductivity and reliability. Copper’s excellent electrical conductivity enables stable signal transmission, and its plasticity also makes it easier to manufacture fine circuits.
最終的に, the substrate material of Microtrace PCB is also crucial. In addition to high-frequency dielectric materials, Microtrace PCB also requires substrate materials with high mechanical strength and dimensional stability. 通常, materials such as plexiglass fiberboard (FR-4) or polyimide (円周率) are often chosen to ensure the stability and reliability of the PCB.
まとめると, the materials used in Microwave/Microtrace PCB manufacturing include high-frequency dielectric materials (such as PTFE, FR-4), conductive materials (such as copper), and special substrate materials (such as FR-4, 円周率). The selection of these materials ensures Microtrace PCB has stable performance and low loss in high-frequency environments, thereby meeting the needs of various microwave and high-frequency circuits.
What size are Microwave/Microtrace PCB?
The size of Microwave/Microtrace PCB is determined according to the needs of the specific application. Microwave/Microtrace PCB manufacturing technology has unique advantages and can realize the design of complex circuits and tiny sizes to meet high-density and high-performance requirements. Whether it is micro-devices in the communication field or high-frequency modules in satellite communication systems, Microtrace PCB has demonstrated excellent adaptability and plasticity.
The flexibility of Microwave/Microtrace PCB manufacturing technology allows PCB dimensions to be adjusted and optimized according to the needs of a specific application. For high-frequency microwave applications, a more compact design is usually required to ensure stable signal transmission and impedance matching. そこで, Microwave/Microtrace PCBs tend to be of relatively small size to meet the balance between device size and performance requirements.
This tiny size design is not only reflected in the overall size of the PCB, but also includes the layout of the circuit and the arrangement of components. Microwave/Microtrace PCB manufacturing technology enables higher circuit density and more compact layout to accommodate more functional modules and components in a limited space. This compact design not only helps improve the performance and functionality of the device, but also reduces the overall volume and weight, meeting the needs of modern electronic devices for thinness, lightness, and miniaturization.
In the Microtrace PCB manufacturing process, high-precision processing of circuits and preparation of fine features can be achieved through advanced processes and technical means. This allows Microwave/Microtrace PCB to achieve smaller circuit sizes and higher-density component layout, providing important support for the manufacturing of high-performance electronic devices.
原則として, the size of Microwave/Microtrace PCBs depends on the needs of the specific application, but its manufacturing technology enables the design of complex circuits and tiny dimensions to meet high-density, high-performance requirements. This flexibility and moldability make Microtrace PCBs play an irreplaceable role in modern electronic device manufacturing.
The Manufacturer Process of Microwave/Microtrace PCB.
The manufacturing process of microwave/microtrace PCB is a highly complex and precise engineering involving multiple technologies and steps to ensure the quality and performance of the final product.
まずは, the design team will conduct detailed design work based on the customer’s needs and application requirements. During the design phase, they will consider factors such as the frequency of signal transmission, インピーダンス整合, circuit layout, 等. to ensure that the PCB performs as expected.
Once the design is complete, next comes the core part of the manufacturing process. The process usually begins with the preparation of the PCB substrate. Use high-quality substrate materials, such as PTFE (ポリテトラフルオロ エチレン), 等。, to ensure the stable performance of the PCB in high-frequency environments.
Imaging technology is then used to transfer the designed circuit diagram to the substrate. This step typically involves photolithography and chemical etching to create the desired circuit pattern on the substrate surface. Precision photolithography equipment and chemical processing processes are key to ensuring pattern accuracy and clarity.
Next comes the electroplating process, where conductive paths are created by applying a layer of metal over the pattern. This process requires precise control of the composition and temperature of the plating solution to ensure the uniformity and density of the metal layer.
After metallization is complete, surface treatment is performed to enhance the corrosion resistance and soldering properties of the PCB. This includes applying protective layers and pads, as well as final surface treatments such as gold plating, silver plating, 等.
最終的に, perform quality control and testing. Each manufacturing step undergoes rigorous inspection and testing to ensure the quality and performance of the PCB meets requirements. This may involve using high-precision test equipment such as network analyzers and signal generators to test the PCB for frequency response, インピーダンス整合, transmission loss, 等.
Throughout the manufacturing process, strict quality control and professional technical support are crucial. Only in this way can the final microwave/microtrace PCB be guaranteed to meet the customer’s needs and perform well in high-frequency microwave applications.
The Application area of Microwave/Microtrace PCB.
Microwave/Microtrace PCB manufacturing technology is widely used in various fields, and its high-frequency characteristics and stable performance make it the first choice for many critical applications.
Communication field
In the field of communications, Microwave/Microtrace PCB is widely used in the construction of wireless network infrastructure. From base stations to antennas, Microwave/Microtrace PCBs play an important role in connecting and transmitting signals. Its high-frequency characteristics and superior performance ensure the stable operation of the communication system and provide reliable guarantee for people’s communication.
Radar technology
Radar technology is at the heart of many fields, including military, 航宇, weather and traffic monitoring. Microwave/Microtrace PCBs play a key role in radar systems, transmitting and processing radar signals. Its high-frequency characteristics and stable performance can meet the radar system’s high requirements for signal transmission and processing, and improve the detection accuracy and reliability of the radar system.
Satellite applications
In the fields of satellite communications, navigation and remote sensing, Microwave/Microtrace PCBs also play an important role. Satellite systems need to operate stably in extreme environments and have extremely high requirements for signal transmission and processing. The high-frequency characteristics and stable performance of Microwave/Microtrace PCB make it an ideal choice for satellite systems, ensuring the reliability and performance of satellite systems in various application scenarios.
Medical equipment
医療機器の分野で, Microwave/Microtrace PCBs are widely used in medical imaging equipment, diagnostic equipment, and treatment equipment. 例えば, MRI (magnetic resonance imaging) equipment and ultrasound equipment require high-performance electronic components to transmit and process signals. The high-frequency characteristics and stable performance of Microwave/Microtrace PCB make it the first choice of medical equipment manufacturers, 医療機器の精度と信頼性の確保.
まとめると, Microwave/Microtrace PCB manufacturing technology has a wide range of applications in communications, レーダー, satellites and medical equipment. Its high-frequency characteristics and stable performance make it the first choice for many key applications, providing strong support for the development and innovation of various industries.
What are the advantages of Microwave/Microtrace PCB?
Microwave/Microtrace PCB manufacturing technology has significant advantages in the high-frequency microwave field compared with traditional circuit boards. Below is a detailed description of these benefits:
まずは, Microwave/Microtrace PCBs have lower transmission losses. In the process of high-frequency microwave signal transmission, transmission loss is an important consideration. Microwave/Microtrace PCB manufacturing uses high-frequency dielectric materials and optimized design, which can reduce energy loss during signal transmission, thereby ensuring the stability and reliability of signal transmission.
秒, Microwave/Microtrace PCBs achieve better impedance matching. Impedance matching of high-frequency microwave signals is crucial to the stability of signal transmission. During the design and manufacturing process of Microwave/Microtrace PCB, we focus on optimizing impedance matching to ensure smooth transmission of signals between different parts and avoid signal reflection and interference, thereby improving the overall performance of the system.
かつ, Microwave/Microtrace PCBs have higher frequency response. In the field of high-frequency microwaves, frequency response is one of the key indicators for evaluating PCB performance. Microwave/Microtrace PCB manufacturing technology can achieve higher frequency response, making it suitable for a wide frequency range, from hundreds of megahertz to tens of gigahertz, to meet the needs of different applications.
最終的に, Microwave/Microtrace PCBs offer greater reliability. In high-frequency microwave environments, the reliability requirements for PCBs are more stringent. Microwave/Microtrace PCB manufacturing uses advanced materials and processes, and undergoes strict quality control and testing to ensure its stability and reliability. This enables Microwave/Microtrace PCB to maintain good performance in various harsh working environments and have a long-term stable working life.
全, Microwave/Microtrace PCB manufacturing technology enables it to perform well in the high-frequency microwave field by reducing transmission losses, optimizing impedance matching, improving frequency response, and enhancing reliability. For electronic device manufacturers who require high performance and reliability, choosing Microwave/Microtrace PCB manufacturing technology will be a wise choice.
FAQ
What is the difference between Microwave/Microtrace PCB and traditional PCB?
Microwave/Microtrace PCB differs from traditional PCB in material selection, wiring design and manufacturing process. まずは, the materials used in Microwave/Microtrace PCB usually have higher dielectric constant and lower dielectric loss to meet the transmission requirements of high-frequency microwave signals. 第二に, in terms of wiring design, Microwave/Microtrace PCB pays more attention to microwave characteristics and impedance matching. 最終的に, in terms of manufacturing process, Microwave/Microtrace PCB requires higher precision and professional processing equipment to ensure the quality and performance of the circuit board.
What are the applications of Microwave/Microtrace PCB in medical equipment?
Microwave/Microtrace PCBs have many important applications in medical devices, including medical imaging, vital sign monitoring, wireless communications, and medical diagnostics. 例えば, in the field of medical imaging, Microwave/Microtrace PCBs can be used for signal processing and data transmission in equipment such as ultrasound diagnosis, magnetic resonance imaging (MRI), and computed tomography (CT). In terms of vital signs monitoring, Microwave/Microtrace PCB can be used for sensor interfaces and data transmission of electrocardiogram (ECG), electroencephalogram (EEG) and blood oxygen monitoring equipment. Its high frequency characteristics and stable performance make it the first choice for medical device manufacturers.
What is Microwave/Microtrace PCB?
Microwave/Microtrace PCB is a printed circuit board designed for high frequency microwave applications. It has special design and manufacturing requirements to provide stable performance and low loss in high-frequency environments.
What frequency ranges are Microwave/Microtrace PCBs suitable for?
Microwave/Microtrace PCBs can be applied over a wide frequency range from a few hundred megahertz to tens of gigahertz. They are widely used in communications, レーダー, 衛星, medical equipment and other fields to meet the needs of high-frequency microwave transmission.
How are Microwave/Microtrace PCBs different from traditional PCBs?
While traditional PCBs are primarily used in low- and mid-frequency applications, Microwave/Microtrace PCBs are specifically designed for high-frequency microwaves. They differ in material selection, wiring design, manufacturing process, 等. to meet the special requirements in high-frequency environments.