IPC Class 3 PCB Manufacturer.IPC Class 3 PCB manufacturers adhere to the highest standards of quality and reliability in producing printed circuit boards. They ensure meticulous attention to detail and precision in every aspect of manufacturing, meeting stringent criteria for performance in demanding applications such as aerospace, medical devices, and telecommunications.
IPC Class 3 プリント基板 (Printed Circuit Boards) represent the pinnacle of quality and reliability standards in the electronics industry. These PCBs are designed for applications where performance, reliability, and extended service life are crucial, such as in aerospace, military, medical, and high-end industrial sectors. The IPC Class 3 standard ensures that these PCBs can endure the most demanding conditions without failure, providing unparalleled reliability.
What is IPC Class 3 プリント基板?
An IPC Class 3 プリント基板 is a printed circuit board manufactured according to the stringent standards set by the IPC (Institute for Printed Circuits) for high-reliability electronics. The IPC Class 3 standard is the highest performance classification and is intended for products where continuous operation is critical and downtime must be minimized.
High Reliability: Designed to perform reliably in harsh environments and under extended operational periods.
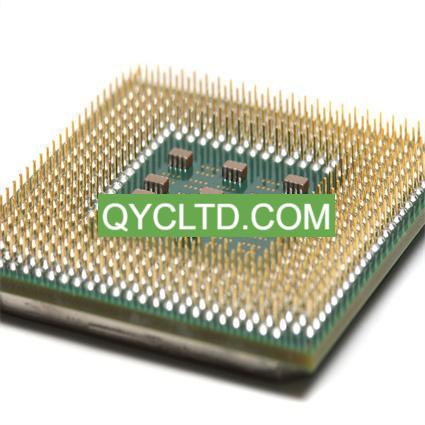
IPC Class 3 PCB Manufacturer
Extended Durability: Built to withstand extreme conditions such as high temperatures, vibration, and humidity.
Stringent Quality Control: Subjected to rigorous testing and inspection to ensure compliance with the highest performance standards.
IPC Class 3 PCB Design Reference Guide
Designing IPC Class 3 PCBs involves adhering to specific guidelines to ensure the highest level of performance and reliability. The following sections outline the critical aspects of designing these PCBs:
The choice of materials is crucial for IPC Class 3 プリント基板:
High-Quality Laminate: Materials such as FR-4, ポリイミド, and other high-reliability laminates are used to ensure durability and performance.
Copper: High-quality copper with precise thickness is used for the conductive traces, ensuring excellent electrical performance.
Solder Mask: High-performance solder masks that can withstand multiple thermal cycles and harsh environments are essential.
Several key design considerations must be addressed:
Trace Width and Spacing: Ensuring appropriate trace width and spacing to handle the required current and voltage without overheating.
Via Design: Using reliable via structures, such as through-hole, blind, and buried vias, to ensure robust electrical connections.
Impedance Control: Maintaining precise impedance control for high-speed signal integrity.
Thermal Management: Incorporating thermal vias, ヒートシンク, and appropriate layout strategies to manage heat dissipation.
What Materials are Used in IPC Class 3 プリント基板?
Materials used in IPC Class 3 PCBs are selected for their reliability and performance under demanding conditions:
High-Quality Laminates: Materials like FR-4, ポリイミド, and high Tg (glass transition temperature) laminates.
Copper: High-purity copper for conductive layers, providing excellent electrical and thermal conductivity.
Solder Mask: Durable solder masks that can withstand multiple reflow cycles and harsh environments.
Surface Finishes: High-reliability finishes like ENIG (無電解ニッケル浸漬金), OSP (Organic Solderability Preservative), and HASL (Hot Air Solder Leveling) for enhanced solderability and corrosion resistance.
What Size are IPC Class 3 プリント基板?
The size of IPC Class 3 PCBs can vary significantly depending on the application and design requirements:
Thickness: Typically ranges from a few millimeters to several centimeters, depending on the number of layers and the application requirements.
Dimensions: Length and width are determined by the specific design and can range from small form factors for compact devices to larger sizes for complex systems.
The Manufacturing Process of IPC Class 3 プリント基板
The manufacturing process of IPC Class 3 PCBs involves several precise and controlled steps to ensure the highest quality and reliability:
High-quality base materials are selected and prepared for processing. The materials are cleaned and treated to remove any impurities and ensure a smooth surface.
Dielectric material is applied to the substrate in multiple layers, with each layer being patterned and cured to form the desired circuit patterns. This process is repeated to build up the required number of layers, ensuring high-density interconnects and excellent electrical performance.
Microvias and through-holes are drilled into the substrate to create electrical connections between the layers. These vias are then plated with copper to ensure reliable electrical conductivity and robust mechanical support.
The substrate surface is finished with a high-precision solder mask to protect the underlying circuitry and provide a smooth surface for component mounting. Surface finishes like ENIG or OSP are applied to enhance solderability and corrosion resistance.
After fabrication, the substrates are assembled with electronic components. Rigorous testing is conducted to ensure that the substrates meet all design specifications and performance requirements. This includes electrical testing, thermal cycling, and mechanical stress testing to verify the reliability and durability of the substrates.
The Application Area of IPC Class 3 プリント基板
IPC Class 3 PCBs are used in a wide range of high-performance electronic applications:
In aerospace and defense applications, IPC Class 3 PCBs provide robust performance in harsh environments and under extreme conditions. These substrates are used in various aerospace and defense systems, such as radar, communication, and navigation systems, ensuring reliable operation and long-term durability.
In medical devices, IPC Class 3 PCBs support high-frequency signal processing and reliable operation in various diagnostic and therapeutic equipment. These substrates ensure precise and accurate signal transmission, making them ideal for use in imaging systems, monitoring devices, and surgical instruments.
In automotive applications, IPC Class 3 PCBs are used in various electronic systems, including infotainment, navigation, and advanced driver-assistance systems (ADAS). These substrates offer high reliability and performance, enabling advanced functionalities and efficient operation in automotive environments.
In industrial automation, IPC Class 3 PCBs are used in various control and automation systems. These substrates offer high reliability and performance, enabling advanced functionalities and efficient operation in industrial environments.
In telecommunications, IPC Class 3 PCBs are used in high-frequency and high-speed communication systems, such as base stations, routers, and switches. These substrates provide excellent signal integrity and reliability, ensuring the efficient transmission of data.
What are the Advantages of IPC Class 3 プリント基板?
IPC Class 3 PCBs offer several advantages that make them indispensable in high-performance electronic applications:
High Reliability: Designed to meet the most stringent standards, ensuring continuous and reliable operation in critical applications.
Extended Durability: Built to withstand harsh conditions, such as extreme temperatures, vibration, and humidity.
Enhanced Performance: Provide superior electrical and thermal performance, supporting high-frequency and high-speed applications.
Strict Quality Control: Subjected to rigorous testing and inspection to ensure compliance with the highest standards.
Versatility: Can be used in a wide range of applications, from aerospace and medical devices to automotive and industrial automation.
FAQ
What are the key considerations in designing an IPC Class 3 プリント基板?
Key considerations include material properties, layer stack-up, impedance control, thermal management, and mechanical stability. The design should ensure optimal electrical performance, efficient heat dissipation, and long-term reliability.
How do IPC Class 3 PCBs differ from IPC Class 2 プリント基板?
IPC Class 3 PCBs are designed for higher reliability and performance compared to IPC Class 2 プリント基板. They are subjected to more stringent testing and quality control measures, making them suitable for critical applications where failure is not an option.
What is the typical manufacturing process for IPC Class 3 プリント基板?
The process involves material preparation, layer build-up, drilling and plating, surface finishing, and assembly and testing. Each step is carefully controlled to ensure high quality and performance.
In which applications are IPC Class 3 PCBs commonly used?
These PCBs are commonly used in aerospace and defense, medical devices, 自動車, industrial automation, and telecommunications, supporting high-performance and reliable operation in these fields.