What is FCBGA (ABFの) 基板?
FCBGA (ABFの) Substrate Manufacturer.FCBGA (ABFの) substrate manufacturers specialize in crafting intricate substrates for high-performance integrated circuits. These manufacturers employ cutting-edge technology to fabricate Flip Chip Ball Grid Array (FCBGA) substrates, crucial components in advanced electronics. With a focus on Advanced Organic Substrate materials, they ensure optimal electrical performance, thermal dissipation, and reliability for semiconductor devices. Through meticulous design and precise manufacturing processes, FCBGA (ABFの) substrate manufacturers play a pivotal role in enabling the functionality and efficiency of modern electronic systems, powering industries ranging from telecommunications to computing and beyond.
FCBGA (ABFの) substrate is a representative of packaging technology, and its full name is Flip-Chip Ball Grid Array. In modern electronic devices, FCBGA (ABFの) substrates are widely used for packaging and connecting high-performance chips. Compared with traditional packaging methods, the FCBGA (ABFの) substrate uses a polyimide (ABFの) substrate containing epoxy resin, which has higher performance and reliability.
In an FCBGA (ABFの) substrate, the chip is flip-chip soldered directly to the surface of the substrate. This flip-chip welding technology can effectively reduce the transmission path of electrical signals, reduce signal delay and transmission loss, thereby improving system performance. Compared with traditional chip packaging methods, flip-chip soldering of FCBGA (ABFの) substrates also enables more compact device layouts, saving space and improving integration.
Meanwhile, the FCBGA (ABFの) substrate uses a solder ball grid array to connect the chip to the substrate. This connection method has good electrical performance and mechanical strength, which can ensure reliable connection between the chip and the substrate and improve the long-term stability of the system. The solder ball grid array also has a certain degree of elasticity and can absorb temperature changes and mechanical stress, reducing the risk of device failure due to environmental changes.
全, FCBGA (ABFの) substrate, as an advanced packaging technology, plays an important role in modern electronic devices. Its flip-chip soldering and solder ball grid connection technologies provide reliable packaging and connection solutions for high-performance chips, promoting performance improvement and size reduction of electronic devices. As electronic technology continues to advance, FCBGA (ABFの) substrates will continue to show strong application potential in a variety of high-performance applications.
FCBGA (ABFの) Substrate design Reference Guide.
FCBGA (ABFの) substrate design is a vital part of the development of modern electronic devices. This guide is designed to provide designers with key guidelines and best practices to ensure design reliability, performance, and manufacturability.
Before starting to design an FCBGA (ABFの) substrate, designers should understand and comply with relevant design specifications and standards. These specifications may involve electrical performance, package size, welding specifications, thermal management, 等。, including but not limited to JEDEC standards and IPC specifications.
Substrate layout is critical to circuit performance and reliability. Designers should position chips, devices, and connecting lines to minimize signal interference, electromagnetic interference, and heat build-up. Optimized substrate layout should consider factors such as signal integrity, power distribution, ground routing, heat conduction, 等.
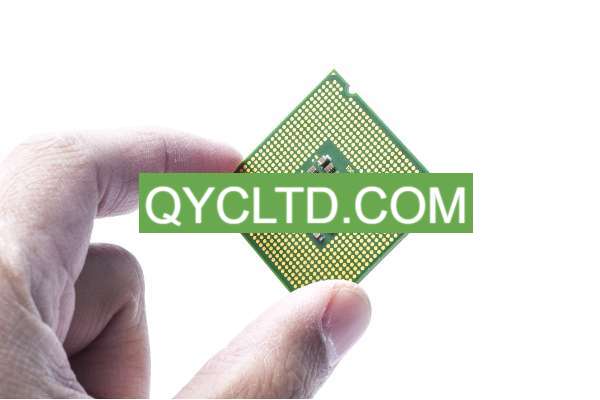
FCBGA (ABFの) 基板メーカー
Flip chip soldering technology is the core packaging technology of FCBGA (ABFの) substrate. Designers should ensure that the welding quality between the chip and the substrate is good to avoid welding defects and open circuits. The selection and application of packaging materials are also key factors, and factors such as thermal expansion coefficient, bonding strength and thermal conductivity should be taken into consideration.
Due to high-density integration and high-power applications, thermal management is critical to FCBGA (ABFの) substrate design. Designers should reasonably design the heat dissipation structure, including radiators, ヒートシンク, heat dissipation channels, 等。, to ensure that the chip operates stably within the normal operating temperature range.
Signal integrity is one of the issues that requires special attention during the design process. Designers should consider issues such as impedance matching, signal propagation delay, crosstalk and reflection of signal transmission lines, and take appropriate measures to ensure signal quality and stability.
During the FCBGA (ABFの) substrate design process, using the appropriate design tools can improve efficiency and accuracy. Commonly used design tools include EDA software, simulation tools, thermal simulation software, 等. Designers should choose appropriate tools and versions based on actual needs.
Designers should consider manufacturing feasibility and cost factors during the design process. Reasonable design layout and material selection can reduce manufacturing costs and reduce the workload of later debugging and correction, while improving product quality and reliability.
FCBGA (ABFの) substrate design is a complex and critical task that requires designers to consider multiple factors and follow strict design specifications and standards. By following the guiding principles and best practices provided in this guide, designers can design FCBGA (ABFの) substrates with high performance, reliability, and manufacturability, driving technological advancement and market competitiveness of electronic devices.
What material is used in FCBGA (ABFの) 基板?
The material of the FCBGA (ABFの) substrate is critical to its performance and application. Its core material, ポリイミド (ABFの), is a high-performance plastic material with excellent mechanical properties and dimensional stability. It also has outstanding electrical properties and is suitable for a wide range of high-frequency and high-speed applications.
まずは, ポリイミド (ABFの), as the core material of FCBGA (ABFの) substrate, has excellent mechanical properties. Its high strength and rigidity enable the substrate to withstand mechanical stress and environmental challenges, ensuring system reliability and stability. Whether it is vibration and shock during transportation, or temperature changes and mechanical loads in the working environment, ABF substrates can provide reliable support and protection.
第二に, ABF substrates have good dimensional stability, which means that the size and shape of the substrates remain stable without deformation or shrinkage under different temperature and humidity conditions. This dimensional stability is critical for packaging high-density electronic devices, ensuring accurate alignment and connection between devices, improving system performance and reliability.
さらに, ABF substrates also perform well in terms of electrical characteristics. Its low dielectric constant and low loss tangent value enable the substrate to have lower signal attenuation and distortion in high-frequency and high-speed signal transmission, ensuring accurate signal transmission and stability. さらに, the ABF substrate has good thermal conductivity, which helps to effectively disperse the heat generated by the device and improve the working stability and reliability of the system.
まとめると, ポリイミド (ABFの), the core material of FCBGA (ABFの) substrate, has become an ideal choice for modern high-performance electronic device packaging due to its excellent mechanical properties, dimensional stability and electrical properties. It can meet the requirements of various high-frequency and high-speed applications and provides a solid foundation and support for the development of the electronics industry.
What size are FCBGA (ABFの) 基板?
FCBGA (ABFの) substrate size often depends on specific application needs and design requirements. This substrate can be manufactured in a variety of size ranges to accommodate different types of chip and device packaging. Generally speaking, FCBGA (ABFの) substrates can be manufactured in square or rectangular shapes and can range in size from a few millimeters to tens of millimeters.
Small FCBGA (ABFの) substrates are suitable for compact electronic devices such as smartphones, tablets and portable consumer electronics. These small substrates enable highly integrated and space-saving designs, making electronic devices thinner, lighter and more portable while maintaining high performance and stability.
一方, large FCBGA (ABFの) substrates are commonly found in high-end servers, network equipment, and industrial control systems. These large substrates can accommodate more chips and connectors, supporting complex circuit designs and high-performance computing needs. They usually have high thermal management capabilities to ensure system stability and reliability.
When manufacturing FCBGA (ABFの) substrates, size selection is also influenced by manufacturing process and cost considerations. Smaller substrate sizes may be easier to process and assemble, but may present challenges in achieving high density connections and heat dissipation. Conversely, larger substrate sizes may require more complex manufacturing equipment and processes, and may be more costly.
全, FCBGA (ABFの) substrates are available in a wide range of sizes and can be customized and optimized for specific application needs. Whether it is a small or large substrate, it can provide stable and reliable connections and performance for various electronic devices, promoting the continuous development and innovation of modern electronic technology.
The Manufacturer Process of FCBGA (ABFの) 基板.
The manufacturing process of FCBGA (ABFの) substrates is a highly sophisticated process involving multiple critical steps, each of which has a significant impact on the quality and performance of the final product. The manufacturing process of FCBGA (ABFの) substrate will be introduced in detail below:
The first step in manufacturing FCBGA (ABFの) substrates is substrate preparation. この段階では, an ABF substrate of appropriate size and material is selected, usually a polyimide resin substrate. These substrates have excellent mechanical properties and dimensional stability and are suitable for packaging processes under high temperatures and pressures.
Next is the chip positioning stage. このステップの内容, the chip is accurately positioned at the designated location on the substrate. This often requires high-precision automated equipment to ensure the correct alignment and positioning of the chip, thereby ensuring the accuracy and reliability of the subsequent soldering process.
Soldering is one of the key steps in the FCBGA (ABFの) substrate manufacturing process. この段階では, heat and pressure are used to solder the interface between the chip and the substrate together. Flip-chip soldering technology is usually used, which means turning the chip upside down so that its pads are directly connected to the substrate pads to achieve higher electrical performance and reliability.
Packaging is the process of assembling the chip and substrate together to form a complete FCBGA (ABFの) package structure. During the packaging process, adhesive or resin encapsulation materials are needed to fix the chip to the substrate and protect the chip from the external environment. Packaging materials usually have good heat resistance and mechanical properties to ensure the stability and reliability of the package.
The last critical step is ball soldering. この段階では, balls of solder are used to connect the chip’s pads to the connection points on the substrate. Ball soldering provides a reliable electrical connection and has good thermal expansion properties to accommodate temperature changes and mechanical stress.
Throughout the manufacturing process, precision equipment and high-temperature environments are required to ensure accuracy and stability at each step. 同時に, strict quality control measures are also indispensable to ensure that the final product meets relevant quality standards and specifications. Through careful execution of these key steps, FCBGA (ABFの) substrates can achieve high-performance, high-reliability packaging structures to meet the needs of various high-end electronic devices.
The Application area of FCBGA (ABFの) 基板.
As an advanced packaging technology, FCBGA (ABFの) substrate has a wide range of applications and plays a key role in high-performance electronic devices. Its excellent electrical performance and reliability make it the packaging technology of choice for a variety of high-frequency and high-speed applications.
最初です, FCBGA (ABFの) substrates are widely used in network communication equipment. Whether used for routers, switches or optical fiber communication equipment, high-performance packaging technology is required to ensure the stability and speed of data transmission. The FCBGA (ABFの) substrate ensures reliable transmission of high-frequency signals through its excellent electrical properties such as low inductance and low impedance, thus meeting the needs of network communication equipment for high-speed data processing.
第二に, computer servers are another important application area. With the rapid development of cloud computing, big data and other technologies, the requirements for server performance and stability are becoming higher and higher. FCBGA (ABFの) substrate plays a key role in server packaging. Its high integration level and excellent thermal performance can ensure the stability of the server when operating under high load. 同時に, its reliable electrical performance also helps to improve the data processing of the server. Speed and efficiency.
さらに, graphics processing unit (GPU) is also one of the important application areas of FCBGA (ABFの) substrate. With the rapid development of games, artificial intelligence and other fields, the requirements for the performance and energy efficiency of graphics processors are getting higher and higher. FCBGA (ABFの) substrate provides a stable and reliable packaging solution for graphics processors through its excellent electrical and thermal properties, ensuring its stable operation in high-load and high-temperature environments.
さらに, embedded systems are also one of the important application areas of FCBGA (ABFの) substrates. Embedded systems are widely used in industrial control, 自動車用電子機器, smart home and other fields, and the requirements for packaging technology are getting higher and higher. FCBGA (ABFの) substrate provides reliable packaging solutions for embedded systems through its high integration, reliability and stability, ensuring the stable operation of the system in various harsh environments.
要は, FCBGA (ABFの) substrate, as an advanced packaging technology, plays an irreplaceable role in high-performance electronic devices. Its wide range of application fields cover network communication equipment, コンピュータサーバ, graphics processors, embedded systems and other fields, providing strong support and guarantee for the development of these fields.
What are the advantages of FCBGA (ABFの) 基板?
FCBGA (ABFの) substrates have multiple advantages over traditional packaging technologies. These advantages not only improve the performance and reliability of electronic systems, but also promote continuous innovation and development of technology.
まずは, FCBGA (ABFの) substrates are known for their high level of integration. Through flip-chip soldering technology, the chip is directly connected to the surface of the substrate, achieving compact design and high-density integration. This design enables electronic systems to be more cost-effective in terms of space consumption while improving system performance, especially in high-end applications such as servers, network communications equipment, and graphics processors.
第二に, the ABF substrate has excellent thermal properties, which is the key to its reliable operation in high-temperature environments. ABF material has good thermal conductivity and can effectively dissipate the heat generated by the chip and maintain the normal operating temperature of the chip, thus improving the stability and reliability of the system. This advantage is particularly prominent in the fields of high-performance computing and data processing.
Third, FCBGA (ABFの) substrates excel in electrical performance. Its excellent electrical characteristics such as low inductance and low impedance make it suitable for high-frequency and high-speed signal transmission. This advantage is particularly important in the fields of modern communications, data transmission and digital signal processing. It can ensure the stability and accuracy of signal transmission and improve the overall performance of the system.
最終的に, FCBGA (ABFの) substrates are highly reliable due to their flip-chip soldering technology and solder ball grid connection method. This connection method ensures a strong connection between the chip and the substrate and can withstand the challenges caused by mechanical stress and temperature changes, thus improving the long-term stability and reliability of the system. For applications that require extremely high system reliability, such as aerospace, medical equipment, and automotive electronics, the advantages of FCBGA (ABFの) substrates are particularly significant.
まとめ, FCBGA (ABFの) substrates are widely recognized for their high integration, excellent thermal performance, excellent electrical performance, and high reliability. With the continuous advancement of electronic technology and the continuous expansion of application fields, FCBGA (ABFの) substrates will continue to play an important role in promoting the continuous improvement of the performance and functionality of electronic devices.
FAQ
What is FCBGA (ABFの) substrate?
FCBGA (ABFの) substrate is an advanced packaging technology that uses Flip-Chip Ball Grid Array to package chips and uses polyimide (ABFの) substrate as a carrier. It achieves high-density, high-performance integrated circuit packaging by flip-chip welding the chip onto the substrate and using a solder ball grid to connect the chip and the substrate.
What are the application areas of FCBGA (ABFの) substrates?
FCBGA (ABFの) substrates are widely used in high-performance electronic devices, including network communication equipment, コンピュータサーバ, graphics processors, embedded systems, 等. Due to its excellent electrical performance and reliability, it has become the packaging technology of choice for a variety of high-frequency and high-speed applications.
What are the advantages of FCBGA (ABFの) substrates over traditional packaging technologies?
Compared with traditional packaging technologies, FCBGA (ABFの) substrates have many advantages, including high integration, excellent thermal performance, excellent electrical performance, and high reliability. It enables higher density integration, better heat dissipation, lower resistance and inductance, and more reliable connections, thereby improving the performance and stability of the overall system.
How to choose a suitable FCBGA (ABFの) substrate?
Selecting a suitable FCBGA (ABFの) substrate requires consideration of many factors, including application requirements, working environment, performance requirements, 等. Focus on factors such as the thermal conductivity performance, electrical characteristics, mechanical strength, and manufacturing process level of the substrate material to ensure that the selected substrate can meet the system design requirements.
What is the manufacturing process of FCBGA (ABFの) substrates?
The manufacturing process of FCBGA (ABFの) substrate includes multiple steps such as substrate preparation, chip positioning, welding, 包装, and ball bonding. The manufacturing process requires sophisticated equipment and a high-temperature environment to ensure reliable connection between the chip and the substrate and packaging quality.