What are Ultrathin BGA Substrates?
Ultrathin BGA Substrates Manufacturer.An ultrathin BGA substrates manufacturer specializes in crafting cutting-edge components for electronic devices. With precision engineering and advanced materials, they produce substrates that are remarkably thin yet durable, catering to the demands of modern technology. These substrates play a crucial role in enabling compact and efficient electronic designs, enhancing performance while minimizing space constraints. Leveraging innovative manufacturing techniques, the company ensures high-quality products that meet the stringent standards of the electronics industry. From smartphones to IoT devices, their ultrathin BGA substrates pave the way for sleeker, more powerful gadgets.
Ultra-thin BGA Substrates are one of the key components in electronic equipment. They use the latest technology and advanced manufacturing processes to reduce the thickness of the circuit board to a minimum, thereby achieving a more compact design. Compared with traditional BGA substrates, ultra-thin BGA substrates are thinner and lighter, and have higher integration and performance advantages.
In the design of ultra-thin BGA substrates, thickness is a key consideration. Traditional BGA substrates usually have to consider the thickness of the board when designing, because their thickness will directly affect the size and weight of the entire electronic device. Ultra-thin BGA substrates use thinner substrate materials and optimized laminate structures to minimize the thickness of the substrate and achieve a more compact design. This thinner design can not only reduce the size and weight of the device, but also improve the heat dissipation performance of the device, making it more suitable for various high-density and high-performance application scenarios.
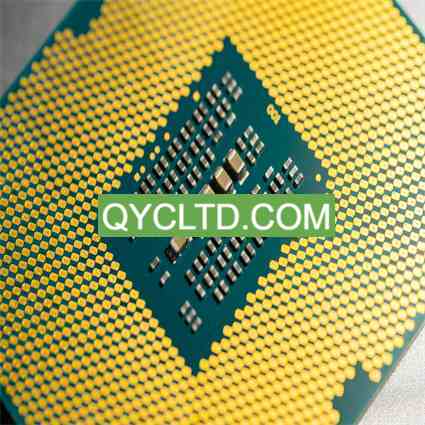
Ultrathin BGA Substrates Manufacturer
Ultra-thin BGA substrates usually use high-performance materials, such as special polyimide (Pi greco) or polytetrafluoroethylene (PTFE), to ensure excellent electrical properties, heat resistance and mechanical strength. Manufacturing ultra-thin BGA substrates requires multiple processes, including film stacking, circuit pattern production, metallization, and so on. Precision manufacturing processes are key to ensuring substrate quality and performance.
Ultra-thin BGA substrates are widely used in the electronics industry, including high-end electronic products such as smartphones, Compresse, and portable medical equipment. Its compact design and excellent performance make it an indispensable component in modern electronic equipment. Compared with traditional substrates, ultra-thin BGA substrates have many advantages such as small size, light weight, and superior performance, providing more flexible and reliable solutions for the design and manufacturing of electronic equipment.
Ultrathin BGA Substrates design Reference Guide.
Ultra-thin BGA substrates are key components in modern electronic devices, and their design must consider many factors to ensure performance and reliability. The following is a brief ultra-thin BGA substrate design reference guide covering key points:
Substrate thickness and laminate structure
The design of ultra-thin BGA substrate must first consider the thickness and lamination structure of the substrate. Since the thickness of the substrate determines the size and weight of the entire device, it is necessary to reduce the thickness of the substrate as much as possible while ensuring electrical performance. Allo stesso tempo, a reasonable laminate structure can improve the strength and stability of the substrate and ensure that it is not easily deformed or broken during use.
Selezione del materiale
Ultra-thin BGA substrates usually use high-performance materials such as polyimide (Pi greco) or polytetrafluoroethylene (PTFE). These materials have excellent electrical properties, heat resistance and chemical stability, making them suitable for various complex working environments. When choosing a material, you also need to consider its compatibility with other components and manufacturing costs.
Line design and impedance control
The circuit design of ultra-thin BGA substrate is crucial, which directly affects the quality and stability of signal transmission. Durante il processo di progettazione, signal lines need to be laid out rationally to avoid cross interference and signal attenuation. Inoltre, for high-speed signal lines, the impedance needs to be strictly controlled to ensure accurate signal transmission and anti-interference capabilities.
Thermal design
Due to the small thickness of ultra-thin BGA substrates, heat dissipation is an issue that requires special attention. Good heat dissipation design can effectively reduce chip temperature and improve device stability and reliability. Durante il processo di progettazione, heat sinks, heat dissipation holes, and so on. can be used to enhance the heat dissipation effect and ensure that it is coordinated with the heat dissipation design of the entire system.
Flexible connection design
Ultra-thin BGA substrates often need to be connected to other components, so elastic connection design is crucial. Durante il processo di progettazione, the location, shape, and material of the connector need to be considered to ensure that the connection is strong and reliable and does not affect the overall performance of the substrate.
The design of ultra-thin BGA substrate is a complex and precise process that requires comprehensive consideration of various factors and reasonable trade-offs. This reference guide aims to provide some guidance for designers to help them design ultra-thin BGA substrates with excellent performance, stability and reliability, and promote the continuous innovation and development of electronic technology.
What material is used in Ultrathin BGA Substrates?
The material of the ultra-thin BGA substrate is an important part of ensuring its performance and reliability. Tipicamente, ultra-thin BGA substrates use high-performance materials, of which special polyimide (Pi greco) e politetrafluoroetilene (PTFE) are two common choices.
Specialty polyimide (Pi greco) is a high-performance engineering plastic with excellent electrical and mechanical properties. It has good heat resistance and chemical stability, and can maintain stable performance over a wide temperature range. This allows the ultra-thin BGA substrate to still perform well in high-temperature environments and is suitable for various demanding application scenarios.
Another commonly used material is polytetrafluoroethylene (PTFE), a high-performance material with a low dielectric constant and low dielectric loss. PTFE material has excellent chemical resistance and high temperature resistance, as well as good mechanical strength. This allows the ultra-thin BGA substrate to perform well in high-frequency circuit design and provide excellent signal transmission performance.
These high-performance materials used in ultra-thin BGA substrates can not only meet the size, weight and performance requirements of electronic devices, but also maintain stable performance under various harsh environmental conditions. Pertanto, choosing the right material is crucial for the design and manufacturing of ultra-thin BGA substrates to ensure that they can perform well in various application scenarios and promote the continuous innovation and development of electronic technology.
What size are Ultrathin BGA Substrates?
Ultra-thin BGA substrates play an important role in electronic devices, and their size is one of the crucial considerations in the design and application process. Although the size of ultra-thin BGA substrates varies depending on application scenarios and needs, they usually follow some common specifications and standards.
Primo, the size of ultra-thin BGA substrates is often limited by required functionality, component density, and device form factor. In today’s electronic products, more and more devices require smaller, lighter, and more compact designs, so the size of ultra-thin BGA substrates is also constantly decreasing.
Generale, the size of ultra-thin BGA substrate can be considered in two aspects: overall size and chip layout area. Overall dimensions refer to the overall dimensions of the substrate, including length, width, and thickness. In practical applications, the external dimensions are usually limited by the device casing, so flexible design is required based on the actual situation.
The chip layout area refers to the area on the substrate used to lay out chips and connection lines. With the advancement of technology, the size of chips is getting smaller and smaller, so the chip layout area of ultra-thin BGA substrates is also constantly decreasing. Allo stesso tempo, in order to achieve higher component density and more complex functions, the chip layout area of ultra-thin BGA substrates often adopts a multi-layer design to improve space utilization and signal transmission efficiency.
Generalmente, the size of ultra-thin BGA substrate depends on many factors, including application scenarios, device appearance, functional requirements, and so on. These factors need to be considered during design and application to achieve optimal performance and reliability. With the continuous advancement of technology and the growing demand for applications, it is believed that the size of ultra-thin BGA substrates will continue to evolve and innovate, bringing more possibilities and opportunities to the development of the electronics industry.
The Manufacturer Process of Ultrathin BGA Substrates.
The manufacturing process of ultra-thin BGA substrates is a complex and precise process involving multiple steps and technologies to ensure that the quality and performance of the substrates meet high standards. Several of the key steps are described in detail below:
Film Stacking
The first step in manufacturing ultra-thin BGA substrates is film stacking. The process involves layering thin films of different materials together to form the basic structure of the substrate. Tipicamente, these films include high-performance materials such as special polyimide (Pi greco) or polytetrafluoroethylene (PTFE). The film stacking process requires a high degree of precision and stability to ensure the thickness and placement of each layer is accurate.
Circuit Patterning
Once the film stacking is complete, the next step is circuit patterning. This step involves patterning circuit traces on the film, typically using techniques such as photolithography or laser cutting. These lines will become the channels connecting various devices and components, so their accuracy and quality are critical to the performance of the entire substrate.
Metallization
After completing the circuit pattern, the next step is metallization. This step involves coating the surface of the substrate with a layer of metal, usually a conductive metal such as copper or silver. The purpose of metallization is to form a conductive path for a circuit and to provide the electrical connections required by the circuit. This requires the use of advanced processes such as chemical deposition and vacuum coating to ensure the uniformity and adhesion of the metal layer.
Throughout the manufacturing process, precision manufacturing processes are key to ensuring substrate quality and performance. Each step requires strict control and monitoring to ensure that the size, thickness, circuit accuracy and other parameters of the substrate meet the design requirements. Deviations in any link may lead to a decrease in substrate performance or an increase in defective products, so quality control during the manufacturing process is crucial.
The manufacturing process of ultra-thin BGA substrates is a highly technology-intensive process that requires sophisticated equipment and professional technicians to complete. Through continuous technological innovation and process improvement, we believe that ultra-thin BGA substrates will play an increasingly important role in the future electronics industry, providing more flexible and reliable solutions for various application scenarios.
The Application area of Ultrathin BGA Substrates.
Ultra-thin BGA substrate is an indispensable key component in today’s high-end electronic products, and its applications cover many fields, including smartphones, Compresse, portable medical equipment, and so on. Its compact design and excellent performance allow it to play an important role in these modern electronic devices.
Innanzitutto, smartphones are one of the important areas for ultra-thin BGA substrate applications. As the size of mobile phones continues to shrink and its functions continue to increase, ultra-thin BGA substrates have become one of the core components that support various functions of mobile phones. Whether it is a processor, memory, or communication module, ultra-thin BGA substrates are required to achieve compact layout and high-speed data transmission.
Secondariamente, tablet computers also widely use ultra-thin BGA substrate technology. As a thin, light and portable electronic device, tablet computers have extremely high requirements on volume and weight. The application of ultra-thin BGA substrate allows the tablet computer to achieve a thinner and lighter design while maintaining excellent performance, improving the user’s carrying and use experience.
Inoltre, portable medical equipment is also one of the important application areas of ultra-thin BGA substrates. In medical devices, size and weight are also critical considerations. The compact design of ultra-thin BGA substrate can make medical equipment more portable, convenient for medical staff to carry and use in different occasions, and also provides stable support for the functions of medical equipment.
Generalmente, ultra-thin BGA substrates play a vital role in high-end electronic products such as smartphones, Compresse, and portable medical equipment. Its compact design and excellent performance provide strong support for the development of modern electronic equipment and promote the continuous innovation and progress of electronic technology. Con il continuo sviluppo della tecnologia, it is believed that ultra-thin BGA substrate will show its broad application prospects in more fields.
What are the advantages of Ultrathin BGA Substrates?
When compared with traditional substrates, ultra-thin BGA substrates exhibit many compelling advantages. These advantages not only make it the first choice component for various electronic devices, but also promote the development of the electronics industry in the direction of thinner, lighter and higher performance.
Innanzitutto, the small size of ultra-thin BGA substrate is one of its most significant advantages. Due to its use of advanced manufacturing processes and materials, the thickness of the ultra-thin BGA substrate is greatly reduced, making the overall size more compact. This compact design makes ultra-thin BGA substrates useful in space-constrained application scenarios, such as smartphones and wearable devices.
Secondariamente, the light weight of ultra-thin BGA substrate is also one of its advantages. Compared with traditional substrates, ultra-thin BGA substrates use lightweight materials and are designed to reduce redundant parts as much as possible, so the overall weight is lighter. This not only helps reduce the overall weight of electronic devices, but also improves portability and comfort.
Inoltre, ultra-thin BGA substrates also perform well in terms of performance. Using advanced materials and manufacturing processes, the ultra-thin BGA substrate has excellent electrical and heat dissipation properties and can meet the needs of various high-performance electronic devices. Its stable and reliable performance makes it the first choice for various key application scenarios, such as aerospace, Attrezzature mediche, and so on.
Generalmente, ultra-thin BGA substrates have become the preferred component of modern electronic equipment due to their small size, light weight, superior performance and many other advantages. With the continuous advancement of electronic technology and the continuous expansion of application scenarios, it is believed that ultra-thin BGA substrates will play a more important role in the future and promote the continued innovation and development of the electronics industry.
Domande frequenti
What is the difference between ultra-thin BGA substrate and traditional BGA substrate?
Ultra-thin BGA substrates are thinner and smaller than traditional BGA substrates, and are suitable for applications with stricter size requirements. Traditional BGA substrates usually have thicker structures and are suitable for electronic devices with generally lower performance requirements.
What is the minimum thickness of ultra-thin BGA substrate?
The thickness of ultra-thin BGA substrates usually ranges from tens to hundreds of microns, depending on specific application requirements. Lower thickness substrates enable more compact designs but may also place higher demands on the manufacturing process.
Is the manufacturing cost of ultra-thin BGA substrate higher?
Because its manufacturing process requires the use of advanced processes and materials, the manufacturing cost of ultra-thin BGA substrates is relatively high, but the performance in high-end electronic products can often offset this cost difference. Inoltre, with the development of technology and the expansion of production scale, the manufacturing cost of ultra-thin BGA substrates is gradually decreasing.
What is the heat dissipation performance of ultra-thin BGA substrate?
The thermal performance of ultra-thin BGA substrates depends on their design and material selection. Although the ultra-thin BGA substrate has a low thickness, it can ensure good heat dissipation performance in high-performance applications through reasonable heat dissipation design and selection of high-quality heat dissipation materials.
What application scenarios are ultra-thin BGA substrates suitable for?
Ultra-thin BGA substrates are suitable for high-end electronic products such as smartphones, Compresse, and portable medical equipment. Due to its compact design and excellent performance, ultra-thin BGA substrates excel in application scenarios with high requirements on size, weight and performance.