Tachyon 100G PCB Manufacturer.Tachyon 100G PCB Manufacturer specializes in producing high-performance printed circuit boards designed for ultra-high-speed applications. Utilizing advanced Tachyon 100G materials, our PCBs offer exceptional signal integrity, bassa perdita, and superior thermal management, making them ideal for cutting-edge telecommunications, data centers, and high-frequency electronics. Our expertise ensures reliable and efficient solutions to meet the most demanding industry standards.
The Tachyon 100G PCB is a cutting-edge high-performance printed circuit board designed to meet the demands of next-generation high-speed communication systems. As the technology landscape evolves, the need for PCB that can support ultra-high data rates and offer superior signal integrity becomes increasingly critical. Tachyon 100G PCBs are engineered to provide exceptional electrical performance, Gestione termica, and reliability, making them an ideal choice for applications such as data centers, telecommunications, and high-speed computing. In this article, we will explore the features, materials, Processo di produzione, applicazioni, and advantages of Tachyon 100G PCBs.
What is a Tachyon 100G PCB?
A Tachyon 100G PCB is a specialized printed circuit board designed to handle data rates up to 100 gigabits per second (Gbps). These PCBs are built using advanced materials and manufacturing techniques to ensure minimal signal loss, low electromagnetic interference (EMI), and robust performance under high-speed conditions. The primary goal of a Tachyon 100G PCB is to provide a stable platform for high-speed signal transmission, ensuring data integrity and reliability in demanding applications.
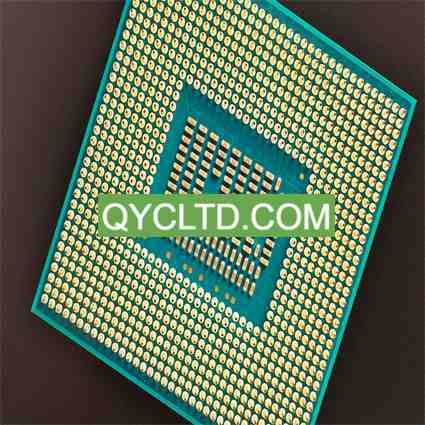
Tachyon 100G PCB Manufacturer
The architecture of a Tachyon 100G PCB typically involves multiple layers of dielectric materials and copper traces. These layers are precisely engineered to achieve optimal signal integrity and electrical performance. Key features of Tachyon 100G PCBs include low dielectric constant (Dk) and low dissipation factor (Df) materials, which help maintain signal speed and reduce energy loss. The PCBs also incorporate advanced thermal management solutions to dissipate heat effectively, preventing performance degradation due to overheating.
Structure of Tachyon 100G PCBs
Tachyon 100G PCBs are characterized by their complex multilayer structure, which is designed to support high-speed data transmission while maintaining signal integrity and reliability. The structure typically includes the following components:
The core layer forms the foundation of the PCB and provides mechanical support and stability. It is usually made from high-performance materials such as low-loss laminates that offer excellent thermal and electrical properties. The core layer is critical for maintaining the structural integrity of the PCB and supporting the overall design.
Prepreg layers are made from resin-coated fiberglass and are used to bond the various layers of the PCB together. These layers provide electrical insulation and mechanical strength, ensuring that the PCB can withstand the stresses of high-speed operation. The prepreg layers also help to maintain the overall thickness and rigidity of the PCB.
The signal layers consist of copper traces that carry electrical signals between different components on the PCB. These layers are designed with precision to ensure minimal signal loss and interference. Advanced techniques such as differential pair routing and controlled impedance are used to optimize the performance of the signal layers.
Ground and power planes are solid copper layers that provide a stable reference voltage for the signal layers and help to distribute power evenly across the PCB. These planes also play a crucial role in reducing EMI and maintaining signal integrity. By providing a continuous ground plane, the PCB can minimize the risk of signal distortion and crosstalk.
The solder mask is a protective layer that covers the copper traces and prevents solder bridges during assembly. It also provides environmental protection and helps to reduce the risk of short circuits. The silkscreen layer is used to print labels and markings on the PCB, aiding in the assembly and troubleshooting process.
Materials Used in Tachyon 100G PCBs
The materials used in Tachyon 100G PCBs are carefully selected to meet the stringent requirements of high-speed data transmission. These materials are chosen for their excellent electrical, thermal, and mechanical properties, ensuring that the PCBs can perform reliably under demanding conditions. Key materials include:
Low-loss laminates are used for the core and prepreg layers to minimize signal attenuation and ensure high-speed performance. These materials have a low dielectric constant (Dk) and low dissipation factor (Df), which help to maintain signal integrity and reduce energy loss. Common low-loss laminates used in Tachyon 100G PCBs include PTFE (Politetrafluoroetilene) and ceramic-filled laminates.
High-quality copper foil is used for the signal layers, ground planes, and power planes. Copper offers excellent electrical conductivity, which is essential for high-speed data transmission. The copper foil is typically applied using advanced techniques such as electroplating and etching to achieve precise and consistent results.
Advanced resins are used in the prepreg layers to provide mechanical strength and electrical insulation. These resins are formulated to withstand the thermal and mechanical stresses associated with high-speed operation. They also offer excellent adhesion properties, ensuring that the layers of the PCB are securely bonded together.
Thermal interface materials (TIMs) are used to enhance the thermal management capabilities of the PCB. These materials help to dissipate heat away from critical components, preventing performance degradation due to overheating. TIMs are typically applied in areas where high-power components are located, such as under integrated circuits (ICs) and power modules.
The selection and combination of these materials are critical for achieving the desired performance and reliability of Tachyon 100G PCBs. Each material contributes to the overall electrical, thermal, and mechanical properties of the PCB, ensuring that it can meet the demands of high-speed data transmission.
The Manufacturing Process of Tachyon 100G PCBs
The manufacturing process of Tachyon 100G PCBs involves several intricate steps, each of which is critical for achieving the high level of precision and performance required for high-speed applications. The process includes:
The first step involves preparing the core materials, prepreg layers, and copper foils. The materials are carefully selected and prepared to ensure that they meet the required specifications for electrical, thermal, and mechanical properties.
The core material is laminated with copper foils to form the initial substrate. Multiple layers of prepreg and copper are then stacked and bonded together using a lamination process. This step requires precise alignment and control to ensure that the layers are properly registered and bonded.
Holes are drilled into the substrate to create vias and through-holes. These holes provide electrical connections between the different layers of the PCB. Advanced drilling techniques, such as laser drilling, are used to achieve the high precision and accuracy required for high-speed PCBs.
The drilled holes are plated with copper to create electrical connections between the layers. This involves depositing a thin layer of copper onto the walls of the holes using electroplating techniques. The plating process must be carefully controlled to ensure uniform coverage and adhesion.
The desired circuit patterns are transferred onto the copper layers using a photolithographic process. This involves applying a photosensitive film (photoresist) to the copper surface and exposing it to ultraviolet (UV) light through a photomask. The exposed areas of the photoresist are developed, leaving behind the circuit pattern. The board is then etched to remove the unwanted copper, leaving only the circuit traces.
A solder mask is applied to the board to protect the circuitry and prevent solder bridges during assembly. The solder mask is typically applied using screen printing or photo-imaging techniques and then cured to harden it.
A surface finish is applied to the exposed copper areas to enhance solderability and protect against oxidation. Common surface finishes include Electroless Nickel Immersion Gold (ENIG), Hot Air Solder Leveling (HASL), and Immersion Silver.
The PCB is assembled with electronic components, such as integrated circuits (ICs), Resistori, Condensatori, and connectors. This step involves placing the components onto the PCB and soldering them in place using reflow soldering or wave soldering techniques.
The final step involves rigorous testing and inspection to ensure the PCB meets all performance and reliability requirements. Electrical testing, visual inspection, and automated optical inspection (AOI) are used to identify any defects or irregularities. Any issues identified during testing are addressed before the PCBs are approved for shipment.
The manufacturing process of Tachyon 100G PCBs requires precise control and expertise to ensure high quality and reliability. Each step is critical for achieving the desired performance and reliability of the final product.
Application Areas of Tachyon 100G PCBs
Tachyon 100G PCBs are used in a wide range of applications across various industries due to their high performance and reliability. Key application areas include:
Tachyon 100G PCBs are widely used in data centers, where high-speed data transmission and reliable performance are critical. These PCBs support the high data rates and low latency required for data center networking equipment, such as switches, routers, and servers.
The telecommunications industry relies on Tachyon 100G PCBs for high-speed networking equipment, come le stazioni base, optical transceivers, and communication systems. These PCBs provide the necessary performance and reliability for handling the high-frequency signals and data rates required in modern telecommunications networks.
In high-speed computing applications, such as supercomputers and high-performance computing (HPC) systems, Tachyon 100G PCBs are used to ensure efficient data transfer and processing. The superior signal integrity and thermal management capabilities of these PCBs are essential for maintaining performance in high-speed computing environments.
Tachyon 100G PCBs are used in aerospace and defense applications, where reliability and performance are critical. These PCBs support high-speed data transmission and robust performance in harsh environments, making them ideal for applications such as radar systems, avionics, and communication equipment.
The automotive industry uses Tachyon 100G PCBs in advanced driver-assistance systems (ADAS), infotainment systems, and vehicle-to-everything (V2X) communication systems. These PCBs provide the necessary performance and reliability for high-speed data transmission in automotive applications.
Advantages of Tachyon 100G PCBs
Tachyon 100G PCBs offer several advantages that make them a preferred choice for high-speed and high-reliability applications. These advantages include:
Tachyon 100G PCBs are designed to minimize signal loss and distortion, ensuring high-speed data transmission with minimal interference. The use of low-loss materials and advanced routing techniques helps maintain signal integrity and reduce electromagnetic interference (EMI).
Effective thermal management is critical for high-speed applications. Tachyon 100G PCBs incorporate advanced thermal interface materials and optimized structures to dissipate heat efficiently, preventing performance degradation due to overheating.
The robust construction and high-quality materials used in Tachyon 100G PCBs ensure reliable performance in demanding applications. These PCBs are designed to withstand thermal cycling, mechanical stress, and harsh environmental conditions, making them suitable for use in critical applications.
Tachyon 100G PCBs are versatile and can be used in a wide range of applications, from data centers and telecommunications to high-speed computing and automotive electronics. The combination of high performance, affidabilità, and scalability makes these PCBs an ideal choice for various industries and applications.
Domande frequenti
What makes Tachyon 100G PCBs suitable for high-speed applications?
Tachyon 100G PCBs are designed with advanced materials and manufacturing techniques that ensure minimal signal loss, low electromagnetic interference (EMI), and robust performance under high-speed conditions. The use of low-loss laminates, precise signal routing, and effective thermal management solutions makes these PCBs ideal for handling data rates up to 100 gigabits per second (Gbps).
Can Tachyon 100G PCBs be used in harsh environments?
Sì, Tachyon 100G PCBs are highly suitable for use in harsh environments. The robust structure, high-quality materials, and advanced manufacturing processes ensure reliable performance under varying environmental conditions, such as high temperatures, humidity, and mechanical stress. This makes them ideal for applications in aerospace, defense, and automotive electronics.
How do Tachyon 100G PCBs ensure effective thermal management?
Tachyon 100G PCBs incorporate advanced thermal interface materials and optimized structures to dissipate heat efficiently. The use of materials with high thermal conductivity and effective heat dissipation techniques ensures that critical components are kept within safe operating temperatures, preventing performance degradation due to overheating.
What industries benefit the most from using Tachyon 100G PCBs?
Industries that benefit the most from using Tachyon 100G PCBs include data centers, telecommunications, high-speed computing, aerospaziale, defense, and automotive electronics. These industries require high-speed data transmission, reliable performance, and robust thermal management, all of which are provided by Tachyon 100G PCBs.