What is Substrate For Chips?
Substrate For Chips Manufacturer.”Substrate for Chips Manufacturer” refers to the crucial foundation material utilized in the production of integrated circuit chips. This specialized substrate serves as the base upon which semiconductor devices are built, providing structural support and electrical connectivity. Engineered with precision, it accommodates intricate circuitry layouts, enabling efficient signal transmission and heat dissipation within the chip. Manufacturers meticulously select and refine substrates to meet exacting standards of durability, conductivity, and compatibility with semiconductor processes. As technology advances, the development of innovative substrate materials remains pivotal, ensuring the continued enhancement of chip performance and functionality across various applications.
Chip Substrati are an indispensable and key component of modern electronic devices. It is a flat substrate that carries various electronic components and provides a platform for connecting these components to build a circuit system. Tipicamente, chip substrates are made of non-conductive materials such as fiberglass-reinforced epoxy (FR-4) or polyimide (Pi greco). These materials have good mechanical strength and electrical insulation properties, and can effectively support and protect electronic components.
The surface of the chip substrate is covered with conductive paths, which are usually made of conductive materials such as copper. These conductive paths are precisely arranged and connected to form various parts of the circuit, thereby achieving electrical connections between electronic components. These paths carry not only current, but also signals and data, enabling electronic devices to function.
On the chip substrate, electronic components such as transistors, Condensatori, Resistori, and so on. are mounted and connected together to form a complete circuit system. These components are connected to each other through conductive paths and jointly implement various functions of electronic devices, such as signal processing, power control, data storage, and so on.
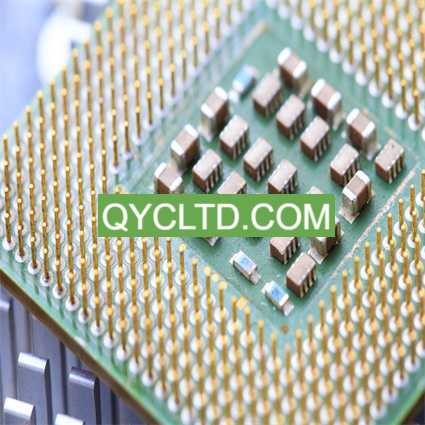
Substrate For Chips Manufacturer
Generalmente, the chip substrate serves as the skeleton of the electronic device, carrying various electronic components and providing a platform to connect and support these components. Its design and manufacturing are crucial and directly affect the performance and reliability of electronic equipment. Through continuous technological innovation and improvement of manufacturing processes, chip substrates will continue to play an important role in promoting the continuous development and progress of electronic technology.
Substrate For Chips design Reference Guide.
In the field of modern electronics, the design of chip substrates is a critical step to ensure circuit performance and reliability. This guide will cover key points and best practices in chip substrate design to ensure design robustness and manufacturability.
Before starting to design the chip substrate, you first need to clarify the functional requirements and performance indicators of the design. This includes determining the functional modules of the circuit, signal transmission requirements, power consumption limits, and so on.
PCB layout design is one of the key steps in chip substrate design. In layout design, the layout relationship between various components needs to be considered to ensure the compactness and signal integrity of the circuit. Reasonable layout design can reduce signal interference and improve circuit stability.
Durante il processo di progettazione, performing signal integrity analysis is an important step to ensure circuit performance. Through simulation and analysis tools, parameters such as signal transmission delay and waveform distortion can be evaluated, and layout and circuit design can be optimized to improve signal quality and reliability.
Electromagnetic compatibility design is one of the key factors to ensure that the circuit will not interfere with the surrounding environment or be subject to external interference when working. Through reasonable layout design, Pianificazione del filo di terra, shielding design and other measures, electromagnetic interference can be effectively reduced and the stability and reliability of the circuit improved.
Thermal management design is particularly important for high-power chips or applications in high-temperature environments. Through reasonable heat dissipation design, heat sink design and other measures, the chip operating temperature can be effectively reduced and the reliability and life of the circuit can be improved.
Selecting the appropriate substrate material is critical to chip substrate design. Different materials have different electrical, mechanical and cost characteristics and need to be selected based on specific application requirements. Commonly used substrate materials include FR-4, Polyimide (Pi greco), aluminum oxide (Alumina), and so on.
Durante il processo di progettazione, manufacturing feasibility and cost factors need to be considered. Reasonable design can reduce manufacturing costs and improve production efficiency while ensuring product quality and reliability.
Chip substrate design is one of the key links in the development process of modern electronic products. By following best practices and design principles, circuit performance and reliability can be ensured, driving continuous progress and innovation in electronic technology.
What material is used in Substrate For Chips?
Material selection for chip substrates is critical to the performance and reliability of electronic products. In different application scenarios, a variety of materials can be used to meet specific requirements.
Silicon substrate is one of the main materials for manufacturing integrated circuits. It has excellent electrical properties and mechanical stability and is suitable for most chip manufacturing processes. Silicon substrates are widely used in fields such as microprocessors, memories, and various sensors.
Glass substrates have excellent flatness and surface quality and are suitable for chip manufacturing that require high-precision processing and packaging. It has important applications in fields such as optical sensors and display driver chips.
Ceramic substrates have good thermal conductivity and insulation properties and are suitable for the manufacture of high-power chips and radio frequency circuits. It plays an important role in fields such as high-frequency communications, power amplifiers, and microwave devices.
Polymer substrates are commonly used in the manufacture of flexible electronic devices and micro-packaged chips. It is lightweight, flexible and corrosion-resistant, and is suitable for fields such as flexible displays, wearable devices and medical devices.
Metal substrates have good heat dissipation performance and mechanical strength, and are suitable for the manufacture of high-power chips and high-power electronic modules. It is widely used in fields such as automotive electronics, power modules and LED lighting.
Choosing the appropriate chip substrate material depends on the circuit requirements and application scenarios. Different materials have their own advantages and disadvantages, and factors such as electrical performance, Resistenza meccanica, thermal conductivity, and cost need to be comprehensively considered during the design process to ensure the performance and reliability of the final product. Through continuous technological innovation and material research and development, chip substrates will continue to play an important role in promoting the development and progress of the electronics industry.
What size are Substrate For Chips?
Chip substrate sizes vary depending on their application and design needs. Generale, chip substrates can be very small to micro size or very large to industrial size, depending on factors such as the type and number of chips carried and the size constraints of the device.
In micro applications, such as smartphones and wearable devices, chip substrates are usually very small. This is because these devices require compact designs to accommodate other hardware components and provide high performance within limited space. Pertanto, microchip substrates may only be a few millimeters or centimeters in size to accommodate the miniaturization trend of devices.
In contrast, in some industrial and communications equipment, the chip substrate may be larger. These devices typically require more processing power and connectivity options, and therefore more chips and electronic components. Pertanto, the chip substrate may be larger, perhaps tens of centimeters or even larger, to accommodate more chips and connections.
Inoltre, the size of the chip substrate is also limited by the manufacturing process and technology. As manufacturing technology advances, manufacturers can produce smaller, denser chip substrates that can pack more functionality and performance into the same space.
Generalmente, the size of chip substrates is diverse and can be adjusted according to the requirements of specific applications and the design of the device. Regardless of size, chip substrates play a key role in providing stable electrical connections and support for electronic devices, driving the development and innovation of modern technology.
The Manufacturer Process of Substrate For Chips.
The manufacturing process of chip substrates is a complex and precise process involving multiple critical steps to ensure the quality and performance of the final product. The following is the basic process of chip substrate manufacturing:
The first step in the manufacturing process is substrate preparation. Typically a substrate made of fiberglass reinforced epoxy (FR-4) or other specific materials is used. These substrates are cut and cleaned to ensure a flat and clean surface ready for subsequent process steps.
Forming conductive paths on the substrate surface is one of the key steps in manufacturing chip substrates. This is usually done by covering the surface of the substrate with a layer of copper foil and using photolithography and etching techniques to define the circuit pattern. Photolithography technology uses photosensitive materials and masks to transfer circuit patterns to copper foil, while etching technology removes unnecessary parts of the copper foil through chemical etching to form the required conductive paths.
After completing the conductive path, next comes the assembly of the components. This involves precisely mounting various electronic components (come le patatine fritte, Resistori, Condensatori, and so on.) on a substrate and connecting them to conductive paths using soldering or other connection techniques. Accurate installation and connection of components are critical steps in ensuring circuit function and performance.
The last important step is quality testing. In questa fase, the manufacturer performs various tests on the chip substrate to ensure that it meets specifications and has good electrical performance. These tests can include visual inspection, connectivity testing, withstand voltage testing, and so on. to ensure that the chip substrate can work reliably in actual use.
Throughout the manufacturing process, advanced manufacturing technology plays a key role. Automated equipment and precision machining processes can ensure the precision and consistency of circuits while improving production efficiency and throughput. Allo stesso tempo, continued R&D and innovation also promote the continuous advancement of chip substrate manufacturing technology, providing the electronics industry with more reliable and higher-performance products.
The Application area of Substrate For Chips.
As an important part of the electronics industry, chip substrates are widely used in various electronic products, providing key support for the function realization and performance improvement of these devices. From consumer electronics to high-end communication equipment, to medical equipment and industrial control systems, the application of chip substrates covers various fields, promoting the continuous development and innovation of electronic technology.
Nel campo dell'elettronica di consumo, come gli smartphone, Compresse, TVs, ed elettrodomestici, chip substrates carry various chips and components to realize complex functions of circuits. Through precision design and manufacturing, chip substrates play a key role in these devices, providing users with a high-performance and reliable electronic experience.
Nel campo delle comunicazioni, chip substrates are widely used in key equipment such as base station equipment, network routers, and optical fiber communication systems. They carry complex communication circuits, support data transmission and network connections, and have made important contributions to the development and popularization of modern communication technology.
In the field of medical devices, chip substrates play a key role in various medical devices, such as pacemakers, medical monitoring equipment, medical imaging systems, and so on. These devices are critical for patient diagnosis, treatment, and monitoring, and the chip substrate provides them with stable electrical connections and efficient data processing capabilities, ensuring device reliability and performance.
In the field of industrial control systems, chip substrates are used in various automation equipment, robotic systems, industrial sensors, and so on. They carry control circuits and data processing units, realize the automation and intelligence of factory production, and improve production efficiency and product quality.
Generalmente, chip substrates, as the core component of electronic products, play an important role in consumer electronics, communication equipment, Attrezzature mediche, and industrial control systems. Through continuous technological innovation and improvement of manufacturing processes, chip substrates will continue to promote the development and innovation of electronic technology and bring more convenience and progress to human society.
What are the advantages of Substrate For Chips?
As an indispensable component of electronic equipment, chip substrates have many significant advantages, making them the core pillar of modern electronic technology.
Provide stable electrical connections: The chip substrate connects various electronic components together through conductive paths to ensure the stability and reliability of the circuit. This stable connection method can not only transmit current and signals, but also provide good electrical performance and reduce circuit noise and distortion.
Support high-density integration: As electronic devices continue to shrink in size and enhance functionality, chip substrates can achieve higher-density integration, allowing more functions and components to be implemented in a limited space. This high-density integrated design not only improves the performance of the device, but also reduces the size and weight of the device, meeting the needs of modern electronic products for miniaturization and lightweight.
Provide mechanical support and protection: The chip substrate not only functions as an electrical connection, but also provides mechanical support and protection for electronic components. With appropriate substrate materials and design structures, chip substrates can effectively absorb external shock and vibration and protect electronic components from damage.
Multi-layer structures can be realized: The chip substrate can realize single-layer, double-layer or even multi-layer structures, allowing the design and implementation of complex circuits. The multi-layer structure achieves higher circuit integration and complexity by arranging conductive and insulating layers between different layers, while reducing circuit noise and interference.
Provide high temperature and environmental adaptability: Choosing the appropriate substrate material can make the chip substrate have good high temperature stability and environmental adaptability. This allows the chip substrate to operate stably in various harsh working environments, come l'alta temperatura, high humidity, and high pressure.
Generalmente, come componente principale delle apparecchiature elettroniche, chip substrates not only provide stable electrical connections and support, but also have the advantages of high-density integration, mechanical protection, multi-layer structure and high-temperature environmental adaptability, promoting modern electronic technology development and innovation.
Domande frequenti
What is the difference between chip substrate and ordinary circuit board?
Chip substrate generally refers to a special type of circuit board used to carry chips and other integrated circuits. Compared with ordinary circuit boards, chip substrates usually have higher density and more complex layout to support the high integration and high-speed operation of integrated circuits.
How to choose a suitable substrate material?
Several factors need to be considered when selecting a substrate material, including operating environment, Requisiti di temperatura, frequency characteristics, e costo. Per esempio, for high-temperature environments and high-frequency applications, high-performance materials such as polyimide (Pi greco) may be more suitable; while for general applications, FR-4 glass fiber reinforced epoxy resin may be a more economical choice.
What are the key steps in the manufacturing process of chip substrates?
The manufacturing process of chip substrates includes steps such as substrate pre-processing, printed circuit patterning, metallization, component mounting and final testing. Among them, printed circuit patterning and metallization are critical steps that directly affect the quality and performance of the circuit.
What is the role of chip substrates in electronic products?
Chip substrates play a role in connecting various electronic components in electronic products, come le patatine fritte, Resistori, Condensatori, and so on. They provide stable electrical connections and mechanical support, ensuring proper circuit operation and reliability.
How to solve the environmental problems of chip substrates?
The manufacturing and processing of chip substrates may involve some environmental issues, such as wastewater treatment, exhaust emissions, and waste disposal. By adopting environmentally friendly materials, optimizing production processes, and implementing recycling and other measures, the impact on the environment can be effectively reduced and sustainable development achieved.