What is PBGA Package Substrate?
PBGA Package Substrate Manufacturer.A leading manufacturer in the industry, specializing in PBGA package substrate production. Renowned for precision engineering and cutting-edge technology, they dominate the market with their superior quality and reliability. With a commitment to innovation and customer satisfaction, they deliver substrates tailored to meet the stringent demands of modern electronics. Their state-of-the-art facilities ensure seamless production processes, guaranteeing consistent excellence in every substrate they produce. Trusted by top-tier electronics companies worldwide, they continue to set the standard for PBGA package substrate manufacturing, driving forward technological advancements in the field.
PBGA Substrato della confezione represents the advancement of electronic packaging technology and plays an important role in modern electronic products. PBGA Package Substrate is a high-density packaging technology that integrates ball grid array packaging. By integrating devices directly on the PCB, it provides a more compact and reliable connection solution for electronic devices, while bringing higher integration and performance.
The advantage of this packaging form is that it not only provides higher connection density, but also greatly reduces the delay and loss of signal transmission. Through the ball grid array, a large number of connections can be established between the device and the circuit board, effectively improving the efficiency and reliability of signal transmission. Compared with traditional packaging technology, PBGA Package Substrate can achieve a more compact layout, significantly reducing the size and weight of electronic devices while also improving overall performance.
Another advantage of PBGA Package Substrate is its reliability and stability. By integrating the device directly with the PCB, soldering issues and connection instability common in traditional packaging are avoided. This integrated design makes the connection between the device and the circuit board stronger and can better resist interference and vibration from the external environment, thus improving the reliability and stability of the entire system.
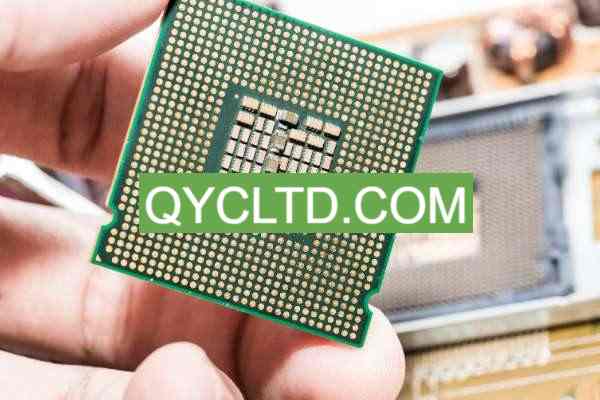
PBGA Package Substrate Manufacturer
In modern electronic products, PBGA Package Substrate has been widely used. Whether it is smartphones, Compresse, industrial control equipment, or medical instruments, you can see it. Its high density and high performance make it an indispensable part of modern electronic products, injecting new vitality into the development of the electronics industry.
Riassumendo, PBGA Package Substrate, as an innovative packaging technology, has brought huge impetus to the development of electronic products. By providing more compact and reliable connection solutions, as well as higher integration and performance, it is changing our understanding of electronic products and pushing the electronics industry to new heights.
PBGA Package Substrate design Reference Guide.
When designing a PBGA Package Substrate, several key factors need to be considered to ensure that the final design can meet performance and reliability requirements. Here are some key design guidelines covering device size, layout, routing, and thermal management:
Device size: Primo, determine the overall size of the PBGA Package Substrate based on the required functions and performance. Size selection should take into account device integration, thermal requirements, and final product size constraints.
Arrangement and wiring: When designing the PBGA Package Substrate, it is necessary to arrange the arrangement and wiring of the devices reasonably. Reasonable layout can minimize the length of the signal transmission path, reduce signal transmission delay and power consumption, and reduce the possibility of signal crosstalk and electromagnetic interference.
Signal transmission optimization: Special attention should be paid to the design of signal transmission lines during the design process. By adopting appropriate wiring techniques, ground and power plane design, and impedance matching, signal transmission quality can be optimized and system stability and reliability improved.
Gestione termica: Since PBGA Package Substrate usually integrates a large number of devices, thermal management is crucial. The power consumption, heat dissipation structure and heat dissipation material selection of the device need to be taken into consideration during the design process to ensure that the system can effectively dissipate heat under normal working conditions and prevent performance degradation or damage caused by overheating.
Electromagnetic interference control: Measures should be taken during the design process to reduce the impact of electromagnetic interference. This includes good isolation and shielding of signal lines, proper grounding design, and avoiding cross-interference between signal lines and high-power components.
Riassumendo, designing PBGA Package Substrate requires comprehensive consideration of device size, arrangement, wiring, and thermal management. Proper design can optimize signal transmission, reduce electromagnetic interference, and improve system stability and reliability. By following these design guidelines, you can ensure that PBGA Package Substrate provides excellent performance and reliability in various application scenarios.
What material is used in PBGA Package Substrate?
PBGA Package Substrate is a key packaging technology whose performance and reliability are closely related to the materials used. Normally, PBGA Package Substrate uses high-quality substrate materials, mainly including the following:
FR-4 (Flame Retardant-4): FR-4 is a common glass fiber reinforced epoxy resin substrate material, which is widely used in electronic manufacturing. It has good mechanical strength, heat resistance and chemical corrosion resistance, and can operate stably in complex working environments. FR-4 substrate is widely used in PBGA packaging substrates to provide reliable support and connection for electronic devices.
Polyimide (Pi greco, Polyimide): Polyimide is a high-performance engineering plastic with excellent heat resistance, mechanical properties and chemical stability. Due to its low dielectric constant and low dielectric loss, polyimide substrates are often used in high-frequency and high-speed circuit designs. In PBGA Package Substrate, the polyimide substrate can effectively improve the speed and quality of signal transmission while reducing the heat dissipation requirements of the circuit board.
In addition to the two common substrate materials mentioned above, there are also other materials, come il PTFE (Politetrafluoroetilene), RO4000 series (high-frequency low-loss glass fiber reinforced PTFE), metal substrates, and so on., which are also used in specific in application scenarios. Selecting the appropriate substrate material is critical to the performance and reliability of PBGA Package Substrate.
Generalmente, the substrate material used in PBGA Package Substrate has excellent electrical, thermal and mechanical properties and can meet the needs of complex electronic systems. Through careful selection and design, these materials provide stable and reliable support for electronic devices and promote the development and progress of modern electronic technology.
What size are PBGA Package Substrate?
The size of the PBGA Package Substrate is customized according to the application needs, which makes it flexible to adapt to the requirements of various electronic devices. Different application scenarios may require PBGA packaging substrates of different sizes to meet design compactness, performance requirements, and heat dissipation needs.
Nei moderni dispositivi elettronici, more and more products require integrating more functions and components in a limited space. Pertanto, PBGA packaging substrates often have smaller dimensions to provide higher integration in space-constrained environments. Compared with traditional packaging technology, PBGA Package Substrate can achieve more functions in a relatively small size, thus bringing greater flexibility and innovation space to the design of electronic products.
Inoltre, the packaging form of PBGA Package Substrate also makes it easier to integrate with other components, thereby achieving a compact design of the overall system. This packaging method effectively reduces the overall size of the electronic system by connecting the device to the bottom of the printed circuit board, while improving system reliability and performance.
In addition to flexible customization of size, PBGA packaging substrates can also achieve higher integration by optimizing wiring and device arrangement. This means that more devices and functional modules can be integrated on the same size substrate, thereby improving the performance and functionality of the overall system.
Grembiule, the flexible size customization of PBGA Package Substrate brings significant advantages to the design of electronic products. By sizing to specific application needs, more compact, higher performance, more reliable electronic system designs can be achieved to meet evolving market demands.
The Manufacturing Process of PBGA Package Substrate.
The manufacturing process of PBGA Package Substrate is a complex and precise process involving multiple critical steps to ensure the quality and performance of the final product. The following are its main manufacturing processes:
Substrate production: The first step in manufacturing PBGA Package Substrate is to prepare the substrate. Tipicamente, the substrate is made of high-quality base materials such as FR-4 or polyimide (Pi greco). The fabrication of the substrate includes steps such as cutting, surface treatment and patterning chemical processing to ensure that the substrate has the required size, surface properties and geometry.
Device assembly: After the substrate production is completed, the next step is the device assembly stage. This step involves precisely mounting various electronic devices (come le patatine fritte, Condensatori, Resistori, and so on.) into predetermined locations on the substrate. This is often done through automated robotic systems to ensure assembly accuracy and efficiency.
Soldering: Once all components are accurately mounted on the substrate, the next step is soldering. Soldering is a critical step in joining the device to the substrate. This can be achieved through various soldering techniques, such as surface mount technology (SMT) or hot air fusion (reflow) soldering. The quality of welding directly affects the stability and reliability of the final product.
Inspection and testing: After completing the welding, the PBGA Package Substrate will undergo strict inspection and testing. This includes visual inspection, X-ray inspection, Collaudo elettrico, and so on. These tests are designed to ensure that each device is connected correctly and meets specifications.
Encapsulation and Protection: Finalmente, the completed PBGA Package Substrate will be encapsulated and protected. This can be achieved, for example, by coating with a protective resin or by installing a casing to protect it from external factors such as mechanical damage, dust and moisture.
Through the above advanced manufacturing technology, PBGA Package Substrate can ensure high-quality packaging, thereby ensuring the stability and reliability of electronic equipment. The precision and craftsmanship of this manufacturing process are crucial to the performance of modern electronic products and are one of the keys to the success of PBGA Package Substrate in the market.
The Application area of PBGA Package Substrate.
PBGA Package Substrate (PBGA package substrate), as a highly integrated packaging technology, is widely used and indispensable in modern electronic products. Its high density, high reliability and excellent thermal management performance make it the preferred packaging solution for industries such as communication equipment, elaboratori, industrial control equipment, and medical equipment.
Nel campo delle apparecchiature di comunicazione, PBGA Package Substrate is widely used in mobile communication base stations, network routers, optical fiber communication equipment, and so on. These devices usually require highly integrated electronic components and have extremely high requirements for the stability and reliability of signal transmission. PBGA packaging substrates can meet these needs and provide excellent performance.
Nel campo informatico, PBGA Package Substrate is used for packaging core components such as CPU, GPU, and motherboard. With the continuous development of computer technology, the requirements for packaging technology are becoming higher and higher. Through its highly integrated characteristics, PBGA packaging substrate enables computer hardware to perform better and have a smaller size.
Industrial control equipment is another important application field. PBGA Package Substrate is widely used in PLC (programmable logic controller), sensori, industrial robots and other equipment. These equipment usually need to operate stably for a long time. The high reliability and stability of PBGA packaging substrate make it an ideal choice for industrial control equipment.
Nel campo delle apparecchiature mediche, PBGA Package Substrate also plays an important role. Per esempio, high-precision equipment such as medical imaging equipment and medical monitoring instruments require stable signal transmission and reliable performance. PBGA packaging substrates can meet these needs and play an important role in medical diagnosis and treatment.
Insomma, the high density, high integration and reliability of PBGA Package Substrate make it the preferred packaging technology in communications, elaboratori, industrial control, medical and other fields. With the continuous advancement of electronic technology, PBGA packaging substrates will continue to play an important role in various fields and promote the development of the entire electronics industry.
What are the advantages of PBGA Package Substrate?
In modern electronics manufacturing, PBGA Package Substrate (PBGA package substrate), as an advanced packaging technology, has many advantages compared with traditional packaging technology. These advantages make it perform well in various application scenarios.
Innanzitutto, the size of PBGA Package Substrate is relatively small. Due to its ball grid array packaging, more devices can be integrated into a smaller space, thereby achieving streamlined design of electronic products. This is particularly important for devices that require a high degree of integration and compact size, such as mobile devices such as smartphones and tablets, as well as application scenarios that require space saving such as medical equipment and industrial control equipment.
Secondariamente, PBGA Package Substrate has stable performance. Due to the advancement of packaging technology and the precision of the manufacturing process, PBGA packaging substrates can provide stable electrical performance and ensure the accuracy and reliability of signal transmission. This makes it an ideal choice for high-performance electronic products that meet users’ high requirements for stability and performance.
Inoltre, PBGA Package Substrate also has strong anti-interference capabilities. Due to the ball grid array connection method, the PBGA packaging substrate is more stable in the face of environmental factors such as vibration, temperature changes, and electromagnetic interference compared with traditional soldering connections. This makes its application in harsh environments more reliable and ensures long-term stable operation of electronic equipment.
Generalmente, PBGA Package Substrate, as an advanced packaging technology, has obvious advantages in terms of volume, performance stability and anti-interference ability. These advantages make it an indispensable part of modern electronics manufacturing and can play an excellent role in various application scenarios. Con il continuo sviluppo e innovazione della tecnologia, I believe that PBGA Package Substrate will play a more important role in the design and manufacturing of future electronic products.
Domande frequenti
How does PBGA Package Substrate solve thermal management problems?
PBGA Package Substrate usually takes thermal management into consideration when designing and uses appropriate heat dissipation design, heat conduction materials and heat dissipation structures to ensure that the device can effectively dissipate heat during operation and maintain a stable operating temperature.
What ambient temperature ranges is PBGA Package Substrate suitable for?
The applicable temperature range of PBGA Package Substrate usually depends on the materials and processes used, and can generally cover various working environments from normal temperature to high temperature. The specific applicable temperature range can be customized according to actual needs.
How reliable is PBGA Package Substrate?
PBGA Package Substrate has undergone strict design verification and production testing and has high reliability. It adopts advanced manufacturing technology and high-quality materials to meet various harsh working environment requirements and ensure long-term stable operation of the equipment.
What are the advantages of PBGA Package Substrate in terms of electromagnetic compatibility?
Because PBGA Package Substrate uses a high-density wiring design and excellent packaging materials, it has strong anti-electromagnetic interference capabilities. This enables it to better maintain signal stability in complex electronic systems and improves the overall performance of the system.
What are the application cases of PBGA Package Substrate in electronic product design?
PBGA Package Substrate is widely used in mobile phones, Compresse, laptops, industrial control equipment, apparecchiature mediche e altri campi. Per esempio, in mobile phones, PBGA Package Substrate is used to package core chips such as CPUs and GPUs, achieving the dual goals of high performance and miniaturization.