What is Cavity Package Substrate?
Cavity Package Substrate Manufacturer.A Cavity Package Substrate Manufacturer specializes in crafting intricate substrates for electronic components, meticulously engineered to house delicate microchips securely. These substrates feature precisely carved hollow spaces, or cavities, tailored to snugly accommodate various electronic elements. Employing advanced fabrication techniques, they ensure optimal conductivity, Gestione termica, and durability. From initial design to final production, these manufacturers uphold stringent quality standards, catering to diverse industry needs. Their expertise lies in crafting bespoke solutions, integrating cutting-edge materials and innovative designs to meet the evolving demands of modern electronics, guaranteeing reliability and performance excellence.
Cavity Package Substrate (CPS) is a specially designed PCB (Printed Circuit Board). Its unique feature is that one or more cavities are formed on the PCB board specifically to accommodate IC packages (Integrated Circuit Package). , integrated circuit packaging). Compared with traditional flat PCB design, CPS’s cavity design provides a more superior environment for IC packaging.
Innanzitutto, one of the design goals of CPS is to improve the heat dissipation effect. Due to the increasing power consumption of integrated circuits in modern electronic devices, heat dissipation has become an important challenge. CPS effectively increases the heat dissipation surface area and improves heat dissipation efficiency through the design of the cavity. This is critical to keeping the temperature of the integrated circuit within a safe range, extending its service life and improving performance stability.
Secondariamente, CPS can also effectively reduce electromagnetic interference. In high-density electronic equipment, electromagnetic interference between circuits may cause signal distortion or unstable equipment operation. By encapsulating ICs in cavities, CPS effectively isolates electromagnetic interference between circuits, improves the anti-interference ability of the equipment, and ensures the stability and reliability of signal transmission.
Inoltre, CPS can provide higher performance and reliability. By precisely controlling the size and shape of the cavity in the design, the needs of specific application scenarios can be better met, providing higher integration and functionality. Allo stesso tempo, due to the introduction of cavity design, CPS can also reduce the overall thickness of the circuit board, making the device thinner, lighter and more portable, and easier to maintain and upgrade.
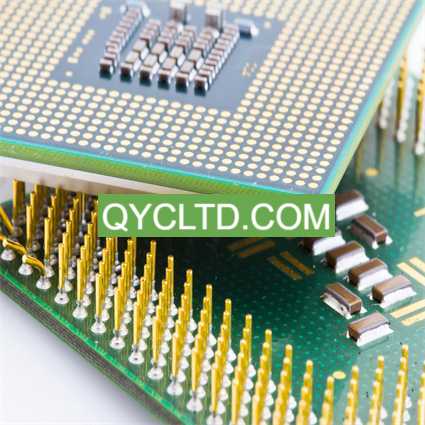
Pacchetto cavità Substrato Fornitore
Generalmente, Cavity Package Substrate (CPS), as an innovative PCB design solution, can not only improve heat dissipation and reduce electromagnetic interference, but also provide higher performance and reliability. Its unique cavity design provides a superior environment for IC packaging, brings more possibilities to the design and manufacturing of electronic devices, and will play an important role in the future electronics field.
Cavity Package Substrate design Reference Guide.
When designing Cavity Package Substrate (CPS), a range of factors need to be carefully considered to ensure its performance and reliability. Here is a design reference guide for some key factors:
The location and size of the cavity: The location and size of the cavity directly affect the layout and heat dissipation effect of the IC package. Tipicamente, the cavity should be located in the center of the PCB to ensure package stability and balance. Inoltre, the size of the cavity should be accurately calculated based on the size and height of the package to ensure that the IC package can be fully accommodated within it and there is enough space for heat dissipation.
Circuit layout: In the design of CPS, circuit layout is crucial, as it directly affects the stability and electromagnetic compatibility of signal transmission. Optimized circuit layout should consider the length and routing of signal lines to minimize signal crosstalk and electromagnetic interference.
Gestione termica: Since CPS are often used in high power applications, good thermal management is critical. Materials with excellent thermal conductivity, such as copper substrates or metal substrates, need to be considered during design to improve heat dissipation. Inoltre, you can consider adding accessories such as radiators or heat pipes to further improve thermal management capabilities.
Selezione del materiale: In the design of CPS, choosing the right materials is crucial to ensure performance and reliability. In addition to materials with good thermal conductivity, factors such as mechanical strength, temperature resistance, and corrosion resistance of the material also need to be considered.
Packaging type and process requirements: Different packaging types may have different requirements for the design and manufacturing of CPS. Pertanto, customized designs are required based on specific package types and process requirements to ensure CPS compatibility and reliability.
Riassumendo, designing CPS requires comprehensive consideration of multiple factors such as the location and size of the cavity, circuit layout, Gestione termica, Selezione del materiale, packaging type and process requirements. The detailed design reference guide can help engineers better grasp these key factors to design CPS products with excellent performance, Affidabilità e stabilità.
What material is used in Cavity Package Substrate?
In the design and manufacturing of Cavity Package Substrate (CPS), material selection is a crucial part. CPS usually uses materials with high thermal conductivity to ensure good heat dissipation and electromagnetic shielding effects, thereby improving PCB performance and reliability.
Innanzitutto, metal substrate is one of the common CPS materials. Metal substrates are usually made of metal materials such as aluminum or copper, which have excellent thermal conductivity and mechanical strength. By forming cavities and circuit layouts on metal substrates, more efficient heat dissipation can be achieved, thereby reducing the operating temperature of electronic components and improving system performance and reliability. Inoltre, the metal substrate also has a good electromagnetic shielding effect, which can effectively reduce the impact of electromagnetic interference on the circuit and improve the anti-interference ability of the system.
Another commonly used CPS material is ceramic substrate. Ceramic substrates have excellent thermal conductivity, dimensional stability and chemical stability, and are suitable for applications in high temperature and high frequency environments. Because the ceramic substrate has a high dielectric constant and low loss, it can achieve higher signal transmission rates and lower signal attenuation, and is suitable for scenarios that require high-frequency signal processing. Inoltre, ceramic substrates also have good corrosion resistance and mechanical strength, making them suitable for harsh working environments.
Generalmente, whether it is a metal substrate or a ceramic substrate, they have excellent thermal conductivity and electromagnetic shielding effects, and can meet the needs of CPS in high-performance electronic products. Nella selezione dei materiali, comprehensive considerations need to be made based on specific application scenarios and performance requirements to ensure that the CPS design can achieve optimal performance and reliability.
What size are Cavity Package Substrate?
The size of the CPS is one of the crucial considerations in the design process. It directly affects the adaptability, heat dissipation effect and overall performance of the IC package. The determination of the size needs to fully take into account the requirements and actual conditions of the specific application, and be customized based on the size and quantity of the IC package.
Primo, the size of the CPS must be compatible with the selected IC package. Different types of IC packages have different sizes and shapes, so the design of CPS needs to ensure that the cavity size can fully accommodate the package used to ensure the stability and safety of the package. Inoltre, the depth of the cavity should also take into account the space between the package and the PCB surface so that the package can connect seamlessly to other components or circuit board connections.
Secondariamente, the size of CPS is also affected by the number of IC packages. In practical applications, multiple IC packages may need to be mounted into the same CPS at the same time, so it is necessary to ensure that the size of the CPS can accommodate and effectively manage the spacing and layout between these packages. Reasonable size design can maximize the integration of PCB boards and reduce the overall size and weight, thereby meeting the design requirements for product compactness and lightweight.
Inoltre, the size of the CPS also needs to take into account the heat dissipation effect. By rationally designing the size and layout of the cavity, the heat dissipation surface area can be effectively increased and the heat dissipation efficiency can be improved, thereby ensuring the stability and reliability of the IC package under high load operating conditions. Pertanto, when determining the size of the CPS, it is necessary to comprehensively consider the heat dissipation requirements and take corresponding heat dissipation design measures, such as installing heat sinks and designing ventilation holes.
Riassumendo, the size design of CPS is a process that comprehensively considers many factors and needs to be customized according to specific application requirements, the size and quantity of IC packages, and heat dissipation requirements. Through reasonable size design, the advantages of CPS can be fully utilized, the performance and reliability of the product can be improved, and the application needs of different scenarios can be met.
The Manufacturing Process of Cavity Package Substrate.
The manufacturing process of CPS is a complex and precise process, and its successful implementation relies on highly precise process control and advanced processing equipment. The manufacturing process of CPS will be introduced in detail below.
The first is PCB manufacturing. This step is the basis of CPS manufacturing and involves transferring the desired circuit pattern onto the substrate via printing technology. FR-4 fiberglass material is usually used as the substrate, and methods such as chemical etching or laser cutting are used to accurately create the required circuit pattern. During this process, various parameters such as temperature, humidity and chemical liquid concentration need to be strictly controlled to ensure the quality and accuracy of the circuit board.
Next is cavity machining. This is a critical step in CPS manufacturing and involves precisely machining cavities onto the PCB board to accommodate the IC package. Cavity processing usually uses CNC machining technology, and the cavity is accurately processed according to the design requirements through equipment such as CNC milling machines or CNC lathes. In this process, high-precision tools and work fixtures are used, and processing parameters are precisely controlled to ensure that the size and shape of the cavity meet the design requirements.
Finalmente, there is encapsulation. This step involves mounting the IC package into the cavity and connecting it to the PCB circuit. The packaging process usually uses soldering technology such as surface mount technology (SMT) or plug-in soldering technology. In this process, high-precision welding equipment, such as a hot air furnace or a reflow oven, is required to accurately weld the package to the PCB board and ensure welding quality and reliability.
Generalmente, the manufacturing process of CPS is a highly precise and complex process that involves multiple steps and the comprehensive application of multiple technologies. Only through strict process control and advanced processing equipment can we ensure that the quality and performance of CPS meet the design requirements to meet the growing demand for high-performance electronic products.
The Application area of Cavity Package Substrate.
Cavity Package Substrate (CPS), as an innovative PCB design solution, is widely used in various fields. Its specially designed cavity structure and excellent heat dissipation performance and electromagnetic compatibility make it particularly suitable for scenarios that require high performance and high reliability.
Innanzitutto, in the field of high-performance computing, CPS is widely used in servers, supercomputers and other equipment. As data processing and storage requirements continue to grow, these devices have increasingly higher requirements for heat dissipation performance and electromagnetic interference. The design of CPS can effectively improve the heat dissipation effect of the equipment, while reducing electromagnetic interference and ensuring the stability and performance of the computer system.
Secondariamente, in the field of communication equipment, CPS is also widely used. Whether it is a base station, optical fiber communication equipment or network router, it needs to have good heat dissipation performance and electromagnetic compatibility to ensure stable and reliable communication. The design of CPS can help these devices better cope with high-frequency, high-power working environments and improve the performance and reliability of communication systems.
Inoltre, in the field of automotive electronics, CPS also plays an important role. With the continuous upgrading of automotive electronic systems, automotive electronic equipment has increasingly higher requirements for heat dissipation and electromagnetic compatibility. The design of CPS can effectively reduce the temperature of automotive electronic equipment, improve the stability and reliability of the system, and at the same time meet the special requirements of the automotive working environment.
Generalmente, Cavity Package Substrate (CPS) has broad application prospects in high-performance computing, communication equipment, automotive electronics and other fields. Its excellent heat dissipation performance and electromagnetic compatibility make it an ideal choice to meet various high-demand scenarios. With the continuous development of technology and the continuous expansion of application scenarios, CPS will surely show its unique advantages and value in more fields.
What are the advantages of Cavity Package Substrate?
Cavity Package Substrate (CPS), as an innovative PCB design solution, brings many advantages that make it an ideal choice to meet the growing demand for high-performance electronic products. Rispetto al PCB tradizionale, CPS shows significant excellent performance in the following aspects.
Primo, CPS has excellent heat dissipation performance. Because the cavity structure in CPS can provide a larger surface area, heat dissipation is more efficient. Inoltre, CPS often uses materials with high thermal conductivity, such as metal substrates or ceramic substrates, to further improve the heat dissipation effect. This excellent heat dissipation performance enables CPS to maintain stable operation under high power density and long-term load, providing an important guarantee for the reliability of electronic products.
Secondariamente, CPS has lower electromagnetic interference. Due to the presence of cavities in CPS, the distance between circuits is increased, thereby reducing crosstalk and interference between signals. Inoltre, the special design in CPS can effectively reduce electromagnetic leakage and improve the anti-interference ability of electronic products, making them more stable and reliable in complex electromagnetic environments.
Third, CPS has a higher level of integration. The CPS design allows multiple components to be integrated onto a single PCB board, thereby reducing the size and weight of the board. This highly integrated design not only improves the performance of electronic products, but also reduces the overall cost, while also improving the reliability and stability of electronic products.
Finalmente, CPS has higher reliability. By using advanced materials and processes, CPS can achieve higher manufacturing accuracy and consistency, thereby reducing defective rates during the manufacturing process. Inoltre, the cavity structure in CPS can effectively slow down the impact of temperature changes on electronic components and extend the service life of electronic products.
Riassumendo, Cavity Package Substrate (CPS) has become an ideal choice to meet the needs of high-performance electronic products due to its excellent heat dissipation performance, low electromagnetic interference, high integration and reliability. With the continuous advancement of electronic technology and the expansion of application fields, it is believed that CPS will play an increasingly important role in the future, bringing more possibilities to the development of electronic products.
Frequently Asked Questions
What are the advantages of CPS compared with traditional PCB?
CPS has many advantages over traditional PCB. Innanzitutto, the cavity in the CPS design can effectively improve the heat dissipation effect, allowing the electronic components to maintain a lower temperature during work, improving the stability and reliability of the system. Secondariamente, CPS can reduce electromagnetic interference, improve the system’s anti-interference ability, help improve signal transmission quality and reduce error rates. Inoltre, CPS also has a higher degree of integration and can integrate more functional modules in a limited space, thereby reducing the overall size and improving system performance. Taken together, CPS is superior to traditional PCB in terms of heat dissipation performance, electromagnetic compatibility, integration and reliability, and is suitable for the design and manufacturing of electronic products with higher performance requirements.
How is the cavity size of CPS determined?
The cavity size of CPS is usually determined based on the specific IC package type and size. During the design stage, engineers need to consider factors such as the IC package’s outer dimensions, pin layout, and heat dissipation requirements, and determine the most appropriate cavity size based on the layout and connection requirements inside the cavity. Generale, the size of the cavity should be slightly larger than the overall size of the IC package, with an appropriate margin left to ensure component installation and heat dissipation.
What package types is CPS suitable for?
CPS is suitable for a variety of packaging types, including but not limited to BGA (ball grid array), LGA (pin grid array), QFN (exposed lead package), and so on. Different packaging types are suitable for different application scenarios and performance requirements. When designing a CPS, engineers need to select an appropriate package type based on specific application requirements, and perform corresponding design optimization and layout planning to ensure the performance and reliability of the CPS.
What is the difference between CPS and traditional PCB?
The biggest difference between CPS and traditional PCB is its special design, which forms one or more cavities on the PCB board to accommodate IC packaging. These cavities provide better heat dissipation and electromagnetic shielding, thereby improving the performance and reliability of electronic products.
What package types is CPS suitable for?
CPS is suitable for a variety of packaging types, including BGA (ball grid array), LGA (pin array), QFN (exposed lead package), and so on. When designing a CPS, the size and layout of the cavity need to be determined based on the specific package type.
How is the cavity size of CPS determined?
The determination of cavity size requires consideration of many factors, including the size and height of the IC package, heat dissipation requirements, circuit layout, and so on. Normally, the size of the cavity should be slightly larger than the size of the IC package to ensure that the IC package can be fully accommodated within the cavity and provide sufficient space for heat dissipation.