What are CPU substrates?
CPU substrates Fabbricante, “UCPU Substrates Manufacturer specializes in the production of high-quality substrates for UCPU applications. Our state-of-the-art facilities utilize cutting-edge technology to engineer substrates that meet the rigorous demands of modern computing. With a dedicated focus on innovation and quality control, we ensure that each substrate delivers optimal performance and reliability. Whether for data centers, consumer electronics, or industrial applications, our substrates are trusted by leading manufacturers worldwide for their exceptional durability and precision engineering.”
Central Processing Unit Substrates (Central Processing Unit Substrates) are an indispensable part of modern electronic equipment. They play the role of a bridge between the central processing unit (CPU) and the motherboard. As the basic component between the CPU and the motherboard, the CPU backplane not only provides the necessary electrical connections, but also assumes the function of mechanical support to ensure that the CPU can effectively communicate and cooperate with other components on the motherboard.
Tipicamente, CPU backplanes are constructed from multiple layers of composite materials to meet stringent requirements for electrical performance and reliability. These composite materials include FR-4 fiberglass composites, copper foil, and outer pad coverings. FR-4 material has excellent insulation properties and mechanical strength, which can effectively prevent the circuit board from bending and damage; while copper foil, as a conductive layer, provides a reliable electrical connection and ensures the stability of signal transmission.
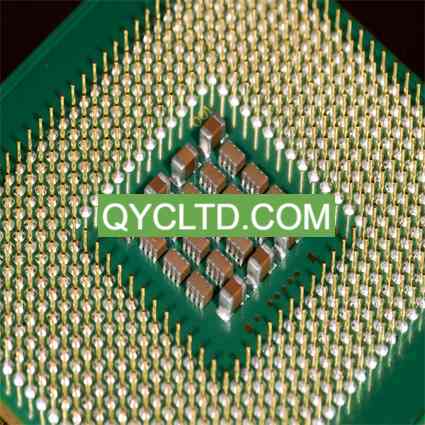
CPU substrates Manufacturer
The design and manufacturing process of a CPU backplane requires consideration of many factors, including circuit layout, signal integrity, Gestione termica, and packaging technology. Through precise design and manufacturing processes, the CPU backplane can achieve high integration, efficient thermal management, and stable signal transmission, thereby ensuring the performance and reliability of the entire electronic device.
Generalmente, the CPU backplane plays an important role in modern electronic equipment. It not only connects the CPU and motherboard, but also connects various components of the entire system, providing a solid foundation and guarantee for the normal operation of electronic equipment.
CPU substrates design Reference Guide.
Designing a CPU backplane requires in-depth consideration of several key factors to ensure it performs well in a variety of application scenarios. Here are some reference guidelines and suggestions for designing a CPU backplane:
Circuit layout
When designing a CPU backplane, proper circuit layout is crucial. A good layout can minimize signal interference and crosstalk and improve the stability and reliability of the circuit. Engineers should take care to separate high-frequency and low-frequency signals to avoid signal crossover and interference.
Signal integrity
Maintaining signal integrity is one of the key goals in designing a CPU backplane. This includes controlling the impedance matching of signal transmission lines, reducing signal reflections and delays, and optimizing signal transmission rate and accuracy. Signal integrity can be maximized through proper layout and layer stack design.
Thermal management
Effective thermal management is critical in CPU backplane design, especially for high-performance CPUs. Engineers should consider using cooling devices such as radiators, heat sinks, and fans to ensure that the CPU maintains a stable temperature under heavy load. Inoltre, proper thermal design can extend the life of the CPU and improve performance.
Packaging technology
Choosing the right packaging technology is critical to the performance and reliability of your CPU backplane. Engineers should select appropriate packaging materials and processes based on specific application requirements to ensure that the CPU can operate normally under various environmental conditions and has good resistance to vibration and corrosion.
Design Reference Guides provide engineers with valuable advice and tips to help them design CPU backplanes more efficiently and reliably. By comprehensively considering factors such as circuit layout, signal integrity, Gestione termica, and packaging technology, engineers can design a CPU chassis with excellent performance, stability and reliability to meet the needs of different application scenarios.
What material is used in CPU substrates?
As the core component of electronic equipment, the choice of materials for the CPU chassis is crucial. Common CPU backplane materials include FR-4 fiberglass composite, copper foil, and pad overlays, among others. These materials offer a range of excellent properties, making them ideal for manufacturing CPU baseplates.
Primo, FR-4 fiberglass composite is a common substrate material with excellent mechanical strength and insulation properties. Its main components are glass fiber and epoxy resin, which can withstand high-intensity mechanical stress and electrical stress. It also has good chemical corrosion resistance and is suitable for various harsh working environments.
Secondariamente, copper foil is one of the main conductive layer materials of the CPU chassis. Copper foil has excellent electrical conductivity and processability, and can effectively transmit current and maintain a stable electrical connection. By covering the FR-4 substrate with a layer of copper foil, efficient routing and connection of circuits can be achieved, improving the overall performance of the CPU backplane.
Inoltre, the pad cover is one of the key components of the CPU backplane, protecting the solder joints and providing additional mechanical support. Pad covers are typically made of high-temperature tolerant materials, such as polyimide (Pi greco) or polytetrafluoroethylene (PTFE), which maintain stability in high-temperature environments and resist stress and vibration during soldering.
To summarize, FR-4 fiberglass composite, copper foil, and pad overlays are the key materials chosen for manufacturing CPU backplanes. They have excellent electrical conductivity, mechanical strength and high temperature resistance, making them suitable for a variety of environments and application needs. By properly selecting and matching these materials, you can ensure that the CPU chassis has stable and reliable performance and meets the design requirements of various electronic devices.
What size are CPU substrates?
The size of the CPU chassis is one of the crucial considerations in the design and manufacturing process. The choice of size directly affects the layout of the CPU chassis, connectivity performance and overall reliability. Tipicamente, a CPU backplane is sized based on specific CPU and motherboard specifications.
In modern electronic equipment, common CPU chassis sizes include standard rectangular form factors as well as various custom designs of specific sizes. Standard sizes are typically based on industry standards and common motherboard sizes, such as ATX, Micro-ATX, or Mini-ITX. These standard-sized CPU backplanes are compatible with a wide range of motherboards, providing flexibility and versatility.
In addition to standard sizes, there are a variety of custom-designed CPU backplanes whose dimensions can be adjusted and optimized for specific application needs. Custom-sized CPU backplanes are often used in special scenarios, such as embedded systems, industrial control equipment, or applications with specific size constraints.
The choice of size is not only to fit the CPU and motherboard, but also affects the layout and wiring of the CPU chassis. Appropriate size can provide enough space to arrange circuit components and ensure the stability and reliability of signal transmission. Inoltre, the size also directly affects the heat dissipation performance of the CPU chassis. Enough space can accommodate radiators and fans to improve the overall heat dissipation effect.
Insomma, the size selection of the CPU chassis is a complex process that requires comprehensive consideration of multiple factors. It must not only meet the compatibility requirements of the CPU and the motherboard, but also consider factors such as layout, dissipazione del calore, and overall performance. Through appropriate size design, you can ensure that the CPU chassis can provide excellent performance and reliability in various application scenarios.
The Manufacturer Process of CPU substrates.
Manufacturing a CPU baseboard is a highly complex and precise process that involves multiple key steps, from design verification to final manufacturing. Each step is critical and directly affects the quality and reliability of the baseboard.
Primo, design verification is the starting point for manufacturing the CPU chassis. In questa fase, engineers will use computer-aided design (CAD) software to design the chassis based on specific needs and specifications. Design verification ensures the rationality of the circuit layout, signal integrity and thermal management of the backplane, laying the foundation for the subsequent manufacturing process.
Next is the graphics drawing stage, where engineers will draw the specific graphics of the base plate based on the results of design verification. This includes converting the circuit diagram into an actual PCB graphic, determining the layout and connection of individual components, and refining the parameters and specifications of the backplane.
After the graphics drawing is completed, it is the stage of material selection. Based on the design requirements and application scenarios, engineers will select appropriate materials, common ones including FR-4 fiberglass composite materials and copper foil. The choice of materials has an important impact on the electrical performance, mechanical strength and high temperature resistance of the backplane.
This is followed by the process steps of lamination and drilling. During the lamination process, various material layers are pressed together to form a multi-layered PCB structure. This step requires highly precise control to ensure a tight fit and smoothness between the individual layers. During the drilling process, engineers will drill holes in the base plate according to the design requirements to prepare for subsequent component installation and circuit connections.
Through the above series of process steps, the manufacturing of the CPU base plate is completed. Exquisite manufacturing technology and strict quality control ensure the quality and reliability of the baseboard, enabling it to operate stably in various application scenarios, providing a solid foundation for improving the performance of electronic equipment.
The Application area of CPU substrates.
As a core component of modern electronic equipment, CPU backplane plays an important role in various fields. It not only provides a stable electrical connection, but also achieves efficient data transmission, bringing key technical support to various application scenarios.
Nel campo informatico, the CPU backplane is one of the key components of the entire system. It connects various core components such as CPU, memory, graphics card, and so on. to ensure that they can work together efficiently. Whether it is a desktop computer, server or supercomputer, it is inseparable from a high-performance CPU chassis to achieve complex computing tasks and data processing needs.
Communication equipment is another important application area. Whether it is a mobile phone, router or base station, they all require reliable electrical connections and fast data transmission capabilities to ensure communication stability and efficiency. The CPU backplane provides powerful support for communication equipment by connecting various communication chips and electronic components.
Consumer electronics are also one of the main application scenarios of CPU backplanes. From smartphones to tablets, from smart homes to smart wearable devices, these products require compact, high-performance CPU backplanes to achieve various complex functions and application requirements. The stability and performance of the CPU chassis directly affect consumer experience and product competitiveness.
In the field of industrial control, the CPU backplane assumes the important tasks of monitoring, control and data processing. It is widely used in various industrial equipment such as factory automation, robot control, intelligent instrumentation, and so on., providing reliable electrical connections and intelligent data processing capabilities for industrial production and manufacturing.
Insomma, CPU backplanes play an irreplaceable role in various fields such as computers, communication equipment, consumer electronics, and industrial control. Its stability, performance and reliability directly affect the functions and performance of various electronic products, providing important support and guarantee for the development and progress of modern science and technology.
What are the advantages of CPU substrates?
When compared with traditional circuit connection methods, the CPU backplane presents a series of compelling advantages. Primo, it has a higher level of integration. As a key component in modern electronic equipment, the CPU backplane can accommodate more circuit components and tightly integrate them together. This highly integrated design makes the overall equipment more compact, saves space, and improves system performance and efficiency.
Secondariamente, the CPU chassis has better thermal management capabilities. As the functionality of electronic devices continues to increase, managing heat has become even more critical. The CPU base plate can effectively reduce the system temperature and maintain the normal operating temperature of the components by effectively distributing heat and using heat sinks and thermal conductive materials. This excellent thermal management capability not only helps extend the service life of the equipment, but also improves system stability and reliability.
Finalmente, the CPU backplane has more stable signal transmission performance. Nei moderni dispositivi elettronici, accurate transmission of data is crucial. The CPU baseboard uses high-quality materials and precise manufacturing processes to ensure signal stability and reliability, thereby reducing the incidence of data transmission errors. This stable signal transmission performance not only improves the overall performance of the system, but also enhances the adaptability of the device in complex environments.
Riassumendo, the CPU backplane has become an indispensable part of modern electronic equipment due to its high integration, excellent thermal management capabilities and stable signal transmission performance. It not only improves the performance and efficiency of the device, but also provides users with a more stable and reliable experience. As technology continues to develop, CPU backplanes will continue to play an important role in promoting the progress and development of the electronic equipment industry.
Domande frequenti
What is the connection between the CPU backplane and the motherboard?
The connection between the CPU backplane and the motherboard is usually made by soldering. The pads on the CPU backplane correspond to the slots or connectors on the motherboard, and they are connected together by soldering. This connection method not only ensures a stable electrical connection, but also provides sufficient mechanical support so that the CPU can be plugged in and out safely and reliably.
How does the size of the CPU chassis affect performance?
The size of the CPU chassis directly affects its layout, cooling effect and electrical performance. Larger baseboard size usually means more space for arranging circuits and components, allowing for more complex circuit designs and higher levels of integration. Inoltre, a larger base plate can also help improve heat dissipation, reduce temperature, and improve CPU performance stability.
What are the considerations in material selection for a CPU backplane?
When selecting a CPU backplane material, there are many factors to consider, including electrical performance, Resistenza meccanica, high temperature resistance, cost, and manufacturing processes. Common materials such as FR-4 fiberglass composites have good electrical properties and mechanical strength and are suitable for most applications. Under certain special needs, such as high frequency, high-speed transmission or extreme environments, special materials may need to be selected to meet performance requirements.