What are GPU Substrates?
GPU Substrates Manufacturer.A cutting-edge producer of GPU substrates, this company leads the market with its advanced manufacturing techniques and superior quality products. Their state-of-the-art facilities utilize innovative processes to craft substrates that optimize GPU performance, ensuring seamless integration into a variety of devices. With a relentless commitment to research and development, they continuously push the boundaries of what’s possible in substrate technology. Renowned for their precision engineering and dedication to customer satisfaction, they stand as the go-to choice for companies seeking top-tier GPU substrates that deliver unparalleled performance and reliability.
The GPU substrate is a flat sheet usually made of non-conductive material such as fiberglass, epoxy or composite. These materials have good insulating properties and mechanical strength, and can effectively support and protect electronic components. On the surface of the GPU substrate, fine and complex circuit paths are laid or printed. These paths are designed to connect the GPU chip with other electronic components to achieve information transmission and signal processing. GPU substrates are carefully constructed and designed to maximize the performance and reliability of electronic devices.
Compared with traditional manual wiring, the circuit paths of the GPU substrate are precisely designed and manufactured to transmit signals more efficiently and reduce circuit noise. In addition, the GPU substrate also has good heat dissipation performance, which can effectively disperse the heat generated by electronic components and maintain the stable operation of the device.
As a core component of modern electronic equipment, GPU substrates are widely used in various fields. In the field of consumer electronics, GPU substrates are widely used in smartphones, tablets, game consoles and other devices to support high-definition video playback, graphics rendering and game running. In industrial control systems, GPU substrates are used for real-time data processing and image recognition, improving production efficiency and product quality. In the field of scientific research, GPU substrates are used for complex simulation calculations and data analysis, accelerating scientific discovery and innovation.
In general, as a key component of modern electronic equipment, GPU substrates are not only important in terms of performance, but also play an irreplaceable role in promoting technological progress and social development. With the continuous advancement and innovation of technology, GPU substrates will continue to play an important role in promoting the development and intelligence of electronic equipment.
GPU Substrates design Reference Guide.
The design of the GPU substrate is a critical step in ensuring graphics processing unit (GPU) system functionality and performance. Designers need to consider many factors to maximize the performance and reliability of the GPU substrate.
First, designers need to carefully consider the layout of electronic components. Good component layout can minimize signal interference and electromagnetic interference and improve the signal integrity of the system. By rationally arranging the positions of GPU chips, memory, power modules and other key components, the delay and loss of signal transmission can be effectively reduced, thereby improving the response speed and stability of the system.
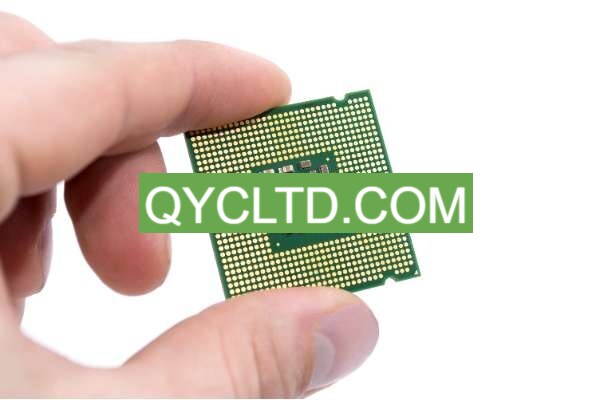
GPU Substrates Manufacturer
Second, designers need to carefully design the routing of circuit connections. Optimized circuit routing can ensure smooth and stable signal transmission and minimize crosstalk and signal distortion. By rationally designing circuit paths and signal layer stacking, designers can effectively reduce circuit complexity and improve system reliability and stability.
In addition, thermal management is also one of the crucial considerations in GPU substrate design. Since the GPU chip generates a lot of heat during operation, good thermal management design can ensure that the system maintains a stable operating temperature under high load conditions. Designers need to properly design radiators, fans and heat dissipation channels to effectively dissipate and remove heat, prevent GPU chip overheating and damage, and ensure the long-term stability and reliability of the system.
Finally, manufacturability is also an important aspect of design considerations. Designers need to ensure that the design of the GPU substrate meets the requirements of the manufacturing process, including material selection, process flow, production equipment, etc. Reasonable design can reduce manufacturing costs and improve production efficiency, while ensuring that the quality and performance of the final product reach the expected level.
To sum up, the design of GPU substrates involves many complex technologies and considerations, including component layout, circuit connections, thermal management, and manufacturability. Only by comprehensively considering these factors can designers design a GPU substrate with excellent performance, stability and reliability to meet the needs of different application scenarios.
What material is used in GPU Substrates?
As a key component in modern electronic equipment, the materials used in GPU substrates are crucial and directly affect their performance, reliability and scope of application. Typically, GPU substrates are made of materials such as fiberglass reinforced epoxy resin (FR4). This is because FR4 has good insulation properties, mechanical strength and heat resistance, and is suitable for most application scenarios.
During the manufacturing process of FR4 substrates, glass fiber cloth is impregnated with epoxy resin and then cured under high temperature and high pressure conditions. This material is not only relatively low-cost, but also easy to process and shape, so it is widely used in many consumer electronics products, such as smartphones, tablets, and game consoles.
In addition to FR4, GPU substrates will also use other materials depending on specific application requirements. For example, where higher performance and reliability are required, ceramic substrates may be selected. Ceramic substrates have excellent thermal conductivity and mechanical strength, making them suitable for applications in high-temperature environments, such as aerospace and automotive electronic systems.
In addition, polyimide (PI) substrates are also widely used in some special fields, such as medical equipment and military applications. Polyimide has excellent high temperature resistance and chemical stability, making it suitable for use in extreme environments.
For some special requirements, such as those requiring better heat dissipation performance or electromagnetic shielding capabilities, metal substrates may become the choice. Metal substrates are usually made of aluminum or copper materials and have good heat dissipation and electromagnetic shielding properties, making them suitable for high-power electronic devices and radio frequency circuit design.
In general, the materials used for GPU substrates depend on their specific application needs and performance requirements. By selecting appropriate materials, you can ensure that the GPU substrate maintains stable and reliable performance under various environments and working conditions, thereby meeting the needs of various types of electronic equipment.
What size are GPU Substrates?
GPU substrate dimensions vary depending on application requirements and the size of the electronic device or system. They can range from tiny substrates for small devices like cell phones and wearables to giant substrates for larger systems like industrial equipment and telecommunications infrastructure.
For small devices, such as smartphones and wearable devices, GPU substrates are usually very delicate and compact. These devices have very strict space requirements, so the GPU substrate needs to be designed to be as small as possible to fit into the compact internal space. Micro-substrates often use advanced manufacturing processes to achieve a high degree of integration and density, thereby maximizing space savings while maintaining an excellent balance of performance and power consumption.
In contrast, GPU substrates used in large systems such as industrial equipment and telecommunications infrastructure tend to be bulkier. These systems need to process large amounts of data and complex computing tasks, so GPU substrates need to have greater computing power and memory capacity. To achieve this, large substrates often use multi-layer designs to accommodate more electronic components and connection lines to meet the performance needs of the system.
Not only that, large substrates also need to have good heat dissipation capabilities and reliability to cope with long-term high-load operation environments. Therefore, when designing a large GPU substrate, in addition to considering performance and size, special attention needs to be paid to thermal design and reliability engineering to ensure stable system operation and long-term reliability.
To sum up, the size of the GPU substrate depends on its application needs and required performance. It can be a micro substrate for small devices or a giant substrate for large systems. Each size has its own specific design considerations and optimizations. direction.
The Manufacturer Process of GPU Substrates.
The manufacturing process of GPU substrates is a complex and precise process involving multiple key steps, each of which has a significant impact on the quality and performance of the final product.
First, the fabrication process starts with substrate preparation. The substrate is usually made of fiberglass reinforced epoxy (FR4) or other materials. During the preparation phase, the substrate is cleaned, cut and coated to ensure a smooth and dust-free surface.
Next is layer alignment. If the GPU substrate is a multi-layer structure, alignment between the different layers is critical. In this step, the layers are precisely stacked together to ensure proper connection of the circuit paths.
Next comes the etching or printing of the circuit paths. This is one of the key steps in the manufacturing process. Through photolithography or printing technology, the required circuit paths or wire patterns are formed on the surface of the substrate. These circuit paths will be used to connect GPU chips and other electronic components.
Then comes the drilling of component holes. The locations for drilling holes in the substrate are pre-designed for mounting electronic components. A precise drilling process ensures correct positioning and secure connection of the components.
Pad application is the next step. Solder pads are small pieces of metal used to connect electronic components, and they are mounted precisely in specific locations on a substrate. Pad applications typically involve thermal fusion or surface mount technology.
Component assembly is another critical step in the manufacturing process. At this stage, electronic components such as GPU chips, resistors, capacitors, etc. are accurately mounted on the substrate at predetermined locations. Precise assembly ensures proper operation and stability of the circuit.
Finally comes the testing phase. The manufactured GPU substrate will be subjected to various tests to ensure that its functionality and performance meet the design requirements. These tests may include electrical testing, signal integrity testing, thermal testing, etc.
Overall, the manufacturing process of GPU substrates is a delicate and complex process that requires a high degree of technology and expertise. Each step is critical and affects the quality and performance of the final product. Through strict quality control and advanced manufacturing technology, GPU substrate manufacturers are able to produce high-quality, reliable products that meet the needs of various electronic devices.
The Application area of GPU Substrates.
GPU substrates are widely used in various industries and play a key role in the technological development and improvement of life in modern society. Consumer electronics is one of the main application areas of GPU substrates. From smartphones and tablets to personal computers and game consoles, almost all modern electronic products use GPUs to process graphics and visual effects, and GPU substrates are one of the core components in these devices.
In the automotive industry, GPU substrates also play an important role. Modern cars are equipped with more and more intelligent systems and driving assistance functions, such as in-car entertainment systems, navigation systems, intelligent driving assistance systems, etc., which require GPUs for efficient graphics processing and calculations.
GPU substrate technology is also widely used in the aerospace field. From flight simulators to flight control systems, GPU substrates bring more realistic and accurate image processing and data calculations, improving the performance and safety of aerospace systems.
Medical equipment is another important GPU substrate application area. Medical imaging equipment such as CT scanners, MRI instruments, etc. require high-performance graphics processing capabilities to process large amounts of image data in real time, and the high parallel computing capabilities of GPU substrates enable these medical devices to diagnose and treat more quickly and accurately.
GPU substrate technology is also widely adopted in the telecommunications and industrial automation fields. In the field of telecommunications, GPU substrates are used for high-performance computing and network processing in data centers, improving the efficiency and throughput of communication systems. In the field of industrial automation, GPU substrates are used in control systems, machine vision and automated production lines, improving production efficiency and quality control levels.
In short, the application of GPU substrates has penetrated into all fields of modern society, making important contributions to technological innovation and productivity improvement in all walks of life. With the continuous advancement of technology and the continuous expansion of application fields, GPU substrates will continue to play an important role in promoting the development of human society in a more intelligent and efficient direction.
What are the advantages of GPU Substrates?
As one of the core components in modern electronic equipment, GPU substrate has many obvious advantages among many excellent features, making it the first choice in the electronics industry. Compared with other wiring methods, GPU substrates have significant advantages in the following aspects:
First of all, the GPU substrate is small in size but can accommodate a large number of electronic components and connection lines. This compact design makes GPU substrates widely used in electronic devices with limited space, such as smartphones, tablets, and portable game consoles. Its compact size provides strong support for the device’s portability and portability.
Secondly, the GPU substrate has a high degree of reliability. Because the GPU substrate adopts industry-standard manufacturing processes and quality control, it has excellent durability and stability. This enables electronic equipment to operate stably for a long time, reduces the frequency of repairs and replacements, and improves user satisfaction and trust.
In addition, GPU substrates are easy to mass produce, greatly improving production efficiency. Using modern manufacturing processes and automated equipment, the production process of GPU substrates can be highly standardized and streamlined, greatly reducing manufacturing costs and production cycles, and meeting the rapid changes in market demand.
At the same time, GPU substrates have fewer assembly errors. During the manufacturing process, precise design and advanced production technology ensure the assembly quality of the GPU substrate, reduce failures and losses caused by incorrect assembly, and improve production efficiency and product quality.
In addition, the GPU substrate has excellent signal integrity. Through precise wiring design and high-quality materials, GPU substrates can effectively reduce interference and distortion in signal transmission, ensuring the stability and performance of electronic equipment.
Finally, the GPU substrate has excellent thermal performance. Its well-designed heat dissipation structure and excellent material thermal conductivity can effectively dissipate the heat generated by electronic equipment quickly, keep the temperature of the equipment within a safe range, and improve the stability and reliability of the equipment.
To sum up, GPU substrates have become an indispensable and important part of modern electronic equipment due to their many advantages such as small size, high reliability, easy mass production, few assembly errors, good signal integrity, and superior thermal performance. With the continuous development and innovation of technology, it is believed that GPU substrates will continue to play an important role in the future electronics industry and bring more convenience and possibilities to people’s lives and work.
FAQ
What factors need to be considered in GPU substrate design?
GPU substrate design requires consideration of multiple factors, including electronic component layout, signal integrity, thermal management, and manufacturability. Proper layout ensures optimal performance of the signal transmission path, while effective thermal management helps prevent the GPU chip from overheating.
What are the commonly used materials for GPU substrates?
Commonly used materials for GPU substrates include fiberglass reinforced epoxy (FR4), ceramics, polyimide and metal substrates. Material selection depends on application needs and desired performance.
What is the manufacturing process of GPU substrate?
The manufacturing process of a GPU substrate usually includes steps such as substrate preparation, layer alignment, etching or printing of circuit paths, drilling of component holes, pad application, component assembly and testing.
In what fields are GPU substrates used?
GPU substrates are widely used in consumer electronics, automotive, aerospace, medical equipment, telecommunications, industrial automation and other fields. They are used in everything from smartphones and computers to automotive control systems and medical imaging equipment.
What are the advantages of GPU substrates over other wiring methods?
Compared with other wiring methods, GPU substrates have advantages such as small size, high reliability, easy mass production, fewer assembly errors, good signal integrity, and superior thermal performance, making them the first choice for many electronic devices.