What is a glass packaging substrate?
Glass Package Substrates Manufacturer.A leading innovator in electronic components, our company specializes in the fabrication of cutting-edge Glass Package Substrates. With state-of-the-art technology and a commitment to excellence, we engineer substrates that optimize performance and reliability in diverse applications, from consumer electronics to automotive systems. Our stringent quality control measures ensure precision manufacturing, meeting the stringent demands of the industry. From initial design to final delivery, we prioritize customer satisfaction, offering tailored solutions and responsive support. Trust us as your partner for superior Glass Package Substrates, where innovation meets reliability.
Glass packaging substrate, as an important component in electronic devices, plays a key role. It is a specially designed substrate that is used to support and connect electronic components, providing a stable structure and reliable electrical connection for circuits. These substrates are made of high-quality glass materials with excellent insulation properties and excellent mechanical strength, making them suitable for a variety of high-temperature and high-frequency applications.
In the electronics industry, glass packaging substrates are widely used in various products, including communication equipment, medical instruments, automotive electronics and industrial control systems. Its excellent performance and reliability make it one of the materials of choice for many critical applications.
The manufacturing process of glass packaging substrates requires strict control and precision processing. From the cutting and surface treatment of glass substrates, to the deposition and encapsulation of conductive layers, each step requires precision equipment and professional technology to ensure product quality and performance.
Overall, glass packaging substrates play an indispensable role in modern technology. They not only provide stable and reliable electrical connections, but also provide important support for the normal operation of electronic equipment, promoting the continuous progress and development of science and technology.
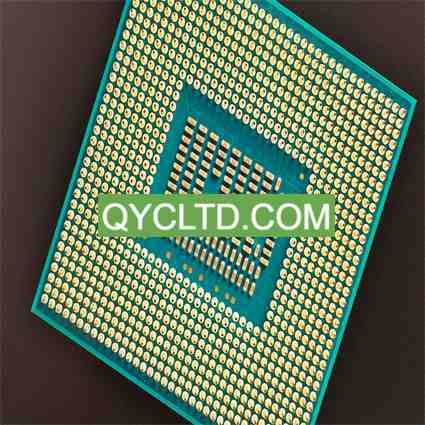
Glass Package Substrates Manufacturer
What is the design process for glass packaging substrates?
The design process for glass packaging substrates is a precise and critical process that determines the performance and reliability of the final product. The design process of glass packaging substrate will be introduced in detail below:
Requirements Analysis: The first step in the design process is a thorough analysis of the circuit requirements. The design team needs to understand the circuit’s functions, performance indicators, and working environment requirements.
Schematic design: Schematic design is the basis of the design process. The designer will draw the corresponding schematic diagram based on the circuit requirements, including the connection relationship and function allocation of each component.
Material selection: Based on the performance requirements of the circuit and the working environment, the design team will select a suitable glass material as the base material of the substrate. Considerations include dielectric constant, coefficient of thermal expansion, and mechanical strength.
Layout design: Based on the schematic design, the design team will conduct layout design to determine the location and wiring direction of each component on the substrate. Layout design needs to consider factors such as the circuit’s signal transmission path, power distribution, and heat dissipation.
Wiring design: Wiring design is an important part of the design process. The designer will conduct wiring design of circuit connection lines on the substrate based on the layout design to meet the transmission speed, anti-interference ability and power consumption requirements of the circuit.
Simulation verification: The design team will conduct simulation verification of the designed layout and wiring to ensure the performance and stability of the circuit. Conduct signal integrity analysis, electromagnetic compatibility testing and thermal analysis through simulation software.
Prototyping: After completing simulation verification, the design team will produce the first batch of sample prototypes for actual testing. Through prototype testing, problems in the design are discovered and corrected to ensure the performance and reliability of the final product.
Design document organization: Finally, the design team will organize the documents and materials generated during the design process, including schematics, layout diagrams, wiring diagrams, simulation reports and test results, etc., as a summary and record of the design.
The design process of glass packaging substrates requires sufficient professional knowledge and experience of the design team to ensure the accuracy and reliability of the design. Through a rigorous design process, reliable guarantee can be provided for the normal operation of electronic equipment.
How are glass packaging substrates made?
The manufacturing process of glass packaging substrates is a precise and complex process that requires highly specialized equipment and technology to ensure the quality and performance of the final product. Below we will delve into the manufacturing process of glass packaging substrates:
First, the first step in manufacturing a glass packaging substrate is to prepare the glass substrate. Typically, this involves cutting and cleaning high-quality glass stock to ensure a smooth and pure surface.
Next is the surface treatment of the glass substrate. This step is very critical because it directly affects the subsequent conductive layer deposition and packaging process. Chemical or physical methods are often used to clean and modify surfaces to enhance their adhesion and smoothness.
Once the surface treatment is complete, the conductive layer can be deposited. In this step, a thin metal film (such as copper) is typically used to chemically or physically form a conductive layer on the surface of the glass substrate. This conductive layer will become the main conductor of the circuit, connecting the various electronic components.
After completing the deposition of the conductive layer, the next step is the packaging process. This includes covering and protecting the conductive layer from environmental influences and damage. It is usually covered with a covering layer or encapsulant, and then the encapsulation layer is cured by heating or UV curing.
Finally, the encapsulated glass packaging substrate undergoes final inspection and testing. This includes a thorough inspection of size, shape, conductivity and durability to ensure it meets specifications and works properly.
To summarize, the manufacturing process of glass packaging substrates involves multiple key steps, including preparation of the glass substrate, surface treatment, conductive layer deposition, encapsulation, and final inspection. These steps require highly specialized equipment and techniques to ensure the quality and performance of the final product.
What materials are used for glass packaging substrates?
As an important component of modern electronic equipment, glass packaging substrates play a vital role in the materials used in their manufacturing process. The following are common glass packaging substrate materials:
Glass substrate: As the main material of glass packaging substrate, glass substrate has excellent mechanical strength and good insulation properties. Common glass materials include Borosilicate Glass and Quartz Glass. These glass materials are high-temperature stable and chemically inert, making them suitable for a variety of high-performance electronic applications.
Conductive layer: A conductive layer is coated on the surface or inside of the glass packaging substrate for connecting electronic components and transmitting signals. Common conductive layer materials include metal materials such as copper and silver, and conductive polymer materials such as polystyrene and polycarbonate. These materials have good electrical conductivity and plasticity, allowing for precise circuit routing and connections.
Insulating layer: There is an insulating layer on the surface of the glass packaging substrate or between the conductive layers to prevent short circuits and electrical interference between circuits. Common insulation layer materials include resin materials such as epoxy resin (Epoxy Resin) and polytetrafluoroethylene (PTFE), as well as glass fiber reinforced resin (Glass Fiber Reinforced Resin). These materials have excellent insulation properties and heat resistance, which can effectively protect the safe operation of circuits.
Covering layer: Glass packaging substrates are usually coated with a protective covering layer on the surface to protect the circuitry from environmental influences and mechanical damage. Common covering materials include epoxy resin, polyimide (Polyimide) and polyurethane (Polyurethane). These materials have excellent heat resistance, corrosion resistance and mechanical strength, ensuring long-term stable operation of circuits.
In general, the material selection of the glass packaging substrate is crucial, not only affecting the performance and reliability of the circuit, but also directly affecting the overall quality and performance of the device. Therefore, when designing and manufacturing glass packaging substrates, manufacturers need to comprehensively consider the physical properties, chemical properties and manufacturing process requirements of the material to ensure that the final product meets the expected performance and quality standards.
How much does a glass packaging substrate cost?
When it comes to the cost of glass packaging substrates, many factors influence the final price. These factors include material selection, number of board layers, complexity, production scale, and any customization requirements. Let’s take a closer look.
First, material selection is a key factor in determining cost. Glass packaging substrates usually use high-quality glass materials, which have excellent insulation properties and mechanical strength, but are also relatively expensive. In addition to the glass itself, the materials of the conductive layer and covering layer also have an impact on cost. Some special materials or coatings may increase manufacturing costs.
Secondly, the number and complexity of board layers will also have an impact on cost. Multilayer PCBs are generally more expensive than single- or double-layer PCBs because they require more materials and manufacturing steps. In addition, design complexities, such as subtle wiring, tight layouts, or special requirements, may require more engineers and production time, thereby increasing costs.
Production scale is also one of the important factors affecting costs. Typically, mass production enables higher efficiencies, thus lowering the cost per unit. In contrast, small batch production may require more manpower and resources, and the cost is relatively high.
Finally, customization requirements may also increase costs. If the customer has special requirements or a custom design, the manufacturer may require additional engineering work and production preparation, which may increase costs.
Overall, the cost of glass packaging substrates varies based on various factors. Generally speaking, high-quality glass packaging substrates may have a higher cost, but they can ensure long-term stability and reliability of the device. Choosing the right manufacturer and proper design can help reduce costs and ensure the quality and performance of the final product.
What are the key attributes of great customer service?
Excellent customer service is one of the key factors to success in any industry. It is not just a service, but an attitude and culture that provides customers with an experience that exceeds their expectations. In the glass packaging substrate manufacturing industry, high-quality customer service is particularly important because it involves long-term and stable cooperative relationships with customers. Here are a few key attributes of great customer service:
Excellent customer service starts with professional knowledge of products and services. The manufacturer’s team should have deep industry knowledge and technical strength, be able to accurately understand customer needs, and provide corresponding solutions. From technical support to after-sales service, professionalism should be demonstrated so that customers can feel the value and trust of cooperation.
In a fast-paced business environment, timely response to customer needs is crucial. Manufacturers should establish an efficient communication mechanism to respond to customer inquiries and feedback in a timely manner to ensure that customers can receive timely support when they need help. This not only shows respect for customers, but also helps build a good working relationship.
Understanding customers’ individual needs and tailoring solutions is an important part of excellent customer service. Manufacturers should establish close cooperative relationships with customers to understand their business models and specific needs, so as to provide products and services that are more in line with customer needs and enhance customer satisfaction and loyalty.
Manufacturers should demonstrate efficient problem-solving capabilities when faced with problems and challenges that may arise from customers. They should be able to quickly identify the source of the problem and take proactive steps to resolve it and ensure that the customer’s interests are protected. At the same time, manufacturers should also focus on problem prevention and reduce the possibility of problems through continuous improvement and optimization.
Excellent customer service is not just a one-time behavior, but a process of continuous improvement. Manufacturers should constantly reflect on and summarize experiences and lessons learned, and look for opportunities and ways to improve customer service quality. Through continuous improvement, manufacturers can continuously improve their competitiveness and win the trust and support of customers.
In the glass packaging substrate manufacturing industry, quality customer service is one of the key factors for long-term business success. Through professional, timely and personalized service, problem solving and continuous improvement, manufacturers can establish solid cooperative relationships with customers and jointly promote the development and progress of the industry.
Who is making the glass packaging substrates?
In today’s fast-paced electronics industry, the task of manufacturing glass packaging substrates is often undertaken by specialized suppliers. These suppliers not only possess advanced production equipment and technology, but also have rich experience and professional knowledge to meet customer demands for high-quality products. The company is at the forefront of this industry with its superior manufacturing capabilities and superior customer service.
As a leading manufacturer of glass packaging substrates, the company is committed to providing customers with high-performance, reliable products. We have advanced production lines and strict quality control systems to ensure that every glass packaging substrate meets the highest quality standards. Whether it is a simple standard product or a customized solution, we are able to meet our customers’ needs and provide fast and efficient production services.
The company’s supply chain management team carefully selects raw materials and partners to ensure stable supply and high quality of products. We have established long-term and stable cooperative relationships with suppliers around the world to provide customers with diverse choices and flexible delivery solutions.
In addition to quality products, the company is also known for its excellent customer service. We have a professional technical team and thoughtful after-sales service, able to respond to customer needs in a timely manner and provide professional technical support and solutions. We are committed to establishing long-term and stable cooperative relationships with our customers to achieve a win-win situation together.
In the process of manufacturing glass packaging substrates, our company always puts quality first and continues to pursue excellence with an attitude of excellence. We will continue to work hard to provide customers with better products and more satisfactory services, and contribute our strength to the development of the electronics industry.
FAQs
How to choose a suitable glass packaging substrate manufacturer?
Choosing the right glass packaging substrate manufacturer is a critical step in ensuring project success. First, you should consider the manufacturer’s technical strength and experience, including its expertise and production capabilities in the field. Secondly, you should understand the manufacturer’s quality control and certification status to ensure that the product meets your standards and requirements. Finally, you should also consider the manufacturer’s customer service level and delivery capabilities to ensure you receive timely support and feedback during the project.
How long is the production cycle of glass packaging substrates?
The production cycle time for glass packaging substrates depends on several factors, including order volume, complexity and the manufacturer’s production capabilities. Generally speaking, the production cycle of ordinary glass packaging substrates usually ranges from a few weeks to a few months. But for high-volume or customized requirements, the production cycle may be longer. Therefore, before starting a project, it is recommended to communicate with the manufacturer and ensure a reasonable timeline is established.
How to optimize the design of glass packaging substrates to reduce costs?
To optimize the design of glass packaging substrates to reduce costs, you can consider the following points. First, layout and wiring are optimized to reduce the number of board layers and line lengths, thereby reducing material and production costs. Second, choose the right materials and processes to ensure performance requirements are met while cost is reduced. In addition, consider mass production and standardized design to improve production efficiency and reduce unit cost. Finally, work with manufacturers to find customized solutions and preferential policies to further reduce overall costs.
How to choose a suitable glass packaging substrate manufacturer?
Choosing the right manufacturer is crucial as they will directly affect your product quality and delivery time. First, you should consider the manufacturer’s experience and reputation. Look for manufacturers that are already serving similar industries and read their customer testimonials and case studies. Secondly, you need to consider their manufacturing capabilities and technical prowess. Make sure the manufacturer has advanced equipment and a professional team that can meet your customized needs and production scale. Finally, communicate with potential manufacturers to learn about their delivery times, after-sales service, and technical support.
How long is the production cycle of glass packaging substrates?
The production lead time for glass packaging substrates depends on several factors, including order quantity, complexity and the manufacturer’s production capabilities. Generally speaking, the production cycle of ordinary glass packaging substrates ranges from several days to several weeks. For customized needs or high-specification projects, the production cycle may be longer. Therefore, when communicating with the manufacturer, make sure you understand the production lead time and possible delivery time delays.
How to optimize the design of glass packaging substrates to reduce costs?
Reducing costs is a concern for every manufacturer. To optimize the design of glass packaging substrates to reduce costs, reasonable design planning is first required. Minimize the number of layers and material usage, and optimize wiring and layout to reduce manufacturing costs. Secondly, choosing the right materials and processes can save costs and improve production efficiency. Additionally, communicate with manufacturers to explore possible customization options and volume production discounts to reduce overall costs.