What are Ultra-Thin CPU BGA Substrates?
Ultra-Thin CPU BGA Substrates Manufacturer.The Ultra-Thin CPU BGA Substrates Manufacturer specializes in crafting cutting-edge components crucial for high-performance computing devices. With precision engineering and advanced materials, they produce substrates that redefine the boundaries of compactness and efficiency in CPU architecture. These substrates, meticulously designed and rigorously tested, enable sleeker and more powerful electronic devices, pushing the boundaries of technology. Leveraging state-of-the-art manufacturing processes, they cater to the demands of industries reliant on miniaturization and performance, ensuring their products uphold the highest standards of quality and reliability in the ever-evolving landscape of semiconductor technology.
Ultra-thin CPU BGA substrate is a special printed circuit board (PCB) characterized by extremely thin thickness and high-density solder ball array (BGA). This advanced substrate technology is mainly used to support and connect modern high-performance central processing units (CPUs) to ensure their efficient operation in various electronic devices. Ultra-thin CPU BGA substrate not only has significant advantages in size and weight, but also excels in performance and reliability, becoming an important part of the development of modern electronic technology.
Tout d’abord, the thickness of the ultra-thin CPU BGA substrate is extremely thin, usually only a few microns to tens of microns. Compared with traditional PCBs, this ultra-thin design allows electronic devices to be lighter and thinner, meeting the needs of modern electronic products for portability and miniaturization. Especially in mobile devices such as smartphones, Comprimés, and ultra-thin laptops, the application of ultra-thin CPU BGA substrates has significantly improved the overall design and user experience of the device.
Deuxièmement, the ultra-thin CPU BGA substrate has a high-density solder ball array. These solder balls (or solder spots) are arranged on the bottom of the substrate and are connected to the motherboard or other components through a hot pressure soldering process. The high-density solder ball array not only improves the reliability of electrical connections, but also supports higher data transmission speeds and processing capabilities. This is particularly important for modern high-performance CPUs, which need to process large amounts of data and complete complex computing tasks in extremely short periods of time.
The material selection of ultra-thin CPU BGA substrate is also one of the keys to its excellent performance. Commonly used materials include fiberglass reinforced epoxy (FR4), polyimide and ceramic substrates. These materials not only provide excellent electrical insulation properties and mechanical strength, but also maintain stable performance in ultra-thin designs. Ceramic substrates, in particular, perform well in high-temperature and high-frequency environments and are widely used in demanding electronic equipment.
De plus,, the manufacturing process of ultra-thin CPU BGA substrate is also very complex and precise. Manufacturing steps include substrate preparation, pattern etching, lamination, forage, plating, and solder ball placement. These steps require highly precise control and strict quality inspection to ensure that each substrate meets design requirements and operates reliably in actual applications. Par exemple, the arrangement of solder balls and the welding process need to be carried out in a high-temperature environment to ensure the firmness of the solder joints and the stability of the electrical connection.
Ultra-thin CPU BGA substrate has shown wide adaptability and superiority in practical applications. They are widely used in a variety of high-performance and high-density electronic devices, tels que les smartphones, Comprimés, ultra-thin laptops, servers and data centers, advanced medical equipment, etc. These devices have extremely high requirements for performance, reliability and volume, and the application of ultra-thin CPU BGA substrates exactly meets these needs.
Bref, ultra-thin CPU BGA substrate, as one of the core components of modern electronic technology, has significantly improved the performance and performance of electronic equipment with its extremely thin design, high-density solder ball array, excellent material properties and complex manufacturing process. reliability. As electronic products continue to develop towards miniaturization, high performance and multi-function, the application prospects of ultra-thin CPU BGA substrates will be broader, pushing electronic technology to new heights.
Ultra-Thin CPU BGA Substrates design Reference Guide.
Designing an ultra-thin CPU BGA substrate is a complex and critical task involving the precise coordination of multiple important factors. To ensure the performance and reliability of the final product, designers must consider aspects such as precise placement of components, integrity of electrical connections, thermal management and manufacturability. Here are some detailed guidelines for designing ultra-thin CPU BGA substrates.
Precise layout of components
When designing an ultra-thin CPU BGA substrate, component layout is the most basic and important step. Designers need to ensure that the placement of individual components on the substrate is optimized to reduce signal delays and interference. The distance between components must be precisely calculated to avoid mutual interference and ensure signal integrity. De plus, designers need to consider the distribution of power and ground planes to provide a stable power supply and reduce electromagnetic interference (EMI).
Integrity of electrical connections
The integrity of electrical connections is a crucial aspect in ultra-thin CPU BGA substrate design. Designers need to ensure low impedance in all electrical connection paths to ensure high-speed signal transmission quality. This involves careful design of wire widths, spacing, and via arrangement. De plus,, designers need to perform signal integrity analysis (Signal Integrity Analysis) and use advanced CAD software to conduct simulations to identify and solve possible signal reflections, crosstalk, impedance mismatch and other issues.
Thermal management
Thermal management is another key factor in ultra-thin CPU BGA substrate design. Since the CPU generates a lot of heat during operation, this heat must be dissipated effectively to avoid overheating and damaging components. Designers can improve thermal management performance by optimizing thermal channel design, using highly thermally conductive materials, adding heat dissipation holes, and laying large ground planes. Thermal Simulation analysis (Thermal Simulation) tools can help designers predict heat distribution and hot spots, thereby optimizing heat dissipation design.
Manufacturability
Pendant le processus de conception, considering manufacturability is key to ensuring that ultra-thin CPU BGA substrates can be produced with high quality and low cost. Designers need to understand and follow the constraints of the manufacturing process, such as minimum line widths, line spacing, and via sizes. De plus,, the design of the substrate should simplify the production steps as much as possible to reduce potential errors and variations in the manufacturing process. Working closely with manufacturers can help designers understand the latest manufacturing processes and capabilities to optimize designs for mass production.
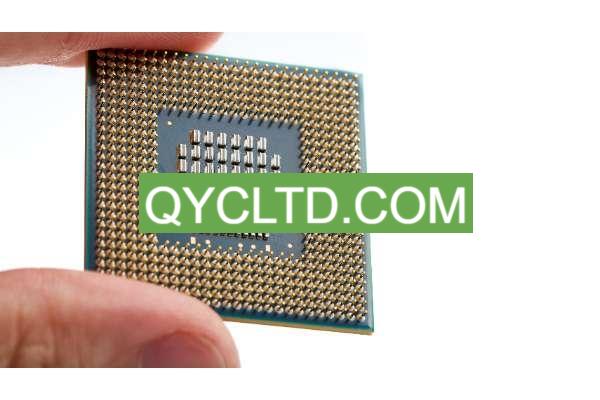
Ultra-Thin CPU BGA Substrates Manufacturer
Application of advanced CAD software
The use of advanced computer-aided design (CAD) software is standard practice for ultra-thin CPU BGA substrate design. These software tools provide powerful capabilities including layout design, signal integrity simulation, thermal simulation analysis and design rule checking (DRC). Through these tools, designers can conduct detailed design and optimization in a virtual environment, thereby improving the accuracy and reliability of the design.
En résumé, designing ultra-thin CPU BGA substrates requires comprehensive consideration of several key factors, including precise placement of components, integrity of electrical connections, Gestion thermique, et fabricabilité. By using advanced CAD software for detailed design and simulation, designers can ensure that the final product meets expected standards in terms of performance and reliability. The combination of these comprehensive considerations and tool applications allows ultra-thin CPU BGA substrates to play a vital role in modern electronic devices and promote the continuous advancement of technology.
What material is used in Ultra-Thin CPU BGA Substrates?
The successful application of ultra-thin CPU BGA substrate is inseparable from the support of high-performance substrates. These substrates are typically made from several key materials, including fiberglass-reinforced epoxy (FR4), Polyimide, and ceramic materials. Each material has its own unique advantages and can meet the stringent requirements of modern electronic devices for electrical performance, mechanical strength and ultra-thin structure.
Glass fiber reinforced epoxy resin (FR4)
FR4 is one of the most commonly used PCB Substrats, which is made of fiberglass cloth and epoxy resin. The glass fiber reinforced structure gives FR4 excellent mechanical strength and stability, able to withstand high temperatures and mechanical stress. This allows FR4 to provide sufficient rigidity and durability while maintaining an ultra-thin design. De plus,, FR4 has good electrical insulation properties and low dielectric constant, which can ensure the integrity of high-speed signal transmission and reduce signal loss and interference.
Polyimide
Polyimide is a high-performance organic polymer material widely used in high-end electronic substrates due to its excellent heat resistance and chemical stability. Polyimide maintains its physical and electrical properties at extreme temperatures, which is particularly important for electronic devices that need to operate in high-temperature environments. Due to its excellent flexibility and mechanical strength, polyimide is also used in the manufacture of flexible circuit boards, which is ideal for applications that require high flexibility and complex three-dimensional structures.
Ceramic material
Ceramic substrates, such as aluminum oxide (Al2O3) and aluminum nitride (Aln), are known for their high thermal conductivity and excellent electrical properties. Ceramic materials have extremely low dielectric losses and high dielectric strength, providing excellent performance in high-frequency applications. De plus,, the thermal expansion coefficient of ceramic substrates is similar to that of semiconductor materials, which can effectively reduce thermal stress and improve the reliability of electronic components. Although ceramic substrates are more expensive, they remain an essential material choice in applications that require extremely high thermal management and electrical performance.
Composite materials
In order to meet more complex and demanding application requirements, modern ultra-thin CPU BGA substrates may also use multi-layer composite materials. These composites combine the benefits of multiple substrates, such as polyimide or ceramic layers embedded between FR4 layers to improve overall thermal management and electrical performance. Composite material technology enables substrates to meet higher performance standards and application requirements while maintaining ultra-thin structures.
The high performance and versatility of ultra-thin CPU BGA substrates are inseparable from the support of advanced materials. Fiberglass-reinforced epoxy (FR4), Polyimide, and ceramic materials each provide superior electrical performance and mechanical strength while supporting complex and delicate ultra-thin structural designs. With the continuous development of electronic equipment, the performance requirements for substrate materials are also constantly increasing. In the future, we will see the application of more new materials and composite materials to further promote the development and application of ultra-thin CPU BGA substrate technology.
What size are Ultra-Thin CPU BGA Substrates?
Ultra-thin CPU BGA substrates are available in different sizes depending on the application, allowing for great flexibility and customization. In modern electronic devices, size and shape requirements vary, so ultra-thin CPU BGA substrates must be customized to specific CPU and device needs.
Premier, let’s take a look at the thickness of the ultra-thin CPU BGA substrate. The thickness of these substrates can typically range from a few microns to tens of microns. Due to their ultra-thin nature, they can be widely used in a variety of space-constrained devices, tels que les smartphones, Comprimés, and portable medical devices. Compared with traditional PCB, the thin design of ultra-thin CPU BGA substrate can make the device thinner, lighter and more portable, thus meeting the needs of modern consumers for portability.
Deuxièmement, the area and shape of the ultra-thin CPU BGA substrate are also important factors for customization according to specific application requirements. Due to the diversity and complexity of modern electronic devices, the shape of the substrate may be square, rectangular or other special shapes. The area depends on the number and layout of electronic components carried, as well as the required density of electrical connections. Some high-performance devices may require larger substrate areas to support more electronic components and complex connection structures, while some small portable devices may require smaller substrate sizes to accommodate their compact designs.
En général, the size design of ultra-thin CPU BGA substrate is a process that comprehensively considers many factors, including the functional requirements of the device, Exigences de performance, manufacturing costs, and the appearance and portability of the final product. Through flexible design and customization, ultra-thin CPU BGA substrates can meet the various size and shape requirements of different devices, providing important support for the development of modern electronic devices.
The Manufacturer Process of Ultra-Thin CPU BGA Substrates.
Manufacturing ultra-thin CPU BGA substrates is a complex and precise process that involves multiple critical steps to ensure the performance and reliability of the final product. Below are the detailed steps of the manufacturing process:
Substrate preparation
Before the manufacturing process can begin, a high-performance substrate needs to be prepared, usually fiberglass-reinforced epoxy (FR4) or other specialty materials. The quality and performance of the substrate are critical to the stability of the final product.
Layer alignment
When manufacturing multi-layer ultra-thin CPU BGA substrates, each layer must be precisely aligned to ensure proper connection of the conductive paths. This is usually achieved through optical alignment systems or mechanical positioning.
Etching or printing of conductive paths
Conductive paths are a critical part of connecting the CPU to other components. Dans cette étape, conductive paths are formed on the surface of the substrate through chemical etching or printing techniques, ensuring that electrical signals can be transmitted between various components.
Drilling of component holes
After the conductive paths are formed, holes need to be drilled into the substrate to mount the CPU and other electronic components. These holes must be precisely located and sized to ensure proper installation and connection of the components.
Solder ball placement
On the CPU mounting holes, the solder balls are fixed to the substrate through a soldering process at high temperatures. These solder balls provide the connection to the CPU, ensuring the transmission of electrical signals and the supply of power.
Final test
The final step in the manufacturing process is thorough testing of the ultra-thin CPU BGA substrate. Cela inclut les tests électriques, connectivity testing and thermal testing to ensure the substrate is functioning properly and meets specifications.
Each step requires strict quality control and precise operations to ensure the quality and reliability of the final product. Problems in any link may affect the performance of the entire product, so every detail in the manufacturing process must be handled with care. Through these steps, the ultra-thin CPU BGA substrate manufactured can meet the high performance and stability requirements of modern electronic equipment, and provide support and guarantee for various application fields.
The Application area of Ultra-Thin CPU BGA Substrates.
The application fields of ultra-thin CPU BGA substrates are very wide, and they play a key role in many fields, including consumer electronics, computers, communication equipment, automotive electronics and medical equipment. These substrates have become core components of modern technology products and play a vital role in various industries.
In the field of consumer electronics, ultra-thin CPU BGA substrates are widely used in products such as smartphones, Comprimés, wearable devices, and home appliances. Their small size, portability and high performance allow these devices to have more powerful functions and better performance.
In the computer field, ultra-thin CPU BGA substrates are a key component of high-performance computers, servers and data centers. These substrates support connections between processors, memory, and other critical components, ensuring the stability and performance of computer systems.
In the field of communication equipment, ultra-thin CPU BGA substrates are used to manufacture products such as routers, switches, base stations and network equipment. Their high-density connections and excellent electrical performance enable communication devices to achieve higher data transmission rates and more stable signal transmission.
Dans le domaine de l’électronique automobile, ultra-thin CPU BGA substrates are widely used in automotive control systems, infotainment systems, vehicle-mounted sensors and other equipment. They are able to withstand harsh environmental conditions and provide reliable electrical connections, ensuring the stability and safety of automotive electronic systems.
Dans le domaine de l’équipement médical, ultra-thin CPU BGA substrates are used to manufacture products such as medical imaging equipment, monitoring instruments, surgical robots, and implantable medical devices. These substrates support complex electronic systems and ensure the accuracy, reliability and safety of medical devices.
Bref, ultra-thin CPU BGA substrates play a vital role in various industries and have become an indispensable key component of modern technology products. With the continuous advancement of technology and the continuous expansion of application fields, ultra-thin CPU BGA substrates will continue to play an important role and promote the development and innovation of various industries.
What are the advantages of Ultra-Thin CPU BGA Substrates?
Ultra-thin CPU BGA substrate has a series of outstanding advantages compared to traditional printed circuit boards (PCB), which make it an indispensable key component in modern electronic equipment.
Premier, the small size and light weight of ultra-thin CPU BGA substrates make them ideal for portable and space-constrained devices. As electronic devices develop toward lighter and thinner devices, the emergence of ultra-thin substrates has effectively reduced the overall volume and weight of the device, improved portability, and enabled users to use these devices anytime and anywhere.
Deuxièmement, the ultra-thin CPU BGA substrate uses high-density connection technology, which can support higher-performance and more-functional CPUs than traditional PCBs. Through a more compact solder ball array layout, ultra-thin substrates can accommodate more connection points in the same or smaller space, thereby achieving higher data transmission rates and more input and output interfaces, providing more powerful devices Computing and processing power.
In addition to this, the ultra-thin CPU BGA substrate also exhibits excellent electrical and thermal performance. Using high-performance substrates and advanced manufacturing processes, these substrates can provide stable electrical characteristics and good thermal conductivity, effectively reducing circuit power consumption and temperature, and improving the overall reliability and performance stability of the device.
Finalement, the ultra-thin CPU BGA substrate also simplifies the device assembly process. Compared with traditional PCBs, ultra-thin substrates adopt a more compact design and simpler connection methods, which reduces the number and complexity of parts in the assembly process, reduces the risk of assembly errors, and improves production efficiency and product quality.
Pour résumer, ultra-thin CPU BGA substrate has become an indispensable key component in modern electronic equipment due to its small size, high-density connection, excellent electrical and thermal performance, and simplified assembly process, driving the continuous development of electronic technology. and innovation.
FAQ
What are the advantages of ultra-thin CPU BGA substrate over traditional PCB?
The ultra-thin CPU BGA substrate has smaller size and higher density, making it particularly suitable for modern compact electronic devices. They also provide improved electrical and thermal performance, as well as simplified assembly processes, helping to improve device reliability and performance.
Is the manufacturing process of ultra-thin CPU BGA substrate complicated?
Manufacturing ultra-thin CPU BGA substrates requires a series of precision processes, including substrate preparation, layer alignment, etching or printing of conductive paths, drilling of component holes, placement and testing of solder balls, and other steps. Although challenging, high-quality and efficient production can be achieved with the help of advanced manufacturing technology and strict quality control.
What are the main applications of ultra-thin CPU BGA substrate?
Ultra-thin CPU BGA substrates are widely used in various fields, including consumer electronics (tels que les smartphones, Comprimés), computers (such as supercomputers, Serveurs), communication equipment (such as network routers, base stations), Électronique automobile (such as car control systems) , car entertainment systems) et du matériel médical (tels que les équipements d’imagerie médicale, implantable medical devices), etc.
What key factors need to be paid attention to in the design of ultra-thin CPU BGA substrate?
When designing an ultra-thin CPU BGA substrate, many key factors need to be considered, including component layout and connection, electrical performance, Gestion thermique, mechanical strength, et fabricabilité. By using advanced CAD software for design and simulation, these factors can be effectively optimized to ensure the performance and reliability of the final product.
What is the future development trend of ultra-thin CPU BGA substrates?
As the performance, size and power consumption requirements of electronic devices continue to increase, ultra-thin CPU BGA substrates will continue to develop and evolve. Future trends may include higher density, thinner thickness, more advanced materials and manufacturing processes, and the integration of more functions to meet changing market needs and technical challenges.