What are Multi-Chip FC-BGA Package Substrates?
Multi-Chip FC-BGA Package Substrates Manufacturer.”Multi-Chip FC-BGA Package Substrates Manufacturer” describes a company specializing in producing advanced substrates for FC-BGA packages that integrate multiple semiconductor chips, ensuring high-density interconnectivity and performance reliability in electronic devices.
Multi-Chip FC-BGA Substrats d’emballage (Multi-core FC-BGA package substrate) is an advanced electronic packaging technology used to integrate multiple chips onto a package substrate to achieve high-density, high-performance electronic device design . This technology utilizes a ball grid array (BGA) packaging format to mount multiple chips on a package substrate and connect them to the motherboard through solder balls to provide reliable electrical connections and thermal management.
Multi-core FC-BGA packaging substrates are usually made of insulating materials, such as FR4 or polyimide, which have good electrical insulation and mechanical strength and are suitable for various application environments. Pendant le processus de fabrication, the substrate is precisely machined and assembled to ensure the correct positioning and connection of the chips. This technology not only allows designers to integrate multiple functional modules in a compact space, but also improves device reliability and performance.
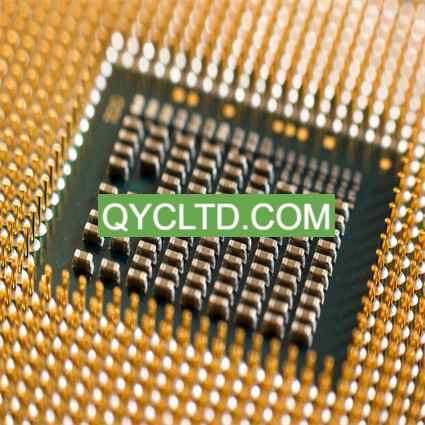
Multi-Chip FC-BGA Package Substrates Manufacturer
Multi-core FC-BGA packaging substrates are widely used in consumer electronics, communication equipment, industrial control, medical equipment and other fields, and are suitable for applications requiring high performance, high reliability and compact size. By using multi-core FC-BGA substrat d’emballage technology, designers can achieve product market competitiveness and improve production efficiency while meeting complex functional requirements.
Bref, multi-core FC-BGA packaging substrate represents the progress of modern electronic packaging technology, provides innovative solutions for various application fields, and promotes the development and progress of electronic equipment design.
Multi-Chip FC-BGA Package Substrates design Reference Guide.
Dans l’équipement électronique moderne, multi-core FC-BGA (Grille à billes) packaging substrates play a key role, providing reliable solutions for high performance and complex circuits. This guide will delve into the design principles and best practices of multi-core FC-BGA package substrates to help engineers and designers effectively create reliable circuit layouts.
Multi-core FC-BGA packaging substrate is an integrated circuit (IC) packaging technology that connects chips through a ball grid array (BGA) to realize the electrical connection of multiple chips within a compact package. This design not only improves the integration of the circuit, but also optimizes signal transmission efficiency and circuit performance.
When designing a multi-core FC-BGA packaging substrate, the following factors need to be considered:
Layout optimization: Reasonably lay out each chip and connection lines to minimize signal interference and crosstalk.
Thermal management: Effectively handle the heat that may be generated by multiple chips operating at the same time to ensure that the internal temperature of the package is stable.
Electromagnetic compatibility (EMC): Take necessary measures to reduce electromagnetic radiation and suppress external interference to ensure the stability and reliability of the circuit.
Multi-core FC-BGA packaging substrates usually use high-performance materials, such as FR4 or high-frequency materials, to meet different frequency and transmission speed requirements. For flexible packaging requirements, materials such as polyimide (PI) can be selected to ensure bending performance and long-term reliability.
Pendant le processus de conception, use advanced circuit design software and simulation tools (such as Cadence Allegro or Mentor Graphics PADS) for routing optimization and signal integrity analysis to ensure that the design meets expected performance indicators and manufacturing requirements.
The manufacturing process of multi-core FC-BGA packaging substrates involves multiple steps such as substrate preparation, solder ball installation, chip mounting, hot pressing packaging, surface treatment and testing. Each step needs to be strictly controlled to ensure the quality and reliability of the final product.
As an important part of modern electronic design, the design and implementation of multi-core FC-BGA packaging substrates require comprehensive consideration of key factors such as layout optimization, Gestion thermique, Sélection des matériaux, et les processus de fabrication. By studying this guide, readers can gain an in-depth understanding of the design principles and implementation techniques of multi-core FC-BGA packaging substrates, providing important reference and guidance for the successful implementation of future projects.
Through the above content, we hope to provide engineers and designers with valuable information and insights, and promote the application and development of multi-core FC-BGA packaging substrates in high-tech fields.
What material is used in Multi-Chip FC-BGA Package Substrates?
Multi-core FC-BGA packaging substrates usually use a variety of materials, which ensure performance and reliability while also meeting the needs of complex electronic devices. Some of the most common materials include:
R4 (glass fiber reinforced epoxy laminate): FR4 is one of the mainstream choices for manufacturing multi-core FC-BGA packaging substrates. It has excellent electrical insulation properties and mechanical strength, and can withstand the weight and vibration of electronic components while providing a stable working environment.
Polyimide (PI): Polyimide material is suitable for multi-core FC-BGA packaging substrates that require flexibility and high-temperature performance. The material’s ability to remain stable over a wide temperature range makes it suitable for specific applications such as aerospace and medical devices.
Metal substrate: Certain applications with high power and strict thermal management requirements may use metal substrates, such as aluminum or copper. The metal substrate provides excellent thermal conductivity, helping to effectively disperse heat and maintain the normal operating temperature of electronic components.
Plastic materials: For certain low-cost and lightweight requirements, multi-core FC-BGA packaging substrates may use special plastic materials, such as high-performance engineering plastics. These materials can achieve more complex design and assembly requirements while ensuring mechanical strength.
Pour résumer, the material selection of multi-core FC-BGA packaging substrate depends on the specific application needs and performance requirements. Different materials provide their own unique advantages, allowing multi-core FC-BGA packaging substrates to play an important role in various electronic devices, thereby promoting technological progress and innovation.
What size are Multi-Chip FC-BGA Package Substrates?
The dimensions of multi-core FC-BGA package substrates vary depending on their application areas and specific designs. These substrates play a key role in electronic devices, and their size and shape directly affect their application and performance in various devices.
Manière générale, multi-core FC-BGA packaging substrates can be designed into various sizes according to needs, ranging from small to large. Multi-core FC-BGA packaging substrates used in small electronic devices, tels que les smartphones, tablets and wearable devices, are usually very small to accommodate the compact design requirements of the device. These small substrates can effectively integrate multiple chips and components while minimizing the overall size of the device, helping to improve the portability and user experience of the device.
D’un autre côté, in large electronic equipment and industrial applications, such as servers, network equipment, industrial control systems, etc., the multi-core FC-BGA packaging substrate may be larger to accommodate more electronic components and complex circuit designs. These large substrates are often more complex in design to meet the high performance and stability requirements of the device.
Whether it is small or large, the size design of the multi-core FC-BGA package substrate must take into account the layout of electronic components, Gestion thermique, optimization of signal transmission, and the feasibility of production and manufacturing. Donc, size selection depends on specific application needs and device design requirements to ensure excellent performance and reliability in different scenarios.
Bref, multi-core FC-BGA packaging substrates come in a wide range of sizes and can be flexibly designed according to different application requirements, thereby meeting the requirements for high performance, compact design and reliable operation of various electronic devices.
The Manufacturer Process of Multi-Chip FC-BGA Package Substrates.
The manufacturing process of multi-core FC-BGA packaging substrates involves multiple critical steps, each of which is critical to the quality and performance of the final product.
Premier, the manufacturing process begins with the preparation phase of the substrate. This includes selecting an appropriate substrate material, typically FR4 or other specific material, to ensure good electrical insulation properties and mechanical strength. The surface of the substrate must be clean and flat so that subsequent process steps can proceed smoothly.
Next comes the deposition of the copper layer. The surface of the substrate is chemically covered with a thin layer of copper. This step is crucial because the copper layer will become the basis for subsequent circuit connections.
Photoresist application and exposure then proceed. Photoresist is coated on the copper layer and exposed to UV light through a photomask to form the desired circuit pattern. These patterns define wire paths and pad locations on the circuit board.
This is followed by an etching process that chemically removes the copper layer that is not protected by the photoresist, creating conductive paths and pads. This step requires precise control to ensure the accuracy and reliability of the circuit board.
This is followed by the drilling stage, where holes are drilled at specific locations to mount electronic components and connect the various interlayer circuits. The location and size of these holes must be precise to ensure that components can be installed correctly and connections between circuit layers are clear.
Next comes the installation and soldering of the components. Electronic components are placed precisely on the pads on the circuit board according to the design requirements and fixed by wave soldering or other soldering methods. This step is often accomplished with the help of automated equipment to improve production efficiency and product consistency.
Finalement, conduct testing and quality control. After soldering is completed, each circuit board undergoes rigorous functional testing and electrical characteristics testing to ensure it meets design specifications and performance requirements. Any defects discovered are recorded and corrected to ensure the quality and reliability of the final product.
Through the above steps, the multi-core FC-BGA packaging substrate has undergone a precise manufacturing process to ensure reliability and performance superiority in various applications, thereby supporting the innovation and development of modern electronic equipment.
The Application area of Multi-Chip FC-BGA Package Substrates.
Multi-core FC-BGA packaging substrates are widely used in multiple industries, and their unique designs and advantages make them an indispensable component in various electronic devices.
Tout d’abord, multi-core FC-BGA packaging substrates are widely used in the field of consumer electronics. High-end consumer electronics products such as smartphones, Comprimés, and wearable devices now commonly use multi-core FC-BGA packaging substrates to achieve compact design and high-performance requirements. These devices require the integration of multiple functions and high-density electronic components in a limited space. Multi-core FC-BGA packaging substrates meet these needs through optimized layout and efficient connection technology.
Deuxièmement, the communication field is also one of the main application fields of multi-core FC-BGA packaging substrates. In network equipment, base stations and communication servers, a large amount of data and signals need to be processed, and multi-core FC-BGA packaging substrates can provide high-speed data transmission and stability, and support complex communication protocols and functional requirements. These substrates not only improve the performance of the equipment, but also increase the reliability and efficiency of the network.
De plus,, multi-core FC-BGA packaging substrates also have important applications in automotive electronics and industrial control systems. In automotive electronics, they are used in in-vehicle infotainment systems, driver assistance systems and in-vehicle electronic control units (Écus), and in industrial control systems, in key applications such as automation equipment, robot control and sensor interfaces. Multi-core FC-BGA packaging substrates adapt to the needs of these harsh industrial environments through high temperature resistance, vibration resistance and long-term stability.
Finalement, the medical device and aerospace sectors are also increasingly adopting multi-core FC-BGA packaging substrates. Dans l’équipement médical, they are used in diagnostic equipment, medical monitoring systems and portable medical devices, providing reliable performance and precise data processing capabilities. In the aerospace field, multi-core FC-BGA packaging substrates are used in satellite communication equipment, avionics and spacecraft systems to ensure the lightweight and high integration of the equipment.
Bref, multi-core FC-BGA packaging substrate has become one of the indispensable key technologies in modern electronic equipment due to its flexible design, high performance and wide applicability. With the advancement of technology and the continuous expansion of application fields, it is expected that its application scope and influence will be further expanded and deepened in the future.
What are the advantages of Multi-Chip FC-BGA Package Substrates?
Tout d’abord, one of the main advantages of multi-core FC-BGA packaging substrate is its excellent compactness and space utilization. By integrating multiple chips on the same packaging substrate, the overall size and volume of electronic devices can be significantly reduced. This compact design is particularly suitable for products such as modern smartphones, tablets and wearable devices that require the smallest possible size and weight.
Deuxièmement, multi-core FC-BGA packaging substrates simplify the circuit design and assembly process by integrating multiple chips and components on a single substrate. This integration greatly reduces product complexity and reduces the number of connecting lines and connectors in the electronic system, thereby improving overall reliability and stability.
De plus,, the multi-core FC-BGA packaging substrate also provides superior electrical performance and signal transmission characteristics. By precisely controlling and optimizing circuit design, higher signal speeds and lower signal attenuation can be achieved, thereby improving device performance and response speed.
In terms of manufacturing, multi-core FC-BGA packaging substrates usually use advanced surface mount technology (SMT) and high-precision manufacturing processes to ensure product production quality and consistency. This not only improves production efficiency but also reduces manufacturing costs, making it ideal for mass production.
Finalement, the design flexibility and customizability of multi-core FC-BGA packaging substrates enable it to meet various complex circuit and functional integration requirements. Whether it is for high-performance computing equipment, communication equipment or industrial control systems, multi-core FC-BGA packaging substrates can provide customized solutions to meet the changing and growing market needs.
En résumé, multi-core FC-BGA packaging substrates, with their compact design, superior performance and flexible customization capabilities, have become an indispensable and important component in modern electronic equipment manufacturing, driving the continuous progress and innovation of technology.
FAQ
What are the main advantages of multi-core FC-BGA packaging substrate?
Multi-core FC-BGA packaging substrates are known for their compact design and high integration capabilities. Compared with traditional wiring methods, they can significantly reduce the size of the circuit board and achieve miniaturization and lightweight of the device. De plus,, automated production processes are adopted to ensure high quality and reliability, thereby increasing production efficiency and reducing costs.
What specific application fields are multi-core FC-BGA packaging substrates suitable for?
These packaging substrates are widely used in consumer electronics such as smartphones and tablets, as well as controllers and sensors in industrial fields. They also play an important role in fields such as communication equipment, Équipement médical, aerospace technology, and automotive electronics, supporting various complex electronic systems and equipment.
What is the design and manufacturing process of multi-core FC-BGA packaging substrate?
When designing a multi-core FC-BGA packaging substrate, engineers first consider the layout and connection methods of electronic components and use CAD software to complete the circuit design. The manufacturing process includes substrate preparation, copper layer deposition, photolithography and etching, forage, component mounting, and soldering and testing. These steps ensure the quality and performance of the final product.
What is the difference between multi-core FC-BGA packaging substrate and traditional PCB?
Traditional PCB usually uses surface mount technology (SMT) or through-hole technology, while multi-core FC-BGA packaging substrate connects chips through a ball grid array (BGA), which has higher connection density and better electrical signal transmission characteristics. This makes them perform better in high-frequency applications and complex circuit designs.
How to choose a suitable multi-core FC-BGA packaging substrate manufacturer?
When selecting a multi-core FC-BGA packaging substrate manufacturer, key factors include its reputation in the electronics industry, manufacturing capabilities, technical support and quality management system. Excellent manufacturers can provide customized design services to meet customers’ specific technical requirements and market needs.