What is Microtrace Antenna Circuit Board?
Microtrace Antenna Circuit Board Manufacturer.As a leading Microtrace Antenna Circuit Board Manufacturer, we specialize in crafting high-quality circuit boards with precision and expertise. Our advanced manufacturing processes ensure optimal performance and reliability for various applications.
Microtrace Antenna Circuit Board is a miniaturized printed circuit board specially designed for wireless communication equipment. In modern wireless communication technology, micro-antenna circuit boards play a vital role. Through precise design and manufacturing, they achieve the ability to efficiently transmit and receive signals in a limited space.
This type of circuit board is usually constructed from an insulating material such as fiberglass-reinforced epoxy (FR-4) to ensure the stability and durability of the circuit. Its surface is covered with a conductive material, usually copper, which connects electronic components by etching or printing precise conductive paths on an insulating substrate. These conductive paths are laid out and designed to maximize antenna performance to ensure efficient signal transmission and reception during wireless communications.
The design of a micro-antenna circuit board needs to consider many factors, including antenna type, frequency range, antenna impedance matching, etc. Through precise design and manufacturing, miniature antenna circuit boards can achieve efficient reception and transmission of signals at different frequencies, making them one of the core components of various wireless communication devices.
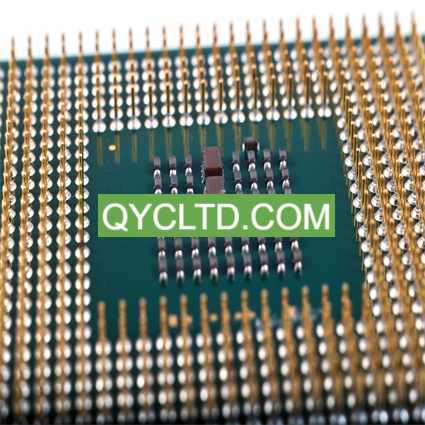
Microtrace Antenna Circuit Board Manufacturer
Bref, the micro-antenna circuit board is an indispensable component of modern wireless communication equipment. Its optimized design and efficient performance provide reliable wireless connection solutions for various application scenarios.
Microtrace Antenna Circuit Board design Reference Guide.
Designing a miniature antenna circuit board is a complex and critical task that requires consideration of multiple factors to ensure the performance and reliability of the final product. Here are the key points to note when designing a miniature antenna circuit board:
Component layout: Proper component layout is critical to the performance of the circuit board. During the layout process, the spacing, location, and orientation between components need to be considered to maximize signal transmission and reception efficiency. Especially when designing miniature antennas, attention should be paid to the positional relationship between the antenna and other components to avoid mutual interference.
Signal Integrity: Maintaining signal integrity is one of the key goals when designing a circuit board. This includes controlling the length and shape of the signal path to reduce signal attenuation and distortion. Through appropriate wiring and impedance matching, losses during signal transmission can be minimized and the stability and reliability of the system can be improved.
Compatibilité électromagnétique: Considering electromagnetic compatibility is an important aspect of designing micro antenna circuit boards. Through appropriate ground wire design, shielding measures and electromagnetic interference suppression technology, the impact of external interference on the system can be effectively reduced and the anti-interference capability and stability of the system can be improved.
Best practices: When designing micro antenna circuit boards, some best practice principles should be followed, such as standardized layout and connection methods, proper ground plane design, good heat dissipation and ventilation design, etc. These practices can help improve circuit board performance and reliability and reduce failure rates and maintenance costs.
Design Rules: Establishing clear design rules is one of the key steps to ensure that the board design meets the intended requirements. These rules include minimum distance requirements, minimum line width/line spacing requirements, maximum current capacity, etc. By strictly adhering to these rules, potential design issues and performance instability can be avoided.
Design Software Tools: Using appropriate design software tools is key to designing miniature antenna circuit boards. Commonly used design software, such as Altium Designer, Cadence Allegro, etc., provide a wealth of design functions and simulation tools, which can help designers quickly and accurately complete circuit board design and simulation analysis.
Designing a micro-antenna circuit board requires considering multiple factors such as component layout, Intégrité du signal, and electromagnetic compatibility to ensure efficient and reliable performance of the final product. By following best practices, establishing clear design rules, and using appropriate design software tools, designers can efficiently complete circuit board designs and ensure that they meet expected requirements and standards.
What material is used in Microtrace Antenna Circuit Board?
Micro-antenna circuit boards are an indispensable part of today’s wireless communication equipment, and their material selection is crucial, directly affecting their performance and scope of application. Typiquement, the main materials used in micro-antenna circuit boards include fiberglass-reinforced epoxy (FR-4) and flexible polymers (such as polyimide).
Premier, fiberglass-reinforced epoxy (FR-4) is one of the most common substrates for micro-antenna circuit boards. FR-4 has good mechanical strength and electrical insulation properties, can effectively support various components on the circuit board, and provide stable electrical performance. Its resistance to heat and chemicals also makes it ideal for many applications. Due to its relatively low cost, FR-4 is widely used in most miniature antenna circuit boards.
Deuxièmement, for some special application scenarios, such as those requiring higher heat resistance or flexibility, flexible polymers may be used as the base material of micro-antenna circuit boards. Flexible polymers such as polyimide offer excellent high temperature resistance and flexibility, allowing them to adapt to complex design needs. De plus,, the use of flexible materials can also reduce the overall weight and volume of the circuit board and increase the portability and flexibility of the device.
En résumé, the material selection for micro-antenna circuit boards depends on specific application needs and design requirements. Whether traditional FR-4 materials or flexible polymers are used, they can provide stable and reliable performance for wireless communication equipment and play an important role in different application scenarios.
What size are Microtrace Antenna Circuit Board?
As a key electronic component, micro-antenna circuit boards have diverse size requirements in different application scenarios. The determination of its size is affected by both the needs of the specific application and the design requirements.
Premier, for portable devices, tels que les smartphones, Comprimés, etc., micro-antenna circuit boards need to be extremely small in size to fit into the compact design of the device. This requires that the size of the circuit board can accommodate the necessary antenna elements in a limited space, and the layout must be coordinated with other electronic components to ensure the thinness and portability of the overall device.
Second, for areas such as industrial equipment or communications infrastructure, micro-antenna circuit boards may need to be slightly larger in size. This is because in industrial environments, equipment is usually more complex and requires more functional modules and connection interfaces, so larger circuit board space is required to accommodate these components and ensure good heat dissipation and signal transmission performance.
In the actual design process, engineers need to comprehensively consider many factors, such as the operating frequency of the antenna, signal transmission distance, environmental conditions, and overall device dimensions, to determine the optimal size of the micro-antenna circuit board. En même temps, factors such as manufacturing cost, production process, and reliability also need to be considered to ensure the practicality and feasibility of the design.
En général, the size of the micro-antenna circuit board has a certain degree of flexibility and can be adjusted according to specific application needs and design requirements. Whether you are pursuing ultimate thinness and portability, or requiring high performance and reliability, the application of micro antenna circuit boards in different fields can be realized through reasonable size design.
The Manufacturer Process of Microtrace Antenna Circuit Board.
The manufacturing process of micro antenna circuit boards is a complex and precise process involving multiple steps to ensure the quality and performance of the circuit boards meet requirements. This process is described in detail below.
Premier, the first step in manufacturing a micro-antenna circuit board is substrate preparation. Typiquement, Résine époxy renforcée de fibre de verre (FR-4) is used as the base material. This substrate has excellent mechanical strength and electrical insulation properties, making it suitable for most applications. Substrate preparation includes cleaning and treating the substrate surface to ensure smooth progress of subsequent processes.
Next comes the copper pattern etching or printing. This step is to form a circuit pattern on the surface of the substrate to achieve conductive connections between electronic components. In traditional manufacturing methods, chemical etching techniques are used to ultimately form the desired conductive paths by exposing and developing photosensitizer-coated copper foil. In modern technology, printing technology can also be used to directly print conductive ink on the surface of the substrate to form a circuit pattern.
This is followed by the component assembly phase. À ce stade,, electronic components will be installed onto the circuit board to complete the functionality of the entire circuit. These components can be mounted via surface mount technology (SMT) or via cavity mount technology. SMT technology can achieve high-density component layout and improve the integration and performance of circuit boards; while hole mounting technology is suitable for components that require additional mechanical support or heat dissipation.
The last step is quality inspection. At the final stage of the manufacturing process, the finished product must undergo rigorous quality inspection to ensure that the performance and reliability of the circuit board meet standard requirements. This includes visual inspection, welding quality inspection, electrical testing and many other aspects. Only by passing strict quality inspection can the quality and reliability of circuit boards be guaranteed and then put into market application.
Pour résumer, the manufacturing process of micro-antenna circuit boards goes through multiple steps such as substrate preparation, copper pattern etching or printing, component assembly, and quality inspection. With the development of modern technology, the circuit board design is more compact, complex, and high-performance. More superior.
The Application area of Microtrace Antenna Circuit Board.
As the core component of modern electronic equipment, micro antenna circuit boards play an important role in various industries. Its wide range of applications covers consumer electronics, automotive, aérospatial, Équipement médical, telecommunications and industrial automation.
In the consumer electronics industry, micro-antenna circuit boards are widely used in portable devices such as smartphones, Comprimés, and smart watches. They provide wireless communication functions for these devices, including Wi-Fi, Bluetooth, GPS, etc., allowing users to implement functions such as data transmission, positioning and navigation.
In the automotive industry, miniature antenna circuit boards are used in vehicle communication systems, navigation systems, and in-car entertainment systems. They can support inter-vehicle communication, in-vehicle infotainment, navigation and positioning and other functions, improving driving experience and safety.
Micro antenna circuit boards are also widely used in the aerospace field and are used in communication, navigation and control systems of aircraft, satellites and other aircraft. These circuit boards are lightweight and reliable, ensuring the stability and reliability of communications in complex aerial environments.
Dans le domaine de l’équipement médical, micro-antenna circuit boards are used in medical monitoring equipment, remote diagnosis systems and other equipment. They can support wireless data transmission, realize real-time monitoring and remote diagnosis of medical data, and improve the efficiency and quality of medical services.
The telecommunications industry uses micro-antenna circuit boards in base stations, communication networks and other equipment to support the coverage and transmission of wireless communications. These circuit boards can provide stable signal transmission and coverage to meet the communication needs of different regions and scenarios.
The field of industrial automation is also inseparable from the application of micro-antenna circuit boards. They are used in industrial control systems, sensor networks and other equipment to achieve wireless communication and data exchange between equipment, improving production efficiency and automation levels.
En général, micro-antenna circuit boards play a key role in multiple industries and have become an indispensable part of modern electronic equipment, driving technological innovation and development in various industries.
What are the advantages of Microtrace Antenna Circuit Board?
Micro-antenna circuit boards have significant advantages over traditional wiring methods in many aspects. These advantages not only improve the performance of the circuit board, but also improve the quality and reliability of the overall electronic device.
Premier, the compactness of the miniature antenna circuit board is one of its outstanding advantages. By integrating complex circuitry into a compact design, micro-antenna circuit boards can accommodate more functionality and components in a limited space. This compact design makes electronic devices lighter and more portable, and can better adapt to the needs of modern consumer electronics for miniaturization and portability.
Deuxièmement, the micro antenna circuit board has high reliability. A standardized manufacturing process results in consistent quality and performance for each micro antenna circuit board. This consistency ensures stable operation of the board under a variety of environmental conditions and reduces failure rates due to manufacturing differences, thereby increasing device reliability and longevity.
Troisième, the assembly of micro-antenna circuit boards is more convenient and efficient. With the help of automated production processes, electronic components can be installed directly on the circuit board accurately and quickly, greatly shortening the production cycle and cost. This efficient assembly process not only improves production efficiency, but also reduces the possibility of human error and ensures the stability of product quality.
De plus, the micro antenna circuit board excels in signal integrity. By providing controlled impedance and effectively reducing electromagnetic interference (EMI), miniature antenna circuit boards ensure the reliability and stability of signal transmission. This is especially important for wireless communications and high-frequency applications, which require high signal accuracy and stability.
Finalement, micro-antenna circuit boards are highly scalable. Its design can be easily expanded or contracted to accommodate different functional requirements or production volume needs. This flexibility makes miniature antenna circuit boards ideal for a variety of electronic devices, from small consumer electronics to large industrial equipment, to meet their specific design and performance requirements.
En résumé, micro-antenna circuit boards have become an indispensable key component in modern electronic equipment due to their compactness, reliability, efficiency, stability and flexibility, promoting the continuous development and progress of electronic technology.
FAQ
What is the difference between single-sided, double-sided and multi-layer circuit boards?
Single-sided circuit boards have conductor paths on only one side, double-sided circuit boards have conductor paths on both sides, and multi-layer circuit boards have conductor paths on multiple levels. Multilayer circuit boards allow for more complex circuit designs, but at a higher cost.
How do you choose the right circuit board substrate for a specific application?
When selecting a substrate, factors such as electrical performance, mechanical strength, thermal performance and environmental suitability need to be considered. Commonly used substrates include FR-4 (for general applications), Polyimide (for high temperature stability), and flexible polyimide (for curved or tight spaces).
What are the factors that affect circuit board manufacturing costs?
Cost factors include board selection, board thickness, Nombre de couches, surface treatment, line density, production volume and complexity, etc. More layers, higher line density and special surface treatments often increase costs.
What are the environmental considerations related to circuit board production and disposal?
The circuit board manufacturing process involves some chemicals and energy consumption, so attention needs to be paid to environmentally friendly production methods. When discarded, appropriate recycling and disposal measures should be taken to reduce environmental impact.