Alumina substrate Manufacturer.As a leading Alumina substrate manufacturer, we specialize in producing high-quality substrates for advanced electronic applications. Our state-of-the-art facilities and rigorous quality control ensure exceptional thermal conductivity, mechanical strength, and electrical insulation properties. We cater to diverse industries, including telecommunications, automotive, and aerospace, providing customized solutions that meet the most demanding specifications. Partner with us to experience innovative designs and reliable performance in your electronic components.
Alumina substrates, composed primarily of aluminum oxide (Al2O3), are widely used in electronics for their exceptional thermal and electrical insulating properties. These substrates are integral to various high-performance applications where reliability, Gestion thermique, and electrical insulation are paramount. This article delves into the properties, structure, materials, Processus de fabrication, applications, and advantages of alumina substrates.
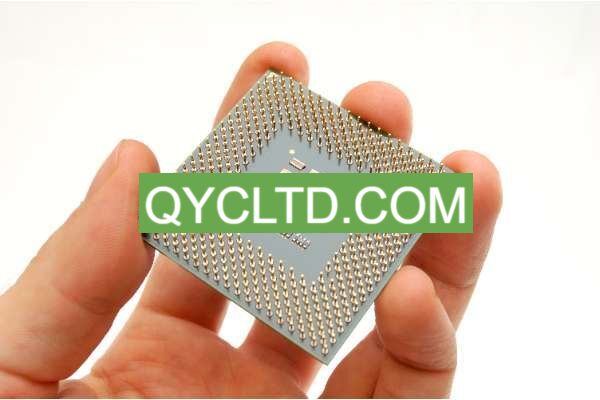
Alumina substrate Manufacturer
Structure of Alumina Substrates
Alumina substrates are engineered to provide optimal performance in demanding environments:
Le substrate is primarily composed of aluminum oxide, offering high thermal conductivity and excellent electrical insulation.
Typiquement, alumina substrates have a smooth, polished surface to enhance the adhesion of thin films and metallization layers.
Thin metal layers (e.g., gold, silver, or copper) are deposited onto the alumina surface for electrical connections and component mounting.
Additional coatings may be applied to protect the substrate from environmental factors and mechanical damage.
Materials Used in Alumina Substrates
Key materials used in alumina Substrats include:
The primary material, known for its high thermal conductivity, excellent electrical insulation, and mechanical strength.
Metals like gold, silver, and copper are used for creating conductive paths and contact points on the substrate.
Materials such as silicon nitride or silicon dioxide can be used to protect the substrate and metallization layers from oxidation and wear.
Manufacturing Process of Alumina Substrates
The manufacturing process of alumina substrates involves several precise steps:
High-purity alumina powder is prepared, often including additives to enhance specific properties.
The alumina powder is formed into a green body using techniques such as tape casting, pressing, or extrusion.
The green body is sintered at high temperatures to achieve densification, creating a solid, robust substrate.
The sintered substrate is polished to achieve a smooth surface, improving the adhesion of subsequent layers.
Metal layers are deposited onto the substrate using techniques such as sputtering, evaporation, or electroplating to create electrical connections and contact points.
Photolithography and etching processes define the conductive paths and contact areas on the metallized surface.
Additional protective coatings may be applied to enhance durability and reliability.
Applications of Alumina Substrates
Alumina substrates are used in a wide range of applications, including:
Used as substrates for integrated circuits (ICs), LEDs, and other microelectronic components due to their excellent thermal and electrical properties.
Utilized in power modules and components that require efficient thermal management and high electrical insulation.
Deployed in automotive sensors, control units, and other electronic systems that demand reliability and thermal performance.
Used in RF and microwave circuits for their low dielectric loss and high thermal conductivity.
Applied in medical implants and diagnostic equipment where biocompatibility and electrical insulation are crucial.
Advantages of Alumina Substrates
Alumina substrates offer several significant advantages:
Efficient heat dissipation, crucial for high-power and high-frequency applications.
Superior dielectric properties prevent electrical leakage and interference.
Robust and durable, making them suitable for harsh environments and demanding applications.
Resistant to oxidation, corrosion, and other chemical reactions, ensuring long-term reliability.
Widely available and relatively inexpensive compared to other high-performance ceramic materials.
FAQ
What makes alumina substrates suitable for high-power applications?
Alumina substrates are ideal for high-power applications due to their high thermal conductivity, which allows for efficient heat dissipation, and their excellent electrical insulation properties, which prevent electrical leakage and interference.
How do alumina substrates compare to other ceramic substrates like aluminum nitride?
Alumina substrates are generally more cost-effective and offer good thermal and electrical properties. Aluminum nitride substrates, while more expensive, provide higher thermal conductivity, making them suitable for applications requiring superior thermal management.
What industries benefit most from using alumina substrates?
Industries such as microelectronics, power electronics, automotive, telecommunications, and medical devices benefit significantly from the use of alumina substrates due to their reliable performance in thermal management and electrical insulation.
How are alumina substrates manufactured to ensure high quality and reliability?
Alumina substrates are manufactured through a meticulous process that includes powder preparation, forming, frittage, surface preparation, metallization, patterning, and protective coating. Each step is carefully controlled to ensure the highest quality and reliability of the final product.