What is AI Accelerator Module Substrate?
AI Accelerator Module Substrate Manufacturer.As an AI Accelerator Module Substrate Manufacturer, we specialize in producing high-performance substrates tailored for artificial intelligence applications. Our substrates are designed to enhance the efficiency and reliability of AI accelerators, ensuring optimal performance in data centers, autonomous vehicles, and advanced computing systems. With cutting-edge technology and rigorous quality control, we provide substrates that meet the demanding requirements of modern AI infrastructure.
The AI accelerator module substrate is a circuit board substrate specially designed for artificial intelligence (AI) hardware accelerators. In AI applications, large amounts of data and complex computing tasks usually need to be processed, and traditional central processing units (CPUs) or graphics processing units (GPUs) may not be able to meet the real-time and efficiency requirements. Donc, the AI accelerator module substrate came into being.
This substrate is usually made of high-performance materials to meet high-speed signal transmission and stability requirements. It not only provides electrical connections to enable effective communication between various electronic components, but also provides mechanical support to ensure that the accelerator module does not suffer mechanical damage or failure during use.
The design of the AI accelerator module substrate takes into account factors such as thermal management, Distribution d’énergie, and high-speed signal transmission. To enable high-performance computing, substrates often feature multi-layer designs and are equipped with efficient heat dissipation systems to ensure stable temperatures over long periods of operation.
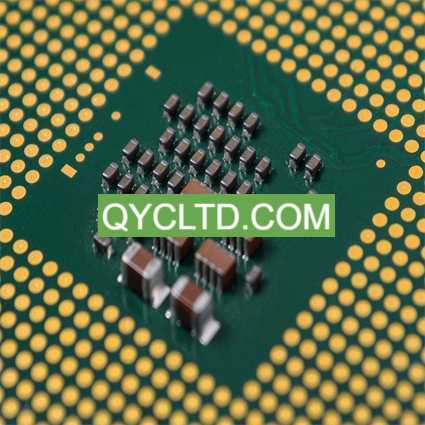
Showa Denko MCL-E-795G Package Substrate Manufacturer
En général, the AI accelerator module substrate is a crucial component of the AI system. It provides a stable operating environment for the AI hardware accelerator and provides strong support for the real-time performance and efficiency of various AI applications.
AI Accelerator Module Substrate design Reference Guide.
Designing an AI accelerator module substrate is a complex and critical task that requires comprehensive consideration of multiple factors to ensure its performance and stability. Here are the key takeaways from the Design Reference Guide:
AI accelerator modules often need to handle a large number of computing tasks, so thermal management is critical. Design should consider how to effectively dissipate heat to avoid the impact of overheating on performance. This may involve selecting appropriate heat dissipation materials, designing heat dissipation structures, and ensuring good air flow.
In the AI accelerator module, the transmission of high-speed signals may be affected by interference or attenuation, thus affecting system performance. Donc, when designing the substrate, attention needs to be paid to the layout and length matching of the signal transmission lines to minimize signal distortion and crosstalk.
AI accelerator modules may need to handle large amounts of power, so the design of power distribution is critical. When designing, you need to consider the power consumption characteristics of different components, rationally allocate power lines, and take appropriate measures to reduce power noise and fluctuations.
AI accelerator modules usually need to work under various environmental conditions, so the mechanical strength of the substrate is crucial. Appropriate substrate material and thickness should be selected during design, and mechanical assembly and fixation needs should be taken into consideration to ensure that the substrate has sufficient strength and stability.
Pendant le processus de conception, designers can leverage various design rules and software tools to optimize substrate performance. Par exemple, thermal management and signal transmission are simulated and analyzed through simulation software to find the best design solution. De plus,, proper use of design rules and guidelines can ensure that the substrate design complies with industry standards and best practices, thereby improving the reliability and stability of the design.
Bref, designing the AI accelerator module substrate requires comprehensive consideration of factors such as thermal management, signal transmission, Distribution d’énergie, and mechanical strength. By referring to the best practices and design rules provided in the guide, designers can better optimize substrate performance and ensure stable operation in high-performance computing tasks.
What material is used in AI Accelerator Module Substrate?
When designing the AI accelerator module substrate, it is crucial to choose the appropriate material, because the choice of material directly affects the performance and stability of the substrate. The following are commonly used AI accelerator module substrate materials:
FR-4 is one of the most common substrate materials and has good electrical properties and mechanical strength. Due to its affordability and ease of processing, FR-4 is widely used in various types of circuit boards. Its characteristics make it a good choice for general purpose performance, especially for low and mid-frequency applications where FR-4 is a cost-effective choice.
Ceramic substrates have excellent thermal conductivity and high-frequency performance, which makes them excellent in high-power and high-frequency applications. Due to its ability to effectively dissipate heat and provide good signal integrity, ceramic substrates are often used in applications requiring high performance and stability, such as high-speed communication equipment, radar systems and radio frequency circuits.
High-frequency materials have excellent dielectric properties and low-loss characteristics, are suitable for high-speed signal transmission, and can effectively reduce signal loss and interference. Polytetrafluoroethylene (PTFE) is a commonly used high-frequency material that performs well in microwave and millimeter-wave frequency bands and is therefore widely used in high-frequency applications such as communication systems and radar.
Selecting the appropriate substrate material depends on the requirements and performance specifications of the specific application. Pendant le processus de conception, design engineers need to comprehensively consider factors such as the material’s electrical properties, thermal properties, mechanical strength, and cost to ensure that the final substrate design meets the expected performance and reliability requirements.
What size are AI Accelerator Module Substrate?
The size of the AI accelerator module substrate varies depending on the application needs, and its size is usually determined by factors such as required computing power, cooling requirements, and available installation space. When designing the AI accelerator module substrate, engineers need to consider these factors to ensure that the substrate can meet the requirements of the specific application.
For applications that require processing of large data sets and complex algorithms, such as deep learning tasks in data centers or real-time image recognition for autonomous driving systems, larger substrate sizes are often chosen. Such a substrate can accommodate more processing units (such as GPUs or TPUs), memory modules, and other auxiliary circuits, and provide sufficient heat dissipation surface area to effectively dissipate heat.
En même temps, in some compact applications, such as embedded smart cameras or portable medical devices, the size of the substrate may be smaller. Despite their smaller size, these substrates still need to ensure adequate performance and stability, so higher-density integrated circuit designs and advanced heat dissipation technologies may be used.
In addition to processing power and cooling requirements, substrate size is also affected by installation space constraints. In some specific application scenarios, such as in-vehicle equipment or robotic systems, the installation space may be severely restricted, so smaller substrates need to be designed to adapt to these environments.
En général, the size selection of the AI accelerator module substrate needs to comprehensively consider factors such as performance, dissipation de chaleur, and installation space. Through reasonable sizing design, the substrate can be ensured to operate stably under high computing loads and meet the needs of specific applications.
The Manufacturer Process of AI Accelerator Module Substrate.
Manufacturing AI accelerator module substrates is a complex and precise process that requires multiple critical steps to ensure the performance and reliability of the final product. The following are the key steps in manufacturing the AI accelerator module substrate:
Substrate Preparation: This process involves selecting the appropriate material and cutting it into the required size of the substrate. Commonly used substrate materials include FR-4, ceramics and high-frequency materials. Each material has different electrical properties and mechanical strength, so choosing the right substrate is crucial.
Pattern Etching: Patterning copper circuits on the surface of a substrate is one of the key steps in the manufacturing process. This is usually achieved through photolithography or direct imaging techniques. Premier, a layer of photosensitive adhesive is applied to the surface of the substrate, and a pattern mask is used to expose the photosensitive adhesive to UV light. Alors, the unexposed copper material is removed through chemical etching or physical etching to form the desired circuit pattern.
Lamination and stacking: For multi-layer substrates, each layer of circuit boards needs to be stacked together through a lamination process. Dans ce processus, the substrate and copper foil of each layer are heated and compressed together to make them tightly bonded together. This stacked structure provides higher circuit density and complexity, suitable for applications requiring more functions and connections.
Component mounting: Once the copper circuit pattern of the substrate is formed, electronic components can be mounted on it. This is usually done via surface mount technology (SMT) or through-hole technology. In the SMT process, components are pasted directly onto the substrate surface and secured with hot melt or UV-curable glue. In through-hole technology, the component’s pins are passed through the holes in the substrate and soldered on the bottom to ensure a stable connection.
Quality Inspection: Finalement, the final stage of the manufacturing process is stringent quality inspection of the substrates. This includes electrical testing and mechanical testing to ensure the correctness and stability of circuit connections, as well as the mechanical strength and appearance quality of the substrate. Any defects or defective products will be identified and repaired or eliminated to ensure that the quality of the final product meets the design requirements.
Through the above key steps, the process of manufacturing AI accelerator module substrates can ensure high-quality, high-performance final products, providing reliable support and guarantee for the development and application of AI technology.
The Application area of AI Accelerator Module Substrate.
AI accelerator module substrate is a key component in today’s technology field. Its application range covers many fields, bringing intelligent and efficient solutions to all walks of life.
In the field of data centers, AI accelerator module substrates play a key role. Data centers need to process large-scale data and perform complex AI training and inference tasks. The AI accelerator module substrate effectively supports the implementation of these tasks by providing high-performance computing capabilities, accelerating the data analysis and decision-making process.
Autonomous driving technology is gradually becoming a mainstream trend in the automotive industry, and the AI accelerator module substrate is one of the core components for realizing autonomous driving systems. These substrates support vehicle-mounted AI systems, which enable vehicles to perceive the environment, make intelligent decisions, and achieve autonomous driving through real-time data processing and decision-making, thus improving driving safety and driving comfort.
In the medical field, the application of AI technology is constantly expanding, especially in image processing and diagnostic assistance. The AI accelerator module substrate provides high-precision image processing capabilities for medical equipment, helping doctors diagnose diseases and plan treatment. Through AI-based medical equipment, diagnostic accuracy and treatment effects can be improved, providing patients with better medical services.
Industrial automation is another important application field, and AI accelerator module substrates also play an important role in it. These substrates can be integrated into production lines to improve the intelligence level of the production line and optimize production efficiency. Through real-time data analysis and intelligent decision-making, industrial automation systems can better respond to changes in market demand and improve production efficiency and product quality.
Pour résumer, AI accelerator module substrates play an important role in many fields such as data centers, autonomous driving, Équipement médical, and industrial automation, bringing new opportunities and challenges to the development of various industries. With the continuous development of AI technology and the continuous expansion of application scenarios, AI accelerator module substrates will continue to play a key role in promoting technological progress and social development.
What are the advantages of AI Accelerator Module Substrate?
The AI accelerator module substrate is a key component in promoting artificial intelligence applications. Its excellent performance and stability provide a solid foundation for the development of AI systems. The following are several significant advantages of AI accelerator module substrates:
High performance: The AI accelerator module substrate provides excellent signal integrity and low latency by optimizing the circuit layout and signal transmission path, and can meet the needs of high-speed computing and large-scale data processing. Its precision design and high-speed signal processing capabilities enable AI systems to perform data analysis and decision-making faster and more accurately, thereby improving the performance and efficiency of the entire system.
Reliability: The AI accelerator module substrate uses high-quality materials and strictly follows advanced manufacturing processes to ensure that the module operates stably under various environmental conditions and has long-term reliability. Substrates that have undergone rigorous testing and quality control can effectively withstand electrical noise, temperature changes and mechanical stress, ensuring system stability and sustained performance.
Heat dissipation performance: The AI accelerator module substrate adopts excellent thermal management design to effectively dissipate heat and prevent overheating from affecting system performance. Through reasonable heat dissipation design and heat dissipation structure, the substrate can effectively conduct and discharge the generated heat, ensuring that the chip and electronic components remain within a safe operating temperature range during long-term high-load operation, thus ensuring the stability and reliability of the system. sex.
Scalability: The AI accelerator module baseboard adopts a modular design and has good scalability, making it easy for system upgrades and expansions. Through standardized interfaces and modular design, users can easily add or replace modules to achieve flexible expansion and customized configuration of system functions to meet changing needs in different application scenarios and improve the flexibility and customizability of the system.
Pour résumer, the AI accelerator module substrate provides stable and reliable hardware support for various artificial intelligence applications with its advantages such as high performance, reliability, excellent heat dissipation performance and scalability, and promotes the continuous development of artificial intelligence technology. and application expansion.
FAQ
How to choose a suitable substrate material?
Several factors need to be considered when selecting a substrate material. Premier, ensure that the material has good electrical properties and can meet the requirements of high-speed signal transmission. Deuxièmement, mechanical strength is also an important consideration, especially if you need to support large heat sinks or other accessories. De plus,, thermal conductivity is critical to heat dissipation performance, so selecting materials with good thermal conductivity is necessary. Commonly used materials such as FR-4, ceramics and high-frequency materials have their own advantages and disadvantages, and selections need to be made based on specific application requirements.
What factors affect the manufacturing cost of AI accelerator module substrates?
Manufacturing costs are affected by many factors. The first is material selection. The costs of different materials vary greatly, and some special materials may require more complex processing techniques, leading to increased costs. Deuxièmement, process complexity is also an important factor. Par exemple, the manufacturing of multi-layer boards will be more complicated than single-layer boards, so the cost will increase accordingly. De plus,, production batch size also affects costs. Manière générale, high-volume production can reduce the manufacturing cost of each substrate.
How to deal with the heat dissipation problem of the substrate?
The heat dissipation issue of the substrate is an aspect that needs to be paid attention to when using the AI accelerator module. To manage heat effectively, several measures can be taken. Premier, optimize the substrate design, rationally layout the heat sink and heat dissipation holes, and improve the heat conduction efficiency. Deuxièmement, choosing materials with good thermal conductivity, such as copper or aluminum, can help speed up the conduction and dissipation of heat. De plus,, adding heat dissipation devices, such as fans or thermal conductive films, can also effectively reduce the temperature of the substrate and ensure stable operation of the system.