What is Flip Chip Ball Grid Array Substrate?
Flip Chip Ball Grid Array Substrate Manufacturer. A Flip Chip Ball Grid Array (FCBGA) Substrate Manufacturer specializes in producing advanced packaging solutions for semiconductor devices. These manufacturers create substrates that provide electrical connections and mechanical support for flip chip technology, enabling high performance, reliability, and miniaturization in electronic components used in a wide range of applications, from consumer electronics to telecommunications and automotive systems. Their expertise ensures efficient heat dissipation and optimal signal integrity, catering to the growing demand for sophisticated microelectronics.
FCBGA substrate (Flip Chip Ball Grid Array Substrate) is an advanced circuit board design that plays a vital role in modern electronic devices. This substrate is designed to connect and support Flip Chip packaged chips, which play an important role in the integrated circuit industry. Compared with traditional surface mount technology, FCBGA substrate adopts a more advanced Ball Grid Array (BGA) structure. In this structure, the chip is flipped over and connected directly to the substrate through solder balls, rather than placing the chip on the substrate and then connecting it like the traditional method.
This direct-connect design brings multiple advantages. First, it enables higher performance because a direct connection reduces the path length and impedance of signal transmission, thereby increasing signal transmission rate and stability. Secondly, the design of the FCBGA substrate also achieves higher integration density. Because the chip is directly connected to the substrate without the need for additional connecting wires or pads, more functions and components can be implemented in a limited space. This high integration density is crucial for miniaturization and lightweighting of modern electronic devices.
In addition, FCBGA substrates also have excellent thermal performance and reliability. Because the chip is directly connected to the substrate, heat can be conducted more efficiently from the chip to the substrate, thereby improving heat dissipation efficiency. In addition, direct connection reduces the risk of failure due to breakage of connecting wires or pads, improving device reliability and stability.
Overall, FCBGA substrate plays a key role in modern electronic devices, and its advanced design and superior performance make it an ideal choice for many high-end electronic products. As technology continues to develop, FCBGA substrates will continue to drive innovation and progress in the electronics industry.
Flip Chip Ball Grid Array Substrate design Reference Guide.
FCBGA substrate design is a complex and critical process, which directly affects the performance and stability of electronic devices. During the design process, several factors need to be considered, including electrical routing, thermal management, and mechanical support. A comprehensive design reference guide provides engineers with key principles and best practices to ensure designs achieve expected performance and reliability.
First, electrical routing is one of the key considerations in FCBGA substrate design. Good electrical wiring design can ensure the stability and reliability of signal transmission. During the wiring process, attention needs to be paid to issues such as signal transmission matching impedance, signal integrity, and crosstalk to minimize signal loss and interference and improve the system’s anti-interference ability.
Secondly, thermal management is an important aspect that cannot be ignored in FCBGA substrate design. Modern electronic devices often have high power densities and tend to generate large amounts of heat. Therefore, designers need to consider how to effectively dissipate heat to prevent chips and other critical components from overheating and affecting performance and lifespan. In terms of thermal management, technologies such as heat sinks, heat sinks, fans, and thermal conductive materials can be used to ensure stable operation of the system under various working conditions.
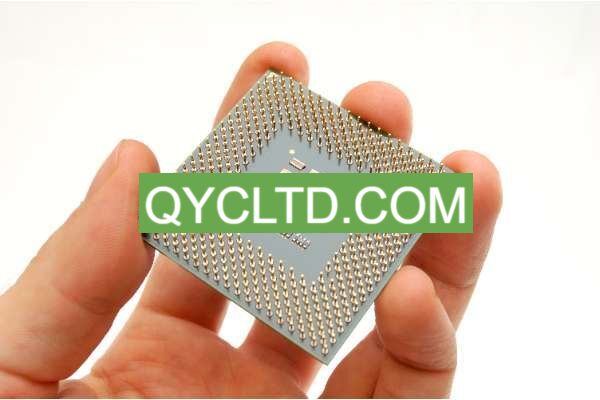
Flip Chip Ball Grid Array Substrate Manufacturer
Finally, mechanical support is an important consideration to ensure the structural stability and reliability of the FCBGA substrate. Good mechanical support design can reduce the impact of vibration and mechanical stress on the substrate, thereby improving the system’s impact resistance and reliability. In terms of mechanical support, suitable fixtures, brackets and structural design can be used to ensure that the substrate is not damaged or deformed during transportation, installation and use.
In summary, the FCBGA substrate design reference guide should comprehensively consider factors such as electrical wiring, thermal management, and mechanical support. By following key principles and best practices, designers can effectively improve the stability and performance of their designs to meet the requirements of electronic devices for a variety of applications.
What material is used in Flip Chip Ball Grid Array Substrate?
As an important part of modern electronic devices, the materials used in FCBGA substrates are crucial, directly affecting their performance, stability and scope of application. Typically, FCBGA substrates use high-performance substrate materials to cope with the increasingly complex needs of electronic equipment. Among them, one of the most common materials is FR-4 fiberglass composite, which has excellent mechanical and electrical properties and is suitable for most general applications.
FR-4 material is a glass fiber reinforced epoxy resin substrate with good heat resistance, mechanical strength and chemical stability. This makes it one of the ideal choices for manufacturing FCBGA substrates. The advantages of FR-4 material are its relatively low price, wide availability, and stable and reliable performance, making it suitable for many general electronic applications.
In addition to FR-4 materials, some more advanced substrate materials have also begun to be used in FCBGA substrate manufacturing. These materials include but are not limited to high-frequency PCB materials, polyimide (PI) substrates, metal substrates, etc. High-frequency PCB materials usually have lower dielectric loss and better high-frequency performance, and are suitable for applications requiring high-speed signal transmission. Polyimide substrates have excellent heat resistance and chemical stability and are often used in electronic devices in high-temperature environments. The metal substrate has excellent heat dissipation performance and is suitable for situations where efficient thermal management is required.
In summary, material selection for FCBGA substrates should be weighed based on specific application needs and performance requirements. Whether it is traditional FR-4 materials or more advanced high-performance materials, they can meet different levels of design requirements and provide reliable guarantee for the performance improvement and stable operation of electronic equipment.
What size are Flip Chip Ball Grid Array Substrate?
The size of the FCBGA substrate is one of the crucial considerations in the design process. Compared with traditional packaging, FCBGA substrate sizes are generally more flexible and can be custom designed according to the needs of specific applications. This means they can be adapted to a variety of space constraints and functional requirements, providing greater flexibility in the design and performance of equipment.
When selecting the FCBGA substrate size, the first thing to consider is the integration density of the device. Smaller sizes usually mean higher integration density, as they can accommodate more chips and other components on the same substrate. This is important for applications that require complex functionality within a limited space, such as portable electronic devices or embedded systems.
In addition, the size of the FCBGA substrate also directly affects the heat dissipation performance. Larger baseboards generally have better heat dissipation capabilities because they can accommodate larger heat sinks or heat dissipation surfaces. This is critical for high-power applications or equipment that needs to run for long periods of time, as they need to efficiently manage the heat generated to ensure stable performance and reliability.
Therefore, when determining the size of the FCBGA substrate, it is necessary to consider the balance between integration density and heat dissipation performance. For some applications, compromises may be required to meet different needs. For example, where space is limited, some thermal performance may need to be sacrificed to achieve higher integration density, or where thermal requirements are high, some increased size may need to be accepted for better thermal dissipation.
In summary, FCBGA substrate size selection is a complex and critical decision that requires comprehensive consideration of multiple factors and optimization based on the needs of specific applications. Careful design and analysis ensures the most appropriate size is selected for optimal performance and reliability.
The Manufacturer Process of Flip Chip Ball Grid Array Substrate.
The manufacturing process of FCBGA substrates is a complex and precise process involving multiple critical stages, each of which is critical to the quality and reliability of the final product. Here is a more detailed description of these stages:
Design verification
The first step in manufacturing an FCBGA substrate is design verification. At this stage, engineers use CAD software to create design drawings and conduct simulations and verifications to ensure the accuracy and functionality of the design. This includes considering factors such as electrical wiring, thermal management, and mechanical support.
Printing
Next comes the printing stage, where the design needs to be converted into the actual substrate. This involves stacking layers of the design onto a substrate and using special chemicals to transfer the pattern to the substrate surface. This step requires highly sophisticated equipment and operations to ensure the accuracy and consistency of the pattern.
Surface treatment
After the substrate is printed, it needs to be surface treated to enhance its electrical properties and durability. This may involve applying a layer of metal or alloy to provide a good soldering surface and conductivity. In addition, anti-corrosion treatments may also be performed to protect the substrate from environmental influences.
Welding
Soldering is a key step in manufacturing FCBGA substrates, which connects chips and other components to the substrate. During this process, the chip’s solder balls are connected to the pads on the substrate to form a solid electrical connection. The welding process requires precise temperature control and welding technology to ensure the reliability and stability of the connection.
Test
The final stage is to test the manufactured FCBGA substrate. At this stage, each substrate undergoes rigorous functional and performance testing to ensure it meets specifications and has stable performance. These tests may include electrical testing, thermal cycling testing, reliability testing, etc. to ensure that the substrate will function properly under various conditions.
By precisely controlling every stage, from design verification to testing, the process of manufacturing FCBGA substrates ensures the quality and reliability of the final product. This highly engineered manufacturing process is one of the keys to modern electronic device manufacturing, providing a stable and reliable foundation for a variety of high-performance applications.
The Application area of Flip Chip Ball Grid Array Substrate.
As a key component of modern electronic device design, FCBGA substrate (Flip Chip Ball Grid Array Substrate) has shown its wide range of applications and importance in many fields. Its high performance, high integration, and stability and reliability make it the preferred solution in many key areas.
First of all, in the field of high-performance computing, FCBGA substrate plays a vital role. In fields such as large-scale data processing, artificial intelligence, and deep learning, high-performance computing equipment needs to process large amounts of data and perform complex computing tasks. FCBGA substrates can provide high-speed signal transmission, low electrical losses, and excellent thermal management capabilities, allowing processors and other key components to operate stably and efficiently.
Secondly, in the field of communication equipment, FCBGA substrate also plays an important role. In fields such as mobile communications, network equipment, and satellite communications, communication equipment needs to be capable of high-speed data transmission and stable connections. FCBGA substrates can meet these needs, providing reliable electrical connections and high-density wiring to ensure stable operation of communication equipment and data transmission quality.
In addition, in the field of industrial control, FCBGA substrates are also widely used. In fields such as automated production lines, robot control, and smart instruments, industrial control equipment needs to be highly reliable and stable. The FCBGA substrate can provide stable electrical connections and anti-interference capabilities, ensuring that industrial equipment can operate stably for a long time in harsh environments.
Finally, in the field of medical diagnosis, FCBGA substrates also play an important role. In medical equipment such as medical imaging equipment, laboratory analysis instruments, and medical monitoring systems, FCBGA substrates can provide highly accurate data processing and stable signal transmission, helping medical professionals conduct accurate diagnosis and treatment.
To sum up, FCBGA substrates are widely used in high-performance computing, communication equipment, industrial control and medical diagnosis and other fields. Its high integration and stability make it the preferred solution for many key applications, providing a solid foundation for technological innovation and development in various industries.
What are the advantages of Flip Chip Ball Grid Array Substrate?
FCBGA substrate plays a vital role in today’s high-end electronic products, and its advantages are clearly reflected in several aspects compared with traditional packaging methods.
First, FCBGA substrates have higher integration density. By using Flip Chip packaging technology, the chip can be directly connected to the surface of the substrate, allowing for a more compact layout. In contrast, traditional packaging methods require connecting chips through wires, which limits the integration of the chip. This high level of integration allows the FCBGA substrate to accommodate more functional modules and components within the same size, providing room for product performance improvements.
Secondly, FCBGA substrate has better thermal performance. Because the Flip Chip package directly connects the chip to the surface of the substrate, the thermal path is shorter and the heat transfer is more efficient. In addition, FCBGA substrates usually use high thermal conductivity substrate materials and designs, such as metal heat dissipation layers and heat dissipation holes, to further improve the heat dissipation effect. This optimized thermal management mechanism enables the FCBGA substrate to better handle heat and maintain a stable operating temperature of the chip in high-performance applications, thus improving product reliability and lifespan.
Finally, FCBGA substrates have lower electrical losses. Because it is directly welded to the surface of the substrate, Flip Chip packaging eliminates the resistance and inductance caused by long wires in traditional packaging, reducing energy loss and signal distortion during signal transmission. This makes the FCBGA substrate perform better in high-speed signal transmission and applications with higher frequency requirements, providing more stable and reliable signal transmission.
To sum up, FCBGA substrate has become an ideal choice for many high-end electronic products due to its higher integration density, better thermal performance and lower electrical loss. It can not only meet the performance and reliability requirements of modern electronic products, but also provide a broader space for product innovation and development.
FAQ
What aspects need special attention in the design of FCBGA substrate?
When designing the FCBGA substrate, special attention needs to be paid to the optimization of electrical wiring to ensure the stability and speed of signal transmission. In addition, thermal management is also a key factor, and thermal design needs to be considered to avoid overheating of the chip. Mechanical support and the effects of the external environment also need to be taken into account to ensure that the substrate operates stably under a variety of conditions.
What are the troubleshooting methods for FCBGA substrates?
If the FCBGA substrate fails, a thorough electrical test and visual inspection will first be required to identify possible problem areas. Further diagnosis can then be performed using professional troubleshooting tools and equipment, such as thermal imaging and X-ray inspection. After troubleshooting the hardware fault, you may need to debug the firmware or software.
How to maintain FCBGA substrate?
Maintenance of FCBGA substrates includes regular cleaning and inspection. When cleaning, use a non-static cleaner and a soft cloth, and wipe the surface gently to avoid damaging electronic components. Check connections and solder joints regularly to make sure they are not loose or damaged. Also, check your cooling systems regularly to make sure they are effectively reducing temperatures and remaining in good working order.
What is the environmental adaptability of FCBGA substrate?
FCBGA substrate has strong environmental adaptability and can operate reliably under various environmental conditions. However, under extreme temperatures or humidity, additional protective measures, such as sealed enclosures or waterproof coatings, may be required to ensure substrate stability and reliability. In addition, anti-static measures are also important to avoid damage to electronic components caused by static electricity.