What is Ultra-thin 5G Substrate?
Ultra-thin 5G Substrate Manufacturer.”Ultra-thin 5G Substrate Manufacturer” refers to a company specializing in the production of exceptionally thin substrates tailored for 5G applications. Their expertise lies in crafting substrates that meet stringent size and performance requirements essential for next-generation telecommunications and electronics.
Ultra-thin PCB (Ultra-thin PCB) is a specially designed printed circuit board whose thickness is much lower than traditional PCB, usually less than 0.2 mm. This ultra-thin design enables it to perform well in high-frequency and high-speed data transmission environments, especially in supporting 5G communication technology.
En comparación con los PCB tradicionales, ultra-thin Placas de circuito impreso use special high-frequency materials, such as polytetrafluoroethylene (PTFE) or polyimide (PI). These materials have excellent electrical properties and stability and can effectively Reduce signal loss and support higher frequencies. This makes ultra-thin PCB an indispensable component of 5G communication equipment, capable of meeting the needs of fast data transmission and frequent signal processing.
Due to its thin design, ultra-thin PCB also supports the compact layout and lightweight design of the device, which is suitable for the miniaturization trend of modern electronic devices. Its manufacturing process still includes multiple key steps such as substrate preparation, copper layer deposition, photoresist coating and exposure, etching, drilling, component mounting, welding and testing. Each step is strictly controlled to ensure the high quality and reliability.
The wide application of ultra-thin PCB is not only limited to 5G communication equipment, but also covers other fields with high-frequency and high-speed data transmission requirements, such as medical diagnostic instruments, satellite communication equipment, and industrial control systems. Its application in these fields has promoted the improvement of equipment performance and innovation of functions, and has become an indispensable technical support in the development of modern science and technology.
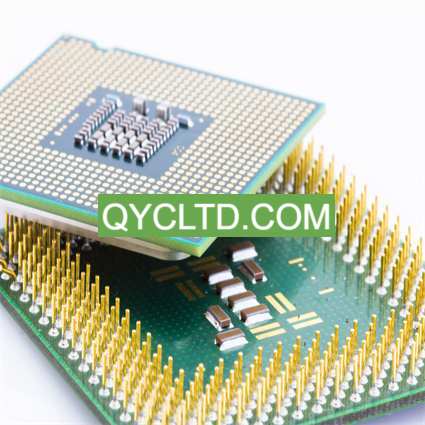
Ultra-thin 5G Substrate Manufacturer
In short, ultra-thin PCB, through its special materials and precision design, provides reliable solutions to the high-frequency and high-speed data transmission needs of electronic equipment, while promoting the innovation and development of electronic products.
Ultra-thin 5G Substrate design Reference Guide.
The Design Reference Guide for Ultra-Thin 5G Substrates is dedicated to providing engineers and designers with critical guidance to ensure efficient and reliable design standards when creating PCB layouts. These guidelines are particularly important in today’s rapidly developing 5G communications environment, as ultra-thin PCBs play a key role in supporting high-frequency and high-speed data transmission.
En primer lugar, an excellent ultra-thin 5G substrate design should start with a comprehensive planning and analysis stage. Designers need to carefully consider circuit layout complexity and the placement of high-density components to ensure that circuit noise and signal interference are minimized while optimizing signal transmission paths and performance. Además, strict compliance with design rules, including minimum line width/line spacing, inter-layer spacing, drilling locations, etc., is crucial to ensure reliability and consistency during PCB manufacturing.
In terms of software tools, modern PCB design software such as Altium Designer, Cadence Allegro, etc. provide powerful functions to support complex circuit design, simulation analysis and automatic routing. These tools not only improve design accuracy and efficiency, but also verify circuit performance through virtual simulation, reducing errors and modifications during the design phase.
Key technologies include high-frequency circuit design, miniaturized packaging, multi-layer board stacking technology, etc. The application of these technologies can significantly improve the stability and reliability of ultra-thin PCBs in the high-frequency 5G environment. For example, using materials with superior high-frequency characteristics such as polytetrafluoroethylene (PTFE) or polyimide (PI) can effectively reduce signal attenuation and loss and ensure the accuracy and reliability of signal transmission.
En resumen, the design reference guide for ultra-thin 5G substrates is not limited to grasping technical details, but also covers best practices and strategies throughout the design life cycle. By in-depth understanding and application of these guidelines, engineers and designers can effectively deal with complex 5G communication requirements, promote the development and application of ultra-thin PCB technology, and provide a solid foundation for innovation in high-speed data transmission and communication networks.
What material is used in Ultra-thin 5G Substrate?
Ultra-thin PCB (Ultra-thin PCB), como componente clave en los equipos electrónicos modernos, usually uses some special high-frequency materials to ensure excellent electrical performance and stability in high-frequency environments. These materials mainly include polytetrafluoroethylene (PTFE) and polyimide (PI).
Polytetrafluoroethylene (PTFE) is a material with excellent electrical insulation and thermal stability. It performs well in high-frequency applications and can effectively reduce signal attenuation and circuit noise in signal transmission, thereby improving overall signal integrity and transmission efficiency. PTFE’s chemical inertness and high-temperature stability enable it to maintain stable electrical properties under various environmental conditions, making it especially suitable for electronic equipment and communication systems that require precise high-frequency transmission.
Another common material is polyimide (PI), which offers excellent mechanical strength, thermal stability, and chemical resistance. The application of PI in ultra-thin PCB is mainly based on its excellent performance in high-temperature environments and its ability to withstand high-temperature welding and working conditions without failure. Its high-frequency characteristics make PI materials particularly useful in high-frequency applications such as 5G communication equipment, ensuring the stability and reliability of signal transmission.
Material selection for ultra-thin PCBs not only takes into account electrical properties, but also must meet requirements in terms of mechanical strength, processing performance, and cost-effectiveness. Therefore, designers and engineers need to consider various factors when selecting materials to ensure that the final product can perform well in high-frequency and high-speed data transmission while having long-term stable performance.
En resumen, Politetrafluoetileno (PTFE) and polyimide (PI), as the main materials of ultra-thin PCB, play an important role in modern electronic communications and high-tech fields due to their superior high-frequency characteristics and stability. It plays a vital role in promoting the development of electronic devices towards higher performance and smaller size.
What size are Ultra-thin 5G Substrate?
The size of ultra-thin PCBs varies due to their wide range of application scenarios, and are usually designed to be minimized to accommodate high-density components and complex circuits in limited spaces. In the design of electronic devices, size is a key consideration, which directly affects the overall volume and functional performance of the device.
En primer lugar, ultra-thin PCB plays an important role in modern high-tech equipment, such as 5G communication equipment, smartphones, Dispositivos portátiles, etc. These devices usually require a small size, so a key goal of ultra-thin PCB design is to reduce its thickness and space as much as possible to meet the compact overall design requirements of the device.
Segundo, the size design of ultra-thin PCB also takes into account the layout requirements of high-density components. With the advancement of technology, electronic components continue to be miniaturized and integrated, and PCBs must arrange more components and more complex circuit structures in a limited space. Therefore, the PCB design must be able to achieve a high degree of integration while maintaining good electrical performance and stability.
During the manufacturing process, to achieve these design goals, engineers use advanced manufacturing technologies and materials, such as special substrate materials (such as polytetrafluoroethylene and polyimide), as well as precision etching and drilling processes. The application of these technologies and processes can not only ensure the thickness limit of the PCB, but also ensure the reliability and long-term stability of the circuit.
En resumen, the size design of ultra-thin PCB is not only to pursue the beautiful appearance and portability of the device, but more importantly, to achieve the requirements of high-performance electronic equipment. Through careful design and advanced manufacturing technology, ultra-thin PCBs can accommodate complex electronic components and circuits in the smallest space, bringing more innovation and progress to modern technology.
The Manufacturer Process of Ultra-thin 5G Substrate.
The manufacturing process of ultra-thin PCB is a complex and precise process chain designed to meet the needs of high-frequency and high-speed data transmission, and is especially suitable for advanced applications such as 5G communication equipment. The following are the main steps of the ultra-thin PCB manufacturing process:
The first step in manufacturing ultra-thin PCB is to prepare the substrate. Materials with excellent electrical properties, such as polytetrafluoroethylene (PTFE) or polyimide (PI), are usually selected to ensure stable performance in high-frequency environments.
On the surface of the prepared substrate, a thin layer of copper foil is covered on it by chemical deposition or electroplating. This step is to form the conductive layer of the circuit board for subsequent circuit connections.
Coat photoresist on the copper foil and use a photomask to expose the photoresist to form the desired circuit pattern. After exposure, the unexposed photoresist is removed by development to expose the circuit pattern on the surface of the copper foil.
The board is immersed in a chemical solution that dissolves the copper foil that is not protected by the photoresist, creating conductive paths for the circuit pattern. After etching, the board is washed to remove residual photoresist and chemical solutions.
A high-precision CNC drilling machine is used to drill holes at designated locations in order to install electronic components and establish electrical connections between different layers. These vias require precise alignment to ensure the overall reliability and stability of the board.
Electronic components are precisely mounted onto the surface of the circuit board through automated patch technology (SMT) or manual soldering. These components include resistors, capacitors, integrated circuits, etc., and their accurate installation directly affects the performance and reliability of the circuit.
After the components are installed, a soldering process is used to firmly connect the components to the copper wires on the circuit board. The temperature and time need to be controlled during the welding process to ensure that the solder joints are firm and reliable and not easily affected by environmental conditions.
Finalmente, the assembled ultra-thin PCB is subjected to comprehensive electrical testing and functional verification. These tests include connectivity testing, electrical performance testing and functional testing to ensure that the PCB meets design requirements and standards.
Through the above strict manufacturing process, ultra-thin PCB can meet high-precision and high-reliability requirements, and is widely used in fields such as 5G communication equipment, medical diagnostic instruments, and industrial automation systems, providing key support for the development of modern electronic technology.
The Application area of Ultra-thin 5G Substrate.
As an important part of modern electronic technology, ultra-thin PCB is widely used in various fields to promote the improvement of equipment performance and the realization of functional innovation. Especially in the fields of 5G communications, medical diagnosis, and industrial control, ultra-thin PCBs have shown unique advantages and application prospects.
Primero, ultra-thin PCB plays a key role in 5G communication equipment. With the construction and popularization of 5G networks, the demand for high-frequency and high-speed transmission is increasing, and traditional PCBs can no longer meet its requirements. With its excellent high-frequency characteristics and electrical performance, ultra-thin PCB can support complex antenna design and miniaturized packaging structure, providing a solid technical foundation for improving the performance of 5G base stations, mobile phones and other communication equipment.
Segundo, the application of ultra-thin PCB in medical diagnostic instruments is also very important. Medical equipment has extremely high requirements for accurate and stable data transmission and processing capabilities, and ultra-thin PCB can support the layout of various high-precision sensors and signal processing units through its highly integrated design and excellent electrical performance. This will improve the accuracy and efficiency of medical diagnosis and contribute to the advancement of medical technology.
Además, ultra-thin PCBs are increasingly used in industrial control systems. The industrial environment has strict requirements on the durability and stability of equipment, and ultra-thin PCB, through its high-density layout and advanced manufacturing process, can achieve more functional integration in a smaller space, improving the reliability of industrial control equipment. The level of intelligence and operating efficiency support the development of industrial automation and intelligent manufacturing.
In short, ultra-thin PCB is not only an inevitable trend in the development of electronic technology, but also an important driving force for technological progress in fields such as 5G communications, medical diagnosis, and industrial control. With its continuous innovation in design and manufacturing technology, ultra-thin PCB will continue to play an important role in various fields, providing strong support for performance improvement and functional innovation of modern high-tech equipment.
What are the advantages of Ultra-thin 5G Substrate?
As a key component of modern electronic equipment, ultra-thin PCB shows many advantages compared with traditional circuit wiring. Primero, they have excellent high-frequency characteristics and are particularly suitable for high-speed and high-frequency transmission needs, such as 5G communication technology. This advantage enables ultra-thin PCBs to perform well in application scenarios with strict frequency requirements, ensuring stable and fast data transmission.
Segundo, the miniaturization design of ultra-thin PCB is another significant advantage. By optimizing the layout and material selection, they support the compact design and lightweight of the device, allowing electronic products to be more refined and portable, in line with modern consumers’ needs for device portability and appearance design.
Ultra-thin PCBs are also known for their stable electrical performance. High-quality materials and advanced processes are used in the manufacturing process to ensure the reliability and stability of the circuit board under various working conditions, thereby reducing circuit failures and equipment maintenance costs.
High reliability is another major advantage of ultra-thin PCB. Strict manufacturing and testing processes ensure the quality and reliability of each PCB, enabling it to maintain stable performance over long-term use and reducing the risk of product damage and repair.
Finalmente, ultra-thin PCBs are highly adaptable and can be customized according to specific application requirements. Whether it is complex circuit layout or high-density component integration, ultra-thin PCB can meet the specific needs of different industries and equipment, providing flexible solutions for various application scenarios.
En resumen, ultra-thin PCB has become an indispensable and important part of modern electronic equipment with its high-frequency characteristics, miniaturized design, stable electrical performance, high reliability and strong adaptability, and has promoted electronic technology. Continuous progress and innovation.
Preguntas más frecuentes
What is the difference between ultra-thin PCB and traditional PCB?
Ultra-thin PCB is different from traditional PCB in material selection and manufacturing process. Traditional PCBs usually use materials such as FR4, while ultra-thin PCBs often use high-frequency materials such as polytetrafluoroethylene (PTFE) or polyimide (PI) to support high-speed and high-frequency applications, especially in 5G communications. It has important application value in technology.
What application scenarios are ultra-thin PCB suitable for?
Ultra-thin PCBs are widely used in 5G communication equipment, medical diagnostic instruments, industrial control systems and other fields. Due to its excellent electrical performance and compact design, it is particularly suitable for modern electronic equipment that requires high integration and miniaturization design.
What are the design considerations for ultra-thin PCB?
When designing ultra-thin PCBs, special attention needs to be paid to issues such as material selection, interlayer coupling, signal integrity, and thermal management. Ensure that the design can meet the requirements of high frequency, low loss and stability while avoiding electromagnetic interference and signal fluctuations.
What are the key steps in the ultra-thin PCB manufacturing process?
Key steps in manufacturing ultra-thin PCBs include substrate preparation, copper layer deposition, photoresist coating and exposure, etching, drilling, component mounting, soldering, and rigorous testing and quality control processes. Each step is critical and affects the quality and reliability of the final product.