What are Ultra-small Size Package Substrates?
Ultra-Small Size Package Substrates Manufacturer.The Ultra-Small Size Package Substrates Manufacturer specializes in crafting compact substrates for diverse electronic applications. With precision engineering and advanced materials, they create substrates that optimize space utilization without compromising performance. Their expertise lies in developing miniature solutions that meet stringent industry standards. From microelectronic components to cutting-edge sensors, their substrates enable the seamless integration of technology into compact devices. Through innovation and quality craftsmanship, they empower manufacturers to design sleek, efficient products for modern markets. Whether for consumer electronics or medical devices, their ultra-small size packages drive the next wave of innovation.
Ultra-small size packaging substrate is a circuit substrate used to install and connect electronic components. It has extremely small size and high-density connection characteristics. These substrates are widely used in fields such as smartphones, Dispositivos portátiles, and medical devices that have strict size and weight requirements.
Driven by modern technology, people’s demands for electronic devices are becoming more and more diverse and personalized, and at the same time, they are also placing increasingly stringent requirements on device size and weight. In order to meet this demand, ultra-small size packaging substrates emerged.
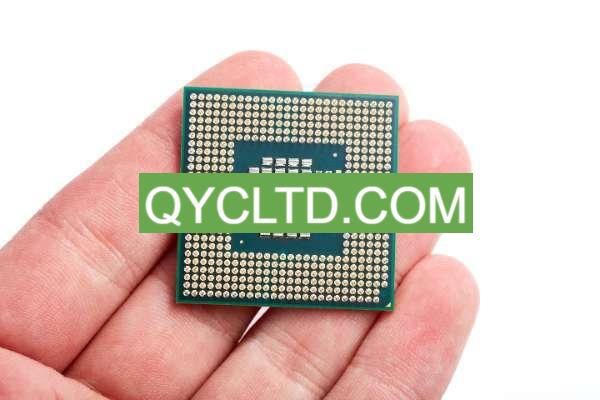
Ultra-Small Size Package Substrates Manufacturer
These substrates are called “ultra-small” because they often have very compact dimensions that allow them to accommodate a large number of electronic components and connections in a very small space. En comparación con los PCB tradicionales, ultra-small size packaging substrates usually have higher integration and smaller dimensions, enabling more functions and performance to be achieved in the same space.
The design and manufacturing of ultra-small package substrates is challenging because of the large number of components that need to be accommodated in a limited space and the need to ensure high-density connections and signal integrity. Designers must lay out components in the smallest possible space and plan circuit connections appropriately to ensure the performance and stability of the entire system. Además, the manufacturing process also requires greater precision and control to ensure that the location and connection of each component are accurate.
The application fields of ultra-small size packaging substrates are very wide. In smartphones, ultra-small size packaging substrates enable thinner and lighter designs and provide more functions and performance. In wearable devices, these substrates can enable a more comfortable and portable wearing experience and provide real-time monitoring and feedback capabilities. In medical devices, ultra-small size packaging substrates can achieve more accurate data collection and processing, helping doctors better diagnose and treat diseases.
En general, ultra-small size packaging substrates play a vital role in modern electronic devices. They not only realize the miniaturization and lightweight of electronic products, but also provide people with a more convenient and smarter life experience. With the continuous advancement and innovation of science and technology, it is believed that ultra-small size packaging substrates will play an increasingly important role in the future and promote the continuous development of the electronic industry.
Ultra-small Size Package Substrates design Reference Guide.
The design of ultra-small size package substrates (Ultra-small Size Package Substrates) is a complex and critical task that requires comprehensive consideration of factors such as space constraints, signal integrity, thermal management, and manufacturing feasibility. Here is a reference guide for designing ultra-small package substrates to help you better meet your design challenges and succeed:
Determine design requirements and functional requirements
Before starting the design, it is necessary to clarify the overall requirements and functional requirements of the product. This includes determining the type, quantity, and layout of electronic components required, as well as interface requirements with other system components.
Choose the right PCB material
Selecting materials suitable for ultra-small package substrates is critical. In addition to the common FR4, high-density interconnect (HDI) materials or flexible substrates can also be considered to meet the needs of high-density, high-performance and flexible connections.
Optimize layout and routing
Optimizing component placement and routing within limited space is key to design. Signal integrity and circuit performance can be maximized by placing components appropriately, optimizing signal paths, and reducing cross-ground and cross-layer connections.
Consider thermal management
Ultra-small packaging substrates may generate more heat, so thermal management is critical. By properly designing heat dissipation holes, heat sinks or heat pipes, and selecting appropriate heat dissipation materials, the temperature can be effectively controlled and the system can operate stably.
Ensure manufacturing feasibility
It is very important to consider manufacturing feasibility during the design process. Communicating with manufacturers and understanding their capabilities and technical limitations can help you design ultra-small package substrates that are more manufacturable.
Perform design verification and simulation
Design verification and simulation are essential steps before submission for manufacturing. By using circuit simulation software and 3D modeling tools, you can evaluate the performance, reliability, and manufacturing feasibility of your designs, and identify and resolve potential issues in a timely manner.
Generate detailed manufacturing documents
Finalmente, ensure that detailed manufacturing documents are generated, including Gerber files, drilling files, assembly drawings, bill of materials, etc. These documents will serve as a guide for the manufacturing process, ensuring that the final ultra-small package substrate meets design requirements.
By following the above reference guide, you can more systematically design ultra-small packaging substrates, overcome challenges, and ensure the performance, quality, and reliability of the final product.
What material is used in Ultra-small Size Package Substrates?
In order to meet the requirements of ultra-small packaging substrates, choosing the right materials is crucial. Durante el proceso de diseño, engineers need to select the most suitable materials based on specific application requirements and performance indicators. The following are commonly used ultra-small packaging substrate materials and their characteristics:
FR4
FR4 is one of the most common PCB substrate materials, and its main components are fiberglass and epoxy resin. Although FR4 has good mechanical properties and thermal stability, improved versions with higher performance may be required in ultra-small package applications. For ultra-small packaging, you can choose high-performance FR4 materials, such as FR4-06 and FR4-08 grades, which have a higher glass fiber ratio, better dimensional stability and thermal conductivity, and are suitable for high-density wiring and micro-packaging.
High Density Interconnect (HDI) Materials
High-density interconnect (HDI) materials are specialized materials designed for ultra-small packaging. They feature higher interlayer connection density and finer line width/spacing, enabling more complex circuit designs. HDI materials usually include polyimide (PI) substrates and special copper foils, which are characterized by high thermal conductivity, low dielectric constant and excellent mechanical properties. HDI technology can achieve smaller size and lighter weight packaging design, which is suitable for high-end mobile devices and embedded systems.
Flexible substrate
Flexible substrates such as polyimide (PI) are thin, soft, and highly moldable materials suitable for ultra-small packaging applications that require bending and bending. Polyimide substrates have excellent high temperature resistance, chemical stability and mechanical strength, allowing for more complex three-dimensional layouts and more compact packaging designs. Therefore, flexible substrates are widely used in wearable devices, medical implants, and flexible electronics.
Overall, choosing the right materials is critical to the design of ultra-small packaging substrates. Engineers should consider factors such as the material’s thermal conductivity, mechanical properties, dimensional stability and cost based on specific application needs and performance requirements to ensure design stability, reliability and superior performance.
What size are Ultra-small Size Package Substrates?
The size of ultra-small size package substrates (Ultra-Small Size Package Substrates) is one of the crucial considerations in design. Since it is used in microelectronics, its size must be as small as possible to meet the compact design requirements of modern electronics.
Although the dimensions of ultra-small packaging substrates vary by application, they typically have the following characteristics:
Tny size
Typical ultra-small package substrate dimensions can range from a few millimeters to tens of millimeters. Their size typically matches the size of the device or device in which they are embedded to maximize space savings and provide a highly integrated solution.
Thin design
In addition to their small size, ultra-small package substrates often feature thinner designs to accommodate limitations on device thickness. This thin design allows them to be easily embedded into various thin devices, como los teléfonos inteligentes, Tabletas, etc.
High density layout
Despite their small size, ultra-small packaging substrates often feature high-density circuit layouts to accommodate more electronic components and connections. This means designers must accurately lay out complex circuits within limited space to ensure signal integrity and electrical performance.
Customized needs
Because ultra-small packaging substrates are often used in specific microdevices, their size and shape are often customized. Based on specific application requirements, designers may customize the size to best meet the requirements of the equipment.
Despite their small size, ultra-small packaging substrates play a huge role in modern electronics. Their miniaturized design makes it possible for electronic products to be lightweight, portable and highly integrated, promoting the continuous development and progress of electronic technology. Therefore, designers must strike a balance between size, performance and manufacturing cost to achieve the best design solution.
The Manufacturer Process of Ultra-small Size Package Substrates.
The manufacturing process of ultra-small packaging substrates is similar to traditional PCBs, but requires greater precision and control. The following is the detailed process for manufacturing ultra-small packaging substrates:
Design preparation
Before fabricating ultra-small package substrates, detailed design preparation is required. This includes generating detailed design files including circuit diagrams, layout designs, Gerber files, drill files, etc. Design documents must accurately reflect every detail and requirement of the ultra-small package substrate.
Substrate production
Substrate fabrication is the first step in manufacturing ultra-small packaging substrates. In this process, high-performance copper foil needs to be laminated to the substrate material. It is very important to choose the appropriate substrate material. A high-temperature and high-pressure process is usually used to firmly combine the copper foil with the substrate material to ensure the stability and reliability of the circuit.
Image transfer
Image transfer is the process of transferring designed circuit patterns to the surface of copper foil. Through high-precision exposure and development technology, the design pattern is accurately transferred to the copper foil. This process requires highly precise equipment and process control to ensure the accuracy and clarity of the pattern.
Etching and plating
Etching is the process of removing unprotected portions of copper foil, leaving the desired circuit pattern. Through chemical etching, unnecessary copper foil is removed so that the circuit pattern is clearly visible. Próximo, the circuits and holes are plated to increase conductivity and ensure the reliability of the circuit connections.
Lamination and drilling
Ultra-small packaging substrates often require multi-layer designs, so lamination and drilling are essential steps. During the lamination process, multi-layer substrates are pressed together through a high-temperature and high-pressure process to ensure the electrical connection and mechanical stability between the layers. The drilling process requires the use of high-precision drilling equipment to accurately punch holes and control the size and location of the holes.
Surface treatment
In order to improve welding performance and corrosion resistance, surface treatment of the substrate is required. Common surface treatments include adding coatings such as gold, silver or other alloys. These surface treatments prevent oxidation and corrosion and improve welding quality and reliability.
Final testing and inspection
Final testing and inspection are the last steps in manufacturing ultra-small packaging substrates. Substrates are thoroughly inspected and tested using automated optical inspection (AOI) and electrical test equipment to ensure they are defect-free and meet design requirements. This step is critical to ensure the quality and performance of ultra-small package substrates meet expected requirements.
Through the above rigorous manufacturing process, it is possible to ensure the production of high-quality, reliable ultra-small packaging substrates to meet the needs of modern electronic equipment for miniaturization and high performance.
The Application area of Ultra-small Size Package Substrates.
Under the trend of modern technology, ultra-small packaging substrates have gradually become an indispensable and important component in various fields. Its wide range of application fields not only promotes the miniaturization, lightweight and intelligence of electronic equipment, but also promotes technological progress in medical, industrial, automotive and other fields. The following are the applications of ultra-small packaging substrates in various fields:
Electrónica de consumo
Ultra-small packaging substrates are widely used in consumer electronics, como los teléfonos inteligentes, smart watches, headphones, etc. As the demand for portable, powerful electronic devices continues to increase, ultra-small packaging substrates provide high-performance circuit connections and compact designs for these devices.
Equipos médicos
In the medical field, ultra-small packaging substrates provide critical support for various medical devices. For example, implantable devices (such as pacemakers, neurostimulators, etc.) and portable monitoring instruments (such as blood glucose meters, heart rate monitors, etc.) require highly integrated and compact electronic designs to meet the miniaturization and miniaturization of medical equipment. Comfort requirements.
Automated industry
In the field of industrial automation, ultra-small packaging substrates are widely used in sensor modules, microcontrollers and other equipment. These devices often need to operate in harsh environmental conditions and require highly reliable circuit connections and stability, and ultra-small packaging substrates can meet these requirements.
Electrónica del vehículo
In the field of automotive electronics, ultra-small packaging substrates play an important role in autonomous driving systems, especially in miniature radar and camera modules. These modules need to work stably under extreme conditions such as vehicle vibration and temperature changes, and provide highly accurate sensor data. Ultra-small packaging substrates can achieve a high degree of integration of electronic components to meet the needs of automotive electronic systems.
En resumen, the application of ultra-small packaging substrates has penetrated into various fields and plays an important role in different industries. Con el continuo avance e innovación de la tecnología, it is believed that ultra-small packaging substrates will continue to promote the development of various fields and bring humans a more convenient, intelligent and efficient life and work experience.
What are the advantages of Ultra-small Size Package Substrates?
Ultra-small packaging substrates play a vital role in modern electronic devices, offering multiple advantages that are critical to meeting the growing demands for miniaturization and performance of electronic products.
Primero, the ultra-small packaging substrate significantly saves space. With the continuous advancement of technology, more and more electronic devices need to implement more functions in a limited space, and ultra-small packaging substrates precisely meet this demand. By optimizing design and material selection, ultra-small packaging substrates can achieve a high degree of integration within a tiny size, providing device designers with more flexibility and space utilization, making products lighter and more portable, while satisfying users’ needs for small The growing demand for electronic equipment.
Second, the ultra-small packaging substrate provides excellent performance. Despite its small size, the ultra-small package substrate provides reliable, high-density electrical connections. Through precise design and manufacturing processes, they can achieve complex circuit layout and high-frequency signal transmission in a limited space, ensuring the performance and stability of the equipment. Whether it is high-speed data transmission or signal processing, the ultra-small packaging substrate is capable of doing the job, and while maintaining high performance, it reduces the power consumption of the circuit and extends the battery life of the device.
Finalmente, ultra-small packaging substrates offer excellent flexibility. They are suitable for a variety of complex and demanding applications, especially where space and weight are limited. Whether in medical equipment, automotive electronics, smart wearable devices or portable consumer electronics, ultra-small packaging substrates are competent and provide customized solutions for various application scenarios. Designers can choose different packaging methods and materials based on specific needs to achieve the best balance of performance and cost-effectiveness to meet the needs of different customers.
En resumen, ultra-small packaging substrates are of irreplaceable importance in modern electronic equipment. Its advantages such as space saving, high performance and flexibility provide strong support for the design and manufacturing of electronic products and promote electronic technology. Continuous development and innovation.
Preguntas más frecuentes
What is the difference between ultra-small packaging substrate and traditional PCB?
Ultra-small packaging substrates pay more attention to size, density and performance than traditional PCBs. They usually require higher manufacturing precision and more complex designs to meet the miniaturization and high performance requirements of modern electronic devices.
What is the minimum size of an ultra-small package substrate?
The size of ultra-small packaging substrates depends on the specific application requirements, but can often be a few millimeters or less. With the advancement of technology, innovative manufacturing processes are constantly being applied, making the size smaller and smaller.
How to solve the thermal management of ultra-small packaging substrates?
Thermal management is an important consideration in ultra-small package substrate design. Technologies such as heat sinks, heat pipes, and fans are usually used to solve the heat generated by high-density circuits and ensure the stability and reliability of the equipment.
Are ultra-small package substrates expensive to manufacture?
The cost of manufacturing ultra-small packaging substrates is generally higher because higher manufacturing precision and more complex processes are required. However, with the advancement of technology and market competition, manufacturing costs are gradually declining.