¿Qué es el sustrato de radar/antena??
Radar/Antenna Substrate Manufacturer, A pioneering radar/antenna substrate manufacturer, they lead the industry with cutting-edge materials and advanced fabrication techniques. Their substrates, meticulously engineered for optimal performance, form the backbone of radar systems worldwide, ensuring unparalleled precision and reliability in communication and surveillance. Through relentless innovation and a commitment to quality, they empower next-generation technologies, from military defense to telecommunications, pushing the boundaries of possibility in the realm of electromagnetic sensing. With a blend of expertise and ingenuity, they stand as the cornerstone of modern radar and antenna infrastructure, shaping the landscape of connectivity and security.
Radar/antenna substrates are an integral and critical component of modern radar systems and antennas. Not only do they provide support and structural support, but more importantly they play a vital role in circuit design. Through their special materials and design, these substrates provide the necessary conductivity and isolation for circuits, ensuring efficient operation of radar systems and antennas.
Primero, the radar/antenna substrate performs support and structural functions. They provide a stable physical platform on which to assemble the individual components of the radar system and antenna. This support structure not only gives the equipment good mechanical stability, but also ensures accurate alignment between various components, thus ensuring the normal operation and long-term reliability of the equipment.
Segundo, the radar/antenna substrate has important conductive properties in circuit design. These substrates are typically made from materials with excellent electrical conductivity properties, such as glass fiber reinforced polyimide (PTFE) covered with copper foil. This material not only has good electrical conductivity, but also maintains stable signal transmission characteristics in high-frequency environments, ensuring the efficient operation of radar systems and antennas.
Finalmente, the radar/antenna substrate also performs the isolation function. In radar systems and antennas, certain electrical isolation needs to be maintained between different components to prevent signal interference and electromagnetic interference. With appropriate design and material selection, the radar/antenna substrate can effectively isolate various circuit components and ensure system stability and performance.
En resumen, radar/antenna substrates are indispensable and critical components in modern radar systems and antennas. They provide support, conductivity and isolation to ensure efficient operation and reliability of the equipment. In future development, as the performance requirements for radar systems and antennas continue to increase, radar/antenna substrates will continue to play an important role in promoting the continuous progress and innovation of related technologies.
Radar/Antenna substrate design Reference Guide.
The design of radar and antenna substrates is a complex and critical process, which directly affects the performance and reliability of radar and antenna systems. There are many factors to consider during the design process. Here are some key considerations commonly found in design reference guides:
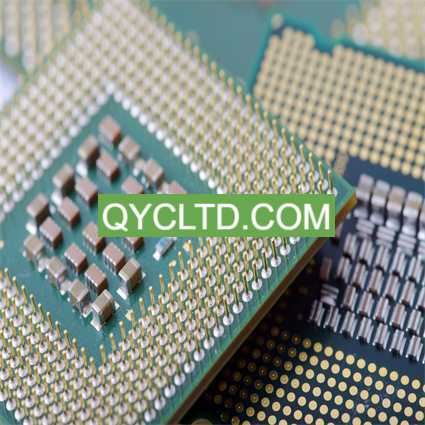
Radar/Antenna Substrate Manufacturer
Primero, frequency range is one of the most important considerations in the design process. Different radar and antenna systems operate in different frequency ranges, so the materials and structure of the substrate must be able to support the required frequency range and avoid signal attenuation and distortion.
Segundo, signal loss is also a critical issue. Designers need to select substrate materials with low-loss characteristics and adopt appropriate layout and connection methods to minimize signal loss and ensure system sensitivity and performance.
Another important consideration is thermal management. Because radar and antenna systems generate heat during operation, designers need to ensure that substrate materials and structures can effectively disperse and remove heat to prevent overheating damage and maintain system stability.
Además, manufacturing feasibility is also one of the important factors to consider during the design process. Designers need to choose materials and structures that are easy to process and assemble to ensure a smooth production process and reduce manufacturing costs.
Design Reference Guides provide key guiding principles and best practices to help designers effectively consider and address these factors during the design process. By following the recommendations in the Design Reference Guide, designers can ensure that the radar and antenna substrate are designed to meet the system’s performance requirements and provide good reliability and stability.
What material is used in Radar/Antenna substrate?
Radar and antenna substrate selection is critical to performance and reliability, and materials are one of the most critical aspects. Common radar/antenna substrate materials include PTFE (Politetrafluoetileno), FR-4 (glass fiber reinforced epoxy resin), and PTFE glass fiber, etc. Each of these materials has unique properties and is suitable for different types of applications and environments.
Primero, PTFE (Polytetrafluoroethylene) is a very common radar/antenna substrate material. It has excellent high temperature resistance, chemical stability and low dielectric loss, making it suitable for high frequency and microwave applications. PTFE substrates are commonly used in applications requiring high performance and low signal loss, such as satellite communications systems and radar systems.
Segundo, FR-4 (fiberglass reinforced epoxy) is another commonly used radar/antenna substrate material. It has lower cost and higher mechanical strength and is suitable for most general radar and antenna applications. FR-4 substrates are commonly used in consumer electronics, communications equipment, and general industrial applications.
Además, PTFE glass fiber is a composite material that combines PTFE and glass fiber, which has the excellent properties of PTFE and the mechanical strength of glass fiber. This material excels in high frequency and microwave applications, delivering superior performance and reliability.
Selecting the appropriate radar/antenna substrate material depends on specific application requirements, including factors such as frequency range, signal loss, thermal management, and cost. Durante el proceso de diseño, engineers need to carefully consider the characteristics of each material and make the best choice based on project requirements to ensure that the final product can achieve the expected level of performance and reliability.
What size are Radar/Antenna substrate?
Radar and antenna substrates are sized according to specific application needs, and this flexibility allows them to be adapted to a variety of scenarios and missions. From tiny antennas to large radar systems, substrates of all sizes play key roles in different applications.
In the field of micro-antennas, small size substrates are crucial. For example, the micro-antenna substrates required for mobile communication equipment and drones must be compact and lightweight to meet the requirements for miniaturization and portability of the equipment. These micro-substrates typically feature highly integrated designs that utilize advanced microfabrication technologies such as microelectronics processing and SMT (surface mount technology) to achieve higher performance and reliability.
In large radar systems, larger substrates are more common. Large radar systems, such as shipboard radars, ground surveillance radars, and weather radars, require large area substrates to support complex antenna arrays and signal processing circuits. These substrates are usually constructed of composite materials to ensure sufficient structural strength and thermal stability, and are equipped with high-power transmission lines and heat dissipation facilities to cope with high energy and long-term operation requirements.
In medium-sized radar and antenna systems, the size of the substrate usually falls between micro and large. Such systems include vehicle radars, aviation radars, and wireless communication base stations. They require relatively large substrates to accommodate complex circuit board layouts and connector configurations, while also requiring volume and weight constraints to ensure system portability and installation flexibility.
En general, radar and antenna substrates come in a wide range of sizes, from micro to large. Whether it is a small portable device or a large industrial system, the size of the substrate is a key factor in being carefully designed and optimized based on specific application needs and performance requirements.
The Manufacturer Process of Radar/Antenna substrate.
The manufacturing of radar and antenna substrates is a complex and sophisticated process involving multiple critical steps, each of which has a significant impact on the performance and reliability of the final product.
Primero, the manufacturing process begins with the design phase. During the design phase, engineers need to consider the requirements of the radar or antenna system, including frequency range, power requirements, space constraints, etc. Based on these requirements, engineers design the layout of the circuit board and the way the circuits are connected.
Next comes prototyping. By using computer-aided design (CAD) software, engineers transform designs into actual prototypes. This prototype is usually implemented through prototyping or rapid prototyping techniques for preliminary testing and verification.
Once the prototype is verified, the next step is chemical etching. In this step, unnecessary parts of the metal layer covering the circuit board are removed by exposing the circuit board to a specific chemical solution to create the desired conductive paths. This step is crucial because it directly affects the conductive properties and signal transmission quality of the circuit board.
Next comes drilling. In this step, engineers use high-precision drills to drill holes into the circuit board to accommodate electronic components and connectors. The precision and placement of drilled holes is critical to the performance and reliability of the circuit board.
After drilling is complete, the next step is metallization. During the metallization process, engineers ensure the circuit board’s conductive properties and signal transmission quality by covering the circuit board’s conductive paths with a metal layer. This usually involves using chemical gold plating or spray-on metal methods.
Finally comes the assembly stage. During the assembly stage, engineers install electronic components and connectors onto the circuit board and perform soldering or other connection methods to ensure they work properly. The quality and precision of assembly directly affects the performance and reliability of the final product.
En resumen, the manufacturing process of radar and antenna substrates is a delicate and complex process involving multiple key steps such as design, prototyping, Grabado químico, drilling, metallization and assembly. Each step has a significant impact on the performance and reliability of the final product and therefore requires a high degree of expertise and precision operations.
The Application area of Radar/Antenna substrate.
Radar and antenna substrates play a vital role in various fields, providing key circuit support and signal transmission functions for the development and application of modern technology.
In the military field, radar and antenna substrates are widely used in various military radar systems, such as air surveillance radar, ground defense radar, and maritime search radar. These systems are critical to the detection, tracking and identification of enemy targets, and high-performance radar/antenna substrates are the basis for their normal operation.
In the aerospace field, radar and antenna substrates are used in communication and navigation systems in aircraft, satellites, spacecraft and other vehicles. They can support data transmission and signal reception during high-speed flight, ensuring the normal operation and mission completion of the spacecraft.
In the field of communications, radar and antenna substrates are key components of wireless communication systems, including mobile communications, satellite communications and wireless networks. By receiving and sending signals, they realize wireless connections between people, people and things, and things and things, and promote the development and popularization of communication technology.
In the automotive field, radar and antenna substrates are widely used in vehicle radar systems, vehicle communication systems, and vehicle navigation systems. They can help realize autonomous driving technology, intelligent traffic management and vehicle interconnection, improving driving safety and comfort.
In the field of consumer electronics, radar and antenna substrates are used for wireless communication and positioning functions in various electronic products such as smartphones, Tabletas, and smart home devices. They can support high-speed data transmission, precise positioning and intelligent control, providing users with a convenient and comfortable experience.
En general, the applications of radar and antenna substrates cover various fields such as military, aeroespacial, communications, automobiles, and consumer electronics, providing indispensable support and infrastructure for the development and application of modern technology.
What are the advantages of Radar/Antenna substrate?
Radar and antenna substrates play a vital role in modern communications and radar technology. Compared with other circuit connection methods, they have many advantages, including but not limited to the following aspects:
High frequency performance
Radar and antenna systems often operate in high-frequency ranges, so the high-frequency performance of the substrate material is critical. Radar/antenna substrates usually use low dielectric constant materials, such as PTFE (Politetrafluoetileno), which can effectively reduce dispersion and attenuation in signal transmission and improve the frequency response and signal transmission efficiency of the system.
Low signal loss
Compared with traditional wiring connections, the radar/antenna substrate uses printed circuit technology, and the connections between circuit components are closer, reducing losses during signal transmission. This design can ensure the signal quality and stability of the system and reduce the bit error rate and error rate of the system.
Good thermal stability
In high-power radar and antenna systems, thermal stability is a critical consideration. Radar/antenna substrates usually use materials with high thermal conductivity and are equipped with heat dissipation designs that can effectively conduct and disperse heat to maintain the stability and reliability of the system during long-term operation.
Design flexibility
When building radar and antenna systems, different frequency, power and size requirements often need to be taken into account. The design flexibility of radar/antenna substrates allows engineers to easily implement the design of different types of systems, including microwave antennas, phased array radars, RF front-end modules, etc. Además, printed circuit technology also makes it possible to integrate multiple functions on the substrate, such as integrated filters, amplifiers, couplers, etc., thus simplifying the layout and design of the system.
En resumen, radar/antenna substrates have many advantages over other circuit connection methods, including high-frequency performance, low signal loss, good thermal stability, and design flexibility. These advantages enable radar and antenna systems to achieve better performance and reliability in various application scenarios, thereby promoting the continuous development and progress of modern communication technology.
Preguntas más frecuentes
How flexible is the radar/antenna substrate design?
Radar/antenna substrates offer high design flexibility and can be custom designed to meet specific application requirements. By selecting the appropriate materials, layout, and hierarchy, designers can implement a variety of functions, including high-frequency transmission, thermal management, and EMI suppression, to meet the requirements of different applications.
What should we pay attention to when maintaining radar/antenna substrates?
Maintenance of radar/antenna substrates typically involves regular inspection and cleaning to ensure connection reliability and performance stability. Además, avoiding excessive heating and mechanical damage is key to maintaining reliable long-term operation of the substrate. For high-performance applications, regular performance testing and calibration is recommended to ensure proper system operation.
What is the cost of the radar/antenna substrate?
The cost of a radar/antenna substrate depends on several factors, including the materials selected, design complexity, production volumes, and manufacturing processes. Generally speaking, the cost of substrates with high frequencies and complex designs is higher, but with the advancement of technology and the expansion of production scale, the cost is gradually declining.
What are the environmental impacts of radar/antenna substrates?
Most of the materials commonly used in radar/antenna substrates are environmentally friendly, such as fiberglass and epoxy resin. However, some waste may be generated during the manufacturing process, so appropriate handling and recycling measures are required to minimize environmental impact.
Can radar/antenna substrates be recycled?
Yes, materials used in radar/antenna substrates such as fiberglass and copper can be recycled. However, because substrates are often tightly integrated with other components, the recycling process can be complex and require specialized equipment and technology.