What are CPU Package Substrates?
Manufacturer Of The CPU Package Substrates.ABC Technologies is a leading manufacturer of CPU package substrates, offering innovative and high-quality solutions tailored to the needs of the semiconductor industry. With advanced production facilities and a commitment to excellence, we ensure that our substrates meet the stringent requirements for performance, reliability, and efficiency, making us a trusted partner for major tech companies worldwide. Our expertise in materials science and engineering drives continuous improvement and supports the evolving demands of modern computing technology.
As an indispensable part of modern electronic equipment, CPU packaging substrate (PCB) carries the important task of connecting and supporting the electrical connection between the CPU and other electronic components. It is called the English abbreviation of “printed circuit board” and is a basic component made of insulating material. Usually, this insulation material is a special epoxy resin, which has good mechanical strength and insulation properties and can reliably support and protect circuits. On the surface of the PCB, it is covered with a layer of metal, usually copper, which is used to transmit signals and power. These metal layers are connected through a series of circuits, connecting the CPU and other electronic components so that the entire circuit system can operate normally.
PCB design and manufacturing is a complex and precise process. During the design stage, engineers need to consider factors such as layout, wire paths, thermal design, etc. to ensure that the circuit board can operate stably under different operating conditions. In the manufacturing process, the design drawing is first converted into an actual printed circuit board through graphical conversion, and then the circuit pattern is printed on the substrate through processes such as printing and metallization. Finalmente, testing and debugging are performed to ensure that the manufactured PCB Meet design requirements and quality standards.
The size of the CPU packaging substrate is usually determined based on the specific CPU and device requirements, and can be a standard size or customized to meet the needs of a specific application. Their application fields are very wide, including computers, Equipos de comunicación, consumer electronics and other fields. In these fields, CPU packaging substrates play the role of connecting and supporting various electronic components, providing key support for the functionality and performance of modern technology products.
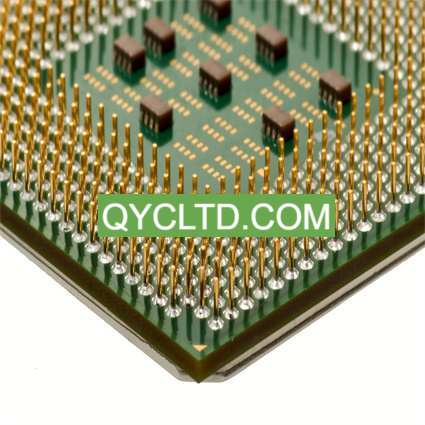
Manufacturer Of The CPU Package Substrates
Compared with traditional circuit wiring, CPU packaging substrates have many advantages. En primer lugar, it has the characteristics of high reliability and can provide stable electrical connection to ensure the normal operation of the entire circuit system. Segundo, due to the compact structure and small size of PCB, it can integrate more electronic components in a limited space and improve the functionality and performance of the device. Además, because the PCB assembly process is automated, the production efficiency is high, large-scale production is possible, and costs are reduced.
En resumen, the CPU packaging substrate, as the basic component that connects and supports the electrical connection between the CPU and other electronic components, plays a vital role in modern electronic equipment. It not only connects various electronic components, but also connects our digital lifestyle and becomes the link between the digital world.
CPU Package Substrates design Reference Guide.
The design of the CPU packaging substrate is critical to the performance and reliability of the device. A sound design guide should include best practices in the following key areas to ensure effective communication and cooling between the CPU and other components:
Layout optimization
Reasonable layout is the key to successful design. By placing critical components (e.g., CPU, memory, interfaces, etc.) in the right locations and taking into account the length and direction of signal transmission paths, signal interference and latency can be reduced, thereby improving system performance.
Wire path design
Well-designed wire paths minimize signal transmission impedance, crosstalk, and signal degradation. Properly planning wire paths, avoiding intersections and sharp angles, and using appropriate interlayer wiring techniques can help improve signal integrity and reliability.
Thermal design
The CPU generates a lot of heat during operation, and effective heat dissipation design can ensure that the CPU operates within an appropriate temperature range to avoid overheating damage. By rationally designing the location, shape, and material of the radiator, as well as adding cooling vents and heat sinks, the heat dissipation efficiency can be improved and the service life of the equipment can be extended.
Ensure signal integrity
Maintaining signal integrity is an important consideration during the design process. Using appropriate impedance matching technology, separation of signal layer and power layer, differential signal routing and other methods can reduce signal distortion and noise and ensure reliable transmission of high-speed signals.
Electromagnetic Compatibility (EMC) Considerations
Electromagnetic interference and anti-interference capabilities should be taken into consideration during the design process. Using appropriate shielding technology, ground wire planning, and reasonable layout and wiring methods can effectively reduce the system’s sensitivity to external interference and improve the system’s anti-interference ability.
Maintainability considerations
Later maintenance and upgrade needs should be taken into consideration during design. Properly arranging the layout of components, marking the location of important components, and leaving enough space for repair and replacement of parts can reduce maintenance costs and improve the maintainability of the system.
En resumen, an excellent CPU packaging substrate design should comprehensively consider factors such as layout, wire paths, heat dissipation design, etc., and adopt corresponding best practices to ensure that the device has good performance and reliability, while reducing production costs and maintenance costs.
What material is used in CPU Package Substrates?
Material selection for a CPU packaging substrate is critical to its performance. As a core component that connects and supports electrical connections between the CPU and other electronic components, it must have a specific set of performance and characteristics to ensure the stability and reliability of the device.
In the material selection of CPU packaging substrate, the most common one is glass fiber reinforced epoxy resin as the substrate material. Epoxy resin is a polymer with excellent mechanical strength and chemical resistance, making it one of the ideal choices for manufacturing PCBs. Glass fiber reinforcement can increase the mechanical strength and heat resistance of the substrate, while improving its insulation properties, thereby reducing the distortion rate during signal transmission. This combination of materials can withstand working conditions in high-temperature and high-pressure environments, ensuring the stability and reliability of the PCB.
Además, copper as a conductive layer is also one of the indispensable materials in the CPU packaging substrate. Copper has good electrical and thermal conductivity, can effectively transmit power and signals, and has good processability, making the PCB manufacturing process more efficient and controllable. By plating a layer of copper on the surface of the substrate, a conductive network can be formed to connect various electronic components to achieve normal operation of the circuit.
En resumen, the materials used in the CPU packaging substrate not only require good electrical conductivity, but also require excellent heat resistance and mechanical strength to ensure stable operation of the device under various environmental conditions. Glass fiber reinforced epoxy resin as the substrate material, and copper as the conductive layer, together form an important part of the PCB, providing a solid support for the functionality and performance of modern electronic devices.
What size are CPU Package Substrates?
The size of the CPU packaging substrate plays a crucial role in electronic device design. It not only determines the volume and shape of the overall device, but also directly affects system performance and heat dissipation. Therefore, when selecting the size, factors such as the power consumption of the CPU, cooling requirements, and space constraints of the device need to be considered.
Típicamente, the size of the CPU packaging substrate is customized based on the specific CPU model and device requirements. For common consumer electronics products, como los teléfonos inteligentes, Tabletas, y ordenadores portátiles, their CPU packaging substrates often adopt standardized sizes to facilitate mass production and assembly.
However, in some specific application scenarios, it is necessary to customize a smaller or larger CPU packaging substrate. For example, in embedded systems, since the device size is usually smaller, more compact packaging solutions are needed to save space. In high-performance computers or servers, in order to meet greater heat dissipation requirements, a larger package substrate may be needed to accommodate more heat dissipation components and fans.
In addition to the physical limitations of size, the complexity of circuit layout and the stability of signal transmission also need to be considered. Therefore, custom-sized CPU packaging substrates often require precise design and simulation to ensure that the layout of various components is reasonable and the reliability and stability of signal transmission are guaranteed.
En general, the size of the CPU packaging substrate is not static, but can be flexibly adjusted according to specific needs and application scenarios. Whether it is a standard size or a customized size, it is designed to meet the functional needs and performance requirements of the device to the greatest extent and bring a better user experience to the user.
The Manufacturer Process of CPU Package Substrates.
The manufacturing process of CPU packaging substrates is a complex and precise process that involves multiple critical steps to ensure the quality and reliability of the final product. The following is the general process of CPU packaging substrate manufacturing:
Design phase
Before manufacturing the CPU packaging substrate, it first needs to be designed. The design process includes determining key factors such as circuit layout, Métodos de conexión, and thermal design. The goal of this phase is to ensure that the performance and functionality of the substrate meet the expected requirements.
Graphical transformation
After the design is completed, the circuit diagram is converted into a graphical file, usually using computer-aided design (CAD) software. These files contain information such as the location, connection method, and circuit path of each component.
After the graphical conversion is completed, the next step is the printing step. This involves the process of transferring the design pattern to the substrate material. Commonly used printing techniques include etching and chemical processing, which ensure the accuracy and clarity of circuit patterns.
Metalization
Once the circuit pattern is printed on the substrate, the next step is metallization. This involves covering a printed circuit pattern with a metal layer, usually using copper. The purpose of metallization is to carry current and signals in a circuit.
Detection
The last critical step is detection. At every stage of the manufacturing process, the CPU packaging substrate needs to be rigorously inspected to ensure there are no defects or errors. These inspections typically include visual inspections, electrical tests, and functional tests to ensure the quality and reliability of the final product.
Through the above steps, the manufacturing process of the CPU packaging substrate is completed. This process is highly automated and sophisticated, requiring a high level of technical and equipment support. The final product will become an important component of various electronic devices, supporting the development and application of modern technology.
The Application area of CPU Package Substrates.
CPU packaging substrates are widely used in various fields, including computers, Equipos de comunicación, and consumer electronics products. In the computer field, the CPU packaging substrate plays the role of connecting the processor, memory, graphics processor and other key components. They are the foundation for building high-performance computer systems, providing users with a fast and stable computing experience. In terms of communication equipment, CPU packaging substrates are used to build network equipment, routers, switches, etc. They enable fast transmission and processing of data, ensuring smooth network operation. Además, consumer electronics products are also one of the important application areas of CPU packaging substrates. For example, devices such as smartphones, Tabletas, televisions, and game consoles all rely on CPU packaging substrates to perform various functions, including processing graphics, playing multimedia content, and connecting to the Internet. En general, CPU packaging substrates provide key support for the functionality and performance of modern technology products. Their widespread application promotes the development of the digital age and brings convenience and innovation to people’s lives.
What are the advantages of CPU Package Substrates?
In modern electronic equipment, the application of CPU packaging substrates has become an indispensable component because of its many advantages over traditional circuit wiring.
En primer lugar, the reliability of the CPU packaging substrate is high. Through professional design and manufacturing processes, the CPU packaging substrate can provide stable and reliable electrical connections, reducing the risk of short circuits and open circuits, thereby ensuring long-term stable operation of the equipment. This kind of reliability is particularly important for various application scenarios, especially fields that require extremely high stability such as industrial control and medical equipment.
Segundo, the CPU packaging substrate is smaller than traditional circuit wiring. By using multi-layer board design and surface mount technology, the CPU packaging substrate can closely arrange electronic components together, effectively saving space inside the device, making the device lighter and more compact, which is conducive to the product’s beautiful design and portability.
Además, the assembly of the CPU package substrate is also easier. Traditional circuit wiring requires manual welding of electronic components, which is not only time-consuming and labor-intensive, but also prone to quality problems such as poor welding. The CPU packaging substrate adopts an automated manufacturing process and uses surface mounting technology to achieve fast and precise installation of components, which greatly improves production efficiency and product quality.
Overall, the high reliability, small size and easy assembly process of the CPU packaging substrate make it an indispensable part of modern electronic equipment. It provides reliable support for the performance improvement and function expansion of various electronic products, and promotes the development process of the digital era.
Preguntas más frecuentes
What should we pay attention to when maintaining the CPU packaging substrate?
To ensure the long-term stable operation of the CPU packaging substrate, regular cleaning is crucial. Use a cleaner to gently wipe the surface to remove dust and dirt while making sure not to damage connectors and components. Also, avoid over-bending or over-stretching the connecting wires to avoid damaging the circuit board.
How to recycle CPU packaging substrates?
The CPU packaging substrate contains a certain amount of metal and plastic, which can be recycled through professional electronic waste recycling channels. Any sensitive information or personal data should be securely removed before recycling to protect privacy.
What impact does the CPU packaging substrate have on the environment?
Because CPU packaging substrates are often composed of a variety of materials, including metals, plastics, and chemicals, there can be environmental impacts during manufacturing and handling. To reduce environmental impact, adopt sustainable manufacturing methods and strictly adhere to relevant waste disposal and recycling regulations.
How to choose a suitable CPU packaging substrate?
Several factors need to be considered when selecting a suitable CPU packaging substrate, including the model and specifications of the CPU, the space constraints of the device, the temperature and humidity of the working environment, etc. It is recommended to work with professional electronic design engineers to select and customize according to specific needs.
How to repair the CPU packaging substrate when the equipment fails?
When equipment fails, you first need to use professional instruments and testing equipment to determine the fault point. If the problem does lie with the CPU packaging substrate, the damaged component or the entire substrate may need to be replaced. It is recommended to seek professional technical support to avoid more serious problems caused by improper maintenance.