What is Flip Chip BGA Substrate?
Flip Chip BGA Substrate Manufacturer.”Flip Chip BGA Substrate Manufacturer” refers to a company specializing in the production of advanced packaging substrates used in Flip Chip Ball Grid Array (BGA) technology. They design and manufacture substrates that facilitate high-density interconnects, superior thermal management, and reliable signal integrity, essential for modern electronic devices.
Flip Chip BGA Substrate (FCBGA substrate) is a key electronic component substrate and is widely used in modern electronic equipment. It is made of insulating materials, usually using FR4 (fiberglass reinforced epoxy laminate) or other high-performance materials to ensure excellent electrical insulation properties and mechanical strength. On these substrates, electronic components are precisely mounted and interconnected through complex conductive traces, pads, and other features.
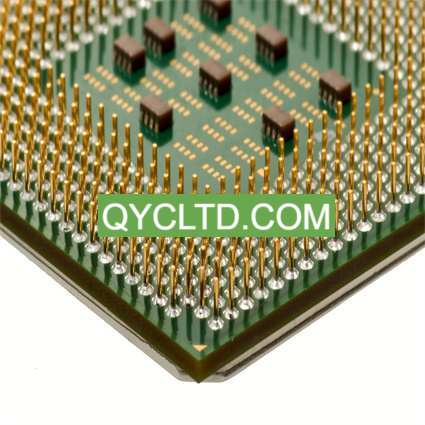
Flip Chip BGA Substrate Manufacturer
One of the key features of FCBGA substrates is their flat-plate structure, which makes them suitable for use in electronic devices that require compact and high-density layouts. Using modern manufacturing processes such as photolithography and etching, copper foil is precisely etched into tiny conductive paths and pads, allowing for reliable connections between electronic components.
In electronics manufacturing, FCBGA substrates are more than just a simple support platform, they also provide critical electrical and structural properties to support the implementation of complex circuits and high-frequency signal transmission requirements. Due to its excellent performance characteristics, FCBGA substrates are widely used in various fields such as communication equipment, computer servers, industrial control systems, and medical diagnostic equipment.
En resumen, FCBGA substrates represent an important technological advancement in modern electronic manufacturing, providing reliable and high-performance solutions for a variety of applications through its precision design and efficient manufacturing process. As technology continues to advance and application fields expand, FCBGA substrates will continue to play a key role in promoting the functionality and performance of electronic devices.
Flip Chip BGA Substrate design Reference Guide.
The Flip Chip BGA Substrate (FCBGA Substrate) Design Reference Guide is an important tool for engineers and designers when creating FCBGA layouts. More than just a technical guide, this comprehensive manual integrates best practices, design rules, software tools, and efficient design techniques to help users optimize and accurately design complex circuit layouts.
During the FCBGA substrate design process, it is crucial to follow best practices. These practices cover how to effectively manage circuit layout to minimize signal interference and electromagnetic compatibility (EMC) issues. The development of design rules is a critical step in ensuring circuit performance and reliability. They define the layout, spacing, and electrical characteristics of various components on the circuit board.
Software tools play a vital role in FCBGA design. From initial concept to final layout, use advanced CAD tools to increase design efficiency and ensure compliance with design rules and circuit requirements. These tools go beyond placement and routing and can perform simulation and analysis to ensure circuit performance and stability.
Effective FCBGA design techniques cover many aspects, including high-density layout, signal integrity analysis, thermal management, power consumption optimization, etc. The application of these technologies can enable smaller and more powerful electronic devices without sacrificing performance and reliability.
In practical applications, design engineers also need to consider manufacturing process constraints and cost-benefit balance. Therefore, the FCBGA Design Reference Guide is not just a technical guide, but also covers practical and economic considerations to ensure that the final design not only meets functional requirements but can also compete in the market.
In short, the FCBGA Substrate Design Reference Guide is an essential manual that provides comprehensive guidance for engineers and designers. It not only helps users master technical details, but also prompts them to make informed decisions during the design process, thereby achieving optimized circuit design and reliable product implementation.
What material is used in Flip Chip BGA Substrate?
FCBGA substrate (Flip Chip BGA Substrate) is an indispensable and key component in electronic equipment, and its choice of materials has an important impact on its performance and application range. Main materials include FR4 and polyimide, which provide diverse solutions for different design needs.
En primer lugar, FR4 material is one of the common choices for FCBGA substrate. It is composed of glass fiber reinforced epoxy resin and has excellent electrical insulation properties and good mechanical strength. This makes FR4 suitable for most conventional PCB applications, such as those widely used in consumer electronics, industrial equipment, and communications technology. The stability and reliability of FR4 material make it the substrate material of choice for many design engineers.
Segundo, polyimide materials have significant advantages in certain specific application scenarios. Flexible FCBGA substrates usually use polyimide, a material with excellent high temperature resistance and excellent flexibility, allowing the substrate to be used in devices that require bending or bending adaptation, such as in medical electronics, flexible displays, and wearable technology middle. The primary advantage of polyimide substrates is their ability to provide stable electrical performance under a wide range of extreme environmental conditions while maintaining their physical strength and durability.
In short, the material selection of FCBGA substrate is crucial, and design engineers must choose suitable materials based on specific application requirements and environmental conditions. As mainstream materials, FR4 and polyimide each provide a wide range of choices in terms of electrical performance, mechanical strength and application flexibility, providing a solid foundation for the design and manufacturing of modern electronic equipment.
What size are Flip Chip BGA Substrate?
As a key component in modern electronic equipment, FCBGA substrates have diverse sizes depending on application requirements. From tiny smartphones and wearable devices to huge industrial equipment and power electronic devices, the size of FCBGA substrates plays an important role in various application scenarios.
In smartphones and wearable devices, FCBGA substrates are usually very small and delicate. Since these devices need to be lightweight and highly integrated, the size of the FCBGA substrate is limited to a very compact range. This miniaturization not only helps reduce the size of the device, but also improves its performance and battery life.
In comparison, FCBGA substrates used in industrial equipment and power electronics are typically larger. These application scenarios require substrates to carry more electronic components and complex circuit designs. Therefore, the size of the FCBGA substrate can be adjusted and optimized based on the availability of space inside the device and the size of the electronic components.
Whether they are tiny or large FCBGA substrates, their design and manufacturing must take into account factors such as the functional requirements, Requisitos de disipación de calor, and reliability of electronic devices. The choice of size not only affects the overall performance of the device, but is also directly related to manufacturing cost and production efficiency.
En resumen, the size of FCBGA substrates varies due to the wide range of applications. With proper design and manufacturing, FCBGA substrates can achieve optimized performance and reliability in various electronic devices, promoting the development and application of modern technology.
The Manufacturer Process of Flip Chip BGA Substrate.
The manufacturing process of Flip Chip BGA Substrate (FCBGA substrate) is a precise and multi-step process, covering a variety of key technologies and engineering processes to ensure the quality and reliability of the final product. The following is a detailed description of the FCBGA substrate manufacturing process:
En primer lugar, choosing a suitable substrate material is the first step in manufacturing FCBGA substrate. Commonly used materials include FR4 (fiberglass reinforced epoxy laminate), which provides good electrical insulation and mechanical strength. The thickness and size of the substrate are selected according to the design requirements, and the necessary surface treatment is performed to ensure the accuracy and reliability of subsequent process steps.
A thin-film copper layer is deposited on the surface of the substrate, which is key to subsequent circuit connections. Through chemical deposition or electroplating, a uniform copper layer is formed on the surface of the substrate to facilitate the subsequent formation and connection of circuit lines.
A photosensitive material (photoresist) is coated on the copper layer and exposed through a UV light source. During the exposure process, a mask is used to expose unwanted areas to light to form conductive paths for future circuit boards.
Chemical etching is used to remove the portion of the copper layer that is not protected by the photosensitive material. This step allows the designed circuit lines to be clearly visible on the surface of the substrate and enables isolation and connection between circuits.
Using high-precision drilling equipment, holes are drilled into the circuit board at predetermined locations for subsequent component installation and plug-in connections. These holes are used not only for circuit connections but also for fixing and aligning components.
Electronic components are precisely mounted on the substrate at predetermined locations using surface mount technology (SMT) or through-hole mounting technology. SMT technology is suitable for fast automated installation of small, high-density components, while through-hole mounting is suitable for larger components and applications that require additional strength support.
After completing component installation, soldering is performed to ensure electrical and mechanical connections between the electronic components and the substrate. Use hot air baking or reflow soldering technology to melt and fix the solder on the pad to ensure the reliability and stability of the connection.
Finalmente, conduct comprehensive functional and electrical performance tests to verify whether the various indicators of the FCBGA substrate meet the design requirements. Testing includes circuit connectivity, component function testing and environmental adaptability, etc. to ensure that the manufactured FCBGA substrate can work reliably in various application scenarios.
En resumen, the manufacturing process of FCBGA substrate covers multiple key steps, from material selection to final testing. Each link requires precise process control and technical support to ensure the high quality and performance stability of the product. The application of these technologies and processes has made FCBGA substrate an indispensable and important part of modern electronic equipment.
The Application area of Flip Chip BGA Substrate.
As a key component of modern electronic equipment, FCBGA substrate (Flip Chip BGA Substrate) is widely used in many important industries. They not only support the development of consumer electronics, but also play an important role in fields such as telecommunications, automobiles, aeroespacial, Equipos médicos, and industrial automation.
In the field of consumer electronics, FCBGA substrates are widely used in high-end electronic devices such as smartphones, Tabletas, y ordenadores portátiles. These devices are favored by consumers for their high performance and compact design, and the tiny size and high integration level of the FCBGA substrate are key to achieving these characteristics.
In the telecommunications industry, FCBGA substrates are used in key facilities such as network equipment and communication base stations to support stable and efficient communication network operations. They can handle complex data transmission and processing tasks, ensuring rapid information transmission and processing efficiency.
In the automotive field, FCBGA substrates are used in vehicle electronic systems, such as vehicle infotainment systems, body control units, etc. They not only improve the intelligence and safety performance of the vehicle, but also support the vehicle’s real-time monitoring and response to the external environment.
In the aerospace field, FCBGA substrates are used in aircraft navigation, communication, control and data processing systems. These systems are critical to the stable flight and safety of the spacecraft, and the high reliability and vibration resistance of the FCBGA substrate make it the component of choice.
In the field of medical equipment, FCBGA substrates are used in various medical imaging equipment, diagnostic instruments and treatment equipment to support the advancement of medical technology and patient diagnosis and treatment effects. These devices are crucial for accurate and reliable data processing and transmission, and the stability and accuracy of FCBGA substrates can meet the stringent requirements of medical equipment.
In the field of industrial automation, FCBGA substrates are widely used in control systems, robots and sensor networks to achieve automation and intelligence in the production process. They can handle complex control algorithms and data transmission, improving factory production efficiency and product quality.
In short, as a core component of modern electronic technology, FCBGA substrate not only supports the functions and performance of various electronic devices, but also promotes technological innovation and application expansion in multiple key industries. With the advancement of technology and the growth of market demand, FCBGA substrates will continue to play an indispensable role in promoting the development of the entire electronics industry.
What are the advantages of Flip Chip BGA Substrate?
As a key component of modern electronic equipment, FCBGA substrate (Flip Chip BGA Substrate) has many significant advantages over traditional wiring methods, making it widely favored in various applications.
En primer lugar, the FCBGA substrate stands out for its excellent compactness. Due to the adoption of advanced flip chip (Flip Chip) technology and BGA (Ball Grid Array) packaging, FCBGA substrates can achieve a high degree of integration of complex circuits in a limited space, thus significantly promoting the miniaturization and lightweight development of electronic equipment. . This compact layout not only saves space inside the equipment, but also improves the overall performance and reliability of the product.
Segundo, FCBGA substrate performs well in terms of reliability. The use of standardized manufacturing processes and strict quality control processes ensures the stable quality and reliability of each FCBGA substrate. This consistency allows the FCBGA substrate to exhibit excellent electrical performance and long-term stable working capabilities under various environmental conditions, greatly improving the service life of the equipment and customer satisfaction.
Tercero, the FCBGA substrate shows significant assembly convenience during the production and assembly process. The widespread application of automated assembly technology has greatly improved the production efficiency of FCBGA substrates and reduced labor costs. This not only shortens product time to market, but also ensures consistency and repeatability in the production process, further enhancing the overall efficiency and competitiveness of the production line.
Además, the FCBGA substrate has excellent customizability and can be designed and customized according to customer-specific needs. Whether in the design of complex circuits or the integration of various components, FCBGA substrates can provide flexible solutions to meet the needs of different industries and applications. This flexibility makes the FCBGA substrate particularly suitable for rapid prototyping in the R&D stage and mass production in the mass production stage, further reducing the overall cost and improving market competitiveness.
Overall, FCBGA substrate has become an indispensable and important part in the design and manufacturing of modern electronic equipment due to its compact, reliable, efficient characteristics, as well as superior economy and customization capabilities. As technology continues to advance and market demand grows, FCBGA substrates will continue to play a key role in promoting innovation and development in the electronics industry.
Preguntas más frecuentes
What is the difference between FCBGA substrate and traditional PCB?
There are significant differences in the interconnection methods between FCBGA substrates and traditional Printed Circuit Boards (Placas de circuito impreso). FCBGA substrate uses Flip Chip technology, that is, the chip is directly flip-chip mounted on the substrate and connected through microscopic solder balls, while traditional PCB is connected through pins or connectors of electronic components. This gives FCBGA substrates advantages in smaller size, faster signal transmission and higher circuit density.
What are the design considerations for FCBGA substrates?
When designing FCBGA substrates, key considerations include thermal management, signal integrity, Compatibilidad electromagnética (EMC), package sealing, and component layout optimization. Especially in high-frequency applications, attention should be paid to the length and matching of signal transmission paths to ensure reduced signal loss and crosstalk.
How complex is the manufacturing process of FCBGA substrates?
The manufacturing process of FCBGA substrates involves multiple precise steps, including substrate pre-processing, patterned copper layer etching, precise coating and welding of solder balls, precise component installation and subsequent testing and quality control. These steps require a high degree of automation and sophisticated equipment to ensure the production of high-quality and reliable substrates.
How to choose a suitable FCBGA substrate material?
When selecting FCBGA substrate materials, factors such as the temperature range of the working environment, mechanical strength requirements, dielectric properties, and chemical stability need to be considered. Commonly used materials include FR4 and polyimide (PI), the latter of which is suitable for flexible FCBGA substrates and can meet the needs of high-temperature and high-frequency applications.