What are CPU Ball Package Substrates?
CPU Ball Package Substrates Manufacturer. A leading manufacturer of CPU ball package substrates, our company excels in precision engineering and advanced material science. With state-of-the-art facilities and a dedicated team of experts, we deliver substrates of unparalleled quality and reliability. Our innovative designs ensure optimal performance and durability, meeting the rigorous demands of modern computing applications. From initial concept to final production, we prioritize excellence, consistently exceeding industry standards. Trusted by top-tier CPU manufacturers worldwide, we are committed to driving technological advancements and shaping the future of computing through our cutting-edge solutions.
In modern electronic devices, the CPU (Central Processing Unit) is considered the brain, which is responsible for processing and performing various computing tasks. As an important auxiliary component, the CPU ball packaging substrate plays a key role in connecting and supporting the CPU chip. Let’s take a closer look at this key technology.
The CPU ball package substrate is a basic material used to support and connect CPU chips. It acts as a bridge connecting the CPU chip to the motherboard (usually a printed circuit board). The core feature of this substrate is that it uses spherical pads as connecting components. These spherical pads are connected to the CPU chip and the motherboard through a special welding process to achieve electrical connection and signal transmission.
Compared with traditional flat soldering technology, the CPU ball package substrate has unique advantages. Primero, ball pads can provide more connection points, resulting in higher connection density and more reliable connections. Segundo, the structure of the spherical pad can reduce stress and improve the stability and durability of the connection. Además, the spherical pad also has a certain degree of elasticity and can adapt to temperature changes and mechanical vibration, thus enhancing the reliability of the connection.
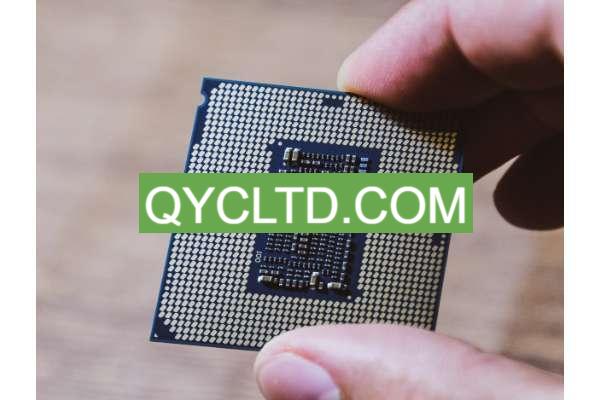
CPU Ball Package Substrates Manufacturer
In the manufacturing process of CPU ball packaging substrates, high-performance base materials and precise manufacturing processes are required. Common substrate materials include FR-4 fiberglass composite materials, which have excellent electrical properties and mechanical strength and are suitable for high-density connection applications. The manufacturing process involves multiple links such as design, pattern conversion, imprenta, Grabado químico, ball pad manufacturing, assembly and testing. Each link requires strict control and precision operation to ensure the quality and performance of the final product.
In practical applications, CPU ball packaging substrates are widely used in various electronic products, including personal computers, servers, smartphones, Tabletas, and embedded systems. Its stability and high performance make it a key component of modern electronic equipment, providing solid support for the device’s performance and functionality.
En resumen, CPU ball packaging substrates play an important role in modern electronic equipment. Through its unique design and excellent performance, it provides a reliable solution for CPU chip connection and signal transmission, promoting the development and innovation of electronic products.
CPU Ball Package Substrates design Reference Guide.
In modern electronic equipment, the CPU ball packaging substrate plays a vital role, and its design quality directly affects the performance and stability of the entire system. In order to ensure that the design of the CPU ball package substrate can meet the high performance and high reliability requirements, engineers need to follow a series of design guidelines and best practices. This article will introduce the CPU ball package substrate design reference guide to help engineers make better decisions during the design process.
Layout design
In the layout design of the CPU ball package substrate, engineers need to consider factors such as the layout of electrical connections, signal integrity, heat dissipation effect, and ease of assembly. Reasonable layout design can minimize signal interference and electrical noise and improve system stability and performance.
Component placement
The placement of components on the CPU ball package substrate needs to take into account factors such as the functional requirements of the circuit, signal transmission paths, and heat dissipation requirements. Proper component placement optimizes circuit performance and ensures good electrical connections and thermal conduction between components.
Signal integrity
In the design of CPU ball packaging substrate, engineers need to pay special attention to signal integrity issues. Through proper signal routing, ground design, and power distribution, signal distortion and clock drift can be minimized and system stability and reliability improved.
Gestión térmica
Thermal management of the CPU ball package substrate is a critical design consideration. Reasonable heat dissipation design can effectively reduce CPU temperature and improve system stability and performance. Engineers can use technologies such as heat sinks, heat sinks and heat pipes to achieve good thermal management.
Selección de materiales
In the design process of CPU ball packaging substrate, appropriate material selection is crucial. Engineers need to choose high-performance base materials, copper foil with good conductivity, and high-temperature and corrosion-resistant solder mask materials to ensure that the CPU ball packaging substrate has excellent electrical performance and stability.
En resumen, the CPU Ball Package Substrate Design Reference Guide provides engineers with valuable design suggestions and guidance. By following these guidelines, engineers can design CPU ball packaging substrates with excellent performance, stability and reliability, and promote the progress and innovation of electronic products.
What material is used in CPU Ball Package Substrates?
In the manufacturing of CPU ball packaging substrates, the materials used are crucial, as they directly affect the performance, reliability and stability of the substrate. The following are materials commonly used for CPU ball packaging substrates:
Base material
The base material of CPU ball packaging substrate is usually made of high-performance glass fiber composite material, and the most common one is FR-4 base material. FR-4 substrate has excellent electrical insulation properties, mechanical strength and heat resistance, and is suitable for applications under various environmental conditions.
Copper foil
Copper foil is the main conductive layer material of the CPU ball packaging substrate and is used to make circuit connection lines. High-purity copper foil has good electrical conductivity and mechanical strength, ensuring the stability and reliability of circuit connections.
Solder mask
The solder mask usually covers the surface of the CPU ball package substrate to prevent short circuits and corrosion, and to provide protection and identification. Commonly used solder mask materials include green, red and blue epoxy resins, which have good heat resistance and chemical stability.
Solder paste
Solder paste is the key material used to make the ball-shaped pads on the CPU ball package substrate. Solder paste is usually made from a metal alloy that conducts electricity well, such as tin-lead alloy or lead-free solder. It has good soldering performance and heat resistance, ensuring the connection quality and stability of ball pads.
Chemical materials
The manufacturing process of CPU ball packaging substrates also requires the use of various chemical materials, such as etching liquids, cleaning agents and solder mask inks. These chemical materials play a key role in the manufacturing process, ensuring the flatness and cleanliness of the substrate surface and improving welding quality and reliability.
En resumen, while ensuring the stability and reliability of circuit connections, the materials used in CPU ball packaging substrates must also take into account factors such as the material’s mechanical properties, heat resistance, and chemical stability. By selecting appropriate materials and strictly controlling the manufacturing process, the CPU ball packaging substrate can be ensured to have excellent performance and long-term reliability to meet the needs of various electronic products.
What size are CPU Ball Package Substrates?
When it comes to the sizes of CPU Ball Package Substrates, they usually depend on the package type of the CPU chip and the application requirements. These substrates can be relatively small in size to accommodate compact electronic devices or relatively large for high-performance computing and server applications. Here are some more details on CPU Ball Package Substrates dimensions:
Small size
For applications such as mobile devices and embedded systems, CPU Ball Package Substrates are typically smaller in size. This small size helps reduce the size and weight of the device, making it more lightweight and portable. For example, CPU Ball Package Substrates for mobile devices such as smartphones and tablets may be only a few centimeters in size to meet compact design requirements.
Medium size
The size of CPU Ball Package Substrates is usually in the middle range for some mid-sized electronic devices such as personal computers and consumer electronics. This size can accommodate more electronic components and connection lines to meet the functional needs of the device. Generally speaking, these dimensions range from a few tens to a hundred square millimeters.
Large size
In high-performance computing and servers, CPU Ball Package Substrates are often larger in size. These large substrates can accommodate more CPU cores and memory chips to support complex computing tasks and large-scale data processing. Its size may exceed one hundred square millimeters or even larger to accommodate the layout and connection needs of high-density integrated circuits.
Custom size
In addition to the common small, medium and large sizes, some specific applications may require custom sized CPU Ball Package Substrates. These substrates can be designed and manufactured to customer specific requirements to ensure optimal performance and adaptability.
Overall, CPU Ball Package Substrates come in a wide range of sizes and can be customized for different application needs. Whether it’s a small mobile device or a large server, you can find the right size substrate to meet your design and performance requirements.
The Manufacturer Process of CPU Ball Package Substrates.
The manufacturing process of CPU ball packaging substrate is a complex and precise process that requires a high degree of technology and strict quality control. The following is a detailed introduction to the process:
Design and graphical conversion
The first step in the manufacturing process is designing according to the specifications and dimensions of the CPU chip. Design engineers use professional software to perform circuit layout and connection design to ensure the reliability of electrical connections and signal transmission between the CPU and the substrate. Una vez que el diseño esté completo, a graphical conversion takes place to convert the design drawings into actual manufacturing documents.
Printing and chemical etching
Next comes the printing stage, where the substrate surface is covered with a conductive copper foil pattern. These patterns will define the connections between the CPU chip and other components. Subsequently, chemical etching techniques are used to remove unwanted portions of the copper foil, leaving the desired circuit pattern.
Making ball pads
The ball pad is a key part of connecting the CPU chip to the motherboard. In this step, small spherical solder joints are formed on the substrate through mechanical or chemical methods. These solder joints are usually composed of tin-lead alloy, which provides good soldering performance and durability.
Assembly and testing
Once the substrate is prepared, it is assembled and tested. CPU chips and other electronic components will be precisely placed on the substrate and secured through soldering or other connection techniques. Strict functional testing and performance verification are then carried out to ensure that the manufactured CPU ball packaging substrate meets the specifications.
Final inspection and packaging
Finalmente, the manufacturer will perform final inspection and packaging of the finished product. Ensure the quality and performance of each substrate is up to standard through visual inspection and electrical testing. They are then packaged into products that meet shipping and storage requirements and are ready for shipment to customers or assembly plants.
En general, the manufacturing process of CPU ball packaging substrates involves multiple precise steps and strictly controlled processes. Only by strictly implementing quality standards and process requirements at every stage can the stability and reliability of the final product be ensured.
The Application area of CPU Ball Package Substrates.
CPU ball packaging substrates are widely used in modern electronics. Its stability and high performance make it a key component of various electronic products. The following is the application of CPU ball packaging substrates in different application fields:
Personal computers (PCs) y ordenadores portátiles
In personal computers and laptops, CPU ball packaging substrates are used to connect the main processor (CPU) and the motherboard to ensure system stability and performance. These substrates typically feature high-density wiring to meet the high-speed data transmission and processing capabilities required by PCs and laptops.
Servers and Data Centers
In the fields of servers and data centers, CPU ball packaging substrates are widely used to build high-performance computing systems. These substrates not only require stable electrical connections and signal transmission, but also require good heat dissipation design and reliability guarantee to meet the needs of large-scale data processing and storage.
Smartphones and Tablets
The miniaturization and lightweight of smartphones and tablets poses challenges to CPU ball packaging substrates, which require high-density wiring and complex functions in a limited space. These substrates often use advanced manufacturing processes and materials to achieve higher levels of integration and performance.
Automotive electronics and industrial control systems
In automotive electronics and industrial control systems, CPU ball packaging substrates are used to control and monitor various systems and equipment. These substrates need to be able to operate stably in harsh environmental conditions and be resistant to vibration, interference, and high temperatures.
Embedded systems and IoT devices
In embedded systems and IoT devices, CPU ball packaging substrates are widely used to connect various sensors, actuators and communication modules to achieve data collection, processing and transmission. These substrates usually feature low power consumption, small size, and high integration to meet the resource constraints of embedded systems and the portability requirements of IoT devices.
En resumen, CPU ball packaging substrates play an important role in various application fields and provide key support for the performance and functionality of modern electronic products. Con el continuo avance e innovación de la tecnología, CPU ball packaging substrates will continue to develop and promote the continued development and progress of the electronic industry.
What are the advantages of CPU Ball Package Substrates?
CPU ball packaging substrates have many advantages over traditional packaging methods, and these advantages play a vital role in the design and manufacturing of modern electronic products. The following is a detailed discussion on the advantages of CPU ball packaging substrates:
Small size
The CPU ball packaging substrate uses advanced packaging technology to achieve a more compact size design. Compared with traditional packaging methods, they are more suitable for the layout of high-density integrated circuits, making it possible to miniaturize and lightweight electronic devices.
Reliable connection
The spherical pad design of the CPU ball package substrate improves the reliability of the connection. Compared with traditional welding methods, the spherical pad provides more welding contact points, effectively reducing stress concentration during welding, thereby reducing the risk of welding point breakage.
Stable performance
Because the CPU ball packaging substrate uses high-performance base materials and advanced manufacturing processes, its performance stability is effectively guaranteed. These substrates have good electrical characteristics and thermal management capabilities, ensuring the stable operation of the CPU chip under various working conditions.
Adaptable
The CPU ball packaging substrate has strong adaptability and can meet the needs of different application scenarios. They can be custom designed according to customer requirements, including parameters such as size, number of layers, electrical characteristics and thermal management, to accommodate various complex electronic system designs.
Optimize heat dissipation
Through the spherical pad design, the CPU ball package substrate effectively improves the heat dissipation effect of the product. The spherical pad provides a larger contact area and better thermal conductivity, helping to quickly transfer the heat generated by the CPU chip to the surrounding environment and maintain the normal operating temperature of the chip.
En resumen, the CPU ball package substrate has obvious advantages in terms of size, Fiabilidad de la conexión, performance stability, adaptability and heat dissipation effect. These advantages make them an indispensable and important component in the design and manufacturing of modern electronic products, providing strong support and guarantee for the development and innovation of the electronics industry.
Preguntas más frecuentes
What are the advantages of CPU ball packaging substrate compared with traditional packaging methods?
CPU ball packaging substrates have many advantages over traditional packaging methods. Primero, its spherical pad design improves the reliability and durability of the connection and reduces connection failures caused by changes in the external environment. Segundo, the size of the CPU ball packaging substrate is relatively small, which helps to reduce the overall packaging volume and improve the integration and reliability of the product. Además, the ball packaging method makes the heat dissipation effect better, which is conducive to the long-term stable operation of the CPU chip.
Is the manufacturing process of CPU ball packaging substrate complicated?
The manufacturing process of CPU ball packaging substrate is relatively complex and involves multiple links and process steps. For example, steps such as pattern conversion, imprenta, Grabado químico, and ball pad manufacturing require sophisticated equipment and technical support. However, with the continuous advancement of manufacturing technology and the improvement of automation level, the manufacturing process has become more efficient and controllable.
In what fields are CPU ball packaging substrates widely used?
CPU ball packaging substrates are widely used in various electronic products, including personal computers, servers, smartphones, Tabletas, and embedded systems. Its stability and high performance make it a key component of modern electronic equipment.
What issues should be paid attention to in the design of CPU ball packaging substrate?
When designing a CPU ball package substrate, you need to pay attention to many aspects. The first is the circuit layout, which must ensure the stability and reliability of signal transmission; the second is the heat dissipation design, which must reasonably lay out the heat dissipation components to ensure that the temperature of the CPU chip is controlled within a safe range; in addition, EMI (electromagnetic interference) and EMC ( Electromagnetic compatibility) and other issues to ensure that the product complies with relevant electromagnetic standards and regulations.
How long is the lifespan of a CPU ball package substrate?
The life of the CPU ball package substrate depends on many factors, including material quality, manufacturing process, environmental conditions and usage patterns. Under normal circumstances, a properly designed and manufactured CPU ball packaging substrate can have a long service life and meet the normal use requirements of the product.