What are Chip Package Substrates?
Chip Package Substrates Manufacturer.A leading producer in the semiconductor industry, our company specializes in the fabrication of chip package substrates. With state-of-the-art facilities and a commitment to innovation, we engineer substrates tailored to the specific needs of integrated circuit manufacturers. Our advanced manufacturing processes ensure precision and reliability, meeting the stringent demands of modern electronics. From compact mobile devices to complex computing systems, our substrates form the foundation for high-performance semiconductor packages. Collaborating closely with clients, we deliver customized solutions that drive technological advancement and empower the next generation of electronic devices.
Chip packaging substrates are an integral part of modern electronic devices, providing critical support and connection functions for electronic components. This substrate is usually made of non-conductive materials such as fiberglass, epoxy or composites. These materials have good insulating properties and can effectively isolate electrical signals between electronic components and prevent short circuits and other circuit failures.
In the manufacturing process of chip packaging substrates, it is first necessary to prepare the substrate material and ensure that its surface is flat. Then, through etching or printing technology, conductive paths are formed on the surface of the substrate, which is what we often call electrical traces. The design and layout of these traces is very important, as they determine how electronic components are connected and the signal path is transmitted.
Once the traces are formed, the next step is to mount the electronic components on the substrate. These components can be various chips, transistors, capacitors, resistors, etc. They are connected to traces via soldering or other connection techniques to provide electrical connection and functionality.
Chip packaging substrates are widely used in almost all modern electronic equipment manufacturing fields. From smartphones and tablets to automotive electronics, Equipos médicos, and industrial control systems, they are all inseparable from the support of chip packaging substrates. These substrates not only provide electrical connections, but also play an important role in stabilizing and protecting electronic components, ensuring proper operation and long-term reliability of the equipment.
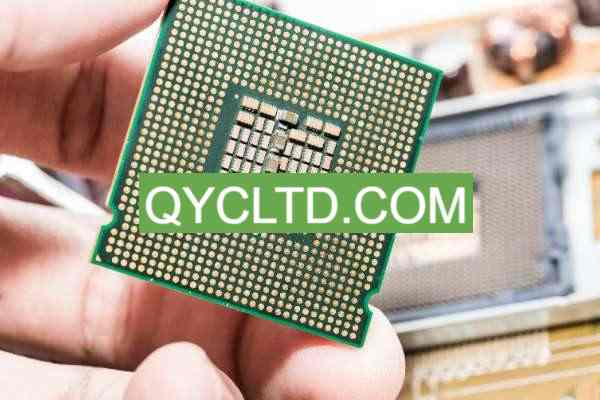
Chip Package Substrates Manufacturer
En general, chip packaging substrates have an irreplaceable position in the modern electronics industry. They are not only the basic building blocks of electronic equipment, but also key components to achieve circuit function and performance. With the continuous development of electronic technology, the manufacturing processes and materials of chip packaging substrates will continue to be innovated to meet changing market demands and technical challenges.
Chip Package Substrates design Reference Guide.
Chip packaging substrate design is a crucial part of modern electronic engineering. Good design ensures that electronic equipment performs stably, reliably, and meets the needs of specific applications. The following is a reference guide on chip packaging substrate design, designed to help engineers and designers formulate high-quality chip packaging substrates.
Design software selection
It is crucial to choose professional software suitable for chip packaging substrate design. Commonly used design software includes Altium Designer, Cadence Allegro, Mentor Graphics PADS, etc. Make sure the software you choose has powerful features and an easy-to-use interface to improve design efficiency and quality.
Component layout
Reasonable component layout is the key to ensuring stable performance of chip packaging substrates. During the layout process, Factores como la integridad de la señal, Compatibilidad electromagnética, and thermal management should be considered, and the length and crossover of signal lines should be minimized to reduce crosstalk and signal loss.
Trace layout
Trace layout should follow best practices to ensure good signal integrity and electrical performance. During the layout process, avoid traces that are too long, too narrow, or too close to other signal lines or edges to reduce the effects of signal distortion and crosstalk.
Power consumption and thermal management
Reasonable power consumption and thermal management design are crucial to the stable operation of chip packaging substrates. Durante el proceso de diseño, the power consumption distribution of components, heat dissipation structure, and heat dissipation material selection should be taken into consideration to ensure that the chip does not overheat during operation.
Manufacturing feasibility
Considering manufacturing feasibility during the design process is key to ensuring smooth production of chip packaging substrates. Avoid overly complex designs or the use of overly special materials and processes to reduce manufacturing costs and production risks.
Testing and Validation
After the design is completed, comprehensive testing and verification must be performed to ensure that the chip packaging substrate meets the design specifications and performance requirements. Commonly used testing methods include electrical testing, functional testing, reliability testing, etc.
Keep improve
Chip packaging substrate design is a continuous improvement process. By collecting user feedback, continuously optimizing the design process and adopting new technologies, we continue to improve the performance and reliability of chip packaging substrates.
En resumen, chip packaging substrate design is a complex and important task that requires comprehensive consideration of multiple factors. Following the above guidelines and combining them with actual application requirements can help designers develop high-quality, high-performance chip packaging substrates, thereby promoting the development and application of electronic products.
What material is used in Chip Package Substrates?
In the modern electronics industry, chip packaging substrates are a vital technology, and their selected materials play a crucial role in their performance and scope of application. Generalmente, the main material used for chip packaging substrates is fiberglass reinforced epoxy resin (FR4). This material combines good mechanical strength and electrical properties and is suitable for most applications.
FR4 material is widely used due to its good insulation properties, heat resistance and mechanical strength. Its manufacturing cost is relatively low, it is suitable for mass production, and it can meet the requirements of many applications. However, in some special applications, a higher level of performance and characteristics is required, and other materials need to be selected.
Ceramics are a common alternative material with excellent high temperature resistance and good dielectric properties. Due to their stability and reliability, ceramic substrates are commonly used in high-frequency and high-power applications such as microwave communications and radio frequency electronics.
Another option is polyimide (PI) sustrato, which offers excellent mechanical properties, chemical resistance, and high temperature resistance. This material is commonly used in applications requiring high temperatures and corrosive environments, such as electronics in the aerospace and automotive industries.
In some special cases, metal substrates are also used as materials for chip packaging substrates. Metal substrates have excellent thermal conductivity properties and can be used in applications requiring efficient heat dissipation, such as high-power LED lighting and motor drives.
Overall, choosing the right material depends on the requirements of the application, including factors such as operating environment, frequency range, power requirements and reliability needs. Therefore, when designing chip packaging substrates, the characteristics of the selected materials must be carefully considered to ensure that the final product can meet its expected performance and reliability requirements.
What size are Chip Package Substrates?
The size of chip package substrates (Chip Package Substrates) varies from application to application and depends on the needs of the specific electronic device or system. They can be tiny, used in smartphones, wearables and portable electronics, or larger, used in areas such as industrial automation, communications infrastructure and automotive electronic control systems.
Típicamente, the size of the chip packaging substrate is designed based on factors such as required circuit complexity, number of components, and assembly space. Small chip packaging substrates may only have an area of a few square millimeters, while large chip packaging substrates can reach tens or even hundreds of square centimeters.
In portable devices such as mobile phones, chip packaging substrates are usually designed to be as small as possible to save space and achieve thinner and lighter products. This miniaturization also allows for greater circuit integration, thereby improving device performance and efficiency.
Conversely, in some industrial applications, chip packaging substrates may need to be larger in size to accommodate more electronic components and provide more connection points to meet complex system requirements. These large substrates are often designed to be more rugged to handle harsh operating environments and vibration conditions.
En general, the size of chip packaging substrates is customized according to specific application requirements, taking into account not only functional and performance requirements, but also the physical size and assembly requirements of the product. Therefore, during the design process, engineers need to consider many factors to ensure that the chip packaging substrate can achieve the best results in a specific application.
The Manufacturer Process of Chip Package Substrates.
The manufacturing process of chip packaging substrates is a complex and precise process involving multiple critical steps, each of which is critical to the quality and performance of the final product. The following will introduce the manufacturing process of chip packaging substrate in detail:
Substrate preparation
The first step in the manufacturing process is to prepare the substrate. Commonly used substrate materials include fiberglass reinforced epoxy resin (FR4), etc. En esta etapa, the surface of the substrate may require cleaning and surface treatment to ensure smooth progress in subsequent process steps.
Layer alignment
Layer alignment is the process of aligning and stacking conductive layers on a multilayer substrate. In this step, it is crucial to ensure accurate alignment between the layers to ensure that the final conductive paths are connected correctly.
Conductive trace etching or printing
Forming conductive paths on a substrate is one of the core steps in chip packaging substrate manufacturing. This can be achieved through methods such as chemical etching or printing conductive ink. The design and fabrication of conductive paths require precise process control to ensure the reliability and stability of circuit connections.
Component hole drilling
After the conductive paths are formed, holes need to be drilled into the substrate to mount the electronic components. These holes need to be positioned accurately to ensure subsequent component installation and connection quality.
Pad coating
To enhance the connection between electronic components and conductive paths, the surface of the substrate needs to be coated with pads. The soldering pad is usually composed of solder paste or other soldering materials and is used to form a reliable soldering connection with the soldering surface after the component is mounted.
Component assembly
After the pads are coated, the electronic components are mounted into the pre-drilled locations. This includes different assembly methods such as Surface Mount Technology (SMT) and Through-Hole Technology (THT). Select the appropriate assembly technology according to the design requirements.
Test
Finalmente, the final step in the manufacturing process is testing of the chip packaging substrate. This includes electrical testing, functional testing, reliability testing, etc. to ensure that the manufactured substrate meets specifications and has stable and reliable performance.
En resumen, the manufacturing process of chip packaging substrates requires strict process control and quality management, and every step is crucial. Only through careful design and precision manufacturing can high-quality and reliable chip packaging substrates be produced, providing a solid foundation for the normal operation of electronic equipment and systems.
The Application area of Chip Package Substrates.
Chip packaging substrates play an indispensable role in today’s technology field and are widely used in multiple industries, incluida la electrónica de consumo, automotive, aeroespacial, Equipos médicos, communications, and industrial automation. The specific applications of chip packaging substrates in these fields will be introduced in detail below.
In the field of consumer electronics, como los teléfonos inteligentes, Tabletas, smart home devices, etc., chip packaging substrates are widely used. As the core components of electronic equipment, they carry electronic components of various functional modules, such as processors, memories, sensors, etc., making the equipment intelligent and multi-functional.
In the automotive industry, chip packaging substrates are used in vehicle electronic systems, como las unidades de control del motor (ECU), anti-lock braking systems (ABS), vehicle entertainment systems, etc. They provide stable and reliable electrical connections, ensuring vehicle performance and safety.
In the aerospace field, chip packaging substrates are used in key equipment such as flight control systems, Sistemas de navegación, and communication systems. They are lightweight and highly reliable, and can adapt to harsh aerospace environments and complex aircraft requirements.
In the field of medical equipment, chip packaging substrates are used in medical imaging equipment (such as X-ray machines, MRI, CT, etc.), patient monitoring equipment, instrumentos quirúrgicos, etc. They provide precise and reliable electrical connections, ensuring the accuracy and stability of medical equipment.
In the field of communications, chip packaging substrates are used in network equipment such as communication base stations, routers, and switches. They can support high-speed data transmission and complex communication protocols to ensure the stable operation of communication networks.
In the field of industrial automation, chip packaging substrates are used in automation equipment such as PLC controllers, sensors, and actuators. They can achieve efficient communication and precise control between equipment, improving the automation level and production efficiency of industrial production.
En resumen, chip packaging substrate, as a key electronic component, plays an important role in various fields and promotes the continuous progress of science and technology and the sustainable development of the industry. With the continuous innovation of technology and the continuous expansion of applications, it is believed that chip packaging substrates will play a more important role in the future and create a better living and working environment for mankind.
What are the advantages of Chip Package Substrates?
Chip Package Substrates are an indispensable part of modern electronic equipment. They provide reliable electrical connections and component support for various electronic equipment. Chip packaging substrates offer numerous advantages over traditional wiring methods that make them the preferred solution in the electronics industry.
Primero, the small size of the chip packaging substrate can accommodate more electronic components in a limited space, thereby achieving a compact design and high integration of the device. This provides greater flexibility and freedom in the design of portable devices and miniature electronics that meet modern consumer demands for portability and performance.
Segundo, the chip packaging substrate has high reliability and can operate stably under various environmental conditions. Uso de materiales de alta calidad y procesos de fabricación avanzados, the chip packaging substrate can effectively resist external influences such as vibration, temperature changes, and electromagnetic interference, ensuring that the equipment works stably for a long time.
Además, mass production of chip packaging substrates is convenient, which can reduce production costs and improve production efficiency. Through modern automated production lines and precision processing equipment, large-scale manufacturing of chip packaging substrates can be achieved to meet the rapid expansion of market demand and the urgent requirements of the product cycle.
Además, because the component layout and connection on the chip packaging substrate are completed by computer-aided design software, errors during the assembly process are greatly reduced. This helps improve product quality and production efficiency, reducing production delays and cost increases caused by human errors.
Notably, the use of chip packaging substrates can also improve signal integrity and thermal performance. Through carefully designed wiring and heat dissipation structures, interference and loss during signal transmission can be minimized, and the operating temperature of electronic components can be effectively reduced and their service life extended.
En resumen, chip packaging substrates have many advantages, including small size, high reliability, convenient mass production, reduced assembly errors, improved signal integrity, and improved thermal performance. These advantages make it an important choice in the design and manufacturing of electronic devices. The ideal choice promotes the continuous development and progress of modern electronic technology.
Preguntas más frecuentes
What are the design software for chip packaging substrates?
Commonly used chip packaging substrate design software includes Altium Designer, Cadence Allegro, Mentor Graphics PADS, etc. These software provide a wealth of functions, including layout design, signal integrity analysis, wire tracing, etc., to help engineers achieve an efficient design process.
How to choose a suitable chip packaging substrate material?
When selecting chip packaging substrate materials, factors such as electrical performance, thermal performance, mechanical strength and cost need to be considered. Generalmente, FR4 is the most common choice, but for high-frequency or high-temperature applications, specialty materials such as polyimide may need to be selected.
What are the key links in the manufacturing process of chip packaging substrates?
The key steps in manufacturing chip packaging substrates include substrate preparation, conductive trace formation, component hole drilling and pad coating. Among them, the formation of conductive traces is crucial to ensure the quality and stability of circuit connections.
How to test the reliability of chip packaging substrate?
Reliability testing of chip packaging substrates usually includes electrical performance testing, thermal shock testing, heat and humidity cycle testing, etc. These tests can evaluate the performance of the substrate under different environmental conditions to ensure its good reliability in practical applications.
How to consider the environmental friendliness of chip packaging substrates?
In the design and manufacturing process of chip packaging substrates, environmental factors such as material selection, production technology, and waste disposal need to be considered. Selecting environmentally friendly materials, optimizing production processes, and disposing of waste in compliance with regulations are key measures to achieve environmental protection for chip packaging substrates.