What is Alumina PCB?
Alumina PCB |Al2O3 PCB Manufacturer.An alumina PCB, crafted with precision by expert manufacturers, showcases the exceptional properties of aluminum oxide (Al2O3). Renowned for its high thermal conductivity, electrical insulation, and mechanical strength, alumina PCBs serve as vital components in demanding electronic applications. These meticulously engineered boards, meticulously designed and manufactured, ensure optimal performance and reliability in diverse industries such as aerospace, automotive, and telecommunications. With their unparalleled heat dissipation capabilities and robust construction, alumina PCBs stand as a testament to innovation and excellence in modern electronics manufacturing.
Alumina PCB is a printed circuit board (PCB) made of alumina ceramic substrate. It is widely used in various high-performance electronic equipment, such as communication equipment, aerospace technology, medical equipment and industrial control systems. Compared with traditional FR4 circuit boards, Alumina PCB has higher thermal conductivity, stronger mechanical strength and better insulation performance, so it is particularly suitable for applications with strict thermal management requirements.
The substrate of Alumina PCB is mainly made of alumina ceramic material, which has excellent thermal conductivity and can effectively conduct the heat generated in electronic equipment to a radiator or other heat dissipation device, thereby maintaining a stable operating temperature of the equipment. Además, Alumina PCB also has excellent mechanical strength and can withstand stress under extreme environmental conditions such as high temperature, high pressure and mechanical shock, ensuring long-term stable operation of the equipment.
There are many factors to consider when designing Alumina PCB, including signal integrity, thermal management, component layout, etc. Engineers often use professional CAD software to create precise layout drawings to maximize circuit board performance and functionality. In layout design, engineers need to rationally arrange components that generate more heat to maximize the use of Alumina PCB’s excellent thermal conductivity and ensure the stability of the equipment under different working conditions.
The manufacturing process of Alumina PCB involves multiple steps, including substrate preparation, conductive line deposition, insulation layer preparation, hole drilling, metallization, etc. These steps require advanced equipment and processes to ensure precision manufacturing and high quality of circuit boards. During the manufacturing process, quality control is a vital part, and strict inspection and testing ensure the performance stability and reliability of Alumina PCB.
Overall, Alumina PCB provides important support for the design and manufacturing of electronic equipment through its excellent performance and reliability. As an advanced circuit board material, it performs well in various high-temperature, high-pressure and high-frequency environments, making it one of the first choices in many key application areas.
How to design Alumina PCB?
Designing an Alumina PCB requires considering many factors to ensure optimal performance and functionality. Here are the key factors to consider when designing an Alumina PCB:
Thermal Management: Alumina PCBs are known for their excellent thermal conductivity, so effective thermal management strategies must be prioritized during the design process. Engineers should properly layout heat sources and heat sinks on the circuit board to ensure that heat can be efficiently conducted away from critical components to reduce temperatures and maintain system stability.
Signal Integrity: Signal integrity requires special attention when routing and laying out Alumina PCBs. This involves avoiding signal interference and distortion, usually by optimizing routing paths, reducing signal transmission distances and using appropriate inter-layer connection techniques.
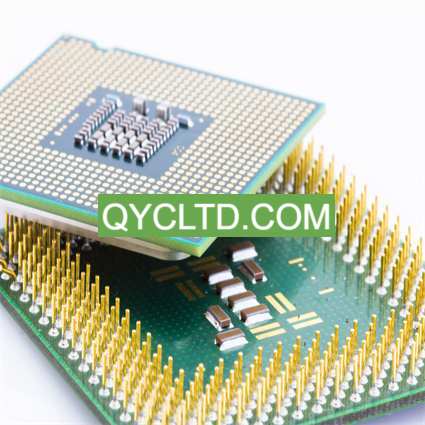
Alumina PCB |Al2O3 PCB Manufacturer
Component layout: The design of Alumina PCB also needs to take into account the layout and arrangement of components. Reasonable component layout can not only save space to the maximum extent, but also optimize signal transmission paths, reduce electromagnetic interference, and simplify the implementation of heat dissipation solutions.
Hierarchical structure: The design of Alumina PCB usually adopts a multi-layer structure to meet the requirements of complex circuits. When designing a multi-layer Alumina PCB, careful planning of signal and power distribution between layers is required to ensure good electrical performance and signal integrity.
Environmental adaptability: Finalmente, Alumina PCB needs to be designed with its use under specific environmental conditions in mind. Engineers must evaluate the durability and stability of the board and solder materials to ensure that Alumina PCBs will perform well in a variety of operating environments and provide long-term reliability.
En resumen, designing Alumina PCB requires comprehensive consideration of key factors such as thermal management, signal integrity, component layout, hierarchy, and environmental adaptability. Through careful design and optimization, Alumina PCB can be ensured to achieve excellent performance and reliability in various application scenarios.
What is the manufacturing process of Alumina PCB?
What is the manufacturing process of Alumina PCB? This question will lead us to deeply explore the mysteries of Alumina PCB. From the preparation of raw materials to the manufacturing of final products, every step is delicate and critical.
Primero, the Alumina PCB manufacturing process begins with the preparation of raw materials. The main material used in Alumina PCB is alumina ceramic substrate, which is highly regarded for its excellent thermal conductivity, high mechanical strength and excellent insulation properties. Manufacturers first cut the required substrate size and shape from high-quality alumina material to ensure it meets design specifications and quality standards.
Next is the preparation of the conductive layer. Using special techniques and equipment, manufacturers coat the aluminum oxide substrate with a layer of conductive material, usually copper or gold. This step is crucial because it determines the conductivity and stability of the circuit. The thickness and uniformity of the conductive layer are critical to the performance of the circuit, so manufacturers employ strict controls to ensure consistent quality from board to board.
This is followed by the processing of the insulation layer. After the conductive layer is covered, the manufacturer applies a layer of insulating material, usually a ceramic or polymer-based film. The function of this layer of insulating material is to ensure electrical isolation between conductive layers and prevent short circuits and circuit interference. Manufacturers use sophisticated techniques to ensure the thickness and uniformity of the insulation layer to ensure circuit reliability and stability.
After the insulating layer is processed, the next step is to make the connection holes for the circuit. Manufacturers use advanced techniques such as laser drilling to create the required connection holes or vias on the board. These contact holes serve as electrical connections between circuit layers, ensuring circuit integrity and functionality. Manufacturers precisely control the location, diameter, and quality of each hole to ensure that the circuit performs as designed.
Finalmente, after strict quality control and inspection, the Alumina PCB manufacturing process is completed. Manufacturers conduct visual inspections, electrical testing and performance evaluations of finished products to ensure each board meets customer requirements and standards. After passing all inspections, Alumina Placas de circuito impreso will be ready to be delivered to customers to provide support and solutions for a variety of high-performance electronic devices and applications.
How are Alumina PCBs made?
The manufacturing process of Alumina PCBs involves a series of precision steps and advanced technologies designed to ensure the highest level of performance and reliability of the final product. The following are the key steps in Alumina PCB manufacturing:
Material preparation: The first step in manufacturing Alumina PCB is to prepare the materials. The main material of Alumina PCB is alumina ceramic substrate, which has excellent thermal conductivity and mechanical strength and is suitable for various high-temperature environments and high-power applications. Además, metal wires (such as copper or gold) and dielectric materials (such as ceramic or polymer films) are needed to build the circuit board’s conductive paths and insulating layers.
Printing the conductive layer: Printing the conductive layer on the aluminum oxide substrate is one of the key steps in manufacturing Alumina PCB. Technologies such as screen printing or chemical vapor deposition (CVD) are usually used to deposit metal wires on the surface of the substrate to form the conductive path of the circuit. These conductive paths will connect electronic components and transmit electrical signals.
Coated dielectric material: To ensure isolation and insulation of circuits, dielectric materials need to be coated between conductive layers. These dielectric layers prevent shorts between wires and provide structural support for the circuit board. Commonly used dielectric materials include ceramic or polymer films, which have good insulating properties.
Drilling and metallization: In order to establish electrical connections between different layers, a process of drilling and metallization is required. Laser drilling technology accurately drills holes in dielectric layers and then coats the holes with metal through metallization to ensure unobstructed electrical signal transmission between different layers.
Processing and Inspection: The final stage of Alumina PCB manufacturing involves the processing and inspection process. En esta etapa, the circuit board is processed into its final form through processing steps such as cutting, drilling, and surface treatment. Subsequently, through strict quality inspection and testing, the dimensional accuracy, electrical performance and reliability of the circuit board are verified to ensure compliance with customer requirements and standards.
The manufacturing process of Alumina PCB requires a high degree of expertise and precision equipment to ensure that every step is completed accurately and reliably. Through strict quality control and continuous technological innovation, Alumina PCB manufacturers are able to provide high-quality, high-performance circuit boards to meet the needs of various complex applications.
How much does Alumina PCB cost?
The cost of Alumina PCBs is affected by a variety of factors, including board size, complexity, quantity, and specific customization requirements. Therefore, a fixed price cannot be provided. However, some of the main factors affecting costs can be explored:
Material cost: Alumina PCB usually uses high-quality ceramic substrates, which are relatively expensive to manufacture. Además, the cost of metallic conductors (such as copper or gold) and dielectric materials (such as ceramics or polymers) can also affect the overall price.
Manufacturing process: Manufacturing Alumina PCB requires complex processes, including preparation of ceramic substrates, deposition of wires, stacking of multi-layer boards, drilling of holes, etc. These processes require sophisticated equipment and technology, thus increasing manufacturing costs.
Customization requirements: If a customer has special customization requirements, such as specific dimensions, thickness, metal thickness, or surface treatment, then the manufacturer may need to perform additional engineering and custom production, which will further increase costs.
Quantity: The quantity ordered also affects the cost of Alumina PCB. Generally speaking, mass production can reduce the unit price, while small batch production will increase the cost of each board.
Overall, Alumina PCBs typically cost a bit more than traditional FR4 PCBs because they use more expensive materials and require more complex manufacturing processes. However, given the superior performance and reliability of Alumina PCBs, this additional investment is often worth it, especially in applications with higher thermal management requirements. To get an accurate price, it’s best to provide detailed design specifications and requirements to the manufacturer so they can provide a customized quote.
What materials are Alumina PCBs made of?
Alumina PCB, as an excellent printed circuit board, its material composition is crucial, directly affecting its performance and reliability. Let’s learn more about the key materials used in Alumina PCB.
En primer lugar, the core material of Alumina PCB is an alumina ceramic substrate, which is known for its excellent thermal conductivity and mechanical strength. Alumina ceramic substrates have excellent thermal conductivity and can effectively transfer the heat generated by the circuit board to the surrounding environment, thereby maintaining the stable operation of electronic equipment. Además, the alumina ceramic substrate also has excellent insulation properties, which can effectively isolate signals in the circuit, reduce signal interference, and improve the performance stability of the equipment.
In addition to the alumina ceramic substrate, Alumina PCB also contains conductive traces. These conductive lines are usually made of metallic materials such as copper or gold to ensure good conductivity and reliable connections. Copper is one of the most commonly used conductive materials. It has good conductivity and processability and can meet the requirements of a variety of circuit board designs. Gold, a precious metal with excellent electrical conductivity and chemical stability, is often used in applications requiring high reliability and corrosion resistance.
Además, a variety of insulating materials are used in the manufacturing process of Alumina PCB to fill the gaps between conductive lines to prevent short circuits and signal interference. These insulation materials usually choose ceramic or polymer-based materials, which have good insulation properties and high temperature resistance, and can effectively protect the conductive lines in the circuit board and ensure its stable operation.
En resumen, Alumina PCB is composed of a variety of materials such as alumina ceramic substrate, conductive lines and insulating materials. These materials work together to ensure the excellent performance and reliability of Alumina PCB, making it the preferred circuit board material for many high-performance electronic devices.
Who makes Alumina PCBs?
In today’s fast-paced electronics industry, the production of Alumina PCBs requires not only a high degree of technical knowledge and expertise, but also supplier reliability and commitment. As a professional Alumina PCB manufacturer, our company is committed to providing customers with the highest quality products and excellent services.
Our manufacturing process combines advanced technology with strict quality control standards to ensure that each Alumina PCB meets customer requirements and expectations. We have a professional engineering team with extensive experience and skills capable of customizing solutions based on our customers’ specific needs.
As a leading manufacturer of Alumina PCBs, our supply chain network covers the world, ensuring timely delivery and competitive pricing. We work with reliable material suppliers to ensure the quality and reliability of the materials used.
In terms of customer service, we are customer-centric and always make meeting customer needs our top priority. Our customer service team is professional and efficient, able to answer customer questions and provide technical support in a timely manner. We strive to establish long-term and stable cooperative relationships and develop together with our customers.
In short, as a manufacturer of Alumina PCB, we insist on putting quality first, focusing on customers, constantly innovating and improving, and providing customers with excellent products and services.
What are the 5 qualities of great customer service?
Excellent customer service is vital to any industry and business. It is not only the process of meeting customer needs, but also the key to building long-term customer relationships and enhancing brand reputation. Here are five qualities of great customer service:
Responsiveness: One of the keys to great customer service is responding promptly to customer needs and questions. This means being able to respond quickly to customers’ emails, phone calls or online messages when they contact you. Whether it’s an inquiry, technical support or complaint, customers want timely feedback. By responding quickly, you not only meet your customers’ expectations, but you also strengthen their trust and loyalty to your business.
Professional Skills: Excellent customer service requires professional skills and knowledge. Customers often have a variety of questions and needs, and a skilled and knowledgeable service team can better meet customer requirements. Through continuous learning and training, ensure your team is always up to date with the latest product information and industry trends to provide customers with professional advice and support.
Reliability: Reliability is the cornerstone of building customer trust. Customers want to be able to rely on your business to provide consistent products and services, whether it’s delivery time or product quality. Prompt delivery of commitments, adhering to contract terms, and quickly resolving issues are all key to building a reliable image. By establishing effective supply chain management and quality control systems, we ensure that products are delivered on time and meet customer expectations.
Flexibility: Customer needs are often changing, so flexibility is key to providing excellent customer service. Being able to adjust product specifications, customize solutions, and provide personalized support based on a customer’s specific needs will make customers feel that your business cares and values them. Establish close working relationships with customers and actively listen to their feedback in order to adjust and improve services in a timely manner.
After-Sales Support: Excellent customer service should not stop at the completion of the sale, but should extend into the post-sales phase. Providing comprehensive after-sales support, including installation guidance, maintenance services and technical support, will make customers feel at ease and trust when using the product. Resolving customer issues in a timely manner and providing them with ongoing attention and support will help build long-term, solid customer relationships.
En resumen, great customer service is an important part of a successful business. Through responsiveness, expertise, reliability, flexibility and comprehensive after-sales support, you can win your customers’ trust and loyalty and build a lasting competitive advantage.
FAQS
Can the thickness of Alumina PCB be customized?
Yes, the thickness of Alumina PCB can be customized according to customers’ specific requirements. Manufacturers often offer a range of thickness options to meet the needs of different applications.
What is the typical lead time for ordering Alumina PCBs?
Alumina PCB lead times vary depending on the manufacturing process and order volume. Generally speaking, the delivery time of regular specifications of Alumina PCB can range from a few weeks to a few months, depending on the manufacturer’s production capacity and order schedule. To ensure timely delivery, it is recommended to consult the manufacturer’s delivery schedule before placing an order.
Is Alumina PCB suitable for high temperature environments?
Yes, Alumina PCB performs well in high temperature environments due to its excellent thermal conductivity and heat dissipation capabilities. This makes them ideal for many high-temperature applications such as automotive electronic systems, aerospace equipment, and industrial control systems.