What is Radio Frequency Cavity PCB?
Radio Frequency Cavity PCB Manufacturer.A Radio Frequency Cavity PCB Manufacturer specializes in crafting intricate circuitry for RF applications. Employing advanced techniques, they engineer printed circuit boards (Leiterplatten) with precisely engineered cavities to contain electromagnetic waves at specific frequencies. These cavities are crucial for shielding sensitive components from interference and optimizing signal transmission. With expertise in RF design and manufacturing, they produce PCBs tailored to diverse industries such as telecommunications, aerospace, und Medizinprodukte. Their commitment to quality and innovation ensures reliable performance in demanding environments where signal integrity is paramount.
RF cavity PCB is a printed circuit board specially designed to handle high-frequency RF signals. Compared with traditional PCB, RF cavity PCB has specific structure and material selection to ensure excellent RF performance and stability. In fields such as radio frequency communications, radar, satellites and wireless networks, radio frequency cavity PCB plays a vital role.
The design and manufacturing process of RF cavity PCB is very precise. Erste, design engineers must consider the characteristics of the RF signal, including factors such as frequency, wavelength, and transmission loss. Sekunde, choosing the right materials is critical to RF performance. High-frequency glass fibers and special dielectric materials are often used in the manufacture of RF cavity PCBs to ensure excellent electrical performance and stability.
The size and shape of the RF cavity PCB can also be customized according to the needs of the specific application. Some applications may require miniaturized RF cavity PCBs, while others may require large boards to accommodate complex circuitry. Regardless of size, RF cavity Leiterplatten must undergo a rigorous manufacturing process to ensure consistent quality and performance.
In practical applications, RF cavity PCB is widely used in various high-frequency electronic equipment. Its excellent radio frequency characteristics make it an ideal choice for wireless communication equipment, radar systems and satellite communication systems. The stability and reliability of RF cavity PCB enable it to work normally under harsh environmental conditions, wie z. B. hohe Temperaturen, high humidity and strong electromagnetic interference.
Kurz gesagt, RF cavity PCB is an indispensable part of modern electronic technology. Through excellent RF performance and stable manufacturing quality, RF cavity PCB provides reliable solutions for various high-frequency applications.
Radio Frequency Cavity PCB design Reference Guide.
RF cavity PCB design is a complex and critical task that requires consideration of many factors to ensure optimal performance and reliability. The following is a brief RF cavity PCB design reference guide designed to help engineers overcome challenges in the design process.
Circuit layout
When designing RF cavity PCB, circuit layout is a crucial part. To ensure smooth transmission of RF signals, components need to be arranged appropriately and signal path length and interference minimized.
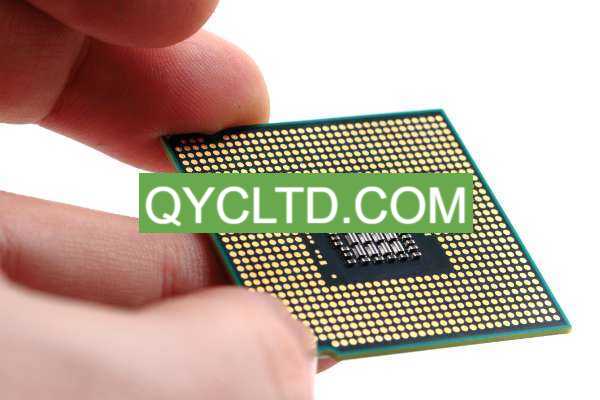
Radio Frequency Cavity PCB Manufacturer
Layer stacking
RF cavity PCBs often adopt multi-layer structures to achieve more complex signal transmission and isolation. Proper layer stacking design can reduce signal crosstalk and loss, improving overall performance.
Impedance matching
In RF circuits, impedance matching is key to ensuring maximum signal transmission. By accurately matching the impedance of the signal line and the transmission medium, reflections and losses can be reduced and signal quality improved.
Ground wire design
The ground wire is an important part of the radio frequency circuit, and its design affects the stability and noise performance of the entire system. Correctly designing the ground wire layout and connection method can reduce the impedance of the ground loop and reduce signal crosstalk and interference.
Material selection
Choosing the right materials is critical to the performance of RF cavity PCBs. High-frequency glass fiber, low dielectric constant substrate materials and high-quality copper foil can improve signal transmission efficiency and stability.
Package design
Package design directly affects the performance and reliability of RF components. Proper packaging can provide good mechanical support and thermal management while protecting the component from the outside environment.
Simulation and verification
After completing the design, simulation and verification are essential steps. By simulating the transmission and response of RF signals through simulation software, potential problems can be discovered early and adjusted.
Iterative optimization
RF cavity PCB design is a process of continuous iterative optimization. Through continuous trials and adjustments, the performance and stability of the design are gradually improved.
Kurz gesagt, RF cavity PCB design requires comprehensive consideration of circuit layout, layer stacking, impedance matching, ground wire design, material selection, packaging design, simulation verification, and iterative optimization. Only by fully considering and optimizing these aspects can we design an RF cavity PCB with excellent performance, stability and reliability.
What material is used in Radio Frequency Cavity PCB?
Material selection for RF cavity PCB is critical to its performance. During the design and manufacturing process, choosing the right materials can ensure that the PCB performs well in high-frequency environments and maintains stable working performance. The following are the key materials commonly used in RF cavity PCB:
High frequency fiberglass
High-frequency glass fiber is one of the commonly used substrate materials in radio frequency cavity PCB. It has excellent dielectric properties and stability, can effectively transmit radio frequency signals, and has low loss. The use of high-frequency glass fiber can reduce signal transmission loss and improve PCB performance.
Copper foil
Copper foil is widely used as a conductor layer in RF cavity PCBs. Because copper has excellent electrical conductivity and good processability, it is an ideal choice for transmitting RF signals. By controlling the thickness and layout of copper foil, precise matching of signal impedance can be achieved, improving PCB performance and stability.
Special dielectric materials
RF cavity PCBs often require special dielectric materials to fill the cavity and serve as interlayer dielectric. These special dielectric materials have low loss, high dielectric constant and good high temperature resistance, which can effectively reduce signal transmission loss and crosstalk. Common special dielectric materials include PTFE (polytetrafluoroethylene), RO4000 series, etc., which perform well in radio frequency applications.
Insgesamt, material selection for RF cavity PCB should take into account its electrical performance, stability, and cost-effectiveness. By rationally selecting and combining the above materials, RF cavity PCBs with excellent performance, stability and reliability can be designed and manufactured to meet the requirements of various high-frequency electronic equipment.
What size are Radio Frequency Cavity PCB?
The dimensions of RF cavity PCBs are customized according to specific application requirements, which makes them widely used in various RF electronic devices. From micro packages to large boards, RF cavity PCBs can be customized in various sizes and shapes to meet the requirements of different devices.
For miniature RF cavity PCBs, the size can be very small and suitable for devices that require compact designs, such as mobile phones, smart watches, and wireless headsets. These micro PCBs typically feature high-density circuit layouts and multi-layer structures to minimize space requirements while maintaining excellent RF performance.
On the other hand, for large RF cavity PCBs, their size may be relatively large and suitable for equipment that needs to process more complex RF signals, such as communication base stations, radar systems, and satellite communication equipment. These large PCBs may have multiple RF cavities and high-power RF components, requiring larger space to accommodate and ensure good thermal performance.
In addition to size, the shape of the RF cavity PCB can also be customized according to specific application needs. Some devices may require specially shaped PCBs to fit specific mechanical structures or space constraints. Deshalb, manufacturers are usually able to provide customized RF cavity PCB solutions according to customer requirements, ensuring that they can be perfectly adapted to various application scenarios.
In summary, the flexible customization of the size and shape of RF cavity PCB makes it an indispensable component in various RF electronic devices. By customizing according to specific needs, RF cavity PCB can provide the best performance and reliability, promoting the application and development of RF technology in various fields.
The Manufacturer Process of Radio Frequency Cavity PCB.
The manufacturing process of RF cavity PCB is a precise and complex project involving multiple key steps, each of which has an important impact on the quality and performance of the final product.
The first is the design phase. Zu diesem Zeitpunkt, engineers use CAD software to design based on the customer’s needs and technical specifications. The design of RF cavity PCB needs to consider the high-frequency characteristics and electromagnetic compatibility of signal transmission, so precise layout and layer stacking design are required to ensure signal stability and reliability.
Next comes prototyping. Based on the design drawings, the manufacturer will produce prototypes for testing and verification. This step usually uses rapid prototyping technology, such as rapid prototyping (RP) or CNC machining, to speed up the manufacturing cycle and reduce costs.
This is followed by chemical corrosion. Using chemical etching technology, manufacturers etch away the excess copper foil covering the surface of the substrate, leaving the desired circuit pattern. Precise control of this step ensures the accuracy and reliability of the circuit.
Then comes drilling. Zu diesem Zeitpunkt, manufacturers use a laser or mechanical drill to drill holes in the PCB according to design requirements in order to install electronic components and connect circuits between various layers.
Finally comes assembly. In diesem Schritt, manufacturers mount various electronic components (such as integrated circuits, capacitors, Widerstände, etc.) onto the PCB, solder and test them. The precision and quality control of assembly directly affects the performance and reliability of the final product.
Insgesamt, the manufacturing process of RF cavity PCB requires a high degree of professional knowledge and technology to ensure that the quality and performance of the product meet customer requirements. Through precise manufacturing processes, manufacturers are able to provide high-quality RF cavity PCBs to meet the needs of different application fields and promote the development and innovation of electronic technology.
The Application area of Radio Frequency Cavity PCB.
RF cavity PCB is a high-performance circuit board specially designed to handle RF signals and plays a key role in various fields. The following will introduce its applications in the fields of communications, radar, satellites and wireless networks.
Communication
In the field of communication, RF cavity PCB is widely used in wireless base stations, communication network equipment and various mobile communication equipment. Its excellent radio frequency characteristics and stability enable it to handle high-frequency signals and maintain stable performance while maintaining communication quality.
Radar
Radar systems need to process large amounts of radio frequency signals to detect targets and obtain their position and velocity information. The high-frequency performance and reliability of RF cavity PCBs make them an indispensable component in radar systems. From civil aviation radar to military defense systems, RF cavity PCBs play a key role.
Satellite
Satellite communications systems rely on high-performance radio frequency electronics to transmit data and information. RF cavity PCB plays a vital role in satellite communication systems. Its stable performance and high-frequency characteristics ensure reliable transmission and reception of satellite signals.
Wireless Network
In the field of wireless networks, RF cavity PCBs are used to manufacture various wireless routers, base stations and network equipment. Its excellent radio frequency characteristics enable it to provide stable performance in wireless signal transmission while maintaining high-speed data transmission and stable connections.
Im allgemeinen, the wide application of RF cavity PCB in fields such as communications, radar, satellites and wireless networks demonstrates its irreplaceability in high-frequency electronic equipment. Its stability, reliability and high-frequency characteristics make it the first choice for various high-frequency electronic equipment, providing a solid foundation for the development of modern technology.
What are the advantages of Radio Frequency Cavity PCB?
RF cavity PCB is a key component that plays an important role in the manufacturing of modern electronic equipment. Compared with traditional wiring methods, RF cavity PCB has many advantages, making it widely used in fields such as communications, radar, satellites and wireless networks.
Erste, the size of the RF cavity PCB is smaller. Due to the highly sophisticated technology used in its design and manufacturing, a more compact layout can be achieved, thereby saving space and making the equipment more lightweight and compact, suitable for various application scenarios with strict size requirements.
Zweitens, RF cavity PCB has stable performance. During high-frequency signal transmission, the stability of the circuit board is crucial. RF cavity PCB uses specialized materials and processes to effectively control signal transmission and interference, ensure signal quality and stability, and improve system performance.
Ease of mass production is another major advantage of RF cavity PCBs. The modern electronics market poses challenges to the rapid delivery and mass production of products, and the manufacturing process of RF cavity PCB has been optimized to achieve efficient and automated production to meet market demand.
Endlich, RF cavity PCBs offer design flexibility. Designers can customize the design according to specific application requirements, including optimization of layer stacking, wiring methods, impedance matching, etc., to achieve better performance and reliability.
In summary, RF cavity PCB has many advantages over traditional wiring methods, including small size, stable performance, easy mass production, and flexible design. These advantages make it an indispensable and important part of modern electronic equipment manufacturing, promoting the continuous progress and development of electronic technology.
Häufig gestellte Fragen
What is the cost of RF cavity PCB?
RF cavity PCBs typically cost slightly more than regular PCBs because their manufacturing process requires greater precision and expertise. Aber, with the development of technology and intensified market competition, the cost of RF cavity PCB has gradually become more reasonable, and more cost advantages can be obtained in mass production.
In which industries are RF cavity PCBs widely used?
RF cavity PCB is widely used in communications, satellites, radar, wireless networks, medical equipment and military fields. Its advantages in high-frequency signal transmission and anti-interference make it an indispensable key component in these fields.
How to troubleshoot RF cavity PCBs?
Troubleshooting of RF cavity PCB requires a combination of professional testing instruments and techniques. Common faults include impedance mismatch, signal attenuation and circuit short circuit, etc., which require instrument testing and circuit analysis to determine and solve the problem.
How environmentally friendly is RF cavity PCB?
The materials of RF cavity PCB are usually recyclable and environmentally friendly. Materials such as PTFE will not produce environmentally harmful substances during production and use. Gleichzeitig, reasonable manufacturing and recycling processes can also reduce its impact on the environment.