Military Circuit Board Manufacturer, A leading manufacturer specializing in military-grade circuit boards, our expertise lies in crafting high-performance electronic components engineered to withstand rigorous environments. With cutting-edge technology and stringent quality control measures, we ensure precision and reliability in every board produced. Our commitment to excellence extends to meeting stringent military standards, guaranteeing optimal performance in critical defense systems. From conception to production, our skilled team meticulously crafts circuit boards tailored to meet the demanding requirements of modern military applications. Trust us for dependable solutions that safeguard national security with uncompromising efficiency.
In today’s modern warfare and defense systems, the role of military circuit boards cannot be underestimated. These complex electronic components are the basis of advanced weapons, communications systems and surveillance equipment and are used by armed forces around the world. In this comprehensive guide, we’ll delve into the complexities of military circuit board manufacturing, revealing the processes, Materialien, and key considerations that shape this critical aspect of military technology.
What is a military circuit board?
Military circuit boards are electronic components specially designed and manufactured for military applications, which play a vital role in modern warfare and defense systems. In today’s highly digitalized and informationized battlefield environment, military circuit boards carry key functions such as connection, control and communication, providing support for various advanced weapon systems, communication equipment and surveillance devices.
One of the key features of military circuit boards is that their design and manufacturing processes are subject to extremely high standards and stringent requirements. Due to the particularity of military applications, military circuit boards must have excellent durability, reliability and anti-interference capabilities. This means that they need to be able to operate stably in harsh environmental conditions, wie z. B. hohe Temperaturen, low temperature, high humidity, vibration and shock, etc., and they also need to have properties such as resistance to electromagnetic interference and resistance to nuclear radiation.
In advanced weapons systems, military circuit boards play a key role. Zum Beispiel, in missile systems, military circuit boards are responsible for controlling the flight path of the missile, the detonation device, and the processing and transmission of sensor data. In radar systems, military circuit boards are used to process radar signals, target tracking and data processing. Außerdem, military circuit boards are also widely used in communication systems, reconnaissance equipment, drones, military vehicles, satellite systems and other fields.
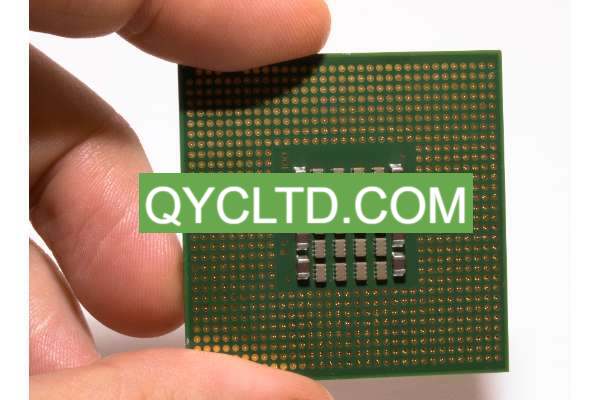
Military circuit board Manufacturer
Due to their criticality and particularity, the design and manufacturing of military circuit boards must undergo rigorous review and testing. Military standards and specifications impose strict requirements on performance, reliability and environmental adaptability. Deshalb, military circuit board manufacturers must have advanced technology and equipment and strictly follow relevant quality management systems and standards to ensure product compliance and reliability.
Im allgemeinen, military circuit boards play an irreplaceable role in modern warfare and national defense systems, and their high reliability and superior performance provide a solid foundation for military applications. Through continuous technological innovation and quality improvement, military circuit boards will continue to play an important role and contribute to the national defense industry.
What is the design of military circuit boards?
The design of military circuit boards is a complex and precise process that requires strictly following a series of steps and using specific techniques to ensure reliability and performance in military applications. Here’s a closer look at the process of designing a military circuit board and how to ensure it meets stringent military requirements.
Erste, the process of designing a military circuit board usually begins with a clear requirements analysis. The design team must work with the military to understand the board’s functional, performance and environmental requirements for the specific application. This may involve working closely with military engineers to ensure that the boards can operate reliably under extreme conditions.
Nächster, the design team will design the circuit schematic diagram. Zu diesem Zeitpunkt, engineers use professional design software to graphically present circuit functions and connection relationships. This requires an understanding of circuit principles and signal transmission to ensure that the board functions and performs as expected.
This is followed by the layout design phase. During this stage, engineers place the components on the circuit board and design how the wiring will be connected. This requires consideration of factors such as signal transmission paths, Energieverteilung, Thermomanagement, and electromagnetic compatibility. By optimizing the layout design, signal interference and electromagnetic interference can be minimized and the performance and reliability of the circuit board can be improved.
Once the layout design is completed, it enters the wiring design stage. Zu diesem Zeitpunkt, engineers will draw the actual line connection diagram based on the layout design, and determine the paths and specifications of each signal line. This needs to take into account factors such as signal transmission speed, impedance matching, electromagnetic compatibility, and the stacking sequence between board layers.
Engineers also need to pay close attention to the requirements of military standards and specifications at all stages of the design process. This may involve specific material selection, production processes, reliability testing, and environmental suitability. Zum Beispiel, military circuit boards often need to pass rigorous temperature, humidity and vibration testing to ensure their reliability under extreme conditions.
Endlich, the design team will perform simulation and verification testing to ensure the board meets the stringent requirements of military applications. This may involve simulation of circuit performance, production of prototypes, and functional and reliability testing. Only through comprehensive testing and verification can the design team ensure that the board will operate reliably in real-world applications and meet the requirements of the military sector.
Zusammenfassend, designing a military circuit board is a complex and critical process that requires strictly following a series of steps and using specific techniques. By working closely with the military and strictly adhering to military standards and specifications, the design team ensures the board’s reliability, performance and adaptability in military applications.
What is the manufacturing process of military circuit boards?
The manufacturing process of military circuit boards is a precise and complex process involving multiple critical steps and special technologies to ensure the reliability and performance of the final product. The following is an overview of a typical military circuit board manufacturing process:
The first step in the manufacturing process is selecting high-quality raw materials suitable for military applications. This includes substrate materials, conductive layers, insulating materials, covering layers, etc. The substrate material is usually a material with strong high temperature resistance, such as FR-4 fiberglass composite or higher grade materials, to ensure the reliability of the circuit board in harsh environments.
After deciding on the raw materials, the manufacturer will proceed with PLATINE design, which involves converting the circuit design diagram into an actual circuit board layout. The design process includes selecting the appropriate number of board layers, layout components, routing paths, and noise control techniques.
Before converting the design into an actual circuit board, the raw materials need to undergo some pre-processing steps such as cleaning, removing oxides, applying chemical treatments, etc. These steps ensure the surface quality and adhesion of the final circuit board.
After the pretreatment is completed, the surface of the PCB board is coated with a layer of photosensitive material, and then the circuit pattern is transferred to the board through a process of exposure and chemical etching. This step requires high-precision equipment and strict operations to ensure the accuracy and clarity of the circuit pattern.
After patterning, the PCB board undergoes a chemical etching process to remove the portions not protected by the photosensitive material. This step is usually performed using an acidic or alkaline solution and requires strict control of time and temperature to ensure accurate corrosion depth and uniformity.
After chemical etching, the exposed copper layer on the PCB board is metallized, usually using electroplating techniques such as electroplating copper or other metals. This step increases the electrical conductivity of the circuit board and prepares it for the subsequent assembly process.
After metallization, the holes on the PCB board will be drilled to facilitate the installation and connection of components. Rivets are also installed where needed to enhance the structural strength and stability of the circuit board.
Once the basic structure of the circuit board is established, printing and assembling components can begin. This includes soldering the electronic components to the board and ensuring correct placement and connections.
The final step in the manufacturing process is a comprehensive final inspection of the finished product. This includes visual inspection, electrical testing, inspection of soldered connections and, if necessary, functional testing. Only after passing strict inspection can the circuit board leave the factory and be put into practical use.
Through these critical steps, military circuit board manufacturers are able to produce high-quality, reliable circuit boards that meet the stringent requirements of military applications.
How are military circuit boards made?
The manufacturing of military circuit boards is a complex and critical process that requires the use of advanced equipment and technology to ensure product high quality, reliability and performance. Military circuit board manufacturers are usually equipped with a series of advanced equipment, including automated production lines, precision processing equipment, and high-precision testing instruments. Among them, automated production lines can achieve high-efficiency production, greatly improving manufacturing speed and consistency.
During the production process, manufacturers use a series of advanced technologies to ensure product quality and performance. Zum Beispiel, surface mount technology (SMT) and soldering technology enable high-density component layout and reliable soldering connections, thereby improving circuit board integration and reliability. Außerdem, precision printing and chemical etching technology can achieve fine lines and apertures to ensure the signal transmission performance and stability of the circuit board.
To ensure product reliability and performance, military circuit board manufacturers adopt strict quality control measures. They monitor and manage every production link through a comprehensive quality management system and strict process control. Außerdem, manufacturers also conduct rigorous performance testing and reliability verification to ensure that the circuit board can operate stably for a long time in extreme environments.
In addition to technology and equipment in the production process, manufacturers also focus on personnel training and technology research and development. They continuously improve the technical level and professional knowledge of their employees and introduce new production technologies and processes to adapt to changing market demands and technological development trends.
Zusammenfassend, military circuit board manufacturers ensure that products can meet the strict requirements of military applications and provide reliable electronic solutions for national defense security by using advanced equipment and technology, strict quality control measures, and continuous technological innovation.
How much do military circuit boards cost?
The cost of military circuit boards is influenced by a variety of factors that determine the complexity of their manufacturing and design as well as the quality and performance of the product. Here are a few key factors that impact military circuit board costs:
Erste, the cost of military circuit boards is affected by their complexity and technical requirements. Because military circuit boards need to meet strict military specifications and performance requirements, the design and manufacturing process may require the involvement of more engineers and specialized technicians. This increases design and manufacturing costs.
Zweitens, the choice of materials also has an important impact on the cost of military circuit boards. Military circuit boards often require the use of high-performance materials, such as high-temperature-resistant substrates, special conductive layers, and covering layers to ensure their reliability and durability in extreme environments. These specialty materials are typically more expensive than those used in commercial circuit boards.
Außerdem, technical requirements during the manufacturing process will also affect costs. Zum Beispiel, military circuit board manufacturing may require more stringent quality control and inspection processes to ensure products meet military standards. This may require the investment of more human resources and equipment, thereby increasing costs.
Military circuit boards typically cost more than commercial circuit boards. This is because military circuit boards need to meet higher performance and reliability requirements, have more complex design and manufacturing processes, and require the use of more expensive materials and technologies. Außerdem, the production scale of military circuit boards is usually smaller, which also leads to an increase in unit costs.
Zusammenfassend, the cost of military circuit boards is affected by many factors, including complexity, technical requirements, material selection and production scale. Although the cost of military circuit boards is higher compared to commercial circuit boards, this is to ensure their reliability and performance in military applications, thereby ensuring national defense security.
What materials are used in military circuit boards?
As an integral part of military applications, military circuit boards must have high durability and reliability. In order to ensure that its performance can operate stably for a long time in harsh environments, military circuit boards use a series of special materials. Here are some common military circuit board materials and their characteristics:
High-Temperature Substrates: Military circuit boards often use high-temperature substrates, such as polyimide (Polyimide) or polytetrafluoroethylene (PTFE). These materials have excellent high temperature resistance and are able to maintain circuit board stability under extreme temperature conditions.
Metal Coatings: In order to enhance conductivity and corrosion resistance, military circuit boards usually use metal coatings, such as gold or silver plating. These metal layers not only improve the conduction efficiency of the circuit, but also prevent oxidation and corrosion, thereby extending the life of the circuit board.
Specialized Coatings: Military circuit boards often need to be used in harsh environments, so special coatings are often used to enhance their durability and protection. Zum Beispiel, coating materials such as epoxy resin or polyurethane can effectively prevent moisture, chemicals and mechanical damage from affecting circuit boards.
Shock-Resistant Materials: Military circuit boards often need to work in combat and extreme conditions, so they must have good impact resistance. For this reason, circuit boards often use materials with high strength and impact resistance, such as glass fiber reinforced resin (Glass-Reinforced Resin) or polyether ether ketone (Polyether Ether Ketone, referred to as PEEK).
Flame-Retardant Materials: Considering that military circuit boards may be exposed to dangerous situations such as fire or explosion, their materials must have good flame-retardant properties to reduce the risk of fire spread. Deshalb, flame retardants, such as bromide or phosphorus compounds, are added to commonly used circuit board materials to improve their flame retardancy.
Zusammenfassend, the material selection of military circuit boards is crucial and directly affects its performance, durability and reliability. By using special high-temperature substrates, metal coverings, special coatings, impact-resistant materials, and flame-retardant materials, military circuit boards can operate stably in harsh environments and ensure the smooth progress of military applications.
Who can make military circuit boards?
Who can make military circuit boards? In the field of military technology, it is crucial to manufacture high-quality, reliable military circuit boards. And manufacturers who are up to the task are crucial. In this regard, Suppliers is an important department we have within our company, dedicated exclusively to providing quality military circuit boards to the defense sector.
Our company has an experienced engineering team that is proficient in the design, manufacturing and testing of military circuit boards. They are familiar with various military specifications and standards and can ensure that the circuit boards they produce meet the most stringent requirements. Our company actively adopts the most advanced technology and processes and invests in advanced equipment and facilities to ensure product quality and production efficiency.
As a reliable military circuit board manufacturer, we have established close cooperative relationships with the defense sector and military industrial enterprises. Our clients include all levels of government agencies, defense contractors, and other key stakeholders in key sectors. Our products are widely used in key areas such as radar systems, missile control, Kommunikationsgeräte, drones and satellite systems.
In addition to high-quality products, our company is known for its excellent customer service and technical support. Our team is always ready to provide customers with professional consultation and support, ensuring that their needs are met promptly and receive the best solution.
In the fiercely competitive military electronics market, our company has always adhered to the principle of quality first and is committed to providing customers with excellent products and services. Through continuous innovation and improvement, we firmly believe that we will continue to be a leader in the field of military circuit board manufacturing and make greater contributions to the national defense industry.
What are 5 qualities of a good customer service?
Professionalism: Good customer service starts with professionalism. Professional customer service represents an accurate understanding of customer needs and solving problems with a professional attitude and skills. The professional customer service team has rich product knowledge and problem-solving abilities, and can provide timely and effective support and suggestions, providing customers with confidence and peace of mind.
Timely response: Timely response is the basis for building a good customer relationship. A good customer service team can promptly respond to customer inquiries, complaints or suggestions and solve the problem in the shortest possible time. Timely feedback and responses make customers feel valued and respected, enhancing customers’ trust and loyalty to the company.
Personalized care: Personalized care is key to customer satisfaction and loyalty. A good customer service team not only meets the basic needs of customers, but also provides customized solutions and services based on customers’ specific needs and preferences. By developing a deep understanding of customer needs and expectations, customer service teams are able to develop strong connections with customers and achieve higher levels of customer satisfaction.
Problem-solving skills: A good customer service team has excellent problem-solving skills. They are able to quickly identify and understand the problems faced by their customers and take effective measures to solve them. An excellent customer service team not only solves superficial problems, but can also analyze the root cause of the problem in depth and provide lasting solutions to avoid recurrence of the problem and ensure customer satisfaction and trust.
Continuous Improvement: Continuous improvement is a key driver of good customer service. Excellent customer service teams constantly reflect on and summarize experiences and lessons learned at work, actively seek opportunities for improvement and innovation, and continuously improve service quality and customer experience. Durch kontinuierliche Verbesserung, customer service teams can adapt to changing market and customer needs, maintain a competitive advantage, and continuously improve customer satisfaction and loyalty.
In einem hart umkämpften Marktumfeld, good customer service is not only a service, but also a key factor for enterprises to win the trust and support of customers. Through professional, timely and personalized service, problem-solving capabilities and a spirit of continuous improvement, companies can establish close ties with customers and achieve sustainable development and success.
FAQS
What certifications should a military circuit board manufacturer have?
Military circuit board manufacturers should typically have ISO 9001 quality management system certification, AS9100 aerospace quality management system certification, and ITAR (International Traffic in Arms Regulations) compliance certification. These certifications demonstrate that manufacturers have production capabilities that meet international standards and are able to meet the needs and requirements of military customers.
What is the lifespan of military circuit boards?
The lifespan of military circuit boards depends on several factors, including material quality, Fertigungsprozesse, environmental conditions, and usage patterns. Im allgemeinen, well-designed and manufactured military circuit boards can have a service life of up to decades, but in actual applications they may require regular maintenance and updates.
How complex is the process of manufacturing military circuit boards?
The process of manufacturing military circuit boards is very complex and involves multiple links and process steps. From the procurement and handling of raw materials, to board stacking, printing, chemical etching, Bohrung, metallization and final inspection, each step requires precision operations and strict quality control to ensure the quality and performance of the final product meets military standards. standard.