What is Ceramics Substrate?
Ceramics Substrate Manufacturer. A leading ceramics substrate manufacturer, renowned for its precision engineering and cutting-edge technology. With a relentless commitment to quality, they specialize in crafting substrates tailored for diverse industries like electronics, aerospace, and automotive. Their state-of-the-art facilities ensure unparalleled durability and thermal stability, meeting the stringent demands of modern applications. From intricate circuitry to robust structural components, their expertise spans the spectrum, empowering clients with reliable solutions that push the boundaries of innovation. With a legacy of excellence and a forward-looking approach, they remain the cornerstone of ceramic substrate manufacturing, driving progress and reliability worldwide.
Ceramics Substrate, also known as Ceramics Substrate, is a substrate material used in electronic components that has excellent thermal conductivity and insulation properties. It plays a key role in modern electronic devices, providing a stable support platform for circuit components and effectively managing heat to ensure device performance and reliability.
Material properties
Ceramic substrates are usually made of high-performance ceramic materials, such as alumina (Alumina) or aluminum nitride (Aluminum Nitride). These materials have good thermal conductivity and insulation properties and can effectively conduct and disperse heat to prevent electronic components from being damaged due to overheating. In addition, the ceramic substrate also has excellent high temperature resistance and chemical stability, and can operate stably for a long time in harsh environments.
Application areas
Ceramic substrates are widely used in various electronic equipment and systems, including power modules, radio frequency devices, LED lighting, sensors and other fields. In power modules, ceramic substrates can effectively disperse the heat generated by power devices and improve system efficiency and stability; in radio frequency devices, ceramic substrates can provide good high-frequency characteristics and signal transmission performance; in the field of LED lighting, ceramics The substrate can withstand high temperature and high humidity environments, ensuring the long-term stable operation of LED lamps; in sensor applications, the ceramic substrate can provide stable mechanical support and environmental protection to ensure the accuracy and reliability of the sensor.
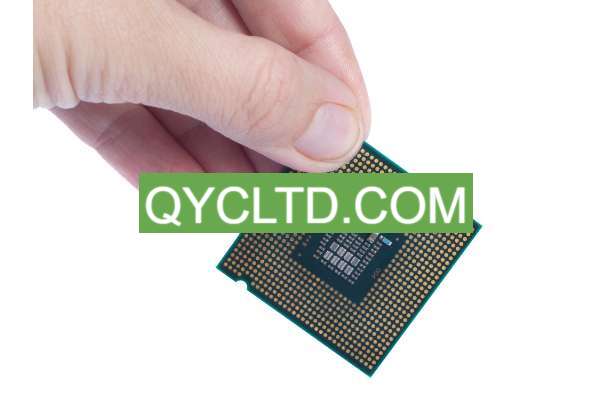
Ceramics Substrate Manufacturer
Manufacturing process
The manufacturing process of ceramic substrates includes material selection, molding, sintering, processing and testing. During the manufacturing process, various parameters need to be strictly controlled to ensure the dimensional accuracy, surface flatness and performance stability of the substrate. Advanced manufacturing technology and equipment can achieve high-precision and high-efficiency production to meet the needs of different application fields.
As an important part of electronic components, ceramic substrates have excellent thermal conductivity, insulation and high temperature resistance, and play an irreplaceable role in modern electronic equipment. Through continuous innovation and optimization, ceramic substrates will continue to provide solid support and guarantee for the development of electronic technology.
Ceramics Substrate design Reference Guide.
Designing ceramic substrates is a comprehensive task that requires consideration of multiple factors to ensure the performance and reliability of the final product. Here are some key steps and best practices for designers to consider:
Circuit layout
When designing the circuit layout, factors such as signal transmission paths, power distribution, and ground wire planning need to be considered. Reasonable layout can reduce signal interference, improve anti-interference ability, and ensure the stability and reliability of the circuit.
Thermal management
Since ceramic substrates have good thermal conductivity properties, thermal management is critical during the design process. Designers should consider how to effectively dissipate heat to avoid overheating damage to electronic components. The use of appropriate heat dissipation structures, heat dissipation materials and heat dissipation paths is the key to ensuring effective thermal management.
Material selection
Selecting the appropriate ceramic material is critical to substrate performance. Commonly used ceramic materials include alumina, aluminum nitride, etc., which have different thermal conductivities, dielectric constants and mechanical properties. Choosing the most appropriate material based on specific application requirements can maximize substrate performance and reliability.
Interface design
Ceramic substrates usually need to be connected to other components, so interface design is also an important part of the design process. Reasonable interface design can ensure stable and reliable signal transmission, reduce contact resistance and crosstalk, and improve the overall performance of the system.
Simulation and verification
After the design is completed, simulation and verification are essential steps. Use simulation software to simulate circuit operation and verify whether the design meets expected performance indicators. At the same time, actual testing and verification are carried out to ensure the reliability and stability of the design.
Continuous optimization
Design work is not completed once and for all, continuous optimization is an important part of the design process. By continuously collecting feedback information, improving and optimizing, the performance of ceramic substrates is continuously improved to adapt to changing needs and challenges.
To sum up, designing ceramic substrates requires comprehensive consideration of multiple factors such as circuit layout, thermal management, material selection, etc., and following a series of key steps and best practices. Only in this way can high-quality ceramic substrates with stable performance and high reliability be designed to provide reliable support for the development of electronic products.
What material is used in Ceramics Substrate?
Ceramic substrates are an integral part of modern electronic devices, and their material selection is crucial. Typically, ceramic substrates are made of high-performance ceramic materials such as aluminum oxide and aluminum nitride. These materials have excellent physical and chemical properties that allow ceramic substrates to perform well in a variety of harsh working environments.
First, alumina is a common ceramic substrate material with excellent high temperature resistance. It can maintain stable physical and electrical properties under extreme temperature conditions and is suitable for the manufacturing of high-temperature electronic equipment. In addition, alumina also has good insulation properties, which can effectively prevent the leakage of current and ensure the stable operation of the circuit. Its corrosion resistance also allows it to maintain excellent performance under harsh environments for long periods of time.
Another common ceramic substrate material is aluminum nitride. Compared with aluminum oxide, aluminum nitride has higher thermal conductivity and mechanical strength, and is suitable for electronic equipment that requires higher heat dissipation performance. The thermal conductivity of aluminum nitride is many times higher than that of aluminum oxide, and it can conduct heat to the external environment more effectively and maintain the normal operating temperature of the equipment. This has led to widespread use of aluminum nitride in high-power electronics and radio frequency applications.
In general, alumina and aluminum nitride are two common ceramic substrate materials. They both have excellent high temperature resistance, corrosion resistance and insulation properties, and are suitable for various harsh working environments. When selecting ceramic substrate materials, comprehensive considerations need to be made based on specific application needs and performance requirements to ensure the stability and reliability of electronic devices.
What size are Ceramics Substrate?
As a key support for electronic components, ceramic substrates’ size diversity is closely related to their flexibility in various application scenarios. Ceramic substrate dimensions can vary depending on specific application needs. From microelectronics to large industrial equipment, ceramic substrates of varying sizes and shapes are possible.
In microelectronic devices, such as smartphones, tablets, and wearable devices, small and highly integrated ceramic substrates are often required. These substrates are usually small in size, able to accommodate multiple electronic components in a limited space, and provide stable support and good heat dissipation. In the industrial field, such as power electronics, automotive electronics and aerospace, large industrial equipment usually requires larger-sized ceramic substrates to meet the layout requirements of complex circuits and high-power electronic components.
The shape of the ceramic substrate also varies depending on the application. In some scenarios, specially shaped substrates are required to accommodate specific installation space or circuit layout requirements. For example, some electronic modules may require round or shaped ceramic substrates to work with other components or to accommodate special physical structures.
In addition to size and shape, the thickness of the ceramic substrate is another important consideration. In some high-density integrated circuit applications, extremely thin ceramic substrates are required to reduce the overall size and improve circuit performance and heat dissipation. In some high-power electronic devices, thicker ceramic substrates may be needed to withstand greater current and heat.
In summary, the size of ceramic substrates varies depending on specific applications, ranging from micro to large, and from standard to special shapes, to meet the needs of various electronic devices. This flexibility makes ceramic substrates an integral part of modern electronics.
The Manufacturer Process of Ceramics Substrate.
The manufacturing process of ceramic substrates is a complex and precise process involving multiple links, requiring strict control and a high degree of expertise from material preparation to final testing. The following is a detailed analysis of each aspect of the ceramic substrate manufacturing process:
Material preparation
The first step in manufacturing ceramic substrates is to select a suitable high-performance ceramic material, usually aluminum oxide or aluminum nitride. These materials have excellent thermal conductivity, insulation and high temperature resistance, and can meet the needs of various harsh working environments. During the material preparation stage, the purity and uniformity of the material need to be ensured to ensure the quality of the final product.
Forming
Shaping is a critical step in shaping the raw ceramic material into the desired shape and size. Common molding methods include injection molding and tablet molding. During the molding process, parameters such as temperature, pressure and time need to be precisely controlled to ensure the accuracy and consistency of the molded parts.
Sintering
The formed ceramic substrate needs to be sintering to achieve densification and increased strength of the material. During the sintering process, the ceramic substrate is heated in a high-temperature environment for a long time to combine the material particles into a hard whole. Control of sintering temperature and time is critical to substrate performance and quality.
Processing
The sintered ceramic substrate needs to be machined and trimmed to achieve the required size and surface quality requirements. This includes cutting, drilling, edging and other process steps. The processing process requires high-precision equipment and technology to ensure the dimensional accuracy and surface flatness of the substrate.
Test
The last critical link is strict testing and quality control of the ceramic substrates. This includes testing and evaluation of dimensions, surface quality, insulation properties, thermal conductivity and more. Only substrates that pass various tests can be recognized as qualified products and enter the next stage of assembly and application.
Through precise manufacturing processes, ceramic substrates can ensure stable and reliable performance in various application scenarios. Every aspect of the manufacturing process requires strict control and highly professional technology to ensure the quality and performance stability of the final product.
The Application area of Ceramics Substrate.
The wide application of ceramic substrates in the electronics industry is not limited to specific fields, but spans multiple fields, providing reliable basic support for various key applications. The following is an overview of the applications of ceramic substrates in various fields:
Power module
In the field of power electronics, ceramic substrates are widely used in various power modules, such as inverters, frequency converters, power modules, etc. The high thermal conductivity and excellent insulation properties of ceramic substrates enable it to effectively manage the heat of power devices and ensure stable operation of the equipment.
RF devices
In the fields of communication and radio frequency control, ceramic substrates are one of the ideal substrates for radio frequency devices. Its low loss, high frequency characteristics and stable dielectric properties make it the first choice material for manufacturing radio frequency filters, power amplifiers, antennas and other equipment.
LED lighting
LED lighting is one of the fields that have developed rapidly in recent years, and ceramic substrates play an important role in LED lighting. Ceramic substrate has excellent heat dissipation performance, which can effectively cool the LED chip, extend its life and improve brightness stability.
Sensor
Ceramic substrates also play a key role in various sensor applications. For example, pressure sensors, acceleration sensors, temperature sensors, etc. often use ceramic substrates as their supporting structures to ensure stable performance and a reliable working environment.
The excellent thermal management and electrical properties of ceramic substrates make them the first choice for many critical applications. Whether it is industrial applications under high temperature and high pressure environments, or applications in precision instruments and medical equipment, ceramic substrates can provide reliable support and stable performance. With the continuous advancement of technology and the expansion of application fields, ceramic substrates will continue to play an important role in promoting the continued development and innovation of the electronics industry.
What are the advantages of Ceramics Substrate?
When it comes to ceramic substrates, the advantages are clear. Ceramic substrates offer a series of unique advantages over traditional substrate materials that make them the first choice for many electronic applications.
First, ceramic substrates have excellent thermal conductivity properties. Ceramic materials themselves are good thermal conductors and can effectively conduct heat from one area to another, thereby helping to maintain a stable operating temperature of electronic devices. This excellent thermal conductivity makes ceramic substrates particularly suitable for applications requiring high power density and high heat, such as power modules and LED lighting systems.
Secondly, ceramic substrates have excellent high temperature resistance. In many electronic applications, devices may need to operate under extreme temperature conditions, and ceramic substrates can withstand high-temperature environments without damage. This high temperature resistance makes ceramic substrates ideal for applications requiring high temperature stability, such as automotive electronics and aerospace equipment.
In addition, ceramic substrates offer excellent mechanical strength and impact resistance. Compared with traditional substrate materials, such as FR4, ceramic substrates are more durable and can withstand vibration, impact and other external forces. This excellent mechanical property enables the ceramic substrate to maintain stable and reliable performance in various harsh environments, thereby extending the service life of electronic equipment.
To sum up, ceramic substrates have become an important part of the electronics industry due to their excellent thermal conductivity, high temperature resistance and mechanical strength. Whether in industrial applications or consumer electronics, ceramic substrates have demonstrated stable and reliable performance and play an irreplaceable role in promoting the development and innovation of modern electronic technology.
FAQ
What are the advantages of ceramic substrates over other materials?
Ceramic substrates have better thermal conductivity and insulation properties than traditional substrate materials, such as FR4 (fiberglass reinforced epoxy resin). This makes the ceramic substrate more stable and reliable in high temperature, high frequency and high power applications.
Is the manufacturing process of ceramic substrates complicated?
The manufacturing process of ceramic substrates is relatively complex and involves multiple links such as material molding, sintering and processing. However, the development of modern manufacturing technology has made the production process more precise and efficient, ensuring product quality and performance stability.
What application fields are ceramic substrates suitable for?
Ceramic substrates are suitable for many fields, including power modules, radio frequency devices, LED lighting, sensors, etc. Its excellent thermal management and electrical performance make it outstanding in high power density and high frequency applications.
What is the cost of ceramic substrates?
Since the manufacturing process and material costs of ceramic substrates are relatively high, their prices are usually slightly higher than traditional substrate materials. However, considering its excellent performance and long-term stability, ceramic substrates are still the first choice for many high-end applications.
What issues should be paid attention to when designing ceramic substrates?
When designing ceramic substrates, special attention needs to be paid to aspects such as thermal management, material selection, and wiring. Good design can maximize the performance of ceramic substrates and ensure their good stability and reliability in practical applications.