What is Wire Bonding BGA substrate?
Wire Bonding BGA substrates الشركه المصنعه, A specialized manufacturer in wire bonding BGA substrates, our expertise lies in crafting intricate electronic components essential for cutting-edge technologies. With precision engineering and advanced methodologies, we produce substrates that meet stringent industry standards. Our commitment to innovation ensures optimal performance and reliability, catering to diverse applications in electronics, الاتصالات السلكيه, and beyond. From concept to production, we excel in delivering tailored solutions that empower our clients to stay ahead in a rapidly evolving market. Trust in our experience and dedication as your partner in shaping the future of electronic manufacturing.
Wire Bonding BGA (صفيف شبكة الكرة) substrate is a special type of printed circuit board (ثنائي الفينيل متعدد الكلور) that uses gold wire bonding technology to connect semiconductor devices to the surface of the substrate. Compared with traditional surface mount technology, Wire Bonding BGA substrates demonstrate superior performance and reliability in high-performance electronic systems. Its design structure mainly includes a substrate with a series of pads or solder balls for connecting devices, and the connections are achieved through small metal wires. This design enables the Wire Bonding BGA substrate to have higher density, better electrical performance and stronger mechanical stability.
Wire Bonding BGA substrate plays a vital role in modern electronic devices. They are widely used in high-performance electronic systems such as microprocessors, memory modules, and wireless communication equipment. Its advantages are not only reflected in its highly integrated design, but also in its excellent electrical performance, mechanical stability and thermal management capabilities. By using Wire Bonding BGA substrates, electronic equipment manufacturers can achieve higher performance and reliability requirements, while also providing the possibility for product miniaturization and lightweighting.
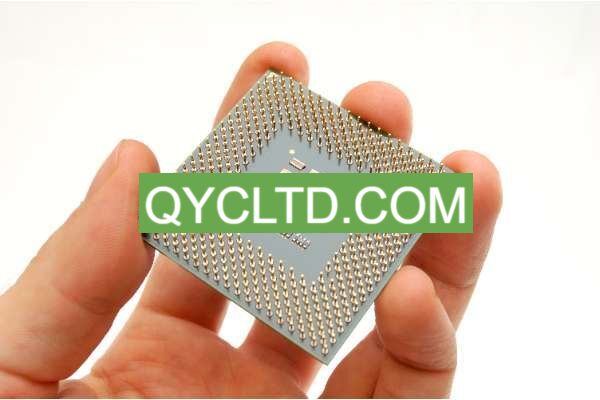
Wire Bonding BGA substrates Manufacturer
بشكل عام, Wire Bonding BGA substrate is a printed circuit board with complex structure and advanced technology. It connects semiconductor devices to the surface of the substrate through gold wire bonding technology, providing a reliable and reliable solution for the manufacturing of high-performance electronic equipment. Efficient solution.
How is the design of Wire Bonding BGA substrate carried out?
The design of Wire Bonding BGA substrate is a key link, which directly affects the performance and reliability of the final product. When designing, engineers need to consider a variety of factors to ensure that the substrate meets the requirements and standards of the application.
أولا, the design engineer needs to clarify the project’s technical specifications and performance requirements. This may include requirements for signal integrity, توزيع الطاقة, الإدارة الحرارية, الخ. Based on these requirements, engineers can determine the size, number of layers, and layout of the substrate.
مقبل, CAD software is used for circuit design and layout. في هذه المرحلة, engineers place circuit components (مثل رقائق البطاطس, المكثفات, المقاومات, الخ.) on the substrate and design corresponding interconnections. بالإضافة, considering that Wire Bonding BGA substrates are often used in high-density integrated circuits, engineers need to pay special attention to the compactness of the layout and the complexity of the interconnect lines.
After the layout design is completed, engineers usually perform electromagnetic simulation and thermal simulation analysis. Through these simulation analyses, they can evaluate the electromagnetic compatibility, signal integrity and thermal distribution of the layout, identify potential problems and optimize them.
After the design is complete, prototyping and verification are typically performed. Build an actual prototype and, through testing and verification, confirm that the design’s performance and reliability meet expectations. During this process, engineers may make multiple adjustments and improvements until the desired effect is achieved.
لتلخيص, the design of Wire Bonding BGA substrate is a complex process that takes into account many factors. Through reasonable design and optimization, the substrate can be ensured to meet the needs of high-performance electronic systems and provide reliable support and guarantee for applications.
What is the manufacturing process of Wire Bonding BGA substrate?
The manufacturing process of Wire Bonding BGA substrates is a complex process that is carefully designed and executed with precision. The main steps of this process are detailed below:
Material Selection: أولا, the manufacturer carefully selects the substrate material suitable for the specific application. Common materials include FR-4 glass fiber composite materials, polyimide films, and ceramic substrates. Material selection depends on required electrical performance, thermal management capabilities and mechanical stability.
Design and Layout: After deciding on the materials, the design team began working on the layout of the substrate. They consider factors such as signal integrity, توزيع الطاقة, heat dissipation and more, utilizing advanced CAD software for design and simulation to ensure optimal performance and manufacturability.
Layer stacking: Layering of substrates is an important step at the beginning of the manufacturing process. This involves stacking thin layers of various materials together to form a complete substrate structure.
Circuit pattern production: مقبل, photolithography technology is used to form a circuit pattern on the surface of the substrate. This involves applying photoresist, exposing the photoresist, and chemically etching or etching areas not protected by the photoresist to create the desired circuit pattern on the substrate.
Metallization: After the circuit pattern is formed, the substrate undergoes a metallization process, usually including a copper plating process, to increase conductivity and strengthen circuit connections.
Final processing: After the metallization treatment is completed, the final processing steps are performed on the substrate, including surface coating with a protective layer and final surface treatment to ensure the stability and reliability of the substrate.
Wire Bonding: For Wire Bonding BGA substrate, wire bonding is a critical step. In this process, tiny metal wires are ultrasonically welded to the surface of the semiconductor device and substrate to achieve electrical connection. This requires highly sophisticated equipment and technology to ensure welding accuracy and reliability.
Through the above steps, the Wire Bonding BGA substrate is manufactured, providing a reliable foundation for various high-performance electronic systems. This manufacturing process requires manufacturers to have advanced technology and extensive experience to ensure that the final product meets high standards of quality and performance requirements.
How much does it cost to manufacture a Wire Bonding BGA substrate?
When we talk about the manufacturing cost of Wire Bonding BGA substrates, we must consider several factors that can have a significant impact on the final cost. Let’s take a closer look:
أولا, the manufacturing cost of Wire Bonding BGA substrates is affected by the materials selected. Different types of substrate materials vary in performance and cost. نموذجيا, materials with higher performance requirements, such as special dielectric materials required for high-frequency applications, result in higher costs. In comparison, conventional FR-4 substrates may be more cost-effective, but may not meet the requirements in certain applications.
ثانيا, design complexity also directly affects manufacturing costs. Factors such as the number of layers, apertures, line width/line spacing in the design will affect the complexity of the manufacturing process, thereby affecting the cost. More complex designs usually mean more manufacturing steps and more material consumption, so costs increase accordingly.
بالإضافة, manufacturing costs are also affected by economies of scale. Large-scale production often allows for lower unit costs because fixed costs can be spread over more products. في المقابل, low-volume production or customized production may require more manpower, time and resources, so the unit cost will be higher.
In addition to the above factors, manufacturing costs are also affected by technical requirements and production processes. Adopting advanced production technology and equipment may bring higher investment costs, but it can improve production efficiency and product quality, thereby reducing costs in the long term.
لتلخيص, the manufacturing cost of Wire Bonding BGA substrate is a complex issue and is affected by multiple factors. To accurately evaluate costs, various factors such as material selection, design complexity, production scale, and technical requirements must be comprehensively considered. Working with an experienced manufacturer, with full communication and collaboration, can help maximize cost optimization and ensure the final product meets expected quality and performance standards.
What material is the Wire Bonding BGA substrate made of?
Wire Bonding BGA substrate material selection is critical to its performance and reliability. Below we will explore some common Wire Bonding BGA substrate materials and their characteristics:
FR-4 (fiberglass reinforced epoxy resin): FR-4 is one of the most common substrate materials and has good mechanical strength, heat resistance and chemical stability. Its low cost and wide availability make it the first choice for many applications. However, the thermal conductivity of FR-4 substrate is relatively poor and is not suitable for certain high-temperature applications.
بوليميد: Polyimide substrates are known for their excellent high temperature resistance and are suitable for applications in high temperature environments, such as aerospace and automotive electronics. It has good mechanical properties and chemical stability and is relatively lightweight, making it ideal for weight-critical applications.
Ceramic substrates: Ceramic substrates have excellent thermal conductivity and dimensional stability and are suitable for high-frequency, high-speed circuits and radio frequency applications. Due to their excellent properties, ceramic substrates are commonly used in communications equipment, أنظمة الرادار, and microwave RF circuits.
Metal substrate: Typically constructed of aluminum or copper, metal substrates have excellent thermal conductivity and can be used in applications that require good heat dissipation, such as high-power LED lighting and power electronics.
High-frequency board materials: High-frequency board materials used in radio frequency and microwave applications have the characteristics of low loss, low dielectric constant and low dielectric loss tangent, which can achieve excellent transmission performance of high-frequency signals.
باختصار, selecting the appropriate substrate material depends on the requirements of the specific application, including factors such as frequency range, environmental conditions, thermal conductivity and mechanical strength. Manufacturers usually select the most appropriate materials based on customer needs and application scenarios to ensure that Wire Bonding BGA substrates have excellent performance and reliability.
Who makes Wire Bonding BGA substrates?
In the field of Wire Bonding BGA substrate manufacturing, supplier selection is crucial. For the production of Wire Bonding BGA substrates, our company focuses on providing solutions with excellent quality and reliability, so we are proud to announce that our company is one of the leading manufacturers of Wire Bonding BGA substrates.
As a Wire Bonding BGA substrate manufacturer, we not only have advanced production equipment and technology, but more importantly, we have a team with rich experience and professional knowledge that can accurately control every detail of the manufacturing process. We are committed to providing high-quality, high-performance Wire Bonding BGA substrates to meet customers’ growing needs for the stability and reliability of electronic systems.
In our manufacturing facilities, we employ state-of-the-art processes and quality control standards to ensure that each Wire Bonding BGA substrate meets the strictest quality requirements. We are committed to continuously improving our manufacturing processes to adapt to changing market demands and technology trends, and to provide customers with the highest quality products and services.
As a manufacturer of Wire Bonding BGA substrates, we not only focus on product quality, but also on cooperation and communication with customers. Our customer service team is always ready to provide support and assistance to ensure that customers receive a satisfactory service experience throughout the entire project cycle.
باختصار, as a manufacturer of Wire Bonding BGA substrates, we are committed to providing customers with high-quality, high-performance products to meet their growing needs. We firmly believe that through our efforts and unremitting pursuit, we will become your trustworthy long-term partner.
What are the five characteristics of great customer service?
Excellent customer service is crucial in any industry. Here are five features that will make your customer service stand out:
Responsive: Effective communication is at the heart of great customer service. No matter what needs or questions customers raise, timely responses can enhance customers’ trust in the brand. Maintaining timely communication through multiple channels such as phone, البريد الإلكتروني, social media, الخ. is key to ensuring that customer needs are met.
Technical expertise: A customer service team with specialized knowledge can provide accurate and targeted solutions. Understanding the details of a product or service and being able to clearly explain customer questions or issues will not only satisfy customer needs, but also build long-term trusting relationships.
Be flexible and adaptable: Every customer has unique needs and expectations, so it is crucial to be flexible and adaptable to their requirements. Being able to adjust service plans or provide customized solutions according to customer needs can make customers feel valued and respected, thus enhancing customer loyalty.
Quality Assurance: Excellent customer service includes not only quality assurance of the product or service itself, but also quality control of the entire interaction process. From product delivery to after-sales service, we ensure that every link reaches the highest standards, allowing customers to feel the brand’s professionalism and trustworthiness.
After-sales support: Customer service should not stop at the completion of the sale, but should continue into the after-sales stage. Providing continuous after-sales support, including product maintenance, technical support, problem solving, الخ., can enhance customer satisfaction and promote word-of-mouth, thus attracting more potential customers.
These five characteristics together form the cornerstone of high-quality customer service. Through continuous efforts and continuous improvement, the company can win more customers and achieve long-term development.
FAQS
In what application areas are Wire Bonding BGA substrates widely used?
Wire Bonding BGA substrates are widely used in high-performance electronic systems such as aerospace, automobiles, communications, الخ. Its excellent electrical performance, mechanical reliability and thermal management capabilities make it ideal for these applications.
What factors should you consider when choosing a Wire Bonding BGA substrate manufacturer?
When selecting a manufacturer, factors such as its technical expertise, manufacturing capabilities, quality assurance processes, and reputation for customer service need to be considered to ensure the best results.
What are the common problems in the manufacturing process of Wire Bonding BGA substrate?
أثناء عملية التصنيع, problems such as material selection, manufacturing equipment failure, and process parameter adjustment may be encountered. Effective quality control and process optimization are the keys to solving these problems.
How much does it cost to manufacture a Wire Bonding BGA substrate?
The manufacturing cost of Wire Bonding BGA substrates is affected by many factors, بما في ذلك اختيار المواد, design complexity, manufacturing scale and technical specifications. When it comes to optimizing costs, there is a need to balance the relationship between product quality and cost.
How to ensure the quality of Wire Bonding BGA substrate?
The key to ensuring the quality of Wire Bonding BGA substrates lies in strict quality control processes and industry-standard manufacturing practices. High-quality product delivery is achieved through the adoption of advanced manufacturing technologies and continuous improvement of quality management systems.