Black Substrate Manufacturer.As a leading Black الركيزه الشركه المصنعه, we specialize in producing high-quality black substrates for various electronic applications. Our advanced manufacturing processes ensure superior performance, durability, and thermal management. We cater to diverse industries, offering customized solutions to meet specific needs. With a commitment to innovation and excellence, our black substrates enhance the reliability and efficiency of your electronic devices.
Black substrates are becoming increasingly popular in the electronics industry due to their aesthetic appeal and unique properties. These substrates are used in a variety of applications, ranging from high-end consumer electronics to advanced military and aerospace systems. The black color is not just for visual purposes; it often indicates specific material properties and benefits that can be advantageous in particular applications. This article delves into the properties, structure, materials, manufacturing process, applications, and advantages of black substrates.
What is a Black Substrate?
A black substrate is a type of printed circuit board (ثنائي الفينيل متعدد الكلور) or electronic substrate that features a black base material or surface finish. Unlike traditional green or other colored substrates, black substrates offer unique advantages in terms of thermal management, optical properties, and aesthetic appeal. They are commonly used in applications where these characteristics are particularly beneficial, such as in high-performance electronics, automotive systems, and consumer devices.
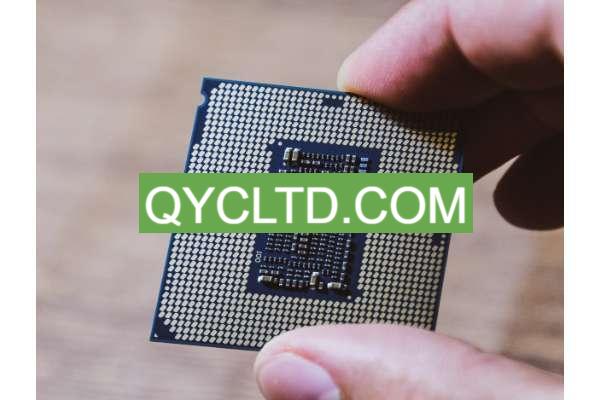
Black Substrate Manufacturer
The black color in these substrates can be achieved through the use of specific base materials, surface finishes, or coatings. The choice of material and the method of achieving the black color can influence the substrate’s electrical, thermal, and mechanical properties.
Structure of Black Substrates
The structure of black substrates is similar to that of traditional PCBs, with some variations to accommodate the specific properties and requirements of the black material. Key structural elements include:
The core of a black substrate is typically made of a fiberglass-reinforced epoxy resin (FR-4) or other advanced materials such as polyimide or ceramic-filled laminates. The core provides the primary structural integrity and electrical insulation.
Prepreg layers, which are resin-coated fiberglass sheets, are used to bond the core and copper layers together. These layers offer insulation and mechanical strength.
The copper layers serve as conductive paths for electrical signals. In black substrates, these layers are often treated or coated to achieve the black appearance.
Vias and through-holes are drilled into the substrate to create electrical connections between different layers. These features are crucial for multi-layer designs and high-density interconnections.
A black solder mask is applied to protect the copper traces and prevent solder bridges. The silkscreen layer, also often black or white for contrast, is used to print labels and component outlines.
The surface finish on black substrates can include finishes like ENIG (Electroless Nickel Immersion Gold), immersion silver, or organic solderability preservatives (OSP). These finishes enhance solderability and protect the copper from oxidation.
Materials Used in Black Substrates
The materials used in black substrates are chosen for their electrical, thermal, and mechanical properties, as well as their ability to achieve a black appearance. Key materials include:
This is a variant of the standard FR-4 material with a black color. It retains the same mechanical and electrical properties as traditional FR-4 but offers a distinct aesthetic and some additional thermal benefits.
For high-performance applications, materials such as black polyimide or ceramic-filled laminates may be used. These materials offer superior thermal stability and electrical performance.
High-quality copper foil is used for the conductive layers. In black substrates, the copper may be treated with a black oxide process to enhance adhesion and achieve the desired color.
Resin-coated fiberglass sheets, known as prepreg, are used to bond the layers together. These materials provide insulation and contribute to the overall mechanical strength of the substrate.
Various surface coatings and treatments can be applied to achieve the black color. These may include black solder masks, black oxide treatments, or other specialized coatings.
The Manufacturing Process of Black Substrates
The manufacturing process of black substrates involves several precise steps to ensure high performance and reliability. The process includes:
High-quality core, prepreg, and copper materials are prepared based on design specifications. For black substrates, materials that inherently have or can achieve a black appearance are selected.
The core, prepreg, and copper layers are stacked and bonded together using a lamination press. The press applies heat and pressure to cure the resin in the prepreg, creating a solid, multi-layered structure.
Holes for vias and through-holes are drilled into the laminated substrate. Advanced drilling techniques, such as laser drilling or mechanical drilling, are used to achieve precise hole dimensions and locations.
The drilled holes are plated with copper to create electrical connections between layers. The entire substrate is also plated to build up the copper thickness on the surface layers.
The circuit patterns are transferred onto the copper layers using a photolithographic process. The exposed copper is then etched away, leaving behind the desired circuit traces.
A black solder mask is applied to protect the copper traces and prevent solder bridges during component assembly. The mask is typically applied using screen printing or photo-imaging techniques.
A surface finish is applied to exposed copper areas to enhance solderability and protect against oxidation. Common finishes include ENIG, immersion silver, and OSP.
Electronic components are placed onto the substrate and soldered in place using reflow soldering or wave soldering techniques. Automated pick-and-place machines are often used for precise component placement.
The assembled substrate undergoes rigorous testing and inspection to ensure it meets performance and reliability standards. Electrical testing, visual inspection, and automated optical inspection (AOI) are used to identify defects and ensure quality.
Application Areas of Black Substrates
Black substrates are used in a wide range of applications across various industries due to their unique properties and advantages. Key application areas include:
Black substrates are commonly used in high-end consumer electronics, مثل الهواتف الذكية, اقراص, and laptops, where aesthetics and performance are critical.
في صناعة السيارات, black substrates are used in advanced driver-assistance systems (ADAS), infotainment systems, and other electronic control units (ECUs). These applications benefit from the thermal management and reliability of black substrates.
The aerospace and defense industries use black substrates in radar systems, معدات الاتصالات, and avionics. These applications require reliable performance and the ability to withstand harsh environmental conditions.
Black substrates are used in medical devices, such as diagnostic instruments and imaging equipment, where precise signal transmission and reliability are essential.
In industrial applications, black substrates are used in control systems, sensors, and other critical electronic components that require robust performance and durability.
Advantages of Black Substrates
Black substrates offer several advantages that make them a preferred choice for specific applications. These advantages include:
The black color provides a sleek and professional appearance, making these substrates ideal for high-end consumer electronics and other visually demanding applications.
Black substrates often have superior thermal properties, helping to dissipate heat more effectively and prevent overheating in high-performance applications.
The materials and design techniques used in black substrates help minimize signal loss and interference, ensuring accurate and reliable signal transmission.
The robust construction and high-quality materials used in black substrates ensure reliable performance in demanding applications, such as automotive, الفضاء, and defense.
Black substrates are versatile and can be used in a wide range of applications, from consumer electronics to industrial equipment, making them an ideal choice for various industries and applications.
الأسئلة المتداولة
What are the key benefits of using black substrates in high-performance electronics?
Black substrates offer several key benefits for high-performance electronics, including enhanced thermal management, improved signal integrity, and a sleek aesthetic appearance. These substrates are designed to dissipate heat more effectively, minimize signal loss and interference, and provide a professional look, making them ideal for high-end consumer devices and critical industrial applications.
Can black substrates withstand harsh environmental conditions?
Yes, black substrates are highly suitable for use in harsh environmental conditions. The robust structure, high-quality materials, and advanced manufacturing processes ensure reliable performance under varying environmental conditions, such as high temperatures, humidity, and mechanical stress. This makes them ideal for applications in aerospace, defense, وإلكترونيات السيارات.
How do black substrates improve thermal management in electronic devices?
Black substrates often have superior thermal properties compared to traditional substrates. The materials and design techniques used in these substrates enhance heat dissipation, preventing overheating and ensuring reliable performance in high-power and high-speed applications. Effective thermal management is critical for maintaining the longevity and reliability of electronic devices.
What industries benefit the most from using black substrates?
Industries that benefit the most from using black substrates include high-end consumer electronics, إلكترونيات السيارات, aerospace and defense, الأجهزة الطبية, and industrial equipment. These industries require high-performance, reliable electronic components and systems, and black substrates provide the necessary properties to meet these demands.