What is Wire Bonding substrates?
Wire Bonding Substrates Manufacturer.A leading innovator in the realm of microelectronics, our company stands as the premier Wire Bonding substrates Manufacturer. With a steadfast commitment to precision engineering and cutting-edge technology, we craft substrates that redefine industry standards. Our state-of-the-art facilities, coupled with a team of skilled artisans, ensure that each substrate meets rigorous quality benchmarks. From concept to creation, we prioritize excellence, delivering products that enable seamless integration and optimal performance in diverse applications. Trust in our expertise to elevate your projects with reliability, ประสิทธิภาพ, and unparalleled craftsmanship.
Wire Bonding Substrates are a key component that connects chips and PCB in electronic devices. In the field of modern electronics, the realization of various complex circuits is inseparable from this technology. The basic principle is to establish a reliable connection between the components in the circuit (such as integrated circuit chips) and the PCB through welding, thereby ensuring the normal function of the circuit.
Wire bonding substrates play a vital role in electronic devices. It is not only a simple connection medium, but also a bridge and support for circuit signal transmission. Through precision design and manufacturing processes, wire bonding substrates can achieve high-speed data transmission, stable power supply, and complex circuit wiring, thereby meeting the performance and reliability requirements of modern electronic equipment.
In the manufacturing process of wire bonding substrates, fine welding wires (usually metal) are usually used for connection. This welding method can achieve high-density wiring and is suitable for miniaturized and integrated electronic devices. Compared with traditional welding methods, wire bonding substrates have higher reliability and lower failure rates, so they are widely used in various high-end electronic products.
The design and selection of wire bonding substrates requires consideration of multiple factors, including chip packaging form, wiring method, working environment conditions, ฯลฯ. ในเวลาเดียวกัน, in order to meet the needs of different application scenarios, manufacturers also provide a variety of material and size options, as well as customized solutions.
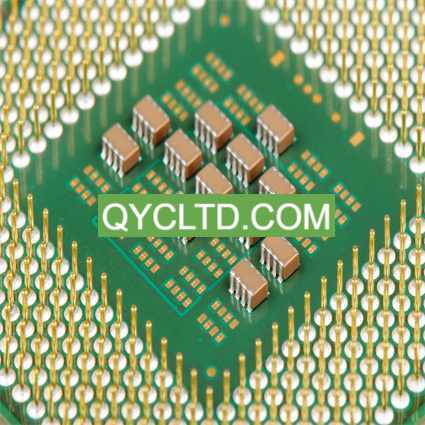
ผู้ผลิตพื้นผิวเชื่อมลวด
ในระยะสั้น, wire bonding substrates, as an indispensable component of electronic equipment, play a vital role in improving circuit performance and reliability. With the continuous development of electronic technology, it is believed that wire bonding substrates will show their unique value in more fields and promote further innovation and development of electronic equipment.
Wire Bonding substrates design Reference Guide.
When designing Wire Bonding Substrates, multiple factors need to be considered to ensure optimal performance and reliability of the final product. Here are some key factors that designers should pay attention to:
Choosing the appropriate chip package is one of the keys to designing Wire Bonding Substrates. Different chip packaging types include bare die packaging (Bare Die), BGA (Ball Grid Array), QFN (Quad Flat No-leads), ฯลฯ. Designers need to consider the chip’s packaging type and compatibility with Wire Bonding Substrates based on the requirements of specific applications to ensure good connection and stability.
In the design of Wire Bonding Substrates, the wiring method is crucial. Reasonable wiring methods can minimize signal transmission loss and interference and improve circuit performance. Designers need to consider factors such as signal transmission paths, wiring length and width, and signal and ground separation to ensure good signal integrity and stability.
The location of the connector is critical to the design of Wire Bonding Substrates. Reasonable connector location can facilitate device connection and maintenance while ensuring the stability of signal transmission. Designers need to consider factors such as the layout relationship between the connector and other components, the type and size of the connector, and the distance between the connector and Wire Bonding Substrates to ensure the reliability and convenience of the connection.
By properly designing Wire Bonding Substrates, the performance and reliability of your circuit can be maximized. Designers need to comprehensively consider multiple factors such as chip packaging, wiring methods, and connector locations to ensure that the final product meets the requirements of specific applications, and continuously optimize during the design process to achieve better performance and reliability.
What material is used in Wire Bonding substrates?
Wire Bonding Substrates are vital components in electronic equipment, and their performance directly affects the reliability and stability of the equipment. When choosing the right material, there are several factors to consider, including high temperature resistance, corrosion resistance, thermal conductivity, ฯลฯ. The following are several high-performance materials commonly used in Wire Bonding Substrates:
FR-4 is a commonly used glass fiber reinforced epoxy resin material with excellent electrical and mechanical properties. It has good high temperature resistance and can maintain stability at relatively high temperatures, making it suitable for applications requiring higher ambient temperatures. นอกจากนี้, the price of FR-4 materials is relatively low and the manufacturing cost is economical, so it is widely used in various electronic devices.
Polyimide (พีไอ) is a high-performance engineering plastic with excellent high temperature resistance, chemical corrosion resistance and mechanical strength. It can still maintain stability in high-temperature environments and is not easily corroded by chemical substances. It is suitable for electronic equipment with strict environmental requirements. Due to its excellent properties, โพลีอิไมด์ (พีไอ) is often selected as a material for Wire Bonding Substrates, especially in applications under special working conditions such as high temperature and high frequency.
โพลีเตตระฟลูออโรเอทิลีน (ไฟเบอร์) is a polymer material with excellent electrical properties and chemical resistance. It has low dielectric constant and low loss factor, making it suitable for high-frequency circuit and microwave circuit applications. ในเวลาเดียวกัน, PTFE also has high heat resistance and chemical stability, and can remain stable in extreme environments. เพราะฉะนั้น, PTFE is often selected as a material for Wire Bonding Substrates, especially in high-frequency circuits such as wireless communication equipment and radar systems.
สรุป, the material selection of Wire Bonding Substrates is very important. It not only needs to consider its high temperature resistance, corrosion resistance and other properties, but also needs to be comprehensively considered according to the requirements of the specific application scenario. High-performance materials such as FR-4, โพลีอิไมด์ (พีไอ), and PTFE have their own advantages in different fields. Reasonable selection of materials can improve the performance and reliability of Wire Bonding Substrates and provide guarantee for the stable operation of electronic equipment.
What size are Wire Bonding substrates?
The dimensional standards of Wire Bonding Substrates are one of the key factors that must be carefully considered during the design and manufacturing process. Although sizes can be customized to meet the requirements of a specific application, in practice the standardized size range makes Wire Bonding Substrates more predictable and versatile.
For small micro packages, Wire Bonding Substrates are typically smaller in size to accommodate compact space layouts and lightweight application requirements. These tiny packages can find applications in smartphones, portable medical devices, and other electronic devices that require small size and high performance. In these packages, the dimensions of the Wire Bonding Substrates need to be precisely controlled to ensure good electrical performance and reliability.
ในทางตรงกันข้าม, large multi-chip modules usually require larger Wire Bonding Substrates to accommodate multiple chips and provide sufficient wiring space. These modules are widely used in high-end computers, communication base stations, ระบบอัตโนมัติทางอุตสาหกรรมและสาขาอื่นๆ. Large-size Wire Bonding Substrates usually have higher density and more complex wiring to meet the complex connection needs between multiple chips.
In addition to the length, width and height of the dimensions, the thickness of Wire Bonding Substrates is also an important consideration. Thinner substrates can reduce the volume and weight of the overall package while improving heat dissipation efficiency and signal transmission performance. อย่างไรก็ตาม, in some applications a thicker substrate may be more suitable to provide additional mechanical support and protection.
Dimensional accuracy and consistency must be ensured when manufacturing Wire Bonding Substrates. Any dimensional deviation can lead to joint failure or performance degradation, so it is crucial to use precision machining and measurement techniques during the manufacturing process.
โดยสรุป, Wire Bonding Substrates range in size from small micro packages to large multi-chip modules, providing flexibility and choice for different applications. Reasonable selection and design size will help improve the performance, reliability and applicability of the circuit to meet the needs of various electronic devices.
The Manufacturing Process of Wire Bonding substrates.
The manufacturing process of Wire Bonding Substrates is a complex and precise process, with key steps including substrate preparation, metallization, welding and packaging. Precise execution of these steps is critical to ensuring product quality and performance.
ที่หนึ่ง, substrate preparation is the first step in manufacturing Wire Bonding Substrates. ในขั้นตอนนี้, a substrate of appropriate material is selected, เช่น FR-4, โพลีอิไมด์ (พีไอ), ฯลฯ, and then processed into the required size and shape through cutting, polishing and other processes to meet the requirements of the specific application.
Next comes the metallization process, which is a crucial step in the manufacturing of Wire Bonding Substrates. Metallization is usually achieved by applying a layer of conductive material such as copper. This conductive layer will be used to connect the circuit between the chip and the PCB. Precise metallization processes ensure the reliability and stability of soldered connections.
Soldering is another critical step in making Wire Bonding Substrates. During the soldering process, bonding wires are used to connect the chip to the substrate. Bonding wires are usually made of metal or alloy and are connected to the chip pins and the surface of the substrate through heat pressing or ultrasonic waves. Precise control of the welding process can ensure the strength and stability of the welding joints, thereby improving product reliability.
ในที่สุด, encapsulation is the final step in Wire Bonding Substrates manufacturing. During the packaging process, the welded connections are protected and fixed by coating a protective layer or installing a shell to improve the durability and environmental adaptability of the product. Quality control of the packaging process is critical to ensuring long-term product stability and performance.
โดยสรุป, the manufacturing process of Wire Bonding Substrates involves multiple key steps, including substrate preparation, metallization, soldering, and packaging. Through precise manufacturing process control, product quality and performance can be ensured to reach the best level and meet the needs of different application fields.
The Application area of Wire Bonding substrates.
As a key connection technology, Wire Bonding Substrates play an irreplaceable role in various electronic devices. Their wide range of applications cover communication equipment, อุปกรณ์อิเล็กทรอนิกส์ยานยนต์, อุปกรณ์ทางการแพทย์, industrial control and other fields.
ในด้านอุปกรณ์สื่อสาร, Wire Bonding Substrates undertake the important task of connecting chips and PCBs. Whether it is a mobile phone, router, or communication base station, reliable Wire Bonding Substrates are needed to ensure the stability and reliability of signal transmission. Its high-density wiring and precision welding technology allow communication equipment to maintain excellent performance in high-speed data transmission environments.
Automotive electronics is another important application area. The electronic systems in modern vehicles are increasingly complex and need to host a large number of sensors, control units and communication modules. Wire Bonding Substrates play a role in connecting and protecting electronic components in automotive electronics, providing solid technical support for vehicle intelligence, safety and comfort.
The requirements for electronic equipment in the field of medical devices are also increasing. เช่น, medical devices such as medical imaging equipment, pacemakers, and prosthetic limb controllers all require reliable electronic components to ensure their normal operation and precise control. Wire Bonding Substrates play a vital role in these devices, ensuring the stability and safety of medical devices, which is directly related to the health and life of patients.
The industrial control field is also an important application scenario for Wire Bonding Substrates. Factory automation, robot control, sensor networks, and more all rely on reliable electronics for precise control and monitoring. Wire Bonding Substrates provide reliable electronic connection solutions for industrial control systems through its high reliability, high density connection and stable performance.
โดยทั่วไป, the wide application of Wire Bonding Substrates in communications, automobiles, medical and industrial fields demonstrates its importance and irreplaceability in the modern electronics industry. With the continuous advancement of technology and the continuous development of electronic equipment, Wire Bonding Substrates will continue to play a key role in promoting innovation and development in various industries.
What are the advantages of Wire Bonding substrates?
As an advanced connection technology, Wire Bonding Substrates has many advantages compared with traditional soldering methods. These advantages make it the first choice for many high-end electronic equipment. Here are some of the main advantages:
In electronic equipment, reliability is a crucial indicator. Traditional welding methods may be affected by factors such as uneven welding point structure and insufficient welding melting point, resulting in loose or broken welding points and equipment failure. Wire Bonding Substrates uses wire bonding technology to achieve more reliable connections, effectively reducing the risk of equipment failure caused by welding failure.
Because Wire Bonding Substrates uses precision wire bonding technology, the temperature control during the welding process is more accurate, the formation of welding points is more uniform, and therefore has a lower failure rate. This means that the parts connected by Wire Bonding Substrates are less prone to failure over long periods of use, extending the life of the equipment.
In some high power density electronic devices, heat dissipation is an important consideration. Traditional welding methods may cause heat accumulation around the welding point, resulting in poor heat dissipation and even affecting the performance of the device. Wire Bonding Substrates have better thermal conductivity, the contact area between the wire bonding point and the substrate is larger, and the heat transfer is more effective, which can effectively improve the heat dissipation performance of the device and enhance the stability and performance of the device.
สรุป, Wire Bonding Substrates, as an advanced connection technology, has obvious advantages in terms of reliability, failure rate and heat dissipation performance. These advantages make it the preferred connectivity solution for many high-end electronic devices. In the future design of electronic equipment, the rational application of Wire Bonding Substrates will provide greater guarantee for the performance and reliability of the equipment and promote the sustainable development of the electronics industry.
Frequently Asked Questions
How are Wire Bonding Substrates different from traditional soldering?
Traditional soldering usually uses solder or tin to connect components to the PCB, while Wire Bonding Substrates use wire bonding technology to connect the chip to the PCB through metal wires. Compared with traditional welding, wire bonding has higher precision and reliability and is suitable for applications that require higher connection quality.
What electronic devices are Wire Bonding Substrates suitable for?
Wire Bonding Substrates are widely used in various electronic devices, including but not limited to smartphones, แท็บ เล็ต, อุปกรณ์อิเล็กทรอนิกส์ยานยนต์, อุปกรณ์ทางการแพทย์, industrial control and other fields. Whether it is consumer electronics or industrial-grade equipment, Wire Bonding Substrates play a key connection role.
How to choose the right Wire Bonding Substrates material?
Selection of the appropriate material should be determined based on specific application needs. Common Wire Bonding Substrates materials include FR-4, โพลีอิไมด์ (พีไอ), ไฟเบอร์, ฯลฯ. When selecting materials, factors that need to be considered include the temperature, humidity, chemicals, ฯลฯ. of the working environment to ensure that the material has sufficient high temperature resistance, corrosion resistance, และความแข็งแรงเชิงกล.
What is the manufacturing process of Wire Bonding Substrates?
The manufacturing process of Wire Bonding Substrates includes multiple steps such as substrate preparation, metallization, welding, and packaging. ที่หนึ่ง, the substrate is prepared by chemical methods or mechanical processing, then metallization is performed on the surface of the substrate, then the chip is connected to the PCB using wire bonding technology, and finally encapsulation is performed to protect the connected components and ensure their stability.
What are the advantages of Wire Bonding Substrates compared to traditional welding?
Wire Bonding Substrates offer several advantages over traditional soldering. ที่หนึ่ง, wire bonding technology can achieve higher connection density and smaller package size, making electronic products thinner and lighter. ประการ, wire bonding has better thermal conductivity, which helps improve the performance stability of the circuit. นอกจากนี้, wire bonding technology can achieve a higher degree of automation, improve production efficiency, and reduce costs.